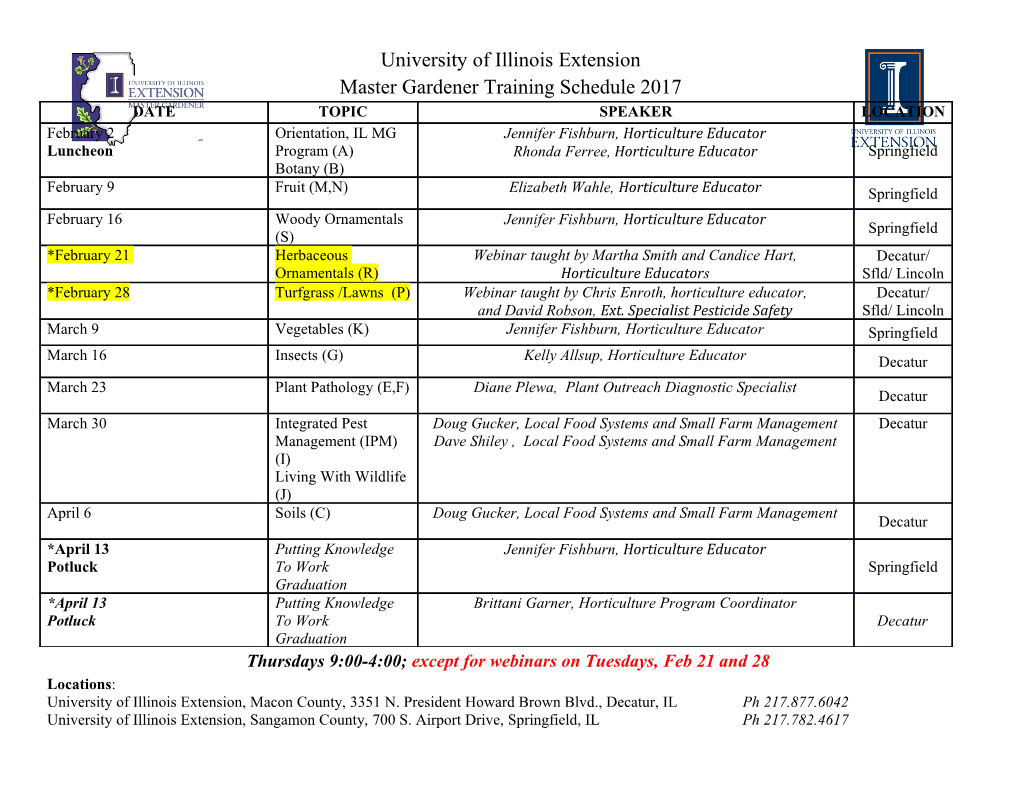
Research Report. ELECTRIC FEED SYSTEMS FOR LIQUID PROPELLANT ROCKET ENGINES. Pablo Rachov, Hernán Tacca y Diego Lentini. Cita: Pablo Rachov, Hernán Tacca y Diego Lentini (2010). ELECTRIC FEED SYSTEMS FOR LIQUID PROPELLANT ROCKET ENGINES. Research Report. Dirección estable: https://www.aacademica.org/hernan.emilio.tacca/9 Esta obra está bajo una licencia de Creative Commons. Para ver una copia de esta licencia, visite http://creativecommons.org/licenses/by-nc-nd/4.0/deed.es. Acta Académica es un proyecto académico sin fines de lucro enmarcado en la iniciativa de acceso abierto. Acta Académica fue creado para facilitar a investigadores de todo el mundo el compartir su producción académica. Para crear un perfil gratuitamente o acceder a otros trabajos visite: http://www.aacademica.org. RESEARCH REPORTS ELECTRIC FEED SYSTEMS FOR LIQUID PROPELLANT ROCKET ENGINES Pablo RACHOV LABORATORIO DE CONTROL DE ACCIONAMIENTOS, TRACCIÓN Y POTENCIA (LABCATYP) Departamento de Electrónica Facultad de Ingeniería UNIVERSIDAD DE BUENOS AIRES Directors: Prof. Hernán TACCA, University of Buenos Aires, Argentina Prof. Diego LENTINI, University of Roma “La Sapienza”, Italy Buenos Aires, December 6th, 2010. DOI: 10.13140/2.1.4431.9042 Comparison of Liquid Propellant Rocket Engine Feed Systems - 1 - 1 REPORT N o 1 COMPARISON OF LIQUID PROPELLANT ROCKET ENGINE FEED SYSTEMS Pablo RACHOV LABORATORIO DE CONTROL DE ACCIONAMIENTOS, TRACCIÓN Y POTENCIA (LABCATYP) Departamento de Electrónica Facultad de Ingeniería UNIVERSIDAD DE BUENOS AIRES Directors: Prof. Hernán TACCA, University of Buenos Aires, Argentine Prof. Diego LENTINI, University of Roma “La Sapienza”, Italy Buenos Aires, December 6th, 2010. Comparison of Liquid Propellant Rocket Engine Feed Systems - 1 - 2 CONTENTS I. INTRODUCTION................................................................................................ 3 II. ANALYTICAL DEVELOPMENT................................................................... 4 III. DATA ESTIMATION..................................................................................... 14 IV. RESULTS........................................................................................................ 19 V. CONCLUSIONS.............................................................................................. 34 VI. REFERENCES................................................................................................ 36 VII. APPENDIX.................................................................................................... 37 Comparison of Liquid Propellant Rocket Engine Feed Systems - 1 - 3 I. INTRODUCTION Since several decades the systems to impel propellants inside the combustion chamber are based on the employment of turbo-pumps or a pressurized gas. However, in virtue of the technological advances of the last 10 years in matter of electric engines and batteries, is possible to think about the viability of development electric-pumps feed systems. One of the most difficult requirements to achieve when designing a rocket engine is to keep the weight as low as possible, because generally the payload is a small fraction of the total weight. For this reason, this requirement turns out to be a basic parameter to compare the three systems. Beginning with a brief description of the parts that compose each feed system, the conceptual diagrams