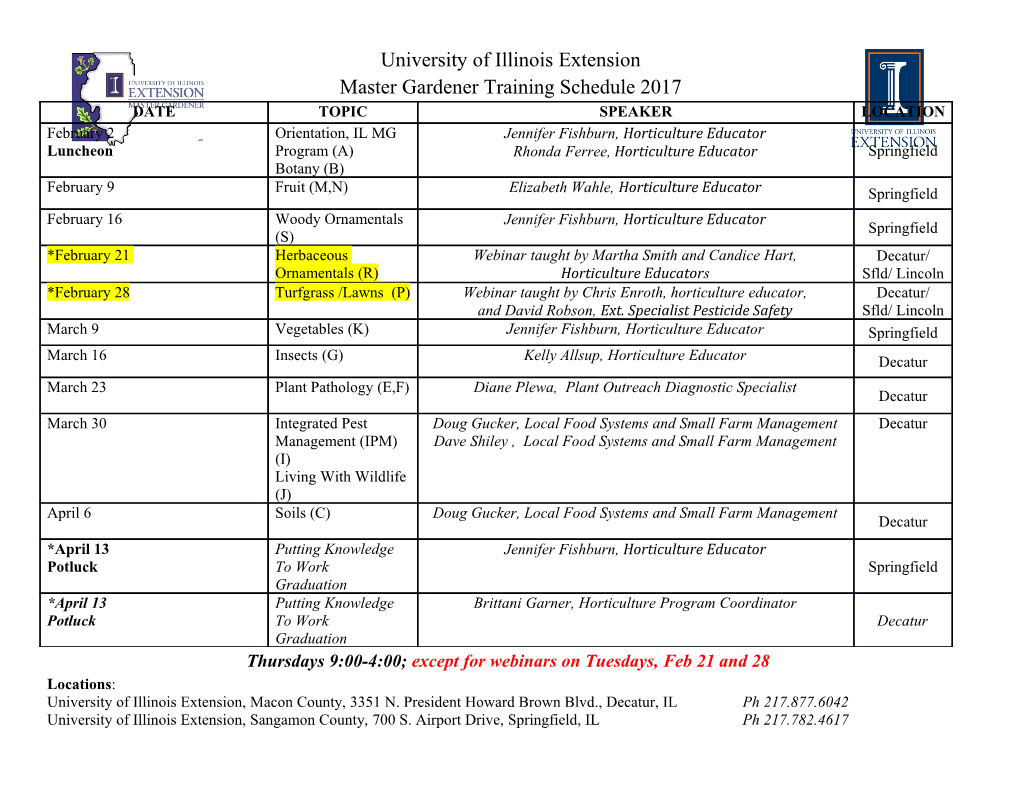
SIMULATIONS OF STEP-LIKE BRAGG GRATINGS IN SILICA FIBERS USING COMSOL A Thesis Presented to The Graduate Faculty of The University of Akron In Partial Fulfillment of the Requirements for the Degree Master of Science Rasika Dahanayake May, 2016 SIMULATIONS OF STEP-LIKE BRAGG GRATINGS IN SILICA FIBERS USING COMSOL Rasika Dahanayake Thesis Approved: Accepted: ______________________________ ______________________________ Advisor Dean of the College Dr. Sergei F. Lyuksyutov Dr. John Green ______________________________ ______________________________ Faculty Reader Dean of the Graduate School Dr. Robert R. Mallik Dr. Chand Midha ______________________________ ______________________________ Faculty Reader Date Dr. Alper Buldum ______________________________ Department Chair Dr. David Steer ii ABSTRACT The purpose of the research was to build a model for simulations of Fiber Bragg Grating (FBG) sensors under harsh conditions. In this thesis we were studying the 2D model of a fiber under different wavelength EM radiation (530 nm, 1310 nm, and 1530 nm), also we introduced a novel 3D model of FBG. The 3D model of the FBG is used to study the modes of the fiber under varying grating period (1310 nm, 908.62 nm, and 454.31 nm) and with varying number of slabs in the grating (10, 50, and 100). The novelty of this work is an introduction of step-like profile in FBGs. Potentially, this approach may be used for experimental high temperature sensing under harsh conditions. iii ACKNOWLEDGEMENTS First I would like to thank Dr. Sergei Lyuksyutov for being my advisor and taking me into your research group. I was able to learn and grow under your guidance and advice during the project and throughout my time at the University of Akron. Then I would like to thank Professor Robert Mallik and Professor Alper Buldum for being kind enough to be on my graduate thesis committee and especially for valuable advice on improvements on my thesis. I would also like to thank colleagues Jeff McCausland, Sajeevi Withanage, Pedram Esfahani and Liudmyla Barabanova for the help and guidance during my time at the University of Akron and on my research. I am grateful to my parents for all the love and guidance they have given me throughout my life. Finally, I would like to thank my wife Ruvini for the love and support. You make everything in my life better. iv TABLE OF CONTENTS Page LIST OF TABLES………………………………………………..….……...….….…vii LIST OF FIGURES……………………………………………………....…....……viii CHAPTER I. INTRODUCTION……………………………………………………………….…...1 II. BACKGROUND…………………………………………………..………………...3 2.1. Optical Fibers………………………………………………………….…..3 2.2. Geometrical Optics…………………………………………….………….5 2.2.1. Numerical Aperture………………………………..…………...7 2.3. Wave Optics……………………………………………….…………….…8 2.3.1. Waveguides…………………………………………….……….11 2.3.2. Coupled-Mode theory………………………………………....15 2.4. Fiber Bragg Gratings………………………………………………..…..20 2.4.1. Origin and Inscribing FBG’s………………………………....20 v 2.4.2. Types of FBG’s…………………………………….…………...25 2.4.2.1. By the varying conditions of gratings production.25 2.4.2.2. By the Structure (composition) of the gratings….27 2.4.3. Photosensitivity………………………………….….………....31 2.4.4. Applications of FBG’s……….………….