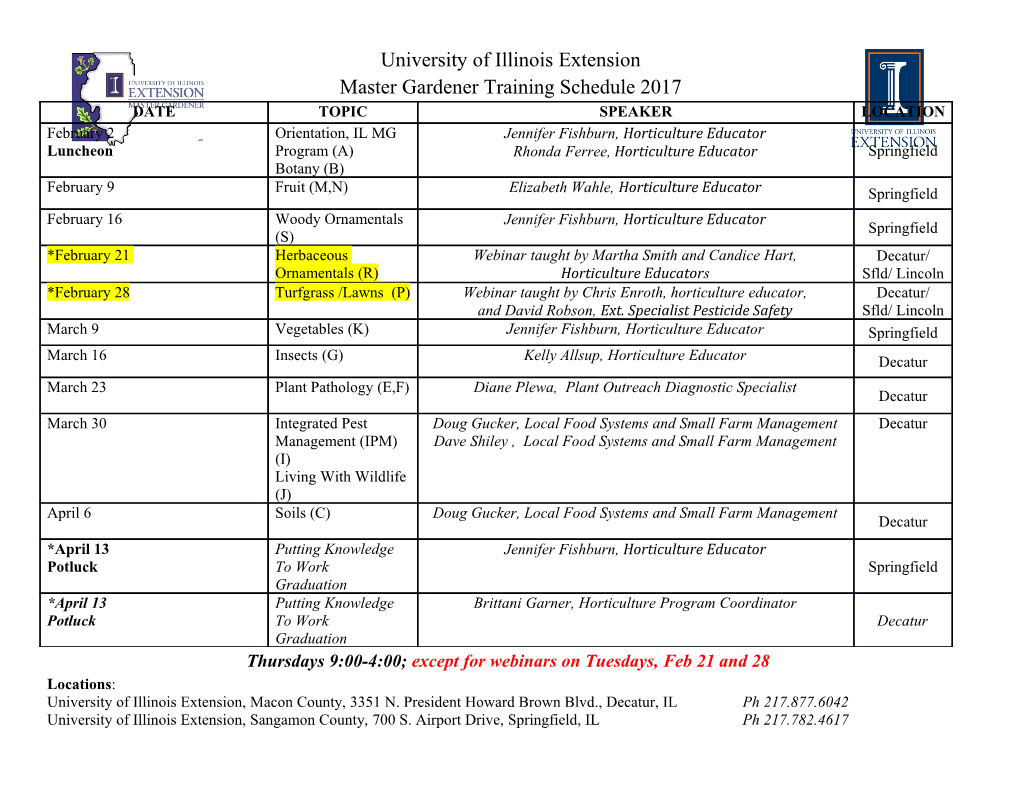
The ABCs of Steelmaking Inspectors can perform their duties better if they possess an understanding of the qualities of steel, the most common base material they work with, and its inherent defects BY RAYMOND R. SHEPARD This article is the first in a four-part series dealing with steelmaking and how the quality of the base material affects the manufactured products inspectors must examine. It gives a his - torical perspective on iron and steel - making and an overview of the steel manufacturing process. The next issue will highlight modern steel making with a basic oxygen furnace, and the final two articles will deal, respective - ly, with steelmaking using an electric arc furnace and the rolling and form - ing of steel. nspectors and nondestructive examination (NDE) technicians Iwork with a wide range of mate - rials — plastics, composites, and wood, as well as metals. Of all the materials we inspect, however, one is so ubiquitous, with an impact so far-reaching, that the majority of Fig. 1 — The Saugus Iron Works finery is shown center image. Notice the waterwheel that our society takes it for granted. powered the bellows for the hearth. The casting shed of the blast furnace appears at the bottom That material is steel. left. (Photo by Raymond R. Shepard.) Inspectors and NDE techni - cians perform many types of tests. We perform tasks ranging from quality control of base materials other metal. The metalworking industry’s impact on the econo - to verifying the success of the processes used for joining mate - my is significant, accounting for a large portion of the gross rials. In essence, our job is to investigate one or more properties national product of the United States. Today, we cannot imagine of a material and determine if that material meets or exceeds what our society would be like without the far-reaching effects design requirements. The inspection method utilized for a par - of steel. ticular application may depend on the material being investigat - But what exactly is steel? Steel is an alloy. An alloy is a sub - ed, where in the manufacturing process the inspection is being stance consisting of a metal and at least one other element. performed, and the severity of the discontinuities that apply to Steel, therefore, consists of iron (Fe), minute amounts of carbon the component in question and how they affect the safe use of (C), and possibly other alloying elements, depending on the that component. required properties of the steel. In any alloy system, the metal - To do our jobs properly, we need to understand not only the lic element of the greatest percentage is called the solvent. The types of defects associated with the joining process but also the alloying element is called the solute. inherent defects in the base material. To address this, we must There are several steps involved in making steel. The first have a firm understanding of how the material we are inspecting step is the production of pig iron from iron ore. The carbon con - is made. This article examines the history and manufacture of tent of pig iron is too high for it to be used as an end product; it iron and steel. is too brittle. Carbon content must be reduced to levels that are appropriate for the type of steel being produced. This task is per - formed in furnaces that make steel in batches of hundreds of The Steelmaking Process tons per heat. It is then cast into ingots or sent to a continuous In 1854, Henry Bessemer devised an improved method for casting mill. Once steel is in ingot form, it may be further making steel. Production soared and the face of the earth processed by rolling mills and formed into a variety of shapes changed forever. Worldwide, more steel is produced than any and products. RAYMOND R. SHEPARD ([email protected]) is Quality Specialist/Training Coordinator, Kakivik Asset Management and Adjunct Professor, University of Alaska, Fairbanks College of Rural Alaska. FALL 2003 • 19 Fig. 3 — A blast furnace in Fairfield, Ala. Notice its size. Historically, as blast furnaces grew larger in capacity, technology had to be developed that was more efficient in moving large amounts of raw materials faster. (Photo courtesy of United States Steel Corp.) Fig. 2 — This bellows blows air on one of the finery hearths. The late 1800s that coke came into use as the primary fuel in blast same type of bellows system also supplied air to the blast furnace. furnaces. Today, coal-tar chemicals released during the coking The shaft is connected to a waterwheel outside the building. (Photo process, such as asphalt, are vital industrial products. Due to a by Raymond R. Shepard.) better understanding of chemistry, modern blast furnaces use a combination of coke in the furnace and powdered coal added to Pig Iron: Ingredients