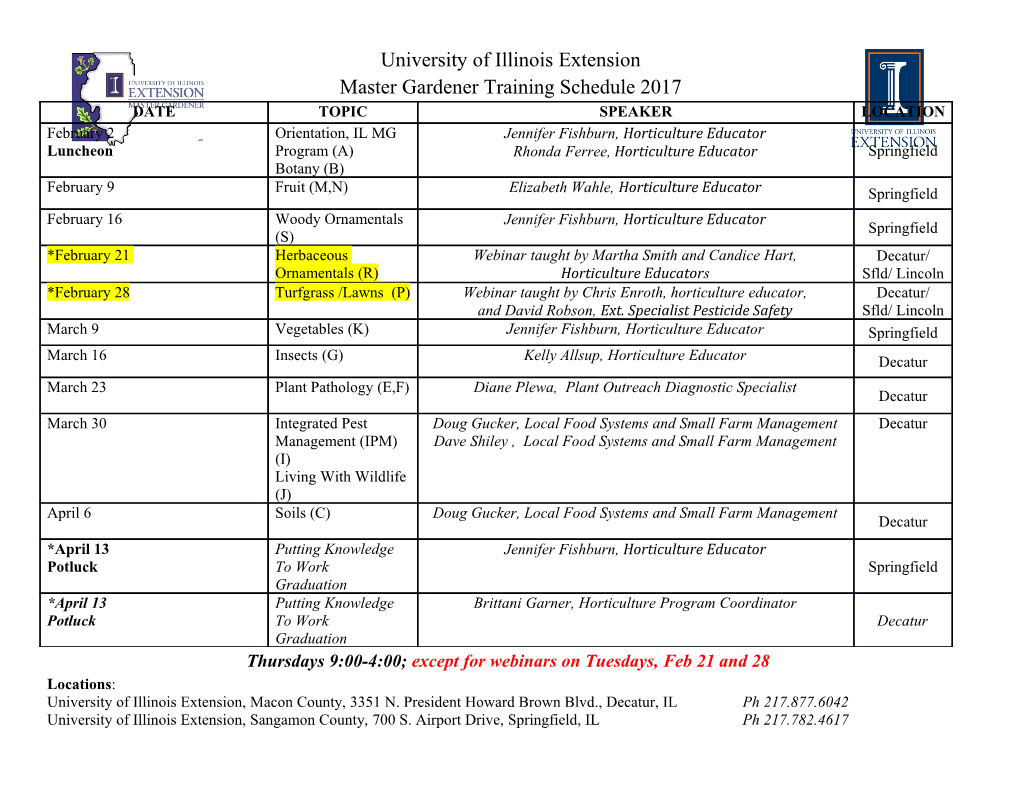
JOM, Vol. 67, No. 5, 2015 DOI: 10.1007/s11837-015-1380-1 Ó 2015 The Minerals, Metals & Materials Society Energy Consumption in Copper Smelting: A New Asian Horse in the Race P. COURSOL,1,5 P.J. MACKEY,2 J.P.T. KAPUSTA,3 and N. CARDONA VALENCIA4 1.—5N Plus Inc., Montreal, QC, Canada. 2.—P.J. Mackey Technology, Inc., Kirkland, QC, Canada. 3.—BBA Inc., Montreal, QC, Canada. 4.—Deltamet Consulting, Pointe-Claire, QC, Canada. 5.—e-mail: [email protected] After a marked improvement in energy consumption in copper smelting dur- ing the past few decades, technology development has been slowing down in the Americas and in Europe. Innovation, however, is still required to further reduce energy consumption while complying with stringent environmental regulations. The bottom blowing smelting technology being developed in China shows success and promise. The general configuration of the bath smelting vessel, the design of high-pressure injectors, and the concentrate addition system are described and discussed in this article with respect to those used in other technologies. The bottom blowing technology is shown to be operating at a temperature in the range of 1160–1180°C, which is the lowest reported temperature range for a modern copper smelting process. In this article, it is suggested that top feeding of filter cake concentrate, which is also used in other technologies, has a positive effect in reducing the oxidation potential of the slag (p(O2)) while increasing the FeS solubility in slag. This reduction in p(O2) lowers the magnetite liquidus of the slag, while the in- creased solubility of FeS in slag helps toward reaching very low copper levels in flotation slag tailings. The application of high-pressure injectors allows for the use of high levels of oxygen enrichment with no requirements for punch- ing. Using a standard modeling approach from the authors’ previous studies, this article discusses these aspects and compares the energy consumption of the bottom blowing technology with that of other leading flash and bath smelting technologies, namely: flash smelting, Noranda/Teniente Converter, TSL (Isasmelt [Glencore Technology Pty. Ltd., Brisbane, Queensland, Aus- tralia]/Outotec), and the Mitsubishi Process (Mitsubishi Materials Corpora- tion, Tokyo, Japan). technology configurations, remains an important INTRODUCTION topic for copper smelters. One of the biggest business stories of 2014 was The first published concept of bottom blowing the huge drop in the price of oil. Thus, the West smelting for nonferrous metals dates back to 1974 Texas Intermediate oil price dropped amid an oil and the paper by Paul E. Queneau and Reinhardt surplus and lower demand by almost 50% from ap- Schuhmann1 titled ‘‘The Q-S Continuous Oxygen proximately $100/barrel in the middle of 2014 to Converter.’’ The authors explained that the Q-S around $50/barrel by early 2015. For a large energy oxygen process invention was a response to the consumer such as a copper smelter, this provided challenges of the time (first oil crisis resulting in some relief to ever rising operating costs. However, high oil prices and pressure to fix sulfur dioxide analysts expect some rebound in the oil price later gases) to increase process efficiency by a systematic this year or into 2016. Hence, energy consumption use of oxygen