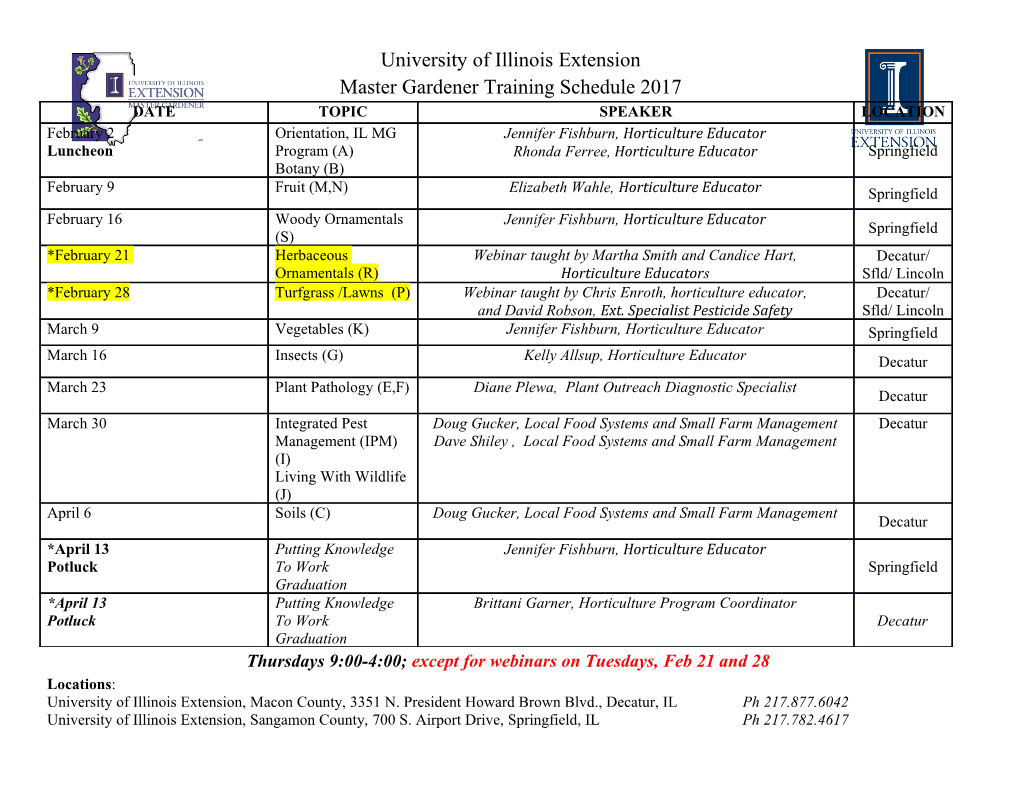
NEi Nastran in-CAD Features Overview NEi Nastran in-CAD combines a FEM Modeler with comprehensive pre- and post- processing capabilities, and NASTRAN Solvers. Parts and assemblies can be analyzed for a wide spectrum of static, dynamic, and thermal loading. NEi Nastran in-CAD features true geometry associativity, composite elements, custom coordinate systems and nonlinear analyses for plasticity and true surface to surface contact. With NASTRAN being one of the most Dual Kernel Support and Kernel widely used solutions, NEi Nastran in-CAD collaboration (ACIS and Parasolid) users can now communicate their data to Support both top-down and bottom-up most standard pre- and post-processors design process through support of the NASTRAN file format. This provides versatility to a product which is CAD Interoperability: already easy to use and backed by the Native file translators to and from nearly renowned NASTRAN solution. all mechanical CAD products and graphical applications on the market Capabilities: today: CATIA® V4 & V5, SolidWorks®, Unique Methodologies: Pro/ENGINEER®, IPT & IAM (Autodesk Innovative Part Design, Intuitive feature Inventor®), Unigraphics®, IGES, STEP, history with flexible design intent X_T (Parasolid®), SAT (ACIS®), VRML, 3D Dynamic Modeling, Mixed feature STL, DWG, DXF™, EXB (CAXA based and direct editing design DRAFT), TIFF, JPG, PNG, TGA, BMP, Single scene part and assembly EPS, HSF (Hoops), 3DS (3D Studio), environment POV-Ray, Raw, Romulus, TrueSpace, IntelliShape™ Handled based design OBJ (Wavefront), 3D PDF editing Supported standards: ANSI, DIN, ISO, IntelliShape Modeling Intelligence, JIS, and GB Advanced modeling settings connected to features Part Modeling: SmartSnap™ Technology enabling Feature based, parameterized solid automatic catching to existing geometry modeling SmartAssembly® Technology for Scene Browser dynamic design tree automatic positioning, sizing, and (e.g. re-order, drag and drop, etc.) orientation of parts, and assemblies Property Browser direct input and DesignVariation™ parametric and context based actions property configurations at any part, Quick Access contextual pop-up hotkey feature, and assembly level commands for in-place design creation TriBall® advance positioning and In-place editing of features, parts, and operation tool faces Catalog based design environment for History Independent referencing to part drag and drop design geometry IntelliStretch™ dynamic resizing for Integrated sketching with dynamic assemblies/parts optional constraints 2011 NEi, NEi Software, Inc. NE, NE/, and NEi logo are Registered Trademarks of NEi Software, Inc. NASTRAN is a registered trademark of the National Aeronautics and Space Administration. Windows is a registered trademark of the Microsoft Corporation. All other trademarks and registered trademarks are the property of their respective owners. Extrudes, revolves, feature patterns, Advance Photo-Realistic Rendering holes, etc. Engine Advanced 3D operations, e.g. lofting, Drag and Drop color and image sweeping, complex blending, capabilities chamfering, etc. Drag and Drop animation support Advanced shelling, trim operations, and Key Frame animation manipulation and Boolean operations advance animation positioning with Catalog based functional features, e.g. TriBall Custom Holes, Fasteners, Gears, 3D E-mail Package builder for sharing Bearing, etc. Web Publishing for project review and Direct Face modification support for communication native features and imported data Free 3D IC-Viewer Support for creating 3D models from existing 2D data, e.g. 2D-to-3D Meshing: extrusion, etc. Global and local controls for part Multiple design variations with geometry with default sizing Configuration Management support Mesh control on arbitrary user defined regions Sketch line or curve meshing Free surface meshing: quads or triangles Auto mesh, loads and constraints update with geometry changes Mesher status window and progress bar Display/hide shell element normals Reverse normals for shell elements Mesh validation checks - distortion, Jacobian, and skew Display/hide beam element orientation and direction Assembly Modeling: Display/hide beam element and shell Flexible Assemble and Disassemble element cross-section support 1D element cross-section property Complete range of mating conditions, definition snap-to-fit SmartAssembly® Technology Combined shell (2D) and beam (1D) Cross parent constraint relation support meshing Real-time Collision Detection and Interference Checking Assembly Connectors: Multiple sub-assembly support True surface contact Easily design-in-the-context of an Automatic contact assembly Thermal contact resistance Easy designing and changing of parts and subassemblies from