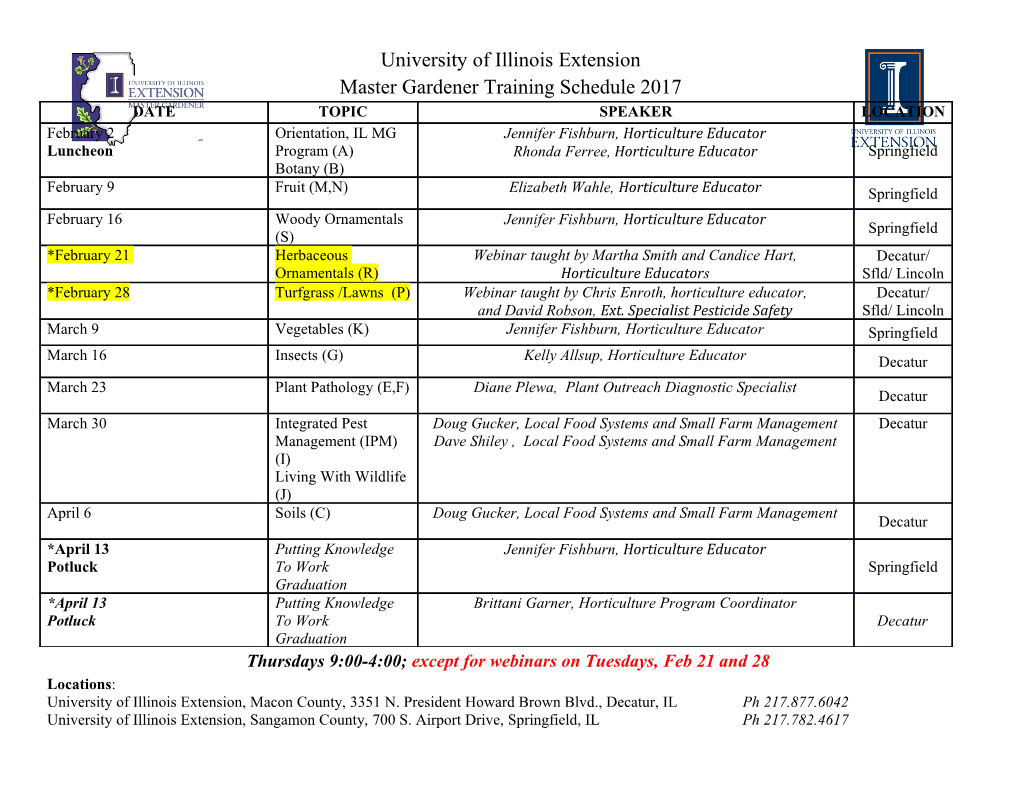
GAS TURBINE ENGINES The simplified operation of the gas turbine engine is as follows: 1. Air is taken in, and compressed to a high pressure. 2. The compressed air is then mixed with a fuel and ignited, producing high-velocity, high- pressure gas. 3. This gas is then used to turn a turbine, providing useful work, and the exhaust gases emitted, sometimes through a nozzle. The turbine itself is used to power the compressor, through the use of a coupling shaft between turbine and compressor. For this reason a starter motor must be employed in order to bring the engine up to speed when starting. Below is a diagrammatic representation of a gas turbine engine showing the fundamental processes: A useful way of looking at the workings of the gas turbine engine is to view it as following the same process as a reciprocating IC engine. Air is drawn in, compressed, ignited, expanded and exhausted in the both the reciprocating IC and gas turbine engines. The difference is that in a gas turbine engine these processes are not carried out in one cylinder, but rather are spread over different components of the engine. The three main stages of the engine are now examined in further detail. Compression In this stage either centrifugal or axial compressors are employed to compress the ambient air to a high pressure. Some of this air will then be fed into the combustion chamber, whilst some will be used to cool the turbine. The ratio of final pressure to ambient pressure is called the pressure ratio and for a modern engine may be as high as 40:1.Centrifugal compressors, although cheaper to manufacture, are less widely used because they are unable to achieve such high pressure ratios. An axial compressor consists of alternate rows of stationary and rotating aerofoil blades along the shaft of the compressor. In most gas turbine engines, there will be a multiple compression stage. This is because current designs do not allow for air to be compressed to a high enough ratio in only one stage. Further Design Considerations: The blades of the compressor need to be designed to be resistant to vibrations, and to be light. In recent years CAD (Computer Aided Design) has been pivotal in developing advanced blade design. However, losses are inevitably still incurred due to flow friction and turbulence associated with secondary swirls of air after each set of blades. In order to increase the efficiency of the compressor, spooled shafts can be used. In this system, a shaft driving the low pressure end of the compressor runs inside the main shaft through to the low pressure output of the turbine. This enables different stages of the compressor to run at different speeds, and can be used to increase efficiency. This describes a twin-spool set up, but triple-spool engines have also been constructed. Combustion In this stage the compressed air is mixed with a fuel (often Kerosine) and ignited by a continuously burning flame. The combustion, which burns the mixture at temperature of up to 2000 degrees, may be carried out in one, or a number of parallel chambers. The major design consideration is enabling the ignition flame to continue burning despite the fast flowing air around it. In a modern engine this may be achieved by creating a purposeful turbulence around the flame. Turbine In the turbine stage, the hot, high velocity combustion products are expanded through blades, turning the turbine and thus providing useful work. However, the combustion products must be cooled before entering the turbine stage, since the temperature the gas may reach would exceed the melting point of many of the turbine's components. This cooling is achieved by adding compressed air which has been diverted around the combustion chambers. In addition, the turbine blades themselves may be air-cooled internally, or by 'film' technology, where air is leaked from small pores creating a layer of cooled air around the blade. In many engines, there will be a number of turbine stages, so that the compressor can be driven at different speeds. As mentioned above, this can be achieved using spooled shafts. Furthermore, some systems will incorporate separate turbine stages, whereby one turbine will be used to drive the compressor, and another separate turbine will be used to power any external equipment. Overall design improvements Heat exchangers - This is whereby hot exhaust gases are run through a heat-exchanger with the compressed air. Therefore the heat energy of the compressed air entering the combustion chamber will be increased, so less fuel will be needed to provide the same output. The following design additions are specific to aircraft and are used to provide a particular function. Afterburners - This is where the exhaust gases following the turbine stage are re-ignited. This increases exhaust velocity