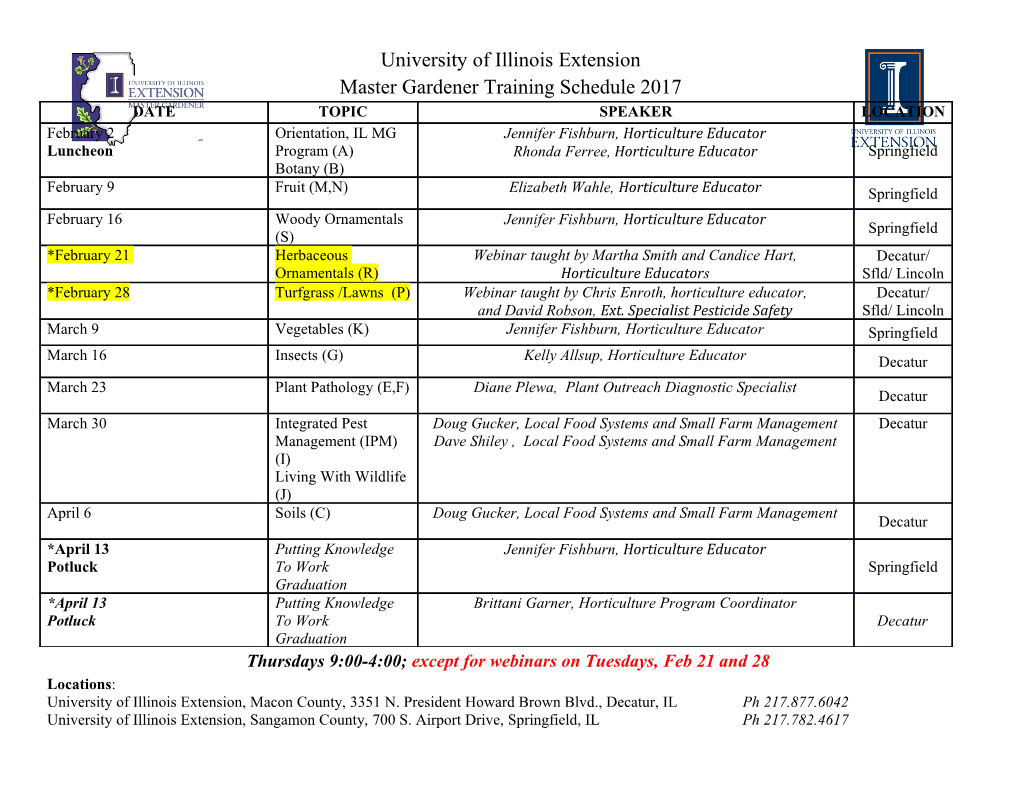
Weld Residual Stress Finite Element Analysis Validation Introduction and Overview June 14-15, 2011, Rockville, MD Paul Crooker EPRI Howard Rathbun U.S. Nuclear Regulatory Commission Introduction • Welcome • Introduction by meeting attendees – Names and affiliations • Agenda – Revised since Public Meeting Announcement – Hardcopy available • Review revised agenda © 2010 Electric Power Research Institute, Inc. All rights reserved. 2 This is a Category 2 Public Meeting • Category 1 – Discussion of one particular facility or site • Category 2 – Issues that could affect multiple licensees • Category 3 – Held with representatives of non-government organizations, private citizens or interested parties, or various businesses or industries (other than those covered under Category 2) to fully engage them in a discussion on regulatory issues © 2010 Electric Power Research Institute, Inc. All rights reserved. 3 Program Overview •Scientific Weld Specimens •Fabricated Prototypic Nozzles •Phase 1A: Restrained Plates (QTY 4) •Type 8 Surge Nozzles (QTY 2) •Phase 1B: Small Cylinders (QTY 4) •Purpose: Prototypic scale under controlled NRC EPRI - - •Purpose: Develop FE models. conditions. Validate FE models. Phase 2 Phase Phase 1 Phase •Plant Components •Plant Components •WNP-3 S&R PZR Nozzles (QTY 3) •WNP-3 CL Nozzle (QTY 1) •Purpose: Validate FE models. •RS Measurements funded by NRC EPRI EPRI - - •Purpose: Effect of overlay on ID. Phase 3 Phase Phase 4 Phase © 2010 Electric Power Research Institute, Inc. All rights reserved. 4 Goals of the Meeting • Focus on finite element modeling techniques – What works well, what doesn’t • Allow meeting participants to express their views • Day 1: Present modeling and measurement results • Day 2: Discuss the implications of the findings • Present plans for documentation • Future work opportunities © 2010 Electric Power Research Institute, Inc. All rights reserved. 5 Welding Residual Stress Validation Program Phase 1 Summary Presented To: Welding Residual Stress Validation Experts Meeting Presented By: John Broussard Dominion Engineering, Inc. June 14, 2011 12100 Sunrise Valley Dr. #220 Reston, VA 20191 703.657.7300 www.domeng.com Phase 1 Weld Specimen Design Phase 1A Phase 1B Restrained Plates Cylinders . Fabricate and measure RS in simple Geometry 0.6" Thk, 0.4" Groove, 14" Long 6.51" OD x 0.47" Thick experimental specimens in order to Simplest Geometry Increasing Specimen Complexity develop and refine FE models Base Metal: 304L SS Base Metal: 304L SS, CS . Scientific Design Approach: Material Weld Metal: Alloy 82 Weld Metal: Alloy 82 – Investigate how weld parameters and Buttering: Alloy 82 Fix Geometry Fix Weld Parameters geometry affect RS distribution Variables – Representative weld configurations Vary Weld Parameters Vary Configuration – Controlled fabrication P-3: Base Case - 11 passes C-1: SS to SS – Maximize region of fully-developed stress P-4: Incr. Heat Input - 7 passes C-3: Buttered CS to SS w/ PWHT Specimens – Facilitate multiple RS measurements P-5: Incr. Heat Input - 7 passes C-4: Buttered CS to SS w/o PWHT . Investigate influence on RS state of: P-6: Decr. Heat Input - 23 passes C-5: Add SE and Repair to C-4 Aluminum backing plate is fairly Machine beam windows allow – Phase 1A: weld parameter