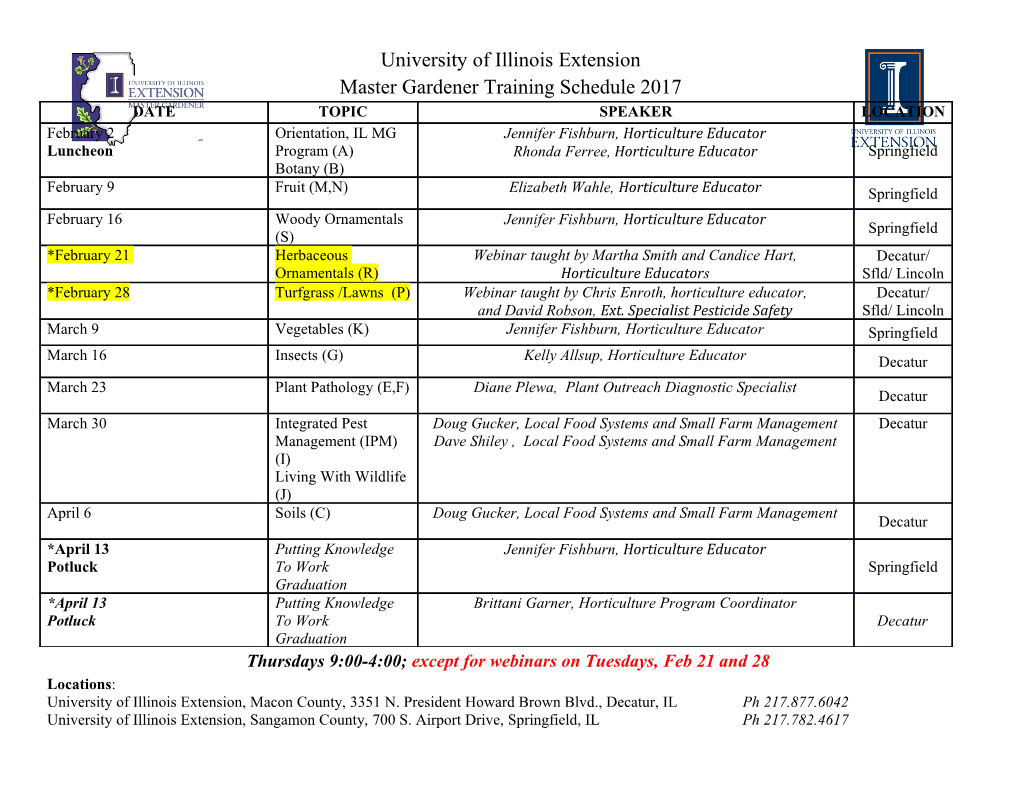
Characterization and Utilization of Cement Kiln Dusts (CKDs) as Partial Replacements of Portland Cement by Om Shervan Khanna A thesis submitted in conformity with the requirements for the degree of Doctor of Philosophy Department of Civil Engineering University of Toronto © Copyright by Om Shervan Khanna (2009) Characterization and Utilization of Cement Kiln Dusts (CKDs) as Partial Replacements of Portland Cement Doctor of Philosophy, 2009 Om Shervan Khanna Department of Civil Engineering University of Toronto Abstract The characteristics of cement kiln dusts (CKDs) and their effects as partial replacement of Portland Cement (PC) were studied in this research program. The cement industry is currently under pressure to reduce greenhouse gas (GHG) emissions and solid by- products in the form of CKDs. The use of CKDs in concrete has the potential to substantially reduce the environmental impact of their disposal and create significant cost and energy savings to the cement industry. Studies have shown that CKDs can be used as a partial substitute of PC in a range of 5 – 15%, by mass. Although the use of CKDs is promising, there is very little understanding of their effects in CKD-PC blends. Previous studies provide variable and often conflicting results. The reasons for the inconsistent results are not obvious due to a lack of material characterization data. The characteristics of a CKD must be well-defined in order to understand its potential impact in concrete. The materials used in this study were two different types of PC (normal and moderate sulfate resistant) and seven CKDs. The CKDs used in this study were selected to provide a representation of those available in North America from the three major types of cement manufacturing processes: wet, long-dry, and preheater/precalciner. The CKDs have a wide range of chemical and physical composition based on different raw material sources and technologies. Two fillers (limestone powder and quartz powder) were also used to compare their effects to that of CKDs at an equivalent replacement of PC. ii The first objective of this study was to conduct a comprehensive composition analysis of CKDs and compare their characteristics to PC. CKDs are unique materials that must be analyzed differently from PC for accurate chemical and physical analysis. The present study identifies the chemical and physical analytical methods that should be used for CKDs. The study also introduced a method to quantify the relative abundance of the different mineralogical phases within CKDs. It was found that CKDs can contain significant amounts of amorphous material (>30%) and clinker compounds (>20%) and small amounts of slag and/or flyash (<5%) and calcium langbeinite (<5%). The dissolution of ionic species and composition of the liquid phase play an important role in PC hydration. The dissolved ion contributions from CKDs were compared to PC using dilute stirred suspensions at 10 minutes and it was found that the ion contributions from CKDs are qualitatively the same as the ion contributions from PC, with the exception of chloride ions. The second objective was to utilize the material characterization analysis to determine the relationships among the composition properties of CKD-PC blends and their effects on fresh and hardened properties. The study found that CKDs from preheater/precalciner kilns have different effects on workability and heat evolution than CKDs from wet and long-dry kilns due to the presence of