of each system are presented in figure 1. Figure 1: Schemes of the 3 feed systems to analyzing. The figure 1 shows that all the three systems have fuel and oxidizer tanks, and also a third tank containing a pressurized gas. In the first system, that gas makes the work of displacing the propellant’s masses inside the combustion chamber. Hereby, the stored gas in the above mentioned tank is under high pressure with typical values ranging from 6.9MPa to 69MPa [1]. For the other two systems, the pumps make the work of displacing the propellants while the gas function is only to prevent cavitation in the pumps. Therefore, the gas mass necessary in such systems is much lower. The two pumps systems differ from each other by the pump drive method. In the turbo- pump system, the device that provides power to the pumps is a gas turbine (sometimes one by pump). The available methods to drive the turbine can be found detailed in [2]. Here the gas generator method will be evaluated. Such a gas generator takes a fraction of the tank stored propellants and, by a separated combustion process (usually fuel rich), provides the gas that drives the turbine. The gas generator is fed usually with propellants that are taken from the feed lines located after the pumps to improve the efficiency. This requires the use of some start method, being usual to use a solid fuel cartridge. In the case here depicted, the turbine gas discharge is done through a separated nozzle direct on the atmosphere (which is named as open cycle turbopump system). Otherwise, the electric pump system is driven by a brushless synchronous electric motor (also can have one by each pump). Each motor is fed by an inverter which converts the direct Comparison of Liquid Propellant Rocket Engine Feed Systems - 1 - 4 current from the battery to alternative current with a frequency suitable enough to drive the electric motor at the required speed. II. ANALYTICAL DEVELOPMENT To realize comparisons it is necessary to estimate the total mass of each feed system described in the previous section. To simplify this analysis, only the mass of the principal components of each system will be considered. That is, the masses of the plumbing system, the mounting system, the valves and the electronics controls will be assumed as negligible. Hence, giving denominations to the diverse masses of the components of each feed system yields: mtp: total mass of the turbo-pump feed system. mep: total mass of the electric-pump feed system. mpg: total mass of the pressurized-gas feed system. mg: pressurizing gas mass. mtg: pressurizing gas propellant tank mass. mto: oxidizer tank mass. mtf: fuel tank mass. mpu: pumps mass. mtu: turbine mass. mgg: gas generator mass. mee: electric engine mass. minv: inverters mass. mbat: batteries mass. mo: oxidizer mass. mf: fuel mass. mp = mo + mf: propellant total mass. mptu: turbine driven propellant mass. Thereby, and taking into account the figure 1 schemes, the total masses of each feed system respond to the following equations: mtp = mg + mtg + mto + mtf + m pu + mtu + mgg + m ptu mep = mg + mtg + mto + mtf + m pu + mee + minv + mbat m pg = mg + mtg + mto + mtf The comparisons presented in this report, deal with engines primarily intended to be applied in vehicles operating far above of the sea level, where the atmospheric pressure is very low. Therefore, in the following calculations the atmospheric pressure will be neglected. 