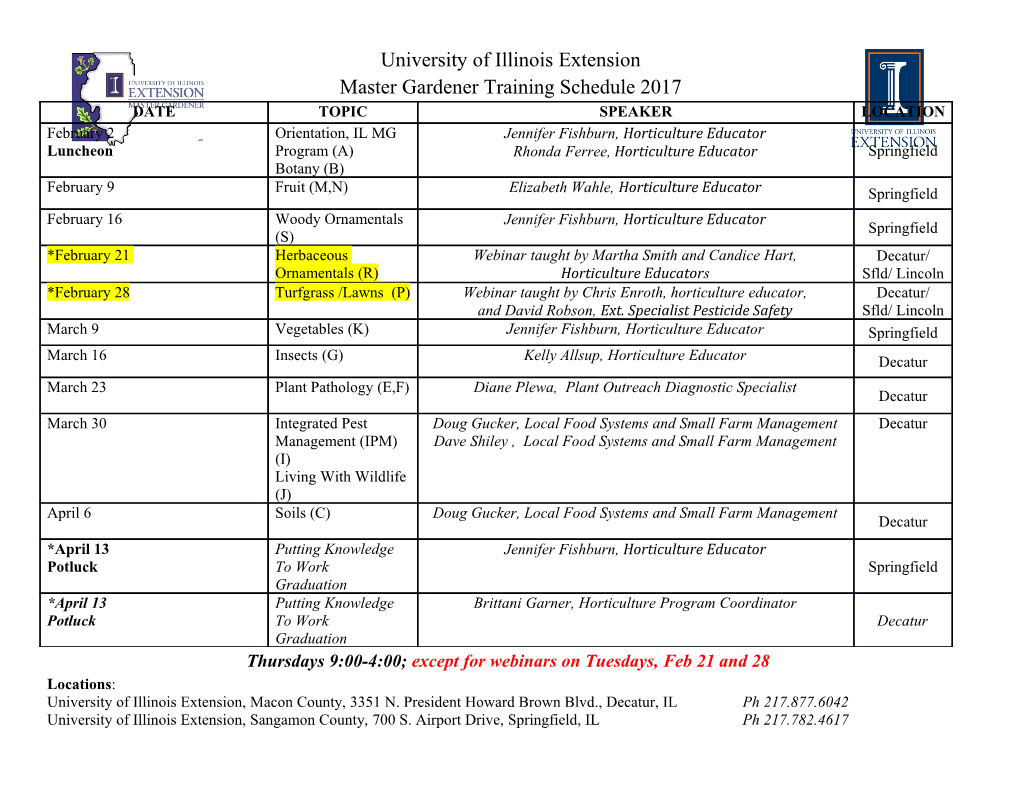
©Freund Publishing House Ltd. Science and Engineering of Composite Materials 17, 199-212 (2010) The Effects of the Butterfly Joints on Failure Loads and Fatigue Performance of Composite Structures G rkan Altan*, Muzaffer Τορφυ, Hasan Qalhoglu Faculty of Engineering, Department of Mechanical Engineering, Pamnkkale University, Kinikli 20070 Denizli, Turkey ABSTRACT The present study was designed to examine experimentally the effects of butterfly fitting clearances and different adhesives on the load carrying abilities of the composite structures joined via a butterfly-shaped joining component and the fatigue performance of the specimens joined by the best joint style obtained. Experiment specimens and butterfly- shaped locking components were cut from a composite plate by means of water jet. Fatigue experiments were conducted at the constant load ratio and at different maximum fatigue loads. To compare the fatigue performance, the fatigue experiments of the butt joints were also carried out. According to the experiment results obtained, it was determined that fatigue strengths of adhesively-bonded butterfly joints have a longer life span than those of the bonded butt joints under the same circumstances. The present study has made it possible that with the use of butterfly joining component, the earliest damage should occur on the butterfly and should have a longer service life with the repairs of the butterfly joining component. Keywords: Butterfly joint; Composite; Fatigue life; Failure load. 1. INTRODUCTION Composite materials are especially preferred in the aviation, navigation and automobile industries for their lightness. Large structures made from composite materials are generally used under static and dynamic loading conditions. Each large composite structure consists of one or more joints because of their production and design circumstances. Composite structures are usually joined via mechanical and adhesive joints. While industrial adhesive is used for the adhesive joints, such joining components as bolts and pins are preferred for mechanical joints. The main purpose here is to conduct the transfer of strength from the main structure through the combination of two or more materials. The most important problem with composite structures is the weakness in the joint areas. Load-carrying behavior of the joints and their advantages and disadvantages over each other were analyzed numerically and experimentally by many researchers and the researches are still going on. It is seen in the studies on mechanical joints that three types of damage modes are observed on the joining areas; net-tension, shear-out and bearing. The damage by net-tension and shear-out are more dangerous than the one by bearing /I, 21. Adhesive joint of the composite structures can be carried out by various designs /3-7/. Whether the ' Corresponding author. Tel: +90 258 296 31 63; Fax: +90 258 296 32 62 E-mail address: [email protected] (G rkan Altan). 199 Vol. Ð, Ëá 3, 2010 The Effects of the Butterfly Joints on Failure Loads and FatiguePerformance of Composite Structures adhesive to be used here adapts well with the composite material, the type of the joint geometry and the thickness of adhesion are factors that affect the capacity of carrying the load. Kim et al. /8/ presented a methodology for the failure prediction of the composite single lap bonded joints considering both the composite adherent and the bond line failures. In this methodology, they used an elastic-perfectly plastic model of the adhesive and a delamination failure criterion. They verified their suggested technique with numerical investigation. Alex and Wang /9/ optimized the profile of the scarf joint .between dissimilar modulus adherents with an analytical method. Chen /10/ examined the effects of hygrothermal cycling upon the performance of a bolted composite joint. He determined that the bolt torque relaxed as the number of environmental cycles increased. Avila and Bueno /I I/ carried out a performance study on a new design of single-lap bonded joint, so called wavy-lap joint for laminate composites. Τορςõ et al. /12/ investigated damage forces formed on glass-fiber laminated composite plates that were joined with a component in the shape of butterfly with experimental method. Choi and Chun /13/ investigated a failure area method to predict failure loads of mechanically-fastened composite joints under plane stress condition. Herrington and Sabbaghian /14/ investigated the effects of a number of parameters; applied stress level, orientation of the outer layer reinforcing filaments and the bolt torque level on the fatigue life on the fatigue characteristics of a bolted graphite/epoxy composite laminate. Joining of the composite structures is commonly made by the single or double lap techniques. The increase in thickness of composite structure in the single or double lap joints affects the strength of the whole joined composite structure negatively. In such joints, the increase in the value axial width of the