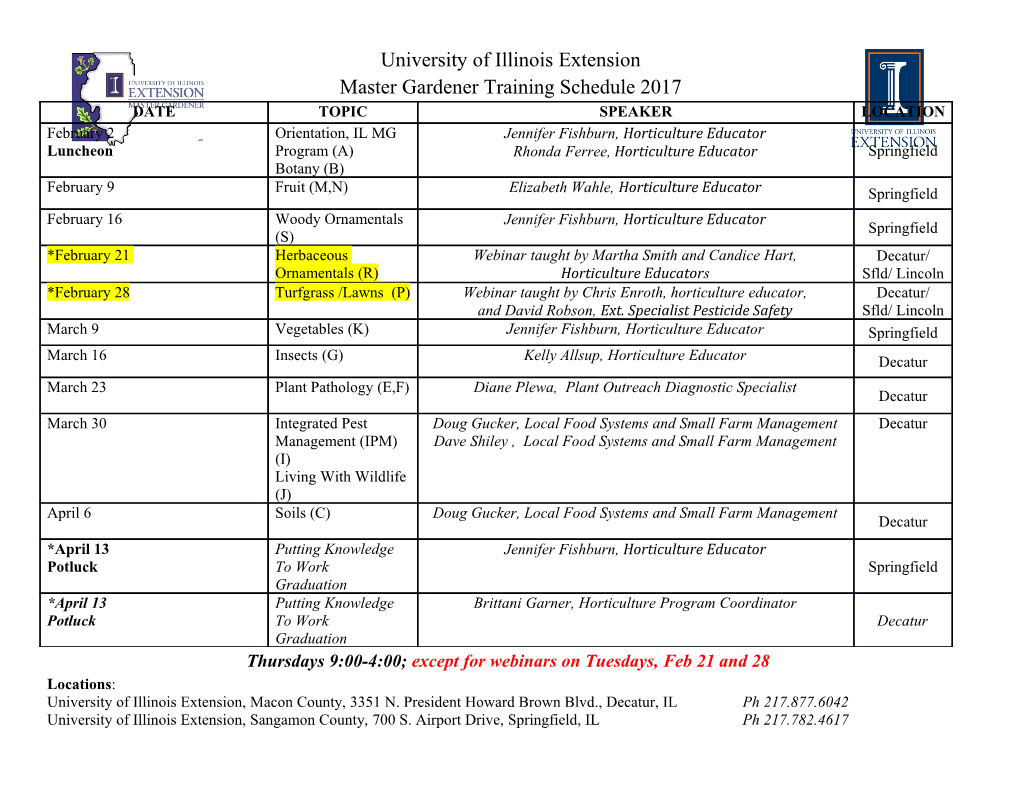
THE MEASURABLE DIFFERENCE. OXYGEN Training CAN CAN-FD FlexRay © DEWETRON GmbH | June 21 PUBLIC 1 CAN CAN bus available on > TRION-CAN (2/4 buses) > TRION-2402-MULTI (1 bus) > CAN (Control Area Network) is a serial bus system and was > TRION-1802/1600-dLV (1 bus) initiated 1983 by BOSCH and is mainly used in the 21 June > TRION-1820-MULTI (1 bus) > TRION(3)-18x0-MULTI (1 bus) automotive industries > Differential data transmission, CAN-High, CAN-Low ref. to CAN-GND > High Speed CAN (1 Mbaud) for short distances and much data vs. | GmbH DEWETRON © Low Speed CAN (125 kBaud) for long distances and reduced data > Data: 0-8 times 8-bit 2 CAN – CHANNEL SETUP ① In case of TRION-CAN and TRION- 1802/1600-dLV, go to the channel setup ⑥ of the respective CAN channel ① ② In case of TRION-MULTI: CAN bus is 21 June available on AI 1; Turn AI 1 into CAN mode and enable the CAN bus at the bottom of the Channel List ③ Open the CAN channel setup afterwards ② ④ Select the baudrate of the CAN bus © DEWETRON GmbH | GmbH DEWETRON © ⑤ Select Termination True if no termination is applied at the end of the transmission line to apply a 120 Ohm resistance ⑥ If all settings are correct, the frame ④ preview will show the received message ⑤ and the included data bits; ③ ⑤ 3 CAN – CHANNEL SETUP ⑦ Load the proper dbc- or arxml-file ⑧ A channel selection dialog will open; Select either all channels or only certain channels to be decoded and recorded 21 June ⑨ The decoded channels will appear as separate channels in the Channel List ⑦ and contain a preview of the decoded ⑩ signal ⑨ More channels can be selected and decoded by reloading the dbc-file and ⑧ | GmbH DEWETRON © selecting additional channels ⑩ Channels can be deleted by pressing the Clear all button It is also possible to decode the CAN stream offline by recording only the raw CAN stream and perform the steps ⑦ and ⑧ during data analysis 4 CAN – SHOW ONLY ACTIVE MESSAGES ① If Show only active messages is selected, all available messages from the loaded dbc-file with the actual bus traffic will be filtered. Messages that are currently not 21 June present on the CAN bus will not be displayed ② The J1939 Source address is displayed as well to clearly see which ECU is ② transmitting the data in case several ECUs are transmitting on the same CAN bus | GmbH DEWETRON © ③ If Replace Address is selected, only the CAN mesages from the specified Source Address will be displayed ① ③ 5 CAN – TIME BASE SELECTION ① Possibility to select internal 10 MHz clock for timestamping (100 ns steps) ② Possibility to align the CAN samples to the highest analog sample rate 21 June ③ Possibility to select an arbitrary timestamp alignment ④ The selection mainly affects the structure of the exported data ① ② ④ © DEWETRON GmbH | GmbH DEWETRON © CPADs are CAN datalogger ③ No functionality of Listen only during DAQ 6 CAN – SAE J1939 > Create DBC-File, adapt Message IDs to specify source address if necessary > Load DBC-File in Oxygen > J1939 is a protocol overlay of CAN-Bus used in heavy duty vehicles 21 June > Check Messages for right PGN and Source Address > Message IDs have standarized pattern > Oxygen CAN is able to decode J1939 CAN Frames > Loading of DBC-files with J1939 Messages > Showing PGN Number and Source Address | GmbH DEWETRON © > Decoding of Multi-frame messages > No special setting necessary 7 CAN OUT – GENERAL > Cyclic output of measurement data via TRION-CAN > Compatible with all TRION-Based CAN interfaces 21 June > Selectable transmission rate (0.1 Hz to 100 Hz) for each CAN-Message > Selectable delay for tuning the signal quality © DEWETRON GmbH | GmbH DEWETRON © > Receive/Transmit setting for each