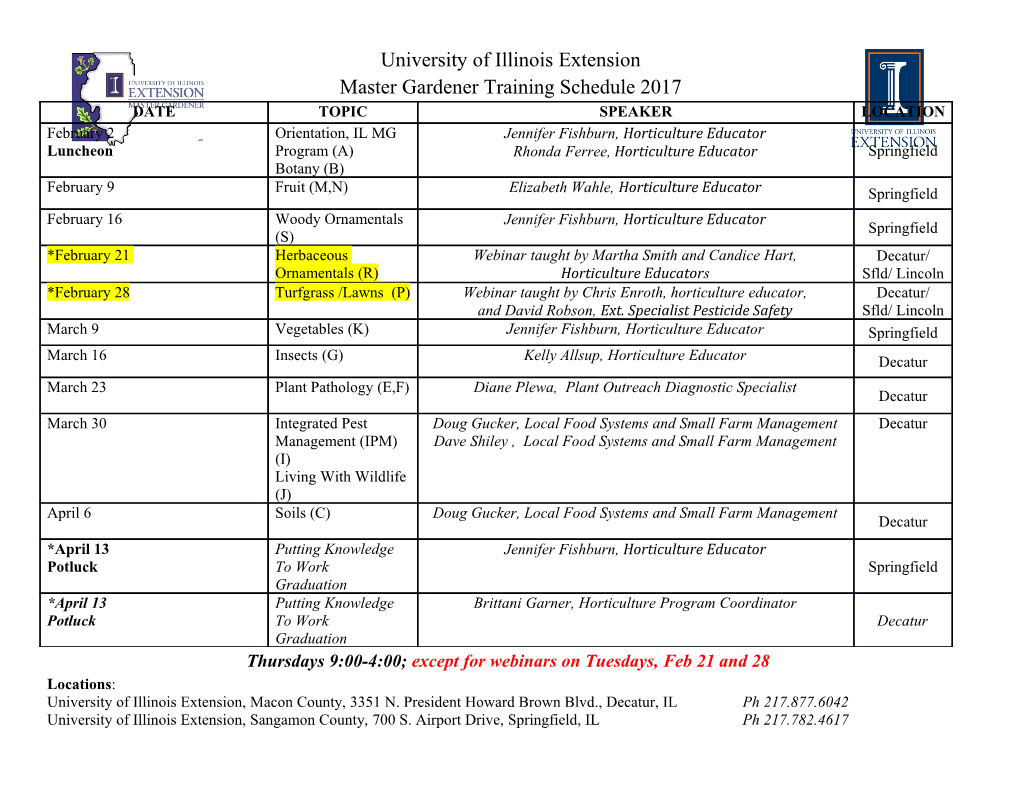
Technology Forum on Small Body Scientific Exploration – 4th Meeting of the NASA Small Bodies Assessment Group Michael Patterson NASA Glenn Research Center John Brophy Jet Propulsion Laboratory California Institute of Technology January 24, 2011 National Aeronautics and Space Administration www.nasa.gov 1. In-Space Propulsion Overview 2. Current In-Space Investments for Robotic Missions 3. Description of Electric Propulsion 4. Current Technology Investments and Development Status 2 3 Flight System Development Future Applications Non-toxic propellant-based propulsion systems (LOX, LH2, LCH4, Ethanol) Main Propulsion Systems (MPS) Propulsion systems for orbit transfer, orbit injection, spacecraft maneuvering, landing, and ascent Development of component technologies (igniters, exciters, injectors , combustion chambers, nozzles) for non-toxic propellants Current Focus Areas • LOX/LCH4 propulsion technologies for main propulsion systems (MPS), reaction control systems (RCS), and propellant storage and distribution • Development of Orion Service Module propulsion system Reaction Control Systems (RCS) • Preliminary trade studies, requirements development, and planning for Altair ascent propulsion subsystem Research and Technology Development Materials Evaluation Combustion Diagnostics Ignition Performance Propellant Properties 4 Future Applications • Next generation ion propulsion system for deep-space science missions (NEXT) • Propulsion systems for Earth orbital applications including satellite servicing, repositioning, re-boost, orbital debris removal, and de-orbit • High power propulsion systems for cargo transportation in support of future human crewed missions beyond LEO Technology and Flight System Development of Ion and Hall Thrusters Current Focus Areas • Ion and Hall thruster design, fabrication, evaluation 200 kWe Class SEP Stage • VASIMR or other high power EP • Innovative concept development and evaluation technology • Reusable orbit transfer • Power electronics design, bread-boarding, evaluation • Robotic interplanetary cargo transfer • System integration, system qualification and acceptance testing • Thermal, stress, vibration analysis and test • Capability to fabricate laboratory and flight hardware SEP Stage Upgrade • 90 kWe class system Solar Electric Propulsion (SEP) Stage • Orbital servicing and debris removal • 30 kWe class system with advanced PV and AR&D technologies • ISS reboost • NASA science missions • Science missions, e.g., Mars Sample/Return • Small commercial servicing applications in Earth orbit • Use of NEXT ion or Hall thruster technology 5 Future Applications • High-thrust/high-Isp injection stage to Mars and other destinations within inner solar system • Cargo and crewed transportation for human missions to the Moon, NEOs and Mars • Strong synergy with existing chemical rocket and stage hardware • Evolvability to propulsion and power (“Bimodal operation”), variable thrust and Isp (“LOX-afterburner” nozzle), ISRU and hybrid operation (BNTR with EP) Integrated NTP Crewed Vehicle Design for Mars DRA 5.0 Current Focus Areas • Vehicle / engine concept design and analysis, and requirements definition for Human Mars missions (DRA 