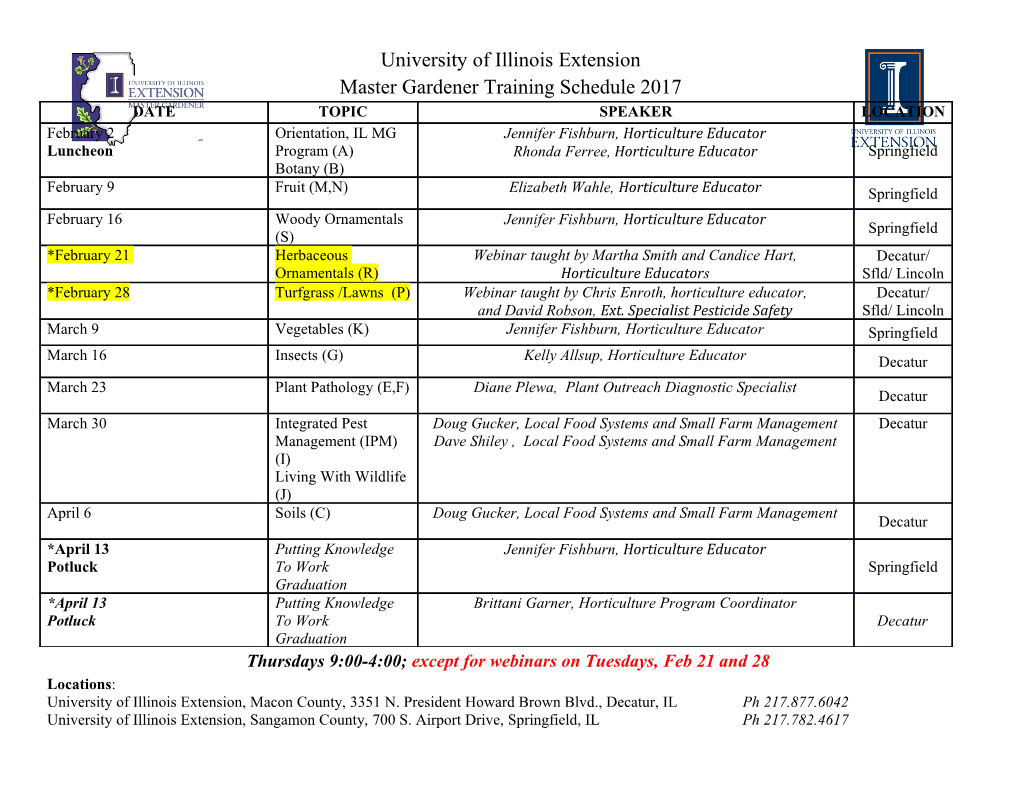
Commercial Rooftop HVAC Energy Savings Research Program Bench Test Report June 2008 Prepared by: Mark Cherniack – Senior Program Manager Howard Reichmuth PE – Senior Engineer Prepared for: Northwest Power and Conservation Council 851 SW Sixth Avenue, Suite 11100 Portland, Oregon 97204 (503) 222-5161 Acknowledgements Acknowledgements The design and set up of the testing chamber, testing of the components/systems, and initial data assessment was completed by David Robison, P.E., Stellar Processes, Bob Davis, Ecotope and Dennis Landwehr, P.E. under subcontract to New Buildings Institute (NBI). NBI staff is responsible for the final report and conclusions. The following organizations provided funding to make this phase of the ongoing research possible. They responded to an invitation to participate in this opportunity to further the potential for cooperative research partnerships among interested participants nationwide on small commercial HVAC system issues. Their contributions are much appreciated. From the Pacific Northwest through the Northwest Power and Conservation Council Avista Utilities Bonneville Power Administration Eugene (OR) Water and Electric Board Energy Trust of Oregon Idaho Power PacifiCorp (non-Energy Trust area) Puget Sound Energy Snohomish Public Utility District From the Northeast Cape Light Compact (through Northeast Energy Efficiency Partnership-NEEP) Connecticut Light & Power (NEEP) Long Island Power Authority (NEEP) The United Illuminating Company (NEEP) Western Massachusetts Electric (NEEP) Efficiency Maine Efficiency Vermont National Grid New York State Energy Research and Development Authority NSTAR The Project Team also acknowledges the responsiveness of Honeywell Product Manager Adrienne Thomle and her engineering staff for making recommendations that strengthened the research, as well as responding with new product designs that will allow economizers to fully function as intended in saving energy. Executive Summary This work has been done as part of the Commercial Rooftop HVAC Energy Savings Research Program which includes four interdependent elements: 1) bench testing of economizer controls, 2) field testing of repair protocols, 3) devising an appropriate measurement and verification (M&V) approach and 4) developing a savings prediction methodology based on prototypical buildings. Taken together, these elements are intended to lead to the development of a reliable field repair protocol with a higher level of confidence in the associated energy savings. This document summarizes the results of only the first of the four elements, the bench testing of economizer controls. This document is also an interim summary of results because the bench testing capability is being retained and will be used further during the project. The bench testing research was applied to the most typical type of dry bulb economizer controller using controlled environmental chambers to determine the environmental and control factors that influence the operation of the economizer. The principal findings are: • The sensors and economizer controller system exhibits an operational pattern (deadband) that can significantly interfere with expected economizer operation by limiting the economizer potential during seasons with warm nights. We refer to this as “hysteresis” in this report. • The sensor and controller components tested exhibited a consistent low bias in temperature. Environmental temperatures that are supposed to activate the controller do not correspond to those specified by the manufacturer. The apparent wide sensor and controller tolerance leads to loss of economizer energy savings potential. • The enthalpy sensors tested appear initially to be more accurate than the dry-bulb sensors tested. However, this stage of research did not measure sensor response over the range of humidity that would be necessary to fully test enthalpy sensors. Some “hysteresis” is present with enthalpy sensors as was exhibited in the dry-bulb sensors tested, but the magnitude of the deadband across a range of conditions is not yet bounded by the available data. Additional testing of the enthalpy sensor is still underway. • A dual differential economizer strategy was tested and compared to the single changeover strategy as a potential improvement. The differential control strategy used in conjunction with a 2-stage thermostat has the potential for a more sophisticated control than a simple single change point strategy. However, test results showed only modest improvement from this control strategy. This strategy may be more complex to execute in a simplified and consistent field procedure. It also requires a 2-stage thermostat, which is recommended in any case for effective economizer performance. • A proposed “work-around” solution in the field would substitute an inexpensive