2.1. Pressurizing gas mass From the analysis done in [1], about the propellant tank pressurization, using the energy conservation principle, the next expression can be obtained: ⎛ ⎞ ⎜ ⎟ p V pp ⎜ γ g ⎟ m = (2.1.1) g R T ⎜ p ⎟ g 0 ⎜ g ⎜1− ⎟ ⎝ po ⎠ Comparison of Liquid Propellant Rocket Engine Feed Systems - 1 - 5 where, mg: Pressurizing gas mass (kg). pp: Propellant tank instantaneous pressure (Pa). pg: Gas tank instantaneous pressure (Pa). po: Pressurizing gas initial pressure (Pa). To: Pressurizing gas initial temperature (K). 3 Vp: Propellant volume (m ). Rg: Pressurizing gas constant (J/kgK). γg: Pressurizing gas specific heat ratio. To foresee the scope of this analysis, the assumptions that allow deriving the previous equation will be enunciated: • Adiabatic process. • Ideal gas. • Negligible initial mass inside the pipes and propellant tanks. It will be assumed that the instantaneous pressure in the gas and propellants tanks is the same, that is, there are no losses in the pipes connecting them. Also, it is interesting to refer all feed system pressures to the combustion chamber pressure, which is a project parameter [3]. Based on this criterion, the following constant is defined: p p pg k p = = (2.1.2) pC pC where pC is the combustión chamber pressure (Pa). Not all the volume of a propellant tank is occupied by this one. A small part is occupied by gas and that portion of the total volume of the tank is denominated ullage. This is the necessary space to allow the propellant thermal expansion, the accumulation of gases that were originally dissolved in the propellants and to contain the reaction products of the slow reactions, which occurs during storage [1]. To assess this quantity in the analysis, an additional constant relating both volumes will be introduced, also assuming that it is the same for both tanks: Vtf Vto ku = = (2.1.3) V f Vo 3 where, Vtf: Fuel tank volume (m ). 3 Vto: Oxidizer tank volume (m ). 3 Vf: Fuel volume (m ). 3 Vo: Oxidizer volume (m ). Besides, the gas constant should be expressed in terms of their molar mass, thus: Ru Rg = (2.1.4) M g where, Ru: Universal gas constant (8314.41J/kmolK). Mg: Pressurizing gas molar mass (kg/kmol). Furthermore, volume and mass will be related through the following expressions: Comparison of Liquid Propellant Rocket Engine Feed Systems - 1 - 6 * * mo ρo v o O / F = * = * (2.1.5) m f ρ f v f * O / F ⎛ 1 ⎞ * * v o = ⎜ ⎟ m p = α o m p (2.1.6) ρo ⎝1+ O / F ⎠ * 1 ⎛ 1 ⎞ * * v f = ⎜ ⎟ m p = α f m p (2.1.7) ρ f ⎝1+ O / F ⎠ * 3 where, vo &v f : Oxidizer or fuel volumetric flow as designated with “o” or “f” (m /s). * * mo &m f : Oxidizer or fuel mass flow as designated with “o” or “f” (kg/s). 3 ρo & ρf: Oxidizer or fuel density (kg/m ). O/F: Propellant mixture ratio. mp: Propellant total mass (kg). Note that once defined the αo and αf constants is possible to write: α o + α f = α (2.1.8) V p = Vo +V f = α o m p + α f m p = α m p (2.1.9) Finally, a safety constant kg is defined, which provides a margin to account the gas mass that, at the end of the operation cycle, will stay inside the gas tank and in the feed system pipes. Thus, the equation 2.1.1 becomes: ⎛ ⎞ ⎜ ⎟ M m p m = k k k γ α g ⎜ p C ⎟ g pg u g ⎜ ⎟ (2.1.10) RuT0 pC ⎜1− k p ⎟ ⎝ po ⎠ 2.2.
Details
-
File Typepdf
-
Upload Time-
-
Content LanguagesEnglish
-
Upload UserAnonymous/Not logged-in
-
File Pages178 Page
-
File Size-