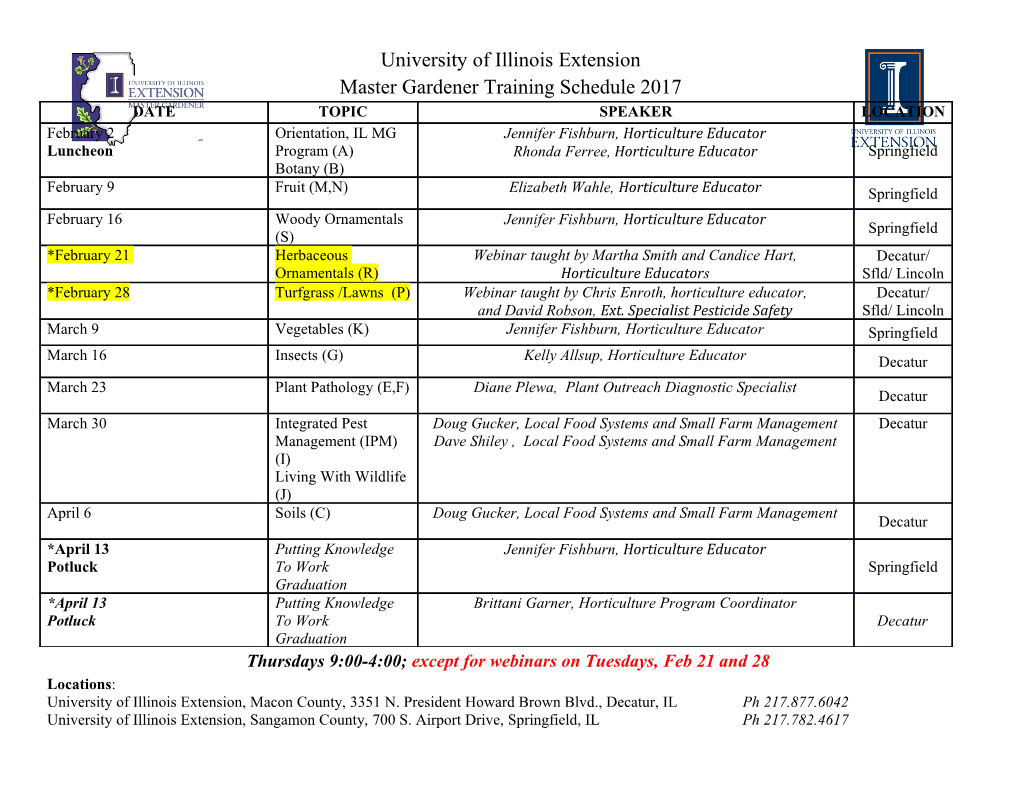
Miniature Stirling-type pulse-tube refrigerators Citation for published version (APA): Hooijkaas, H. W. G. (2000). Miniature Stirling-type pulse-tube refrigerators. Technische Universiteit Eindhoven. https://doi.org/10.6100/IR534736 DOI: 10.6100/IR534736 Document status and date: Published: 01/01/2000 Document Version: Publisher’s PDF, also known as Version of Record (includes final page, issue and volume numbers) Please check the document version of this publication: • A submitted manuscript is the version of the article upon submission and before peer-review. There can be important differences between the submitted version and the official published version of record. People interested in the research are advised to contact the author for the final version of the publication, or visit the DOI to the publisher's website. • The final author version and the galley proof are versions of the publication after peer review. • The final published version features the final layout of the paper including the volume, issue and page numbers. Link to publication General rights Copyright and moral rights for the publications made accessible in the public portal are retained by the authors and/or other copyright owners and it is a condition of accessing publications that users recognise and abide by the legal requirements associated with these rights. • Users may download and print one copy of any publication from the public portal for the purpose of private study or research. • You may not further distribute the material or use it for any profit-making activity or commercial gain • You may freely distribute the URL identifying the publication in the public portal. If the publication is distributed under the terms of Article 25fa of the Dutch Copyright Act, indicated by the “Taverne” license above, please follow below link for the End User Agreement: www.tue.nl/taverne Take down policy If you believe that this document breaches copyright please contact us at: [email protected] providing details and we will investigate your claim. Download date: 28. Sep. 2021 Miniature Stirling-Type Pulse-Tube Refrigerators PROEFSCHRIFT ter verkrijging van de graad van doctor aan de Technische Universiteit Eindhoven, op gezag van de Rector Magnificus, prof.dr. M. Rem, voor een commissie aangewezen door het College voor Promoties in het openbaar te verdedigen op dinsdag 13 juni 2000 om 16.00 uur door Herbert Willem Gerrit Hooijkaas geboren te Schoonhoven Dit proefschrift is goedgekeurd door de promotoren: prof.dr. A.T.A.M. de Waele en prof.dr. G. Thummes Druk: Universiteitsdrukkerij TUE CIP-DATA LIBRARY TECHNISCHE UNIVERSITEIT EINDHOVEN Hooijkaas, Herbert Willem Gerrit Miniature Stirling-type Pule-Tube Refrigerators / by Herbert Hooijkaas. - Eindhoven: Technische Universiteit Eindhoven, 2000. - Proefschrift. - ISBN 90-386-1559-0 NUGI 812 Trefw.: pulsbuis koeler / regenerator / cryogenie / thermodynamica Subjects: pulse-tube refrigerator / regenerator / cryogenics / thermodynamics Aan mijn vader Abstract ABSTRACT Pulse-tube refrigerators have the potential to be widely applied for producing low- temperatures. The main benefit of these systems is the absence of moving mechanical parts at the regions of low temperature. This lowers the induced mechanical vibrations significantly and strongly improves the reliability of these systems. Other benefits are lower manufacturing costs and less magnetic noise. This research focuses on