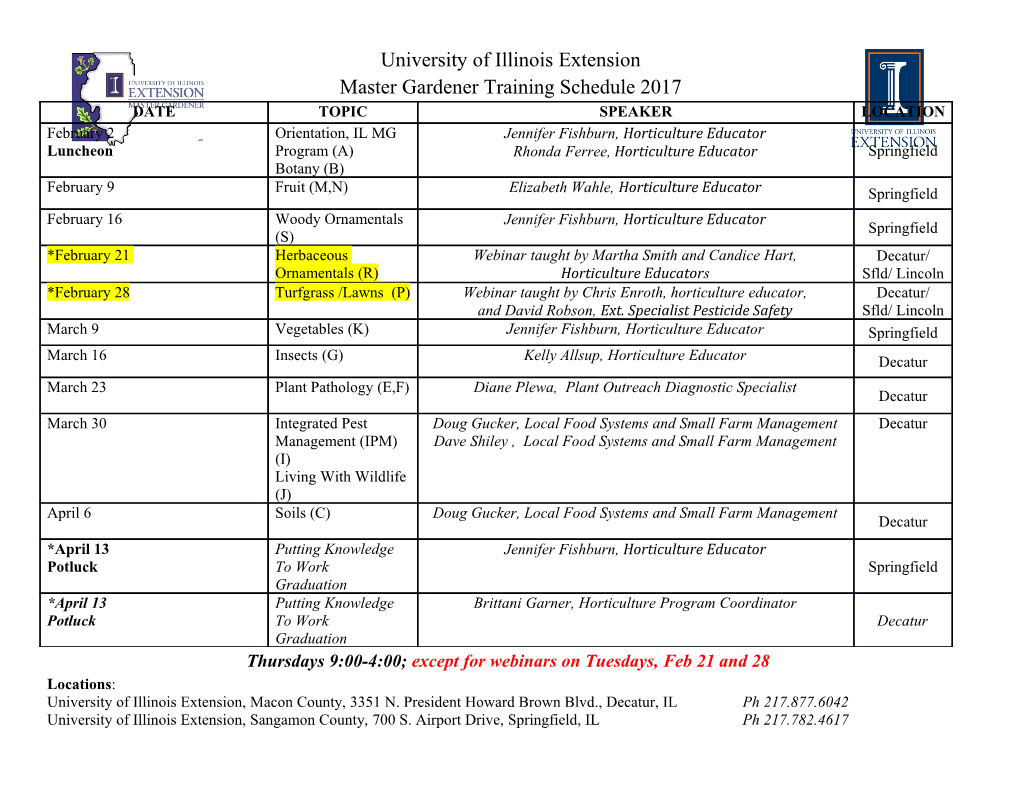
Startup I General startup instructions 10 0 10 Startup 1 10.1 General startup instructions 2 Comply with the safety notes during startup! 3 4 Before startup Correct project planning of the drive is the prerequisite for successful startup. Refer to the MOVIDRIVE® MDX60/61B system manual for detailed project planning notes and 5 an explanation of the parameters. 6 VFC operating MOVIDRIVE® MDX60/61B drive inverters are factory set to be taken into operation with modes without the SEW motor which is adapted to the correct power level. The motor can be connected 7 speed control and the drive started immediately in accordance with the section "Starting the motor" (→ page 387) icon. 8 Inverter/motor The following tables indicate which inverter/motor combinations this applies to. combinations 9 400/500 V units 10 MOVIDRIVE® MDX60/61B in VFC mode SEW motor 0005-5A3-4 DT80K4 11 0008-5A3-4 DT80N4 0011-5A3-4 DT90S4 12 0014-5A3-4 DT90L4 0015-5A3-4 DT90L4 0022-5A3-4 DV100M4 13 0030-5A3-4 DV100L4 0040-5A3-4 DV112M4 14 0055-5A3-4 DV132S4 0075-5A3-4 DV132M4 15 0110-5A3-4 DV160M4 0150-503-4 DV160L4 16 0220-503-4 DV180L4 0300-503-4 DV200L4 17 0370-503-4 DV225S4 0450-503-4 DV225M4 18 0550-503-4 DV250M4 0750-503-4 DV280S4 19 0900-503-4 DV280M4 1100-503-4 D315S4 1320-503-4 D315M4 20 21 22 System Manual – MOVIDRIVE® MDX60B/61B Drive Inverters 375 I Startup 10 General startup instructions 0 230 V units MOVIDRIVE® MDX60/61B in VFC mode SEW motor 0015-2A3-4 DT90L4 0022-2A3-4 DV100M4 0037-2A3-4 DV112M4 0055-2A3-4 DV132S4 0075-2A3-4 DV132M4 0110-203-4 DV160M4 0150-203-4 DV160L4 0220-203-4 DV180L4 0300-203-4 DV200L4 The startup functions described in this section are used for setting the inverter so it is optimally adapted to the motor which is actually connected and to the given boundary conditions. It is essential to perform a startup as described in this section for the VFC operating modes with speed control, all CFC operating modes and SERVO operating modes. Hoist applications Do not use MOVIDRIVE® MDX60/61B drive inverters for any safety functions in con- junction with hoist applications. Use monitoring systems or mechanical protection devices as safety features to avoid possible damage to property or injury to people. 376 System Manual – MOVIDRIVE® MDX60B/61B Drive Inverters Startup I Preliminary work and resources 10 0 10.2 Preliminary work and resources 1 • Check the installation. • Take suitable measures to prevent the motor starting up inadvertently, for example 2 by removing the electronics terminal block X13. Furthermore, additional safety pre- cautions must be taken depending on the application to avoid injury to people and 3 damage to machinery. •For startup with the DBG60B keypad: 4 Plug the connector of the DBG60B keypad into the Xterminal slot. •For startup with PC and MOVITOOLS® (version 4.0 or higher): 5 Plug the UWS21A option into the Xterminal slot and use an interface cable (RS232) ® to connect it to the PC. Install and start MOVITOOLS on your PC. 6 • Switch on the power system and, if necessary, the DC 24 V supply. • Check the correct default parameter settings (e.g. factory setting). 