and Process hot blast gases for their fuel. Iron production in a blast furnace is a chemical reduction Pig iron production starts with three main ingredients — iron process. At high temperatures, carbon has great affinity for oxy - ore, limestone, and a source of fuel — that are charged in a blast gen. When oxygen comes in contact with melted iron ore, car - furnace. Additionally, oxygen is required to convert the raw ore bon and oxygen combine to form carbon monoxide (CO) gas. into usable iron. While iron can be found in a natural state, it is The CO then combines with another molecule of CO to form very rare. For instance, meteorites are sources of natural iron, but carbon dioxide (CO ). Solid carbon is removed from the molten due to their scarcity, they could never be used for iron production 2 iron by conversion into a gas. In the furnace, gases work their on an industrial scale. Iron ore, however accounts for approxi - way to the top, while the heavier liquids fall to the bottom. The mately 5% of the earth’s crust. The waste material (noniron-bear - heated gas is vented off and recycled as hot fuel gas is delivered ing rock) in lower-grade iron ore must be removed. This waste to the blast furnace. material is called gangue from the word gangen meaning “to go.” Iron ore with concentrations of iron exceeding 50% can be directly charged into a blast furnace. Ores of lower concentration must be An Early American Blast Furnace refined through the process of beneficiation (concentration). The During colonial times, iron and steel were very scarce in the main ores utilized for iron making are hematite (Fe 2O3), mag - New World. England produced iron and steel, but in limited netite (Fe 3O4), and tacomite (Fe 3O3). quantities and not of the highest quality. Sweden and Finland Limestone acts as a fluxing agent within a blast furnace. It produced excellent steel; however, they released only limited performs an important function by removing impurities such as amounts for export to countries such as England. Additionally, sulfur. The limestone melts to form a liquid slag within the fur - England did not have the prodigious forests that the nace. Being less dense than liquid iron, the slag floats above it. As the slag builds up, it is periodically tapped and drained from Scandinavian countries possessed. Demand for steel outpaced the furnace. Historically, slag was disposed of as a waste prod - supply. Colonists in the New World realized they needed to pro - uct, but these days it may be used as aggregate in concrete or duce iron and steel themselves instead of relying on imports. In asphalt roadways. 1620, an ironworks of limited capability was started in In the past, charcoal was used to provide the fuel necessary Jamestown, Va., and met with minimal success. In 1646, the first for the reduction process; coke is used today. Blast furnaces blast furnace and comprehensive, integrated ironworks was required large volumes of charcoal, thus many furnaces were built along the banks of the Saugus River in Saugus, Mass. located in areas that had healthy forests. Coal could not be used Today, restored to its original state and now a U.S. National directly for the production of iron due to the fact coal contains Historic Site, the ironworks allows a glimpse of what iron pro - unacceptably high levels of sulfur and other impurities. When duction was like during the colonial period in America. experimenting with coal as a fuel, early ironmasters realized the Saugus Iron Works was technically advanced for its time and end product was too brittle to be of any use. on par with the leading technology found in Europe. As it pro - In England, Abraham Darby discovered a way to convert coal gressed through the site, iron production went from the blast into coke in the early 1700s. By placing coal in an oxygen- furnace to a finery, chafery, slitting mill, and then to a black - reduced atmosphere and burning it, the majority of the sulfur smith shop — Fig. 1. The slitting mill was state of the art and and other coal tar chemicals are driven off as gas, leaving produced elongated stock sold to blacksmiths for production of behind the carbon. Upon cooling, the resulting product is a items such as wagon wheel rims, nails, etc. Products produced hard, porous material. Darby then used the coke to produce cast at Saugus included finished wares such as cast iron stove backs iron. Darby kept his method of converting coal into coke a and pots, blooms and bars for resale, bar for nail manufacturing, secret for many years. In the United States, it wasn’t until the and forged products such as tongs and hinges. 20 • INSPECTION TRENDS Fig.
Details
-
File Typepdf
-
Upload Time-
-
Content LanguagesEnglish
-
Upload UserAnonymous/Not logged-in
-
File Pages4 Page
-
File Size-