with a substantial corresponding in smelting, examined in this article for a number of reduction in fossil fuel usage. Queneau and 1066 (Published online March 18, 2015) Energy Consumption in Copper Smelting: A New Asian Horse in the Race 1067 Schuhmann adopted the following key concepts in The number of SKS lead reactors in China quickly their process design: grew after 2002; Stephens7 reported that the SKS lead furnace had been described ‘‘as the smelting Continuity—to limit capital and operating costs section of a QSL reactor.’’ As for the SKS copper Autogenous—by using oxygen to lower energy 5 furnace, Kaixi Jiang et al. described it as similar in and fossil fuel consumption design to the Noranda Reactor, contrasting with the Single off-gas of minimal volume—to lower costs fact that ‘‘the air in the copper matte layer is blown of sulfur fixation into the furnace via the oxygen guns set in the Bottom blowing—to attain optimal solid–liquid– furnace bottom.’’ These oxygen ‘‘guns’’ are essen- gas contact tially Savard–Lee-type shrouded injectors with Countercurrent flow of matte and slag—to compressed air as shrouding gas. The process at achieve bath oxidation and slag reduction in a Dongying is now known as the bottom blowing single vessel smelting (BBS) process. Several other copper smel- An elongated, kiln-like vessel—to improve heat ters in China have since adopted the SKS/BBS and mass transfer. technology. It has also been reported that the tech- In 1989, Queneau2 provided historical insights into nology is being evaluated as an alternative for some the conceptual phase of the Q-S process develop- copper smelters in Chile. ment mentioning that a key driver that triggered The goal of this article is to discuss the SKS/BBS the search for a new nonferrous smelting process technology features and to evaluate the energy re- was the invention of the Savard–Lee shrouded in- quirements for this technology compared with other jector and its success in steel refining. In fact, modern smelting technology. To do so, the approach Queneau and Schuhmann3 had filed their patent in used by Kellogg and Henderson8 and Coursol 1973 and entered into a collaborative agreement et al.9,10 is used. In this approach, all technologies with Savard, Lee, and Canadian Liquid Air that are compared on the same basis, with the same same year, forming QSOP Inc. (Queneau–Schuh- concentrate, flux and coal composition, this allows mann Oxygen Process). evaluating both the electrical and thermal energy With a lack of interest from the copper industry, required to operate a smelter from concentrate to QSOP found support from Werner Schwartz of anode for a given technology. Lurgi, leading to a QSOP-Lurgi agreement in 1974 for the development of the QSL (Queneau–Schuh- BOTTOM BLOWING SMELTING mann–Lurgi) lead smelting reactor. After 15 years TECHNOLOGY (SKS/BBS) of efforts in the laboratory and in pilot and demon- General Description stration plants, including further developments of the Savard–Lee injectors, the QSL became the first The SKS/BBS reactor, as shown in Fig. 1,isa bottom blown smelting vessel commercialized in cylindrical vessel with gravity top feeding of wet nonferrous pyrometallurgy with lead smelting re- concentrate through several ports. The injectors are actors installed in 1990 in Canada (Trail Smelter of all located on one side