7 • Check the terminal assignment that has been set (→ P60_ / P61_). 8 Startup automatically changes a group of parameter values. The parameter descrip- tion P700 "Operating modes" explains which parameters are affected by this step. Refer 9 to the MOVIDRIVE® MDX60/61B system manual, section "Parameters" for the param- eter description. 10 11 12 13 14 15 16 17 18 19 20 21 22 System Manual – MOVIDRIVE® MDX60B/61B Drive Inverters 377 I Startup 10 Startup using the DBG60B keypad 0 10.3 Startup using the DBG60B keypad General Startup with the DBG60B keypad is possible in VFC operating modes only. Startup information in CFC and SERVO operating modes is only possible using the MOVITOOLS® software. Required data The following data are required for successful startup: • Motor type (SEW motor or non-SEW motor) • Motor data – Rated voltage and rated frequency. – In addition, with a non-SEW motor: Rated current, rated power, power factor cosϕ and rated speed. • Rated supply voltage The following information is also required for the startup of the speed controller: • Incremental encoder type • Encoder type and resolution of the incremental encoder: Startup parameters SEW encoder type Encoder type Encoder resolution AS1H, ES1H, AV1H HIPERFACE® 1024 ES1S, ES2S, EV1S, EH1S SINE ENCODER 1024 ES1R, ES2R, EV1R, EH1R INCREM. TTL SENSOR 1024 ES1T1), ES2T1), EV1T1), EH1T1) 1) DC 5 V TTL sensors ES1T, ES2T, EV1T and EH1T must be connected via the DWI11A option (→ Sec. Installation). • Motor data – SEW motor: Brake yes or no and flywheel fan (Z fan) yes or no – Non-SEW motor: Mass moment of inertia [10-4 kgm2] of the motor, brake and fan • Stiffness of the closed-loop control system (factory setting = 1; applies to most appli- cations) If the drive tends to oscillate → Setting < 1 If the transient recovery time is too long → Setting > 1 Recommended setting range: 0,90 ... 1... 1.10 (factory setting = 1) • Mass moment of inertia [10-4 kgm2] of the load (gear unit + driven machine) extrap- olated for the motor shaft. • Time for the shortest required ramp. • Activate encoder monitoring (P504 = "ON") after completing startup. The function and voltage supply of the encoder are then monitored. Important: Encoder monitoring is not a safety function! 378 System Manual – MOVIDRIVE® MDX60B/61B Drive Inverters Startup I Startup using the DBG60B keypad 10 0 Selecting a The figure below shows the keys for selecting the language. 1 language 2 3 4 5 2. 6 3. 7 1. 4. 8 9 10 06534AXX Figure 192: Keys for language selection 11 1. Language selection 12 2. Up arrow, moves up to the next menu item 3. OK, confirms the entry 13 4. Down arrow, moves down to the next menu item 14 The following text appears on the display when the keypad is switched on for the first time or after activating the start mode: 15 SEW EURODRIVE 16 The symbol for language selection then appears on the display. 17 18 54533AXX 19 Proceed as follows to select the language: 20 • Press the "Language selection" key. A list of available languages is displayed on the screen. 