and therefore thrust. This works particularly well in a turbofan engine, where there is an abundance of excess oxygen. Afterburners provide short term thrust increases and so are typically used in military aircraft which require good acceleration. Vectored thrust - This is where the discharge nozzle can be angled to provide thrust in angled directions. This was developed to enable aircraft to take-off on short runways, or even vertically. Perhaps the only example of a vertical take-off aircraft is the Harrier Jump-Jet, which uses the Pegasus Turbofan engine. Reverse thrust - This is where some, or all of the exhaust stream can be mechanically deflected to a forward direction, therefore slowing the aircraft. Reverse thrust is common on commercial aircraft and is used to provide additional braking on landing. What follows is calculations for the work output of a gas turbine, from a thermodynamic stance. In a coupled system, where the compressor is powered directly by the turbine, it can be stated that the total work output is, Total work output = Turbine output - Compressor work Compressor: For a rotary air compressor, commonly used in gas turbines, the work done by the compressor is, Where = mass of airflow per second Cpa = specific heat capacity of air (constant pressure) T2 = final temperature T1 = intake temperature Turbine: For the turbine the output can be found in a similar way as above, Where = mass of combustion products per second Cpt = specific heat capacity of combustion products T3 = intake (to turbine) temperature T1 = exhaust temperature Net Work: If we ignore the mass of the added fuel as negligible, which is a fair assumption given the quantity of air involved, we can say that, And also then that, fuel ignored, So, the n et work output is, GAS-TURBINE THEORY A simple gas turbine is comprised of three main sections a compressor, a combustor, and a power turbine. The gas-turbine operates on the principle of the Brayton cycle, where compressed air is mixed with fuel, and burned under constant pressure conditions. The resulting hot gas is allowed to expand through a turbine to perform work. In a 33% efficient gas-turbine approximately two / thirds of this work is spent compressing the air, the rest is available for other work ie.( mechanical drive, electrical generation) The image cannot be displayed. Your computer may not have enough memory to open the image, or the image may have been corrupted. Restart your computer, and then open the file again. If the red x still appears, you may have to delete the image and then insert it again. However there are variations... One variation of this basic cycle is the addition of a regenerator. A gas- turbine with a regenerator (heat exchanger) recaptures some of the energy in the exhaust gas, pre-heating the air entering the combustor. This cycle is typically used on low pressure ratio turbines. The image cannot be displayed. Your computer may not have enough memory to open the image, or the image may have been corrupted. Restart your computer, and then open the file again. If the red x still appears, you may have to delete the image and then insert it again. Turbines using this cycle are: Solar Centaur / 3500 horsepower class up to the General Electric Frame 5 Gas-turbines with high pressure ratios can use an intercooler to cool the air between stages of compression, allowing you to burn more fuel and generate more power. Remember, the limiting factor on fuel input is the temperature of the hot gas created, because of the metallurgy of the first stage nozzle and turbine blades. With the advances in materials technology this physical limit is always climbing. The image cannot be displayed. Your computer may not have enough memory to open the image, or the image may have been corrupted. Restart your computer, and then open the file again. If the red x still appears, you may have to delete the image and then insert it again. One turbine using this cycle is: General Electric LM1600 / Marine version A gas-turbine employing reheat. The image cannot be display ed. Your computer may not have enough memory to open the image, or the image may hav e been corrupted. Restart y our computer, and then open the file again. If the red x still appears, you may have to delete the image and then insert it again. The image cannot be displayed. Your computer may not have enough memory to open the image, or the image may hav e been corrupted. Restart y our computer, and then open the file again. If the red x still appears, y ou may hav e to delete the image and then insert it again. ¢ ¤ ¡ £ A Interc ¡ ed & Rec erated Turbine © ¦ § ¨ ¦ GAS-TUR ¥ E STOR The history of the gas turbine begins with a quest for jet propulsion.
Details
-
File Typepdf
-
Upload Time-
-
Content LanguagesEnglish
-
Upload UserAnonymous/Not logged-in
-
File Pages70 Page
-
File Size-