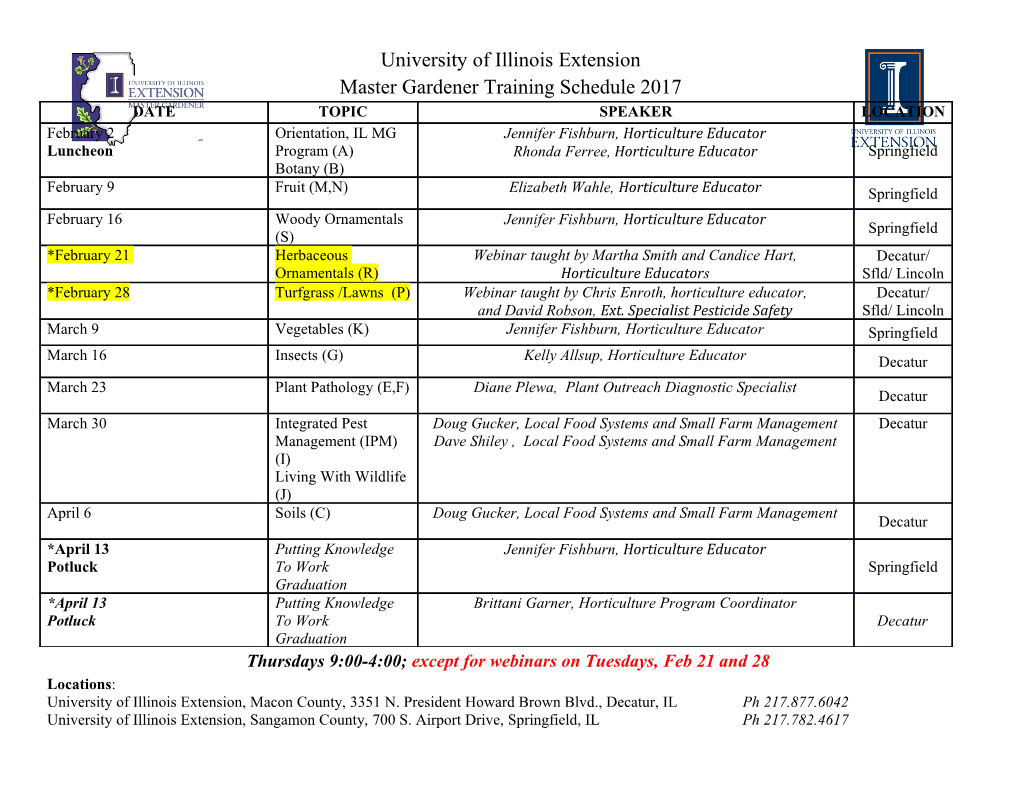
4 High-Performance Physical Modeling and Simulation Mean-Value Internal Combustion Engine Model with MapleSimTM Introduction The development of high-fidelity from the development of a predictive models of vehicle engines parameterized model using a variety is a major preoccupation of of physical modeling techniques to the powertrain engineers. By developing final simulation. Mean-value models virtual prototypes of their engine provide the overall energy designs, automotive manufacturers consumption/production balance can obtain tremendous insight into the without considering the details of the behavior of the engine. This insight is intake/compression/ignition/exhaust particularly valuable during controller cycles. These models are particularly design and development, to maximize favored by engine control developers vehicle performance while because they deal only with the complying with governmental and properties of the system the ecological constraints. Doing this developers are interested in, and the analysis before investing in the physical models are faster to compute. prototyping stages has been proven to save significant time and substantially Note that because this model was reduce costs during the product created using proprietary customer data, development process. the actual values have been replaced with data from public sources. This article describes the development of a mean-value model of an internal combustion engine using MapleSim, Mean-Value IC Engine Model This model provides the overall power/ speed/torque/fuel consumption, given the mass flow of air/fuel gas. The gas flow is determined by the position of the throttle valve, which is set by a simplified engine controller that closes the loop between the actual and desired engine speeds. The engine model itself is composed of three main subsystems: the throttle, intake manifold, and engine power generation from the fuel combustion. Loading on the engine shaft is provided by a model of a dynamometer. Figure 1: Mean-value engine model in MapleSim The Throttle Subsystem The throttle subsystem calculates the air mass flow based on the throttle valve angle. For the purpose of the model, the angle is provided by the engine controller as an input signal. Based on the geometry of the throttle and valve, the effective throttle area (Athr) is related to the valve angle ( ) as follows: (Moskwa, 1988. Note all variable definitions are given in the glossary at the end of this article.) Figure 2: Throttle subsystem, with custom components created in Maple The mass flow rate itself is related to the effective throttle area and manifold pressure as follows: (Heywood, 1988) There are two parts to the relationship: subsonic and supersonic, determined by the ratio between the manifold pressure and ambient pressure at the entrance to the throttle. Mean-Value Internal Combustion Engine Model with MapleSimTM These equations were implemented as choking equation when the supersonic In MapleSim, you can review the Maple custom components in MapleSim by flow condition is exceeded. document that was used to create the simply entering the equations into a custom components by simply double- Maple document template that contains Note that the mass flow block requires clicking on a custom component. The the necessary tools for converting them two inputs: the throttle area (Athr) and document for computing the effective into a MapleSim block, with the neces- the manifold pressure (Pm), which is a throttle area is shown in Figure 3. sary inputs, outputs, and parameters. property fed back from the manifold The equations were implemented as a subsystem. The output signal is the piecewise function to switch to the resulting air/fuel mass flow ( ) through the throttle. Figure 3: Maple document implementing the throttle area equation The Manifold Subsystem The intake manifold has a significant effect on the gas flow and pressure to the engine cylinders. There are two physical effects that need to be included: 1. Manifold Pressure Physically, the intake manifold guides the air/fuel mixture into the cylinders but also causes an obstruction that reduces the pressure, and hence the mass flow, at the cylin- ders. The calculation of the manifold pressure (Pm) and mass flow ( ) is based on the ideal gas equation in derivative form by considering isothermal conditions in the intake manifold control volume (Hendricks, E., et al., 1996). and Figure 4: Intake manifold These include the volumetric efficiency ( ) which is described below. Again, these equations, including the differential equation for the manifold pressure, can simply be entered as they appear above into the Maple custom component docu- ment. The only additional element required is an initial value for the pressure. This can be entered as a parameter in the custom component block (set at slightly below atmospheric pressure). Mean-Value Internal Combustion Engine Model with MapleSimTM Figure 5: Manifold pressure and mass flow equations implemented in Maple as a custom component The inputs to the block are the engine speed (RPM), mass flow from the throttle, and volumetric efficiency from the lookup table. The outputs are the manifold pressure and mass flow going into the cylinders. 