joined composite plates leads to high stresses on the adhering surface and a decrease in the strength of the structure /15/. In the laminated plates joined in this way, the damage usually takes place on the uppermost layer. In other words, with the increase in the amount of the width, the capacity of loading decreases. In mechanical joints, however, the increase in the amount of the width leads to damage in such joining elements as bolts and pins. Therefore, butt joint is often preferred in thick composite structures. In butt joint, bonding joints are used. In such joints, scarf or stepped-overlapping joints are preferred instead of butt joints in order to avoid peeling stresses. Though joint forms change in the bonded butt joints, peeling stresses affect the lifespan of the joint negatively /16-18/. Because of these reasons, butterfly-shaped mechanical butt joints were used in this study to minimize the negative effects. Mechanical butt joints were used to lock two semi specimens through their foreheads in shape. In the composite specimens joined with a butterfly-shaped joining component, the effects of the composite material fiber orientations, the butterfly fitting clearances and different adhesives on the load-carrying capacities were analyzed experimentally, and so have the fatigue performances of the specimens joined with the best joining style obtained; then their results were presented. 2. DESIGN OF THE BUTTERFLY JOINT In this study, a new design of butterfly joint was used instead of bonded butt joints. As the thickness of the composite structure increases, the thickness of the butterfly-shaped joint component increases. This case leads to an increase in the cross section areas affecting the joint strength. Therefore, a fixed thickness was selected for this study and other variables affecting the joint strength were taken into consideration. Butterfly-shaped joining components were used to connect the composite plates from their forehead by the tight fitting method. As seen in Figure 1, specimens were cut out from the composite plate joined mechanically on forehead and then experiments were carried out. The effects of the change of the geometric parameters of butterfly-shaped joining components on the load-carrying capacities were analyzed in detail in Ref 12. In this study, the primary dimensions (b, L, t) of the specimen joined in mechanic butt joint were kept as fixed and width (w), middle width (x) and semi-length (y) of the joint lock in the shape of butterfly were changed. To see the effects of geometric parameters of the butterfly joints on the failure loads, 200 G. Altan. M. Τορςα. If. frllioglu Science and Engineering of Composite Materials t i h T Ku t \fi i, L _\ X Fig. 1: Type of butterfly joint. changes were made in the ratio of butterfly end width to specimen width (w/b), butterfly middle width to butterfly end width (w/x) and butterfly semi-length to specimen width (y/b) and a series of experiments were carried out. According to the result of these experiments, maximum joint load was determined when the butterfly semi-length is y=16 mm, the end width of butterfly joining component is w=16mm and butterfly middle width isx= 3.2 mm I\2I. The dimensions of the butterfly joining component were taken with these values in this study and experiments were carried out. If the joint between the A and B specimens shown in Figure 2 is made by the butterfly joining component only, the load applied from the A specimen is transferred to the B specimen through the edge surfaces shown by 3 via the butterfly joining component. During the transfer of the load, compression and shearing loads are formed on the edge surfaces shown by 3. If the butt joint is made both by the butterfly joining component and adhesive, the load transferred is sent to the B specimen via all the bonded edge surfaces and via the butterfly joining component. In this case, while the surfaces 1 and 2 (thick-lined areas) are exposed to the tension loads, the bonded bevel surfaces 3 (thin-lined areas) are exposed to compression and shearing loads. Â t Figure 2: Load transfer of butterfly joint. 201 Vol. 17, No. 3, 2010 The Effects of the Butterfly Joints on Failure Loads and Fatigue Performance of Composite Structures 3. PRODUCTION OF THE MATERIAL AND ITS MECHANICAL PROPERTIES The glass fiber-epoxy composite material used in this study was produced by the method of hot pressing at Izoreel Composite Isolate Materials. Glass fiber design was chosen as one-sided and two-sided. The epoxy resin used as the matrix material was formed with the mixture of CY224 epoxy of the ratio 100/80 and HY225 hardener. The mixture of epoxy resin and hardener was applied to each glass fiber layer in a mold and a 16-layer wet composite material was obtained. The wet glass fiber obtained in a mold was put under hot press in order that the epoxy composite material will be cured and reduced to minimum thickness.
Details
-
File Typepdf
-
Upload Time-
-
Content LanguagesEnglish
-
Upload UserAnonymous/Not logged-in
-
File Pages14 Page
-
File Size-