the development of miniature Stirling-type pulse-tube refrigerators. These systems are characterized by the direct connection of cooler and compressor and generally have a driving frequency between 20 and 60 Hz. The desired cooling power of the considered systems is 0.5-1.0 W at a temperature of 80 K and an input power of 40 W. In the development of these systems, as presented in this thesis, first the system is analyzed theoretically. Based on the conservation of mass, the equation of motion, the conservation of energy, and the equation of state of a real gas a general model of the pulse-tube refrigerator is made. The general model is specified for low-amplitude applications: a condition that is generally fulfilled by Stirling-type pulse tubes. Assuming this a harmonic approximation can be applied. The use of the harmonic approximation simplifies the differential equations of the model, as the time-dependency can be solved explicitly and separately from the other dependencies. The model applies only to systems in the steady state. Time dependent effects, such as the cool-down, are not described. From the relations the system performance is analyzed. Next, the effect of some conceptual improvements is analyzed. The harmonic model is implemented in a simulation program. The relations are linearized in this program and solved iteratively. In the iterations, the relations for mass accumulation and pressure drop are calculated simultaneously, while the temperature profile is calculated in a separate routine. This method is applied, as the mutual sensibility of these relations is rather weak and the calculation scheme becomes less complicated. In addition to the theoretical model and the simulation program, also experimental pulse tubes are developed. The model is validated with these systems. Some conceptual improvements, such as the inertance tube and the second inlet, are investigated experimentally. The influence of the phase angle, which is important I Miniature Stirling-Type Pulse-Tube Refrigerators for the efficiency, is investigated by means of a warm-end expander. This allows adjustment to any value of the phase angle. The experiments show that for the highest efficiencies, the compression of the gas in the tube should be carried out by a gas flow, which does not flow through the regenerator. Experimentally it has been shown that a cooling power of 400-500 mW at a temperature of 80 K can be achieved with the current technology, at input powers of 40 to 50 W. However, in the near future a cooling power of 1 W must be attainable, if optimizations are applied to the regenerator, regarding the matrix structure and the geometry. This has a high potential, as the regions of high flow resistance and relatively low heat-storage capacity are spatially separated. A modification of the different heat exchangers and the flow straightners in the tube will contribute to future improvements as well. Based on the experimental results and the model, a new pulse tube, which focuses on the performance and the producibility, is developed. Concluding: the miniature pulse tube technology is ready for low-power application at cryogenic temperatures. This holds especially for applications that require a low level of vibrations or high reliability. In the near future, the pulse-tube refrigerator might become a good substitute for the other coolers, as its manufacturing costs are lower as well. II Contents CONTENTS Abstract I Contents III Nomenclature