21 • Use the "up arrow / down arrow" keys to select the desired language. • Confirm your language selection by pressing the "OK" key. The basic display is now 22 shown in your chosen language. System Manual – MOVIDRIVE® MDX60B/61B Drive Inverters 379 I Startup 10 Startup using the DBG60B keypad 0 Startup The figure below shows the keys for required for startup. 3. 1. 4. 5. 2. 6. 06551AXX Figure 193: Keys for startup 1. Cancel or abort startup 2. Change the menu, display mode ↔ edit mode 3. Up arrow, moves up to the next menu item 4. OK, confirms the entry 5. Activates the context menu 6. Down arrow, moves down to the next menu item Startup procedure 1. "0" signal at terminal X13:1 (DIØØ "/CONTROL.INHIBIT"), e.g. 0.00rpm by disconnecting the electronics terminal block X13. 0.000Amp CONTR. INHIBIT 2. Activate the context menu by pressing the key. PARAMETER MODE VARIABLE MODE BASIC VIEW 3. Use the key to scroll down to the "STARTUP PARAMET." MANUAL MODE menu item. STARTUP PARAMET. COPY TO DBG COPY TO MDX 380 System Manual – MOVIDRIVE® MDX60B/61B Drive Inverters Startup I Startup using the DBG60B keypad 10 0 4. Press the OK key to begin the startup procedure. The first 1 parameter appears. The flashing cursor under the parameter STARTUP PARAMET. number indicates that the keypad is in display mode. PREPARE FOR STARTUP • Use the key to change to edit mode. The flashing cur- 2 sor disappears. • Use the key or the key to select "PARAMETER SET 1" or "PARAMETER SET 2". 3 • Confirm the setting using the OK key to confirm your selec- tion. • Use the key to return to the display mode. The flashing 4 cursor appears again. C00*STARTUP • Use the key to select the next parameter. PARAMETER SET 1 PARAMETER SET 2 5 5. Set the required operating mode. Use the key to select the C01*OPER. MODE 1 6 next parameter. VFC1 VFC1&GROUP 7 6. Select the motor type. If a 2 or 4-pole SEW motor is connected, C02*MOTOR TYPE 1 select the correct motor from the list. If a non-SEW motor or an DT71D2 8 SEW motor with more than four poles is connected, select DT71D4 "NON-SEW MOTOR" from the list. DT80K2 Use the key to select the next parameter. 9 C02*MOTOR TYPE 1 NON-SEW MOT. 10 DT63K4/DR63S4 7. Enter the rated motor voltage for the selected connection type C03* V 11 according to the value specified on the nameplate. MOT. RATED VOLT 1 +400.000 Example: Nameplate 230∆/400W 50 Hz 12 W connection → Enter "400 V". ∆ connection, transition point at 50 Hz → enter "230 V". ∆ connection, transition point at 87 Hz → Also enter 230 V. 13 However, after startup first set parameter P302 "MAXIMUM SPEED 1" to the value for 87 Hz and then start the drive. 14 Example: Nameplate 400∆/690W 50 Hz Only ∆ connection possible → Enter "400 V". W connection is not possible. 15 Use the key to select the next parameter. 16 8. Enter the rated frequency specified on the motor nameplate. C04* Hz Example: 230∆/400W 50 Hz MOT. RATED FREQ. 1 17 Enter "50 Hz" in W and ∆ connection.
Details
-
File Typepdf
-
Upload Time-
-
Content LanguagesEnglish
-
Upload UserAnonymous/Not logged-in
-
File Pages25 Page
-
File Size-