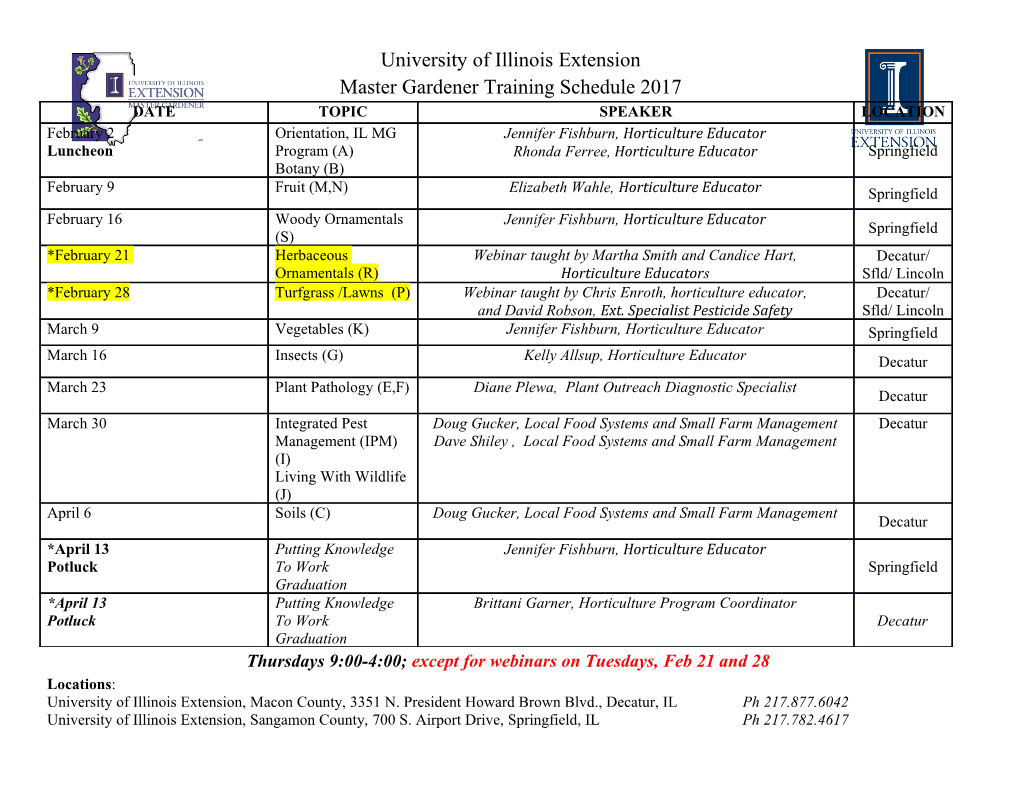
Bhopal disaster From Wikipedia, the free encyclopedia Jump to: navigation, search Bhopal memorial for those killed and disabled by the 1984 toxic gas release. The Bhopal disaster also known as Bhopal Gas Tragedy was a gas leak accident in India, considered one of the world's worst industrial catastrophes.[1] It occurred on the night of December 2–3, 1984 at the Union Carbide India Limited (UCIL) pesticide plant in Bhopal, Madhya Pradesh, India. A leak of methyl isocyanate gas and other chemicals from the plant resulted in the exposure of hundreds of thousands of people. Estimates vary on the death toll. The official immediate death toll was 2,259 and the government of Madhya Pradesh has confirmed a total of 3,787 deaths related to the gas release.[2] Others estimate 3,000 died within weeks and another 8,000 have since died from gas-related diseases.[3][4] A government affidavit in 2006 stated the leak caused 558,125 injuries including 38,478 temporary partial and approximately 3,900 severely and permanently disabling injuries.[5] UCIL was the Indian subsidiary of Union Carbide Corporation (UCC). Indian Government controlled banks and the Indian public held 49.1 percent ownership share. In 1994, the Supreme Court of India allowed UCC to sell its 50.9 percent share. Union Carbide sold UCIL, the Bhopal plant operator, to Eveready Industries India Limited in 1994. The Bhopal plant was later sold to McLeod Russel (India) Ltd. Dow Chemical Company purchased UCC in 2001. Civil and criminal cases are pending in the United States District Court, Manhattan and the District Court of Bhopal, India, involving UCC, UCIL employees, and Warren Anderson, UCC CEO at the time of the disaster.[6][7] In June 2010, seven ex-employees, including the former UCIL chairman, were convicted in Bhopal of causing death by negligence and sentenced to two years imprisonment and a fine of about $2,000 each, the maximum punishment allowed by law. An eighth former employee was also convicted, but died before judgment was passed.[1] Contents • 1 Summary of background o 1.1 Public information o 1.2 Plant production process • 2 Contributing factors o 2.1 Work conditions o 2.2 Equipment and safety regulations • 3 Previous warnings and incidents • 4 The leakage • 5 Health effects o 5.1 Short term health effects o 5.2 Hydrogen cyanide debate o 5.3 Long term health effects • 6 Aftermath of the leakage o 6.1 Compensation from Union Carbide o 6.2 Economic rehabilitation o 6.3 Occupational rehabilitation o 6.4 Habitation rehabilitation o 6.5 Health care o 6.6 Environmental rehabilitation • 7 Union Carbide's defense o 7.1 Investigation into possible sabotage o 7.2 Safety and equipment issues o 7.3 Response • 8 Long-term fallout o 8.1 Legal action against Union Carbide . 8.1.1 Legal proceedings leading to the settlement . 8.1.2 Charges against Warren Anderson and others • 9 Ongoing contamination • 10 Settlement fund hoax • 11 References and additional resources o 11.1 Footnotes o 11.2 Books and reports o 11.3 Journal articles and academic papers o 11.4 Governmental institutions o 11.5 Union Carbide Corporation o 11.6 Dow Chemical o 11.7 Mixed o 11.8 Presentations • 12 External and Wikipedia links o 12.1 News o 12.2 Important Court Orders o 12.3 Films o 12.4 Musical tributes o 12.5 Photos [edit] Summary of background The UCIL factory was built in 1969 to produce the pesticide Sevin (UCC's brand name for carbaryl) using methyl isocyanate (MIC) as an intermediate. An MIC production plant was added in 1979.[8][9][10] During the night of December 2–3, 1984, water entered a tank containing 42 tons of MIC. The resulting exothermic reaction increased the temperature inside the tank to over 200 °C (392 °F) and raised the pressure. The tank vented releasing toxic gases into the atmosphere. The gases were blown by northwesterly winds over Bhopal. Theories differ as to how the water entered the tank. At the time, workers were cleaning out a clogged pipe with water about 400 feet from the tank. The operators assumed that owing to bad maintenance and leaking valves, it was possible for the water to leak into the tank.[11] However, this water entry route could not be reproduced.[12] UCC also maintains that this route was not possible, but instead alleges water was introduced directly into the tank as an act of sabotage by a disgruntled worker via a connection to a missing pressure gauge on the top of the tank. Early the next morning, a UCIL manager asked the instrument engineer to replace the gauge. UCIL's investigation team found no evidence of the necessary connection; however, the investigation was totally controlled by the government denying UCC investigators access to the tank or interviews with the operators.[13][14] The 1985 reports give a picture of what led to the disaster and how it developed, although they differ in details.