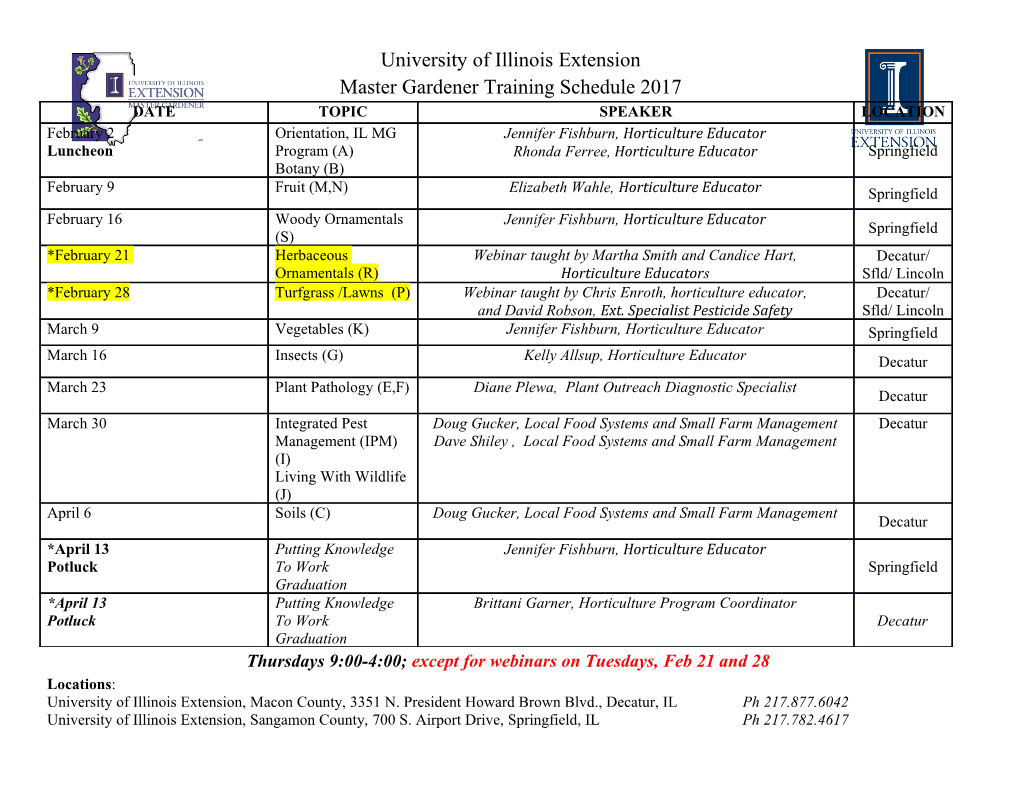
https://ntrs.nasa.gov/search.jsp?R=19740027166 2020-03-23T02:10:34+00:00Z NASA CR-134596 FRACTURE CONTROL METHODS FOR SPACE VEHICLES Volume I Fracture Control Design Methods BY A.F. Liu REPRODUCED BY NATIONAL TECHNICAL INFORMATION SERVICE U. S. DEPARTMENT OF COMMERCE SPRINGFIELD, VA. 22161 Cr; OF: PI *z1-1 m Ff 1x1 t.Q 1-1 Prepared for -4 = i a), mkrzr * I.nmu.5dw NATIONAL AERONAUTICS AND SPACE ADMINISTRATION =lIJ-1 I-I U .ri rn+mor! r Filffiid I IrlII-U Pi U U 4 1-rl 5 5 t PIO-Qh NASA Lewis Research Center Contract NAS 3-16765 FRACTURE CONTROL METHODS FOR SPACE VEH l CLE S Volume I Fractu re Control Design Methods by A. F. Liu Contract NAS3- 16765 NASA Lewis Research Center Cleveland, Ohio August 1974 * 1 Report No 2 Government Access~onNo 3 Reclptent s Cataloq No NASA CR-134596 4 Tttle and Subt~tle 5 Report Date Fracture Control Methods for Space Vehicles Volume I, August 19 74 Fracture Control Design Methods 6 Perforrntng Organlzatton Code 7 Author(s1 A.F. Liu 8 Perforrn~ngOrganlzatlon Report No SD 73-SH-0171-1 9 Perform~ngOrgantzatlon Name and Address 10 Work Unit No Space Division Rockwell International Corporation 11 Contract or Grant No Downey, CA 90241 NAS 3-16765 12 Sponsor~ngAgency Name and Address 13 Type of Report and Pertod Covered National Aeronautics and Space Administration Contractor Report .June 1972 through March 1974- 21000 Brookpark Rd. 14 Sponsortng Agency Code Lewis Research Center, Cleveland, OH 44135 15 Supplementary Notes Project Manager, Gordon T. Smith NASA Lewis Research Center Cleveland, OH 44135 16 Abstract This report is concerned with a systematic approach for applying methods fcr fracture control in the structural components of space vehicles. Four niaj~r steps are required to complete the fracture control sequence. The first step is to define the primary load-carrying structural elements and the type of load, environment, and design stress levels acting upon them. The second step is to identify the potentiai fracture-critical parts by means of a selection logic flow diagram. The third step is to evaluate the safe-life and fail-safe capabilities of the specified part. The last step in the sequence is to apply the control procedures that will prevent damage to the fracture-critical parts. The fracture control methods discussed herein include fatigue design and analysis methods, methods for preventing crack-like defects, fracture mechanics analysis methods, and nondestructive evaluation methods; however, emphasis is placed on the fracture mechanics analysis methods. To illustrate the use of fracture mechanics methodology, an example problem is presented for evaluation of the safe-crack-growth capability of the Space Shuttle crew compartment skin structure. PRICES SU?J:- - 17 Key words (Suggested by Author(s) 18 Dlstr~buttonStatement Fracture Mechanics Space Vehicle Structure Unclassified, Unlimited Fracture Control Procedures 19 Secur~tyClasstf (of thts report) 20 Securtty Class~f (of thts page) 21 No of Pages 22 Prtce' Unclassified Unclassified The work tlescribcd in this report was pc,rfor~ncdby the Spdce I>i\.ision of Rockwcll Intcrnat~onalCorporation under Contract NAS 3- 1076 5, T'racture Control Methods for Space Shuttle Vt.hiclcs, for the 1,cn.i~1lc.st arc]) Ccnter of the National Aeronautics and Spacc Aclministration. TJle ~n\lt.stigatjon\(as