5.0) • Engine conceptual design, analysis and modeling includes neutronics, thermal, fluid, stress and mass estimation • Fuels assessment and development planning with DOE • Innovative NTP engine design concept development • Infrastructure and test facility needs assessment LOX Augmented Nuclear Rocket (LANTR) Engine Demonstration Advanced Technology: Bimodal Propulsion and Power 6 In-Space Propulsion Investments for Robotic Missions Objective: “Develop in-space propulsion technologies that enable or benefit near to mid-term NASA science missions by significantly reducing travel times required for transit to distant bodies, increasing scientific payload capability or reducing mission costs.” ISP will enable access to more challenging and interesting science destinations, including enabling sample return missions. Planetary Earth Entry Vehicles Systems & Sample Return Propulsion Ascent Vehicles /Aerocapture Mission Studies Propulsion Tech High-Temp Engine TPS & Structures (AMBR) Mars Ascent Vehicle Tools Ultra Lt Wt Tank NEXT GN&C Mission Studies System Studies Hall Thruster Multi-Mission Earth Entry Vehicle Component Tech • The ISPT project addresses the primary propulsion technology needs for the agency’s future robotic science missions • The current ISPT focus is on TRL 3-6+ product development 7 8 Chemical propulsion converts the energy stored in the molecular bonds of a propellant into kinetic energy • Typically high thrust to weight (required for launch) • Exhaust velocity is limited by the chemical energy available • Higher exhaust velocities can reduce required propellant mass: M f exp-ΔV v M0 e • For a given change in velocity (ΔV), the delivered mass (Mf) depends on the propellant exhaust velocity (ve) • Once in space, engines that provide a higher exhaust velocity can significantly reduce propellant mass requirements 9 Electric propulsion (EP) uses electrical power to provide kinetic energy to a propellant • Decouples kinetic energy from limitations of chemical energy • Provides higher exhaust velocities than chemical engines - Reduces propellant mass needed for a given impulse - Allows reduction in launch mass a/o increase in payload; can provide substantial benefits in mission cost • Increases launch window as compared to all-chemical systems in certain mission scenarios • Electric propulsion primarily benefits large total impulse missions - Orbit raising, repositioning, long-term station keeping - Cis-lunar, planetary and deep space missions - Precise impulse bits for formation flying 10 Additional considerations… • Significantly lower thrust to weight than chemical engines - Small but steady acceleration vs. short-burn chemical engines - EP engines must be designed for long life (thousands of hours) • Increased dry mass due to: - Solar arrays - Power processing units - and Other EP-specific hardware • Spacecraft integration considerations: - Electric power requirements - Plasma plume and EMI • Propulsion system trades performed to evaluate whether a given mission will benefit from the use of electric propulsion 11 Electric thrusters are categorized by their primary acceleration mechanism: • Electrothermal – Resistojets & Arcjets (commercial flight units available) heat gas and expand gas