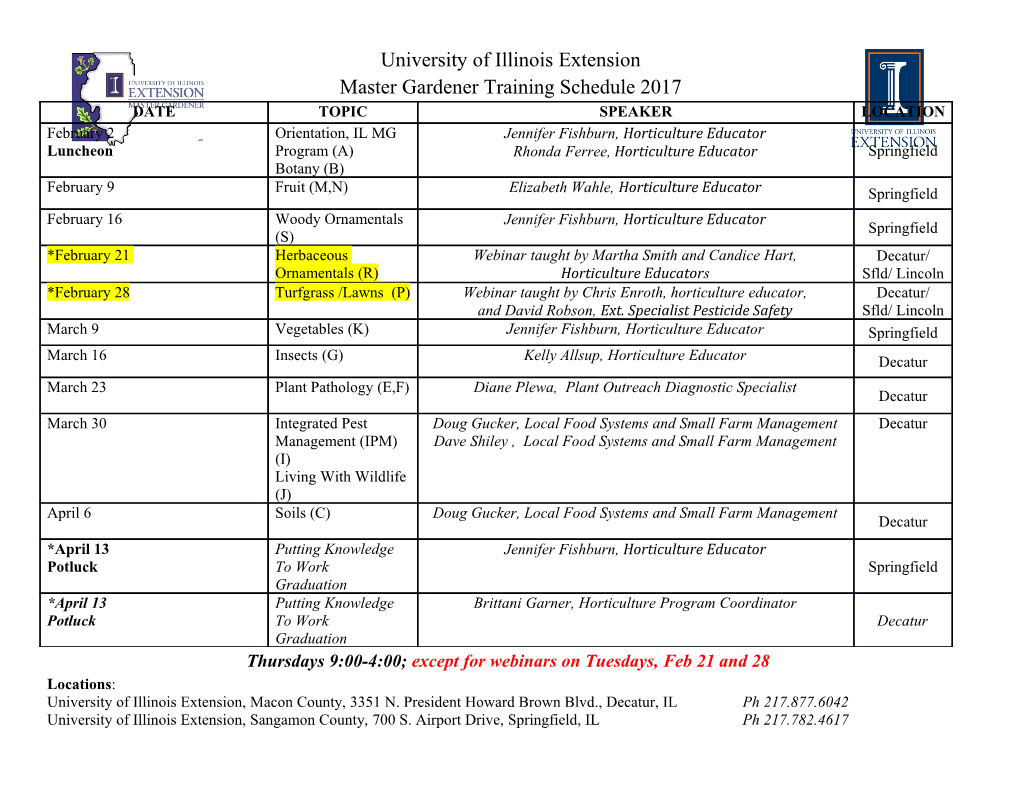
Mech. Sci., 9, 259–266, 2018 https://doi.org/10.5194/ms-9-259-2018 © Author(s) 2018. This work is distributed under the Creative Commons Attribution 4.0 License. Location of unbalance mass and supporting bearing for different type of balance shaft module Chan-Jung Kim Department of Mechanical Design Engineering, Pukyong National University, Busan, 48513, South Korea Correspondence: Chan-Jung Kim ([email protected]) Received: 3 September 2017 – Revised: 17 June 2018 – Accepted: 6 August 2018 – Published: 15 August 2018 Abstract. The dynamic characteristics of balance shaft module is controlled by the design of rotating parts as how to allocate both a unbalance mass and a supporting bearing so that the concept design of a rotor structure is the key issue on determining the overall quality of dynamic performance as well as fatigue resistance. Even the design on balance shaft has some limitation from the lay-out of a vehicle engine system, there is still chance to enhance the reliability of the balance shaft module by the promising design model of the rotor structure including support bearing locations. In this paper, an optimal location of unbalance mass and supporting bearing is proposed to make an efficient conceptual design using an objective function to minimize a bending deformation of rotor as well as a reaction force at supporting bearing. In addition, the application of design optimization of a balance shaft model is explained using an in-house program for inline 3-cylinder and inline 4-cylinder engine, respectively. 1 Introduction forces on bearing or bending deformation, will be dependent on the condition of shape of balance shaft or the location of Vehicle engine produces necessary energy enough to drive unbalance mass, even though the unbalances are fixed as cer- the responding vehicle system as a prime goal. However, it tain value (Stone and Ball, 2004; Ishikawa et al., 2002; Suh also induces an inertia force or moment as a side effect dur- et al., 2000; Meek and Roberts, 1998; Huegen et al., 1997). ing converting the reciprocating motion of pistons into rotat- Recently, Kim et al. (2012) proposed the optimal location of ing motion of crankshaft and the exact phenomenon is deter- both a supporting bearing and a deflection of balance shaft mined by the type of engine as well as kinematics upon sev- by introducing the objective function to minimize interesting eral sub-components of engine system (Heisler, 1998; Stone energy terms, both the elastic strain energy and the kinematic and Ball, 2004; Serrano et al., 2015; Lui et al., 2015). Several energy of a balance shaft (Kim et al., 2012). However, the countermeasures were previously proposed to control the ex- optimal process was limited for the inline 4-cylinde engine citation from vehicle engine using additional device (Lui et only to cope with reciprocal force from a secondary inertia al., 2015; Lin et al., 2017; Shangguan et al., 2016; Hafidi et part. In addition, the kinematic energy in objective function al., 2010) and balance shaft is one of novel solution among did not directly deal with the structural issue of a balance them. Balance shaft module which is generally located un- shaft because the energy from a mass moment of inertia was der the engine block is aimed for reducing the indispensable introduced in order to save the driving torque during opera- but unexpected vibrations as generating equivalent vibrations tion. On the other hand, the objective function in this study having an opposite direction (Heisler, 1998; Stone and Ball, directly tackle the structural issue of a balance shaft; the dif- 2004). Since the fundamental role of balance shaft module ference between both of bearing reaction forces was consid- can be conducted by the rotating unbalance mass on balance ered at inline 4-cylinder engine model and the fundamental shaft while a target engine is under operation, the prior in- resonance frequency was used at inline 3-cylinder model, re- terest should be focused on the design of balance shaft in- spectively. cluding a strategy on unbalance mass as well as supporting bearings. The response of rotor dynamics, shown as reaction Published by Copernicus Publications. 260 C.