…………….…...…..35 2.5. Finite Element Analysis and COMSOL Multiphysics programming……………………………………………………….………….37 III. PROCEDURE…………………………………………………………………….43 3. Simulations Using COMSOL……………………………..………………43 3.1. 2D Step index fiber Model……………………...………….…………....44 3.2. 3D Model for Fiber Bragg grating………………….…….…………....49 IV. RESULTS & DISCUSSIONS……………………………………….……….....61 4.1. Results of the 2D model…………………………………………...……61 4.2. Results of the 3D model……………………………………...…………69 V. CONCLUSIONS…..………………………………………………........…………82 REFERENCES…………………………………………………………….....………84 vi LIST OF TABLES Table Page 3.1 Table of Parameters for the 2D fiber Simulation……………..…………….44 3.2 Table of Parameters for the 3D fiber Simulation……………………..…….50 4.1 Stable modes sustained by the fiber in the 2D model……………..…………68 4.2 Simulation results of the fiber with 10 gratings for different grating periods……………………………………………………………………...…………..78 4.3 Simulation results of fiber’s with grating period Λ = 454.31 nm, and different number of slabs…..…………………………………………...……………79 4.4 Simulation results for the 3D model……………………………………………80 vii LIST OF FIGURES Figure Page 2.1.1 A schematic representation of an optical fiber, with a core of refractive index n1 and a cladding of refractive index n2, the fiber is in air, which has a refractive index of n0……………………………………………….………………..…..………...4 2.2.1 A schematic representation of light wave propagating along a fiber…..…5 2.2.2 Optical fiber with Cartesian coordinates (x,y,z) and Cylindrical coordinates (r,θ,z)………………………………………………………………………9 2.3.1 These are several of the electric field patterns for different LP modes in a fiber. Red is for positive and blue is for negative values of the electric field [22]............................................................................................................………19 2.4.1 The Original setup used by Meltz, Morey and Glenn [20].………………..22 2.4.2 The interference pattern created inside of the fiber [21].……………..….22 2.4.3 Phase Mask technique used to fabricate gratings in a fiber [23].………..24 2.4.4 Representation of uniform refractive index profile FBGs [30]..…………28 2.4.5 Apodized refractive index profile FBGs [30].…………….………………..30 2.4.6 The 3D Tetrahedral crystal structure of silica [35].……………….......…..32 2.4.7 Graphical representation of “wrong bonds” broken under exposure of UV light. (a) Wrong bonds structure, (b) GeE’ structure, (c) oxygen vacant silicon atom, and (d) free electron released from the reaction…………………………..33 viii 2.4.8 The defect Ge(1) in germania-doped silica fiber……………………………34 2.4.9 The defect Ge(2) in germania-doped silica fiber….………………………...34 2.4.10 Schematic representation of the FBG experimental setup [38]………...35 2.4.11 Diagram of the area (A) in the interval between -1 to 1. The area under the function y is found by the integration [36]…………….…………………...…38 2.4.12 Graphical representation of numerical integration of the calculation of A, changing with the number of subsections used [36].………………………… 40 3.1 Basic model of the 2D fiber. Center circle is the core and the bigger circle is the cladding……………………………………………………………………...….45 3.2 A close up of the triangular shaped mesh used for the 2D model………….48 3.3 The 3D model of the fiber……………………………………………………...