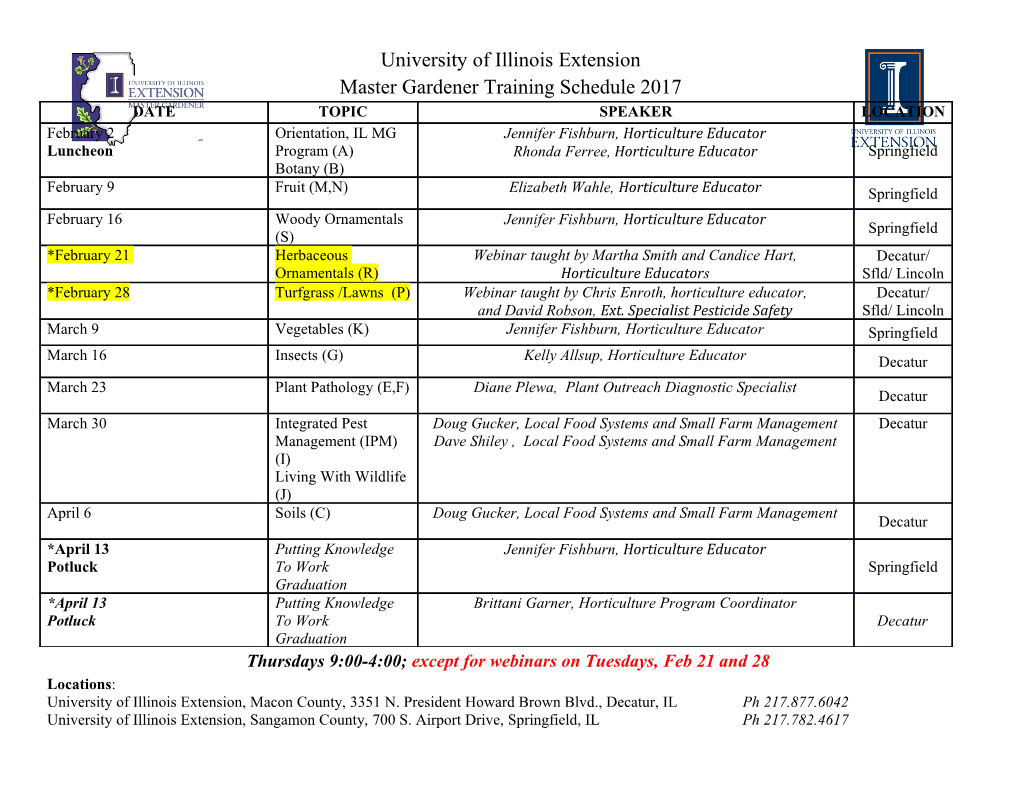
Multilateral Investment Guarantee Agency Environmental Guidelines for Petrochemicals Manufacturing Industry Description and Practices are available to manufacture the desired products. (Further details of typical processes Natural gas and crude distillates such as and products are provided in the annex.) naphtha (from petroleum refining) are used as feedstocks to manufacture a wide variety of Waste Characteristics petrochemicals which are in turn used for the manufacture of a variety of consumer goods. Fugitive air emissions from pumps, valves, The description of petrochemical processes and flanges, storage tanks, loading and unloading products presented here is for illustrative operations, and wastewater treatment are of purposes only. The basic petrochemicals greatest concern. Some of the compounds manufactured by cracking, reforming, and released to air are carcinogenic or toxic. other processes include olefins (including Ethylene and propylene emissions are of ethylene, propylene, butylenes, and butadiene) concern because of their fate processes which and aromatics (including benzene, toluene, and lead to the formation of oxides which are xylenes). The capacity of naphtha crackers is extremely toxic. Compounds considered generally of the order of 250,000 to 750,000 carcinogenic that may be present in air metric tons per year (tpy) of ethylene emissions include benzene, butadiene, 1,2- production. Some petrochemical plants also dichloroethane, and vinyl chloride. A typical have alcohol and oxo-compounds naphtha cracker at a petrochemical complex manufacturing units on-site. The base may annually release about 2,500 emetric tons petrochemicals or products derived from them of alkenes (such as propylenes and ethylene), along with other raw materials are converted when producing 500,000 metric tons of to a wide range of products including resins ethylene. Boilers, process heaters, flares, and and plastics (such as low density polyethylene other process equipment (in some cases may (LDPE), high density polyethylene (HDPE), include catalyst regenerators)are responsible linear low density polyethylene (LLDPE), for the emission of particulates, carbon polypropylene, polystyrene, and polyvinyl monoxide, nitrogen oxides (200 metric tons per chloride (PVC)); synthetic fibers (such as year), and sulfur oxides (SOx) (600 metric tons polyester and acrylic); engineering polymers per year based on a 500,000 metric tons per (such as acrylonitrile butadiene styrene (ABS)); year of ethylene capacity). rubbers (including styrene butadiene rubber The release of volatile organic compounds (SBR) and polybutadiene (PBR)); solvents; (VOCs) to air depends on the products handled industrial chemicals (including those used for at the plant and may include acetaldehyde, the manufacture of detergents such as linear acetone, benzene, toluene, trichloroethylene, alkyl benzene (LAB), coatings, dyestuff, trichlorotoluene, and xylene. VOC emissions agrochemicals, pharmaceuticals, and are mostly fugitive and depend upon the explosives). A number of alternative methods production processes, material handling and 461 Petrochemicals Manufacturing 462 effluent treatment procedures, equipment environmental hazard releasing large maintenance, and climatic conditions. VOC quantities of pollutants and products into the emissions from a naphtha cracker range from environment. Plant safety and fire prevention and 0.6 to 10 kilograms (kg) (75% are alkanes, 20% control procedures should be in place. unsaturated hydrocarbons about half of these is ethylene, and remaining 5% are aromatics) Pollution Prevention and Control per metric ton of ethylene; 0.02 to 2.5 kg (45% of these being ethylene dichloride, 20% being Petrochemical plants are typically large and vinyl chloride, and 15% being chlorinated complex, where the combination and sequence organics) per metric ton of product in a vinyl of processes is usually very specific to the chloride plant; 3-10 kg per metric ton of characteristics of the products manufactured. product in a SBR plant; 0.1-2 kg per metric ton Specific pollution prevention or source of product in ethyl benzene plant; 1.4-27 kg per reduction measures are best determined by metric ton of product in ABS plant; 0.25-18 kg technical staff. However, there are a number of per metric ton of product in a styrene plant; broad areas where improvements are often and 0.2-5 kg per metric ton of product in a possible and site specific emission reduction polystyrene plant. measures in these areas should be designed Petrochemical units generate wastewaters into the plant and targeted by plant from process operations (such as vapor management. condensation), cooling tower blow down, and Areas where effort should be concentrated storm water run off. Process wastewaters are include: generated at a