within an Loads and Boundary Conditions: assembly Uniform pressure and force on faces, Mirrored components to create new edges and vertices parts and assemblies based on existing Directional pressure and force designs Acceleration loads (gravity) Multiple assembly design variations with Enforced motions: acceleration, velocity, Configuration Management for easy displacement (rotational/translational) “what if” design scenarios Temperature, default temperature and Statistical analysis support for mass, heat flux center of gravity, and moments of inertia Symmetric, antisymmetric, axisymmetric boundary conditions Communication: Fixed constraints on faces, edges and Photo-Realistic real-time realistic vertices settings with Image export Directional and prescribed constraints 2011 NEi, NEi Software, Inc. NE, NE/, and NEi logo are Registered Trademarks of NEi Software, Inc. NASTRAN is a registered trademark of the National Aeronautics and Space Administration. Windows is a registered trademark of the Microsoft Corporation. All other trademarks and registered trademarks are the property of their respective owners. Thermal constraints Generalized polynomial Thermal body loads Temperature dependent property Initial temperature conditions support Custom colors and sizes for loads and constraints Material Orientation: Loads defined using edges Vector projection Convection Curve tangent Conduction Rotated curve tangent Radiation Translated curve tangent Heat generation Surface U and V directions Rotational velocity / acceleration From output (thermal) Properties: Load variation using arbitrary 3D scale 1D beam (PBEAM/PBEAML) and bar factors (PBAR/PBARL) 2D plate (PSHELL) and composite Element Library: (PCOMP) 1D line (CBEAM, CBAR, CPIPE) 3D solid (PSOLID) 2D linear shell (CQUAD4 and CTRIA3) Contact (BSCONP) 2D parabolic shell (CQUAD8 and CTRIA6) Surface Contact: 3D linear and parabolic tetrahedron Automatic surface contact generation (CTETRA) General, welded, slide, rough, offset Composites with plates and shells weld and RBE3 element contact types Surface to surface contact with manual Static friction or automatic recognition of surfaces Concentrated mass Analysis Types: Connectors: Linear statics Spring (CBUSH) Normal modes Rigid elements Linear buckling Rod (CROD) Nonlinear static Nonlinear cable Thermal stress Prestress static Materials: Composite Isotropic Contact analysis in assemblies Anisotropic (2D & 3D) Linear steady state heat transfer Orthotropic (2D & 3D) Modal transient response Nonlinear materials Direct transient response Nonlinear elastic Direct frequency response Elasto-plastic Modal frequency response Plastic Nonlinear steady state heat transfer Hardening Nonlinear transient heat transfer Isotropic Nonlinear transient response Kinematic Combined Composite Analysis: Yield Various failure theories supported: Von Mises Hill Tresca Hoffman Mohr-Coulomb Tsai-Wu Drucker-Prager Max. stress Custom stress-strain curve Max. strain Hyperelastic NASA LARC02 Neo-Hookean Mooney-Rivlin Coordinate Systems: Ogden Cartesian, cylindrical and spherical coordinate systems Yeoh 2011 NEi, NEi Software, Inc. NE, NE/, and NEi logo are Registered Trademarks of NEi Software, Inc. NASTRAN is a registered trademark of the National Aeronautics and Space Administration. Windows is a registered trademark of the Microsoft Corporation. All other trademarks and registered trademarks are the property of their respective owners. Referencing global assembly, part or Binary results file in OP2 format usable custom coordinate systems by all Nastran solvers and wide variety Display toggles of post-processors Post-Processing: Stress, deformation plots Principal and directional stress plot Strain plot Resonant frequencies, mode shape plots Temperature, heat flux plots Iso-surfaces Results across composite laminates Partial results generation for modal and transient analysis types Export Nastran input deck to other FEA systems User Interface: Customizable material library Menu support for all features Output within NEi Nastran in-CAD Toolbar shortcuts Modeler view with sensitive Help and Modern tree view layout analysis control, such as pausing and Query display of real time information on solution termination nodes and elements Import results using Femap Binary Highlight specific nodes and elements Neutral file format (FNO) on the model Single and multi-set animations Total number of nodes/elements Max/min labels displayed in assembly tree Results processed on selected parts of Section view for parts and assemblies assemblies Dynamic update of loads, constraints, Dynamic result data display during and rigid bodies
Details
-
File Typepdf
-
Upload Time-
-
Content LanguagesEnglish
-
Upload UserAnonymous/Not logged-in
-
File Pages5 Page
-
File Size-