…53 3.4 The 3D model of the single grating with thickness Λ =454.31 nm……...….54 3.5 The 3D model of the FBG with 10 slabs….………………………….…..…….55 3.6 The 3D model of the FBG with 50 slabs….…………………….……..............56 3.7 The 3D model of the FBG with 100 slabs…..………………….…….………...56 3.8 The grating with of the FBG with 10 slabs. Where the slabs in the core with even number is assigned with the core material and the odd number is assigned with grating material. The outer was cylinder was assigned with the material of the cladding……………………………………………...…..….……….57 3.9 The grating with of the FBG with 50 slabs with each even numbered disk assigned with the core material and the odd numbered disk assigned with grating material ……………………………………………………...……...............58 ix 3.10 The grating with of the FBG with 100 slabs with each even numbered disk assigned with the core material and the odd numbered disk assigned with grating material …………………………………………………………….………...58 3.11 The tetrahedral mesh on the 3D model. Since the light propagates through the core, it has a smaller mesh to increase the accuracy of calculations. Cladding was given a larger mesh to decrease the unnecessary use of the computer power……………………………….………………………………………59 3.12 A close up of the tetrahedral shaped mesh used for the 3D model……....60 4.1 LP01 mode experimental [39] on the left compared to simulated result on the right………………………………………………….………………………..……62 4.2 LP12 mode experimental [39] on the left compared to simulated result on the right………………………………………………….……………………………..62 4.3 LP21 mode experimental [39] on the left compared to simulated result on the right………………………………………………….……………………………..62 4.4 LP01* (donut shape) mode experimental [40] on the top left compared to simulated results of a few modes on the top right and on bottom, the simulated results have the same outer diameter but the inner diameter is changing………………………………………………………………………………..63 4.5 LP41 mode experimental [39] on the left compared to simulated result on the right ………………………………………………………………………………..63 4.6 LP51 mode experimental on the left compared to simulated result on the right……………………………………………………………………………………..64 4.7 LP01 mode experimental [39] on the left compared to simulated result on the right…………………………………………………….……………………..……65 4.8 LP02 mode experimental [39] on the left compared to simulated result on the right…………………………………………………….……………………..……65 x 4.9 LP12 mode experimental [39] on the left compared to simulated result on the right…………………………………………………….………………….....……65 4.10 LP01* (donut shape) mode experimental [40] on the top left compared to simulated results of few modes on the top right and on bottom……………………………………………………………………………..……66 4.11 LP01 mode experimental [39] on the left compared to simulated result on the right……………………………………………………..…………..………..……67 4.12 LP02 mode experimental [39] on the left compared to simulated result on the right……………………………………………………..…………..………..……67 4.13 Incident wave of the fiber with no FBG…………………………………...….70 4.14 LP11 mode experimental [39] on the left compared to simulated result of the
Details
-
File Typepdf
-
Upload Time-
-
Content LanguagesEnglish
-
Upload UserAnonymous/Not logged-in
-
File Pages99 Page
-
File Size-