[14][15][16] Factors leading to the magnitude of the gas leak include: • Storing MIC in large tanks and filling beyond recommended levels • Poor maintenance after the plant ceased MIC production at the end of 1984 • Failure of several safety systems (due to poor maintenance) • Safety systems being switched off to save money—including the MIC tank refrigeration system which could have mitigated the disaster severity The problem was made worse by the mushrooming of slums in the vicinity of the plant, non-existent catastrophe plans, and shortcomings in health care and socio-economic rehabilitation.[3][4][17] [edit] Public information Much speculation arose in the aftermath. The closing of the plant to outsiders (including UCC) by the Indian government and the failure to make data public contributed to the confusion. The initial investigation was conducted entirely by Council of Scientific and Industrial Research (CSIR) and the Central Bureau of Investigation. CSIR was forbidden to publish health effect data until after 1994. [4] [edit] Plant production process Methylamine (1) reacts with phosgene (2) producing methyl isocyanate (3) which reacts with 1-naphthol (4) to yield carbaryl (5) UCC produced carbaryl using MIC as an intermediate.[4] After the Bhopal plant was built, other manufacturers including Bayer produced carbaryl without MIC, though at a greater manufacturing cost.[18] However, Bayer also uses the UCC process at the chemical plant once owned by UCC at Institute, West Virginia, USA and many other states [edit] Contributing factors Other factors identified by the inquiry included: use of a more dangerous pesticide manufacturing method, large-scale MIC storage, plant location close to a densely populated area, undersized safety devices, and the dependence on manual operations.[4] Plant management deficiencies were also identified – lack of skilled operators, reduction of safety management, insufficient maintenance, and inadequate emergency action plans. [4][19] The chemical process, or "route", used in the Bhopal plant reacted methylamine with phosgene to form MIC (methyl isocyanate), which was then reacted with 1-naphthol to form the final product, carbaryl. This route differs from MIC-free routes used elsewhere, in which the same raw materials are combined in a different manufacturing order, with phosgene first reacted with naphthol to form a chloroformate ester, which is then reacted with methyl amine. In the early 1980s, the demand for pesticides had fallen, but production continued, leading to buildup of stores of unused MIC.[4][18] See also: Carbaryl#Production [edit] Work conditions Attempts to reduce expenses affected the factory's employees and their conditions. Kurzman argues that "cuts...meant less stringent quality control and thus looser safety rules. A pipe leaked? Don't replace it, employees said they were told ... MIC workers needed more training? They could do with less. Promotions were halted, seriously affecting employee morale and driving some of the most skilled ... elsewhere".[20] Workers were forced to use English manuals, even though only a few had a grasp of the language.[11][21] By 1984, only six of the original twelve operators were still working with MIC and the number of supervisory personnel was also cut in half. No maintenance supervisor was placed on the night shift and instrument readings were taken every two hours, rather than the previous and required one-hour readings.[11][20] Workers made complaints about the cuts through their union but were ignored. One employee was fired after going on a 15- day hunger strike. 70% of the plant's employees were fined before the disaster for refusing to deviate from the proper safety regulations under pressure from management. [11][20] In addition, some observers, such as those writing in the Trade Environmental Database (TED) Case Studies as part of the Mandala Project from American University, have pointed to "serious communication problems and management gaps between Union Carbide and its Indian operation", characterized by "the parent companies [sic] hands-off approach to its overseas operation" and "cross-cultural barriers".[22] [edit] Equipment and safety regulations Union Carbide MIC plant It emerged in 1998, during civil action suits in India, that the plant was not prepared for problems. No action plans had been established to cope with incidents of this magnitude. This included not informing local authorities of the quantities or dangers of chemicals used and manufactured at Bhopal.[3][4][11][18] • The MIC tank alarms had not worked for four years.[3][4][11][23] • There was only one manual back-up system, compared to a four-stage system used in the US.[3][4][11][23] • The flare tower and the vent gas scrubber had been out of service for five months before the disaster.
Details
-
File Typepdf
-
Upload Time-
-
Content LanguagesEnglish
-
Upload UserAnonymous/Not logged-in
-
File Pages33 Page
-
File Size-