contractor’s thermostat (<$10) for the temperature sensor commonly in use. This combination operates with very little hysteresis and is expected to increase the amount of economizer operation. This work around is amenable to a simple and consistent field procedure. • Honeywell personnel provided helpful feedback on the testing protocol. They do not support the proposed work around due to concerns about high feed-in amps to the controller, even though a resistor could be added the circuit. - 3 - • The test apparatus was successful in providing an inexpensive set of controlled environmental chambers. Taken together these findings cast significant doubt on the capability of existing economizers, specifically with the Honeywell C7450 dry bulb/temperature sensor, to perform according to their potential. Given that economizers have been embodied in building codes on the assumption of performance consistent with their specification, there is an urgency to apply corrective measures. Accordingly, the immediate recommendations are: • A dialog has been opened with Honeywell, the controller/sensor manufacturer, concerning the findings in this report and the proposed work-around. These findings suggest that a significant group of existing economizer controls currently in operating RTUs cannot access the full economizer potential. This is a major functionality problem with significant kWh waste that needs addressing and it is important to continue to access the knowledge of the equipment manufacturer in this regard. • Honeywell, in response to the bench test results that provided important ‘customer’ input to the sensor/controller product manager, has developed a new, advanced dry-bulb sensor that should resolve the field problem. Honeywell has committed to sending several beta stage sensors for bench and field testing in July. If this new sensor works as expected, further discussions about a field retrofit package for utility programs will be held with Honeywell. Commercial availability is expected 3rd quarter of 2008. • Utilities should assess the impacts of identifying the economizer controller sensor equipment described in the report, that may be installed in new RTUs that are receiving financial incentives through current or planned utility energy efficiency/DSM programs. If the particular Honeywell sensor product is present in these new units, a decision must be considered about including a modification to the equipment at installation time so as to not install the problem sensor. A field work-around employing the contractor’s thermostat or snapdisk could be used in lieu of the problematic temperature sensor. The work-around should be based on the single change point control and not use the differential control. The implementation of the work around should be viewed as temporary until the new Honeywell sensor is commercially available. Alternately, utility high efficiency RTU incentive programs could at least flag those systems for a follow up sensor retrofit. • The bench test has been expanded to include Honeywell enthalpy-based economizer controls. It is could be expected that the hysteresis effects observed for dry bulb temperature sensors would not be as significant in the case of enthalpy sensor otherwise, the use of economizing in the more humid eastern US will also be limited relative to its potential. At the time of this report, data is still too sparse from the enthalpy sensor tests for reporting conclusions. - 4 - Introduction The principal conservation benefit from using an economizer proceeds from using cooler outside air for space cooling instead of air-conditioning when conditions permit. Unfortunately, detailed monitoring revealed that economizing is often ineffective. One cause of this problem is due to a known problem with the economizer control system, referred to here as “hysteresis.” In the typical control mode, the controller must sense a sufficiently cold outdoor temperature before economizing is allowed – this temperature is typically 10ºF cooler than the indoor temperature. This required temperature is referred to as the nominal changeover temperature. Earlier monitoring studies have shown that this “hysteresis” effect prevented economizing during warm summer months in mild climates because the coldest nighttime temperatures were not cold enough to allow economizing. The same problem was not observed in climates with a larger diurnal temperature swing and colder night temperatures. The purpose of the current investigation is to test a typical controller system, identifying the extent to which hysteresis or poor sensor calibration might limit full operation, and to develop and test a “work-around” solution as part of the development of the field service
Details
-
File Typepdf
-
Upload Time-
-
Content LanguagesEnglish
-
Upload UserAnonymous/Not logged-in
-
File Pages23 Page
-
File Size-