of the furnace, whereas the Cominco Ltd.), Germany (Stolberg Smelter of Ber- off-gas mouth, matte, and slag tap holes are on the zelius), and China (Baiyin Smelter of CNIEC), and opposite side. This arrangement creates a two-zone in 1991 in Korea (Onsan Smelter of Korea Zinc). A bath: an agitated oxidation zone below the feed more complete story of the QSL development from ports and a quiescent settling zone above the matte patent to commercial implementation was reported tap hole. Two auxiliary burners are located on each by Kapusta and Lee.4 end wall and are used during start-up or stand-by. The Chinese industry developed its own bottom The mouth is small compared with existing bath blowing reactor in the 1990s. China Nonferrous smelting reactors because operating at high oxygen Metal Industry’s Foreign Engineering and Con- struction Co. Ltd. and China ENFI Engineering (ENFI) first piloted their ShuiKouShan (SKS) lead smelting technology in 1999 at the ShuiKouShan lead smelter in Hunan Province. Commercial engi- neering and construction took place in 2001 and successful commissioning in 2002. The SKS copper process was first adopted in 2001 and commissioned commercially at the Sin Quyen Copper Complex in Vietnam in 2008 with a capacity of just 10,000 t/a of anode copper. The second implementation of the technology, and first in China, took place in 2008 at the Dongying Fangyuan Nonferrous Metals Co., Ltd. (Dongying) with an original copper concentrate smelting capacity of 32 dry t/h or 55,000 t/a of an- 5,6 Fig. 1. Schematics of SKS/BBS copper process from Yao and ode copper. Jiang.11 1068 Coursol, Mackey, Kapusta, and Valencia enrichment produces lower volumes of process off- reactor and Teniente converter operations. The gases. original design capacity of the Dongying furnace Cui et al.12 provided a complete description of the was 55,000 t/a of anode copper at 55% oxygen, and bottom blown oxygen smelting process at Dongying. its current capacity has reached 100,000 t/a as the The cylindrical furnace is 4.4 m in diameter by oxygen enrichment reached 75%. 16.5 m in length. The oxygen ‘‘lances’’ are positioned The inherent low level of nitrogen in the blast is in two rows at the bottom of the furnace with five frequently perceived as a weakness of high-oxygen lances in the lower row at 7° to the vertical and the injection due to the diminished mixing of the bath. A four lances in the upper row at 22°. This provides a comparison with the operating oxygen top-blown– 15° angle between the two rows. A photograph of the nitrogen-bottom stirred vessel at Vale’s Copper Cliff Dongying furnace is given in Fig. 2. smelter in Sudbury is opportune at this point. The oxygen lances or guns used to inject the blast Marcuson, Diaz, and Davies reported the use of five are Savard–Lee-type shrouded injectors with simi- porous plugs, each with nitrogen flow rates of lar design and configuration as the original QSL 14 Nm3/h.16 The total flow rate of nitrogen for stir- injectors developed by Lurgi and Air Liquide in the ring was 70 Nm3/h, which was evidently sufficient 1970s.4 The tips of the injectors are built with a to provide stirring in a 135-t semiblister bath (cor- gear-like design as shown on Fig.
Details
-
File Typepdf
-
Upload Time-
-
Content LanguagesEnglish
-
Upload UserAnonymous/Not logged-in
-
File Pages9 Page
-
File Size-