rate of about 15 cubic meters per 3 hour (m /hr) (based on a 500,000 metric tons Reduction of Air Emissions per year ethylene production) and may contain biochemical oxygen demand (BOD ) (100 5 • Minimize the leakages of volatile organics mg/L), COD (1,500-6,000 mg/L), suspended (including benzene, vinyl chloride, and solids (100-400 mg/L), and oil and grease (30- ethylene oxide) from valves, pump glands (use 600 mg/L). Phenol levels of up to 200 mg/L mechanical seals), flanges, and other process and benzene levels of up to 100 mg/L may also equipment by following good design practices be present. and equipment maintenance procedures. Petrochemical plants also generate solid • Use mechanical seals, where appropriate. wastes and sludges, some of which may be • Minimize losses from storage tanks, considered hazardous because of the presence product transfer areas, and other process areas of toxic organics and heavy metals. Spent by adopting methods such as vapor recovery caustic and other hazardous wastes such as systems and double seals (for floating roof distillation residues associated with units tanks). handling acetaldehyde, acetonitrile, benzyl • Recover catalysts and reduce particulate chloride, carbon tetrachloride, cumene, emissions. phthallic anhydride, nitrobenzene, methyl • Use low NO burners to reduce NO ethyl pyridine, toluene diisocyanate, x x emissions. trichloroethane, trichloroethylene, • Optimize fuel usage. perchloroethylene, aniline, chlorobenzenes, • In some case, organics that cannot be dimethyl hydrazine, ethylene dibromide, recovered, are effectively destroyed by routing toluenediamine, epichlorohydrin, ethyl them to flares and other combustion devices. chloride, ethylene dichloride, and vinyl chloride may be generated in significant Elimination/Reduction of Pollutants quantities. Accidental discharges as a result of • Use non-chrome based additives in abnormal operation especially from cooling water. polyethylene and ethylene-oxide-glycol plants • Use long life catalysts and regeneration to in a petrochemical complex can be a major extend the cycle. 463 Petrochemicals Manufacturing Recycling/Reuse Treatment Technologies • Recycle cooling water and treated Air Emissions wastewater to the extent feasible. • Recover and re-use spent solvents and Control of air emissions normally includes the other chemicals to the extent feasible. capturing and recycling or combustion of emissions from vents, product transfer points, Improved Operating Procedures storage tanks, and other handling equipment. Catalytic cracking units should be provided • Segregate process wastewaters from with particulate removal devices. Particulate stormwater systems. removal technologies include fabric filters, • Optimize tank and equipment cleaning ceramic filters, wet scrubbers, and electrostatic frequency. precipitators. Gaseous releases are minimized • Prevent solids and oily wastes from by condensation, absorption, adsorption entering the drainage system. (activated carbon, silica gel, activated alumina, • Establish and maintain an Emergency and zeolites), and in some cases using Preparedness and Response Plan. biofiltration and bioscrubbing (using peat/heather, bark, composts, and bioflora for Target Pollution Loads treating biodegradable organics), and thermal decomposition. Implementation of cleaner production processes and pollution prevention measures Liquid Effluents can provide both economic and environmental benefits. The following production-related Petrochemical wastewaters often require a targets can be achieved by measures such as combination of treatment methods to remove those detailed in the previous section. The oil and other contaminants before discharge. figures relate to the production processes Separation of different streams (such as before the addition of pollution control stormwater) is essential to minimize treatment measures. requirements. Oil is recovered using separation A good practice target for petrochemical techniques. For heavy metals, a combination of complex is that the total organic emissions oxidation/reduction, precipitation, and (including VOCs) from the process units be filtration is used. For organics, a combination reduced to 0.6% of the throughput. Target of air or steam stripping, granular activated maximum levels for air releases of ethylene, carbon, wet oxidation, ion exchange, reverse ethylene oxide, vinyl chloride, and 1,2- osmosis, and electrodialysis is used. A typical dichloroethane are 0.06 kg, 0.02 kg, 0.2 kg, and system may include neutralization, 0.4 kg per ton of product. Methods of coagulation/flocculation, estimating these figures include ambient and flotation/sedimentation/filtration, emissions monitoring, emission
Details
-
File Typepdf
-
Upload Time-
-
Content LanguagesEnglish
-
Upload UserAnonymous/Not logged-in
-
File Pages7 Page
-
File Size-