VII Chapter 1 Introduction 1 1.1 General introduction 2 1.2 Introduction to this thesis 6 Bibliography 7 Chapter 2 Dynamics of the non-ideal gas 9 2.1 Equation of state 10 2.2 Gas distribution 10 2.2.1 Conservation of mass 10 2.2.2 Equation of motion 12 2.3 Thermodynamic properties 13 2.4 Energy conservation in an open volume 15 Bibliography 21 Chapter 3 Pulse-tube model for harmonic signals 23 3.1 Practical operation 24 3.2 Mathematical properties 25 3.2.1 Characteristics 25 3.2.2 Time derivations 25 3.2.3 Complex notation 25 3.2.4 Multiplication of signals 26 3.3 The gas behavior 27 3.4 Temperature oscillations 28 3.5 Energy flow 32 3.6 Gas flow and accumulation 36 Bibliography 42 III Miniature Stirling-Type Pulse-Tube Refrigerators Chapter 4 Model analysis 43 4.1 Flow properties 44 4.2 Cooling power and losses 46 4.3 Optimization of the idealized orifice pulse tube 50 4.4 Conceptual improvements 51 4.4.1 Double-inlet pulse-tube refrigerator 51 4.4.2 Inertance pulse-tube refrigerator 52 4.4.3 Warm-end expander pulse-tube refrigerator 54 4.4.4 Multistage pulse-tube refrigerator 55 4.4.5 Multi-bypass pulse-tube refrigerators 57 Bibliography 58 Chapter 5 Simulation model 59 5.1 The pressure wave and mass distribution 60 5.1.1 Pressure amplitude estimation in the buffer 61 5.2 Average temperature profile 63 5.2.1 Heat exchanger temperatures 65 5.3 Simulation structure 69 5.3.1 Standard pulse-tube refrigerators 69 5.3.2 More advanced pulse-tube refrigerators 70 5.3.3 Pulse tube optimizations 72 5.4 The system parameters 73 5.4.1 Effective heat exchange and storage function; G 73 5.4.2 The flow resistance; RL 75 5.4.3 The mass storage capacity; CL 76 5.4.4 The damping factor; DL 77 5.5 Convergence of the iteration loops 78 Bibliography 79 Chapter 6 Simulations and experiments 81 6.1 Experimental setup 82 6.1.1 Pressure measurements 82 6.2 Inline pulse tubes 84 6.2.1 Dimensions 84 IV Contents 6.3 Results 86 6.3.1 Influence of the operational settings 86 6.3.1.1 Flow resistance 86 6.3.1.2 Frequency 88 6.3.1.3 Input-power 89 6.3.2 Temperature profiles 90 6.3.3 Discussion 91 6.4 U-shaped pulse tubes 91 6.4.1 Dimensions 92 6.4.2 Orifice pulse tube 93 6.4.2.1 Flow resistance 94 6.4.2.2 Buffer volume 95 6.4.2.3 Heat exchanger configurations 96 6.4.3 Inertance pulse tube 97 6.4.4 Double-inlet inertance pulse tube 100 6.5 The influence of the warm-end phase angle 101 6.5.1 Simulations 102 6.5.2 Warm end expander pulse tube 103 6.5.2.1 Active expander operation 103 6.5.2.2 Passive expander operation 104 6.5.3 Discussion 107 6.6 The pulse-tube prototype 107 6.6.1 Dimensions 107 6.6.2 Results 108 6.6.3 Discussion 109 Bibliography 109 Chapter 7 Discussion 111 Samenvatting 113 Dankwoord 115 Curriculum vitae 116 V Nomenclature NOMENCLATURE Greek symbols L scaled heat exchange [1/s] G scaled heat capacity D spatial difference operator Ñc critical gradient a isothermal pressure dependence l thermal conductivity [W/mK] of non-ideality x effective flow friction factor [1/m] a heat exchange coefficient [W/m2K] r density [kg/m3] b isobaric temperature dependence s inverse of flow resistance [ms] of non-ideality t characteristic heat transfer time [s] g adiabatic expansion coefficient fm mass flow [kg/s] 3 dth thermal penetration depth [m] fV volume flow [m /s] e linearity factor c adiabatic pressure dependence z inverse vol.
Details
-
File Typepdf
-
Upload Time-
-
Content LanguagesEnglish
-
Upload UserAnonymous/Not logged-in
-
File Pages131 Page
-
File Size-