-J. Kim: Location of unbalance mass and supporting bearing Figure 2. Equivalent balance shaft model with bearing reaction in inline 4-cylinder engine. the rotation of crankshaft and higher order terms expect sec- ondary one are small enough to be neglected. And any mo- ments are well balanced owing to the kinematics of inline 4- cylinders. So, the coupling inertia force can be approximated by the secondary term in Eq. (2) as: r2 F D 4m !2 cos2θ; (2) SECOND p l The simplified engine module kinematics including bal- Figure 1. Simplified engine module kinematics. ance shaft module is described in Fig. 1 (Kim et al., 2012). To cancel out the second order vibration, it can be balanced by a pair of counter-rotating balance shafts at twice the an- In this paper, the design strategy is focused on the unbal- gular velocity of the crankshaft. ance shaft which is most important item throughout the over- The unbalance quantity is determined by the secondary in- all design process. New method can obtain the optimal model ertia force induced by the given engine specification and the of balance shaft that minimizes the burden issues such as expression of unbalance quantity is denoted in Eq. (3) with bearing force and bending deformation as well as induces the respect to the relation in Eq. (4) as: inertia force or moment equivalent to that of engine part dur- ing the service loading or under operation. Author suggests F D 2 × m r (2!)2 ; (3) the formulation of optimal design about balance shaft by in- SECOND b b troducing the objective function which is subjective to the in- line 3-cylinder and inline 4-cylinder engine respectively, for 2 the sake of deriving the optimal plan of balance shaft. Also, mpr m r D ; (4) the exclusive program is proposed as a practical application b b 2l to assist the concerning design engineer about balance shaft Here, m and r are the equivalent mass and radius of ro- in a field work. b b tation in unbalance quantity, respectively. If the balance shaft module is simplified with single rotor model, the correspond- 2 Formulation of state variables ing function (W) that is equivalent to the inertia force should be dependent on the rotating angle of crankshaft and thereby 2.1 Inline 4-cylinder engine it can be formulated by the Eq. (5) as: Multi-order vibrations are produced by the linkage mecha- 2 2 mpr ! nism at the single piston-crankshaft connecting point as con- W D cos2θ; (5) verting the reciprocal movement into rotating one and cor- 2l responding inertia force (FALL) can be expressed as Eq. (1) as (Heisler, 1998; Stone and Ball, 2004; Meek and Roberts, Using the Eq. (5), the corresponding bearing reaction force 1998): could be derived from the equivalent single rotor system shown in Fig. 2. The bearing reaction force at each location r r 2 F D m !2r cosθ C cos2θ C cos4θ C··· ; (1) is formulated by the Eq. (5). ALL p l l 2 2 2 2 b mpr ! a mpr ! Here, m is mass of reciprocal part, r is radius of fA D cos2θ;fB D cos2θ; (6) p a C b 2l a C b 2l crankshaft, l is length of connecting rod and ! and θ is an- gular velocity and angle of crankshaft, respectively. For in- Here, a, b are positional variables regarding the position line 4-cylinder engine, primary term is self-balanced during of the unbalance mass. Mech. Sci., 9, 259–266, 2018 www.mech-sci.net/9/259/2018/ C.-J. Kim: Location of unbalance mass and supporting bearing 261 Figure 3. Geometry of engine module with balance shaft module at 3-cylinder engine. The bending case caused by inertia force between both sides of bearing is represented by Fig. 2. It could com- prise the entire bending situation of inline 4-cylinder engine. Using the boundary condition of equivalent rotor model in Fig. 2, the corresponding deformation variable, y1;y2 could be formulated by Eqs. (7) and (8), respectively (Gere and Figure 4. Equivalent balance shaft model with bearing reaction in Timoshenko, 1999). In addition, the total deflection of the inline 3-cylinder engine (first bearing: black triangle, second bear- balance shaft (y4c (x)) can be formulated with respect to the ing: white triangle). location of unbalance mass, x, as shown in Eq. (9). 1998; Stone and Ball, 2004; Suh et al., 2000). Wb 3 2 y1 (x1) D x1 − a x1 − 2abx1 (0 ≤ x1 ≤ a); (7) 6EIl 1 h i M D m r!2 l cos(θ − 1200) C 2l cos(θ − 2400) p 2 p p 1 2 Wa D 3mpr! l; (10) y (x ) D x3 − b2x − 2abx (0 ≤ x ≤ b); (8) 2 2 2 6EIl 2 2 2 2 The unbalance quantity (MB) is determined by the similar method in inline 4-cylinder engine (see Eq.4) as: x aCb−x D Z Z Mp MB 4c 1p ; (11) y (x) D y1 (p)dp C y2 (p)dp; (9) , 3m r!2l D m r !2l 2 p B B 3 0 x Here, l3(D x1 C x2) is length of balance shaft, mB, rB is Here, E is an elastic proportional coefficient, I is the sec- equivalent mass and radius of unbalance, respectively. Hence ond moment of inertia about the equivalent rotor’s section the resultant quantity can be formulated as Eq.
Details
-
File Typepdf
-
Upload Time-
-
Content LanguagesEnglish
-
Upload UserAnonymous/Not logged-in
-
File Pages8 Page
-
File Size-