2. Volumetric Efficiency This is modeled as a lookup table of experimental values of volumetric efficiency ( ) over a range of en- gine speeds and manifold pressures, stored in an Excel® spreadsheet. The actual data values shown here have been changed for confidentiality reasons, but they give a reasonably good approximation to demonstrate the principles of its use. Figure 6: Volumetric efficiency lookup table Mean-Value Internal Combustion Engine Model with MapleSimTM The Engine Subsystem The engine subsystem considers the power generated through the combus- tion of the fuel in the gas mixture delivered to the cylinders, and accounts for thermal efficiency, friction and inertial losses in the engine and the inertial load at the drive shaft. The mean engine power subsystem contains the calculations for the thermal efficiency, indicated power generated from the combustion of the fuel, and lost power due to mechanical and pumping effects in the engine. The brake power – the indicated power without the lost power – is fed out to the engine subsystem. In Figure 7, the net power is computed at the interface between the output torque computa- tion (in the output torque subsystem) and the mechanical flange port at the far right. Figure 7: Engine subsystem 1. Thermal Efficiency The thermal efficiency ( ) is modeled using an empirically derived polynomial expression (Hendricks, E., et al., 1996), accounting for speed (n), manifold pressure (Pm), and air-fuel ratio ( ): where Figure 8: Mean engine power subsystem The coefficients bn , cn , and dn are typically generated from manufacturers’ testing data and are considered highly proprietary. For the purpose of this example, the coefficients given in Hendricks were used. A custom component was created using these equations, with air/fuel ratio ( ), engine speed ( n ), and manifold pressure (Pm) as inputs, returning thermal efficiency ( ) as the output. Mean-Value Internal Combustion Engine Model with MapleSimTM 2. Engine Power Calculation Engine power and speed calculations are based on the following engine equations (Hendricks, E., et al., 1996): and where and where and are all constants obtained by experiment. (Textbook values were used in this example.) A custom component was created based on these equations to calculate the net power. However, since the model needs to accommodate external loading, it was desirable to replace the empirical approximation for the load power (Pload) and the differential equation for the engine speed (n) with the computed load power and speed from the drive shaft. Load and Net Power Computation Up to this point in the project, the model has been developed as a signal-flow representation, with engine properties being transported from equation to equation (in custom components) using signal lines. However, one of the strengths of MapleSim is that engineering systems can be represented with connected components where the transfer of properties is implicit in the connections. This “acausal” approach makes it much easier to produce engineering models and has been used to connect the external load from a dynamometer model to the engine model. This means that the load power is implicitly determined and, hence, the engine speed can be computed simply by connecting a speed sensor block to the line that represents the drive shaft. In effect, this implements the speed equation from above: where Pnet = Pbrake - Pload = Pind - Ploss - Pload Figure 9: Available torque with power and speed sensors Mean-Value Internal Combustion Engine Model with MapleSimTM The main challenge was interfacing the signal-flow model with the acausal mechanical model. This was achieved by computing the brake torque ((Pind - Ploss)/n) from the engine and converting this to an acausal torque, applied to an inertia block that represents the internal engine inertia, then to a mechanical rotational flange for connection to the external load (see Figure 10). In Figure 9, the output torque subsystem is connected to the mechanical flange which represents the drive shaft from the engine. Inserted between the two flanges is a power sensor that provides the net power (Pbrake – Pload) and a speed sensor that provides the engine speed as a signal that is sent back to the engine power block to fulfill the requirements of the power equations. Figure 10: Engine torque. Signal-flow to acausal representation External Loading (Dynamometer) The engine power and speed are now represented at the drive shaft as available torque, which allows a mechanical load to be attached via a mechanical flange. This acausal connection makes the addition of loads to the system significantly easier than with signal-flow models. In future phases of this project, the transmission and drivetrain models can be very easily connected to the engine in this way. For the purpose of this phase of the Figure 11: Dynamometer model project, a simple dynamometer model is used to apply the external load to the engine (see Figure 11).
Details
-
File Typepdf
-
Upload Time-
-
Content LanguagesEnglish
-
Upload UserAnonymous/Not logged-in
-
File Pages12 Page
-
File Size-