contlucted undcr the technical direction of Mr. Cortlon T. St111th of NASA/ LeRC. The project study manager at the Space I>i\~isjonof f~ocl<~'cll International Corporation was Mr. A. F. I,iu, nit11 Dr. Paul C. I'aris of Dcl Research Corporation and Dr. Matthew Crca~c,rof JIc1 West Associates, Inc. , acting as primary technical consultants, This report consists of three volumes: Volume I. Fracturcl Control Design h/lcthorls (prc,pared by A. F. 1,iu) Volume 11. Assessment of Fracturc Mech;rnics Tectinology for Space Shuttlc Applications (prepared by R. M. Ehret) Volume 111. Space Shuttle Configurations (prepared by A. 1'. IJiu and E. .J. Mulcahy) Mr. .Jan~esE. Colliprjest, Jr., provided overall technical guidance in the preparation of Volun7e 11. Mr. Eclward .T. Mulcally and Mr. A.S. Muslcman contrj1)utcd significantly to the preparation of Section 1. 1 (Space Shuttle Vehlcle Structural Ilescriptlon) of Volunle I. Mr. John Malnon and Mr. F. Stuckcnbcrg aided substantially in the preparation of the. nondcstruc~iveevaluation sectlons in Volumes I and 11. Mr. K. E. O'Brien and Mr. R.M. Ehret contributc~cl, respcctively, Section 2. 2 (Prevention of Cracks and Crack-Like Defects In Shuttle Vehicle Structure) and Section 2. 3. 8 (Required Material Properties Data for Space Shuttle Fracture Mechanics Analysis) of Volume I. Dr.Matthe\~- Creage r contri butcrl Sc,ct~on2. 3. 6 (Failure Under Complex Loading Conditions) and Section 2. 3. 7. 4 (Damage, Tolerance An:~lysisfor Pressure Vessels) of Volume I and Sectlon 2. 2 (Thin Sheet Behavior) and a discussion of fracture behavior under corn1)jned in-plane loading in Stction 1.2 (Lintbar Elastic Con- cepts of Fracturc Behavior) of Volumc 11. Mr. R. W. Westrup prepared the original proposal response to the RFI' and established ttic basic frame work for tile study program. The managerial guidance provided by Mr. R. I?. Olsen, EnKinccringManager, Materials and I'rocesses, Spacc Division, is acknoq,lc~d~edby thc authors. CONTENTS Section Page INTRODUCTION . 1 1. 0 APPRAISAL OF SPACE SHUTTLE VEHICLE STRUCTURES. 1. 1 Space Shuttle Vehicle Structural Description . 1.1.1 SolidRocketBooster . 1. 1.2 External Tank . 1. 1. 3 Mid Fuselage . 1. 1. 4 Wing . 1. 1. 5 Forward Fuselage and Crew Compartment, 1. 1. 6 Aft Fuselage . 1. 1. 7 Vertical Stabilizer . 1. 1. 8 Landing Gear . 1. 2 Critical Part Selection Logic. 1.2.1 LossofAssembly(Step4) . 1. 2.2 Loss of Vehicle (Step 6). 1. 2. 3 Redundant Member or Multiload Path (Step 5) . 1. 2. 4 Accessibility Requirements (Step 9) . 1. 2. 5 Evaluation of Potentially Fracture- Critical Parts (Step 7). 1. 2. 6 Critical Part Selection Logic Application Examples . FRACTURE CONTROL METHODS . 2. 1 Fatigue Design and Analysis Methods . 2. 1. 1 Fatigue Performance . 2. 1. 2 Detail Design Considerations . 2. 1. 3 Fatigue Analysis Methods . 2.2 Prevention of Cracks and Crack-Like Defects in Space Vehicle Structure . 2. 2. 1 Administrative Controls and Activities . 2.2.2 Technical Activities . 2. 3 Fracture Control Methods for Initially Cracked Structures . 2. 3. 1 Safe-Crack-Growth and Fail-Safe Structures . - . PRECEDING PAGE BLANK. NOT FILD' ' - Section Page 2. 3. 2 Classification of Space Shuttle Structural Elements . 2.3.3 MonolithicStructure . 2. 3. 4 Crack Arrest Structure . 2. 3. 5 Multiple Element Structure . 2. 3. 6 Failure Under Complex Loading Conditions . 