variation Allow ND transparent to neutrons measurement of hoop strain • Current and wire feed rate Fixture design preserves original C-6 has manual 90° 75% TW ID • Torch speed Misc. – Phase 1B: weld configuration stress state. Repair Weld. Groove machined. • Buttering • Post-Weld Heat Treatment (PWHT) • Safe-End and SS weld • Repair Weld 2 Phase 1 Analysis Summary Measurements Performed Phase 1A Plates Measured Specimens RS Measurement Method Vendor Location Directions Measured P-3 P-4 P-5 P-6 Longitudinal Neutron Diffraction: ORNL 45 Point Grid on Cross-section Plane Transverse XXXX Basic Measurements Normal Neutron Diffraction: 7 Depths down Weld Centerline ORNL 6 Directions X Full Strain Tensor 2 Depths in Base Metal Longitudinal Neutron Diffraction: 8 Longitudinal Locations, ORNL Transverse X Longitudinal Traverse 3 Depth in WM & 3 Depths in BM Normal Longitudinal U of Deep Hole Drilling 1 Hole through Centerline of Weld Transverse X Bristol In-plane Shear 7 Surface Points Across Weld Longitudinal X-ray Diffraction TEC XXXX On Topside of Specimen Transverse Longitudinal 7 Surface Points Across Weld Surface Hole Drilling LTI Transverse XX X On Topside of Specimen In-plane Shear 2 Longitudinal Positions, Longitudinal Ring-Core LTI Both down Weld Centerline Transverse XX on Topside of Specimen In-plane Shear Slotting Hill Eng. 4 Transverse Measurement Slots Transverse X 1 Longitudinal Measurement Slice Longitudinal Contour Hill Eng. X 1 Transverse Measurement Slice Transverse ORNL: Oak Ridge National Laboratory TEC: Technology for Energy Corporation LTI: Lambda Technology, Inc. Hill Eng: Hill Engineering, LLC 3 Phase 1 Analysis Summary Plate RS Measurement Locations General Plate Arrangement (P-4 Shown) Contour Transverse - one plate Contour Longitudinal - full cross section - one plate ND Locations - all plate specimens - longitudinal, transverse, normal directions 4 Phase 1 Analysis Summary Measurements Performed Phase 1B Cylinders Measured Specimens RS Measurement Method Vendor Location Directions Measured C-1 C-3 C-4 C-5 C-5R Hoop Neutron Diffraction: ORNL 80 Point Grid on Cross-section Plane Axial XXXXX Basic Measurements Radial Neutron Diffraction: Stepped every 5° for 90° in Normal Weld ORNL Axial Strain X Axisymmetry Study Stepped every 5° for 70° in Repair Weld Hoop Deep Hole Drilling VEQTER 1 Hole through Centerline of Weld Axial XX XX In-plane Shear EPRI-CLT 10-11 Surface Points Across Weld Hoop X X X X-ray Diffraction & on OD & ID of Specimen Axial (EPRI) (EPRI) (TEC) TEC 2 Longitudinal (Hoop) Meas. Slices Hoop Contour Hill Eng. X 2 Transverse (Axial) Meas. Slices Axial ORNL: Oak Ridge National Laboratory TEC: Technology for Energy Corporation LTI: Lambda Technology, Inc. EPRI-CLT: EPRI Charlotte Hill Eng: Hill Engineering, LLC 5 Phase 1 Analysis Summary Cylinder RS Measurement Locations General Cylinder Arrangement (C-3 Shown) Contour Hoop Contour Axial Contour Axial - full cross section - one cylinder - one cylinder - one cylinder OD ID ND Locations DHD and iDHD - all cylinder specimens - all cylinder specimens - hoop, axial, radial directions 6 Phase 1 Analysis Summary Surface Stress Measurement Results Plate P-4, Weld Centerline 500 200 XRD 400 HD 100 300 0 RC Slitting 200 -100 100 RC -200 HD 0 Transverse Stresses (MPa) Stresses Transverse Longitudinal