thru a nozzle – Auxiliary Propulsion; typically ≤ 1 kWe Resistojet thrusters use resistive heating elements to increase the thermal energy of a gas propellant Arcjet thrusters use an electric arc to increase the thermal energy of a gas propellant • Electrostatic – Hall effect and Gridded Ion thrusters (commercial flight units + development) generate high voltages for ion (plasma) acceleration – Auxiliary and Primary Propulsion; typically 1 to 10’s of kWe Ion thrusters use closely spaced high voltage grids to create an electrostatic field Hall thrusters use magnetically trapped electrons to create an electrostatic field 12 Electric thrusters are categorized by their primary acceleration mechanism: • Electromagnetic – Pulsed plasma (commercial flight units available), Magnetoplasmadynamic and Pulsed Inductive thrusters (laboratory model) apply a Lorentz (JxB) force for plasma acceleration – Auxiliary and Primary Propulsion Pulsed Plasma thrusters use a pulsed, repetitive current to ablate solid propellant, induce magnetic field (JxB) Magnetoplasmadynamic thrusters use a high power, steady- state current to ionize gas propellant, induce magnetic field (JxB) 13 14 Objective: Develop advanced ion propulsion system Thruster Attribute with improved performance and life characteristics Thruster power range, kW 0.5 - 6.9 to reduce user costs and enhance/enable a broad Max. Specific Impulse, s 4,190 range of NASA SMD missions Thrust range, mN 26 - 236 Propellant Throughput, kg 450* Mass (with harness), kg 13.5 Envelope dimensions, cm 43.5 x 58.0 Power Processing Unit Attribute Power Processing Unit mass, kg 33.9 Envelope dimensions, cm 42 x 53 x 14 Input voltage range, V 80 - 160 Feed System Attribute High Pressure Assembly mass, kg 1.9 NEXT gridded ion NEXT PM ion thruster operation thruster Low Pressure Assembly mass, kg 3.1 NEXT Thruster NEXT addresses the entire ion propulsion String system PPU Thruster - Gridded ion thruster DCIU - Power processing unit (PPU) - Propellant management system (PMS) HPA - System integration (including gimbal and LPA control functions) Gimbal Primary Partners * Rated Capability Goal 300Kg Design/Qualification Goal (1.5x Rated) 450Kg - NASA Glenn Research Center: Lead Projected 1st Failure >750Kg Potential Rated Capability 500Kg - JPL, Aerojet Corp., L3 Comm. 15 Critical tests have been PM1 PM1R PPU Feed Gimbal System completed, or are imminent, on high fidelity hardware Functional & Complete Complete Complete Complete Complete Performance Testing Qual-Level Vibration Test Complete Complete FY11 Complete Complete Qual-Level Thermal/ Not Complete Complete FY11 Complete Vacuum Test planned FY11 Key activities : • PPU re-verification test, and environmental test • Single-String System Integration Test: Complete • Long-Duration Test (LDT) • Multi-String System Integration Test: Complete • Phase II Review • Thruster Life Test: Completed goal of 450Kg throughput •Technology Maturation Review • >34,000 hours and >570 kg of xenon processed to date FY11-13 Key activities: • Life Test will continue through 750Kg or first failure • PPU design iteration
Details
-
File Typepdf
-
Upload Time-
-
Content LanguagesEnglish
-
Upload UserAnonymous/Not logged-in
-
File Pages44 Page
-
File Size-