message > Messages have to be predefined within a .dbc (e.g. CANdb++ from Vector, installed with CANape) > Usecase: Testbed Integration, Automotive Testbed environment for electrical Powertrain testing 8 CAN OUT – SOFTWARE SETUP ① Load .dbc file with pre-defined messages ② Enable the required messages ③ Go to the channel setup and switch to 21 June Transmit mode ④ Open signal and add channel via ① Drag’n’Drop ⑤ Select output frequency and adjust delay if needed ② | GmbH DEWETRON © ③ ⑤ ④ 9 CAN OUT – INFLUENCE OF DELAY > Due to signal path delays in some parts in the software, realtime processing is not possible > With the selectable output delay, the user 21 June can choose between smoothness or fast reaction > Not used signals are transmitted as Value 0 70ms Delay = Default (Zero) © DEWETRON GmbH | GmbH DEWETRON © 10ms Delay 10 CAN-FD - GENERAL CAN-FD support with > Vector VN 1610 ➢ CAN has reached practical limits in current applications > Vector VN 1630 ➢ CAN buses exceed recommended busloads ( >50 %) 21 June > Vector VN 1640 ➢ High overhead for sending CAN messages ( ≥50 % overhead ) → Only around 40-50 % of the bandwidth is used for actual data ➢ CAN bus speeds are limited to 1-Mbit/s ➢ CAN-FD is based on the CAN 2.0 specification ➢ Physical layer not changed ➢ Support for variable bitrates (FD → Flexible Data) for the two main | GmbH DEWETRON © message segments: > Connection via USB ➢ Arbitration phase –same as standard CAN ➢ Data phase –bitrates >1-Mbit/s possible (up to ~8-Mbit/s) > Theoretically, the whole VN family with ➢ Support for larger data payloads – up to 64 bytes/message CAN-FD support should work > Multiple Adapter support > Synchronized to Analog Data with Delay lower than 50 µs > Can be used as CAN device as well 11 CAN-FD – SOFTWARE SETUP Latest Vector driver setup needs to be installed ① Enable Vector hardware in DAQ hardware setup 21 June ② When hardware is connected, it will be recognized automatically and listed in the Channel List ③ Only difference to conventional CAN setup is Baud rate high which describes ② data transmission speed of the data ① | GmbH DEWETRON © segment ⑤ ④ Load the proper dbc- or arxml-file ⑤ A channel selection dialog will open Select either all channels or only certain channels to be decoded and recorded ③ ④ 12 FLEXRAY - GENERAL Flexray support with > Vector VN 7610 > Development initiated by BMW, Daimler, Motorola and Philips in 2000 21 June > First car with Flexray was BMW X5 in 2006 > Flexray was developed to compensate CAN disadvantages, like > Higher data rates > Realtime capability | GmbH DEWETRON © > Connection via USB > Reliability > Compatible with Fibex 2.0 to 4.1.2 Standard for description file (ASAM MCD-2 > Characteristics NET) > Up to 10-Mbit/s > Decentral synchronization > Multiple Adapter support > Synchronized to Analog Data with Delay > Guaranteed latencies → deterministic lower than 50 µs > 2 channels supported 13 FLEXRAY – SOFTWARE SETUP Latest Vector driver setup needs to be installed ① Enable Vector hardware in DAQ hardware setup 21 June ③ ② When hardware is connected, it will be ② recognized automatically and listed in the Channel List ③ Click „Load Fibex“ and select the Fibex file ④ ① | GmbH DEWETRON © ④ Select the signals from the Fibex file to be created in OXYGEN OFFLINE DECODING SUPPORTED TOO Limitations: > No support of ARXML (AUTOSAR XML) description files > No support of multiplexed frames > No bus settings possible – auto detection enabled > No support of STRING channels > No support of different scaling types of one signal depending on range 14.
Details
-
File Typepdf
-
Upload Time-
-
Content LanguagesEnglish
-
Upload UserAnonymous/Not logged-in
-
File Pages14 Page
-
File Size-