Stresses (MPa) Stresses Longitudinal XRD X-ray Diffraction -300 Ring-Core -100 X-ray Diffraction Ring-Core Surface Hole Drilling Surface Hole Drilling Slitting -200 -400 -2.00 -1.50 -1.00 -0.50 0.00 0.50 1.00 -2.00 -1.00 0.00 1.00 2.00 3.00 4.00 Depth from Plate Top Surface (mm) Depth from Plate Top Surface (mm) 7 Phase 1 Analysis Summary Stress Measurements and FEA Predictions . Results from Plate P-4 and Cylinder C-3 presented . Four sets of model results compared identified “A” through “D” – All models two dimensional plane strain (plate) or axisymmetric (cylinder) – Modeler’s best judgment for mesh, thermal inputs based on fabrication data – All models apply power generation as a function of time for thermal model • Roughly same amount of total energy input consistent with weld process – Model A: ANSYS, elastic perfectly-plastic hardening – Model B: ABAQUS, isotropic hardening law – Model C: ABAQUS, isotropic hardening law – Model D: ABAQUS, kinematic hardening law . Measurements performed at facilities identified “A” through “C” – No correlation between modelers “A” through “D” and facilities “A” through “C” – Facility A: contour method only – Facility B: neutron diffraction only – Facility C: contour method and neutron diffraction 8 Phase 1 Analysis Summary Plate P-4 Measurement and FEA Results FEA Model A FEA Model B FEA Model A FEA Model B FEA Model C FEA Model D FEA Model C FEA Model D Contour, Facility A Contour, Facility C Contour, Facility A Neutron Diff, Facility B Neutron Diff, Facility B Neutron Diff, Facility C Neutron Diff, Facility C 600.0 300.0 500.0 200.0 400.0 100.0 300.0 0.0 200.0 -100.0 100.0 Longitudinal Mpa Stress, Longitudinal -200.0 0.0 Stress, Mpa Transverse -100.0 -300.0 -200.0 -400.0 -4.00 -2.00 0.00 2.00 4.00 6.00 8.00 10.00 12.00 14.00 16.00 -4.00 1.00 6.00 11.00 16.00 Distance from Plate Top Surface, mm Distance from Plate Top Surface, mm 9 Phase 1 Analysis Summary Cylinder C-3 Measurement and FEA Results FEA Model A FEA Model B FEA Model C FEA Model A FEA Model B FEA Model C Contour - A DHD / iDHD Neutron Diff, Facility B Contour - A DHD / iDHD Neutron Diff, Facility B 400.0 600.0 300.0 500.0 200.0 400.0 100.0 300.0 0.0 200.0 -100.0 100.0 Mpa Stress, Axial Hoop Stress, Stress, Mpa Hoop -200.0 0.0 -100.0 -300.0 -200.0 -400.0 0.00 2.00 4.00 6.00 8.00 10.00 12.00 14.00 0.00 2.00 4.00 6.00 8.00 10.00 12.00 14.00 Distance from OD, mm Distance from OD, mm 10 Phase 1 Analysis Summary Three Dimensional Plate Model . Three dimensional model prepared for Plate P-4 . Progressive block dump for thermal model, five blocks lengthwise for each weld pass . Results are identical for the 2D/3D in the weld, with some differences far field in the longitudinal stresses 11 Phase 1 Analysis Summary Conclusions . Surface stress measurements from the plates demonstrate that additional investigation is needed into surface measurements of welded locations . Bead geometry arrangements played a role in scatter among cylinder model stress results – Plate weld cavity did not change shape during welding consistent beads among modelers – Cylinder weld cavity changed shape during welding modelers assumptions for bead shape varied .
Details
-
File Typepdf
-
Upload Time-
-
Content LanguagesEnglish
-
Upload UserAnonymous/Not logged-in
-
File Pages298 Page
-
File Size-