2. 3. 7 Failure of Pressure Vessels and Shells 2. 3. 8 Required Material Property Data for Space Shuttle Fracture Mechanics Analysis . 2. 3.9 Recommendations on Fracture Mechanics Research and Development 2.4 Nondestructive Evaluation . 3. 0 FRACTURE CONTROL PROCEDURES . 3. 1 Fracture Mechanics Procedure , 181 3. 2 An Example Problem 185 3. 2. 1 Design Stress Level, Material and Structural Dimensions . 185 3.2.2 Crack Geometry . 187 3.2. 3 Stress Intensity Factors . 19 0 3.2.4 Initial Crack Lengths . 194 3. 2.5 Crack Growth Predictions ' . 19 4 4. 0 SUMMARY AND RECOMMENDATIONS . 203 5. 0 REFERENCES. 205 APPENDIX SYMBOLS AND SUBSCRIPTS . 215 ILLUSTRATIONS Figure Page Critical Part Selection Logic . Fracture Control Program Elements . Elements for Fatigue Design and Analysis . Double-Scarf Joint Specimen . Double-Shear Joint Specimen . Stepped Double Shear Joint Specimen . Plain- Scarf Joint Specimen . Single- Shear Joint Specimen . Continuous Member Tension Design . Examples for the Definition of GAG Cycle . Comparison of Fatigue Crack Growth Characteristics for Monolithic Structure and Crack Arrest Structure Comparison of Fatigue Crack Growth Characteristics for Monolithic Structure and Multiple Element Structure . Crack Growth Characteristics Under Monotonic Increasing Load . Cross-Sectional Views of Common Crack Geometries Through- t he-Thickness Crack Loaded in Tension . Stress Intensity Factors for Eccentrically Cracked Plate . Through-the-Thickness Edge Crack in a Plate Loaded in Tension . Failure Analysis Using an R-Curve . R-Curves for Aluminum Alloys . Failure of Aluminum Alloy Sheets Predicted From R-Curve . Fracture Toughness of Bare 2024-T3 Sheets . Geometries of Truncated Elliptical Cracks . Front Free Surface Influence Factor Ml . Front Surface Influence Factor M11/4 for a/c I1 . Front Surface Influence Factor Mlf/+-for a/c r 1 . Change of Flaw Shape in Propagation of Surface Crack S.urface Flaw Fatigue Crack Propagation Data . Free Surface Correction Factor for Corner Flaw . Crack or Cracks Emanating F'rom a Hole . - vii - Figure Page Flaw. Shape Factor MI @ . Bowie's F'actors for Influence of a Hole . Stress Illtensity Factor Versus Crack Length for a Lug . Stress Intensity Factor for a Pin-Loaded Hole . Through- the- Thickne ss Cracks in Skin- Stiffened Panel . Strc ss Intensity Analysis of Unstiffened and Stiffened Structure . Stress Intensity Factor for Crack Extending Equally on Both Sides of Point Midway Between Two Stringers (NASA TR R-3 58) . Stress Intensity Factor for Crack Cxtending Equally on Both Sides of Stringer (NASA TR R-358) . Stiffener Stiffness Parameter as a Function of Effective Stiffener Area Stiffener Efficiency Factor for a One-Bay Crack as a Function of Stiffener Stiffness Parameter . Stiffener Efficiency Factor for a Crack Extended Symmetrically on Both Sides of a Stringer . Effects of Applied Stress Levels on the Stiffener Efficiency. The Effects of Broken Stiffener and Stiffener Yielding on Crack Tip Stress Intensity . The Effect of Broken Stiffener on the Stress Intensity Factor . The Effect of Broken Stiffener on the Stress Intensity Factor . Stiffener Efficiency Factor for a Two-Bay Crack With a Center Broken Stiffener .
Details
-
File Typepdf
-
Upload Time-
-
Content LanguagesEnglish
-
Upload UserAnonymous/Not logged-in
-
File Pages225 Page
-
File Size-