very reactive and high free lime contents (>20%). The blends with the two CKDs from preheater/precalciner plants had higher paste water demand, lower mortar flows, and higher heat generation during initial hydrolysis in comparison to all other CKD-PC blends and control cements. The hardened properties of CKD as a partial substitute of PC appear to be governed by the sulfate content of the CKD-PC blend (the form of the CKD sulfate is not significant). According to analysis of the ASTM expansion in limewater test results, the CKD-PC blend sulfate content should be less than ~0.40% above the optimum sulfate content of the PC. It was also found that the sulfate contribution of CKD behaves similar to gypsum. Therefore, CKD-PC blends could be optimized for sulfate content by using CKD as a partial substitute of gypsum during the grinding process to control the early hydration of C 3A. The wet and long-dry kiln CKDs contain significant amounts of calcium carbonate (>20%) which could also be used as partial replacement of limestone filler in PC. iii Acknowledgments I wish to express my sincere gratitude to Professor Doug Hooton, my supervisor, for his excellent guidance and invaluable advice during this investigation. Thanks are also due to Professor Hooton for the facilities extended to me at University of Toronto. This project was initiated by the Products and Quality Department of Lafarge North America Centre for Technical Services in Montreal under the guidance of Mr. Bruce Blair, Dr. Anik Delagrave, and Ms. Claude Lauzon. Acknowledgement is made of their generous assistance and valuable cooperation throughout the research program. I wish to extend my deepest thanks and appreciation to Dr. Laurent Barcelo of Lafarge North America for his helpful suggestions and interest in this investigation. Dr. Barcelo also reviewed this manuscript during the preparation of the dissertation. Thanks are also extended to these Lafarge personnel who shared their technical knowledge and expertise via personal meetings and/or email exchanges: Dr. Jean Philippe Perez, Dr. Ellis Gartner, and Mr. Paul Lehoux. Thanks are due to Lafarge laboratory technicians Rino Lisella and Patricia Martin who shared their expertise and helped in preparing many of the specimens. Thanks also to the many other laboratory researchers and staff of Lafarge for providing assistance: Mr. Denis Belanger, Mr. Denis Leblanc, Ms. Sona Babikan, Mr. Claude Verville, Ms. Julie Morissette, Ms. Lorraine Phang, and Mr. Bernard Brochard. Thanks are also due to my colleagues at the University of Toronto. I wish to extend my gratitude to Dr. Terry Ramlochan for providing technical advice periodically throughout the course of this project, particularly with the CKD phase quantification. I would also like to acknowledge the help provided by other members of the Concrete Materials Group: Dr. Gustavo Julio-Betancourt for his helpful discussions, and Ms. Ursula Nytko and Ms. Olga Perebatova for providing guidance and help with the materials and equipment. Thanks are also due to Dr. S. Petrov from the Department of Chemistry for assisting with the CKD phase quantification and Mr. Dan Mathers from the Department of Chemistry for his help in analyzing some of the solution samples. iv Sincere thanks to my supervising committee members Dr. Brenda McCabe and Dr. Murray Grabinsky for their insightful questions and comments while the thesis was in progress. I would also like to thank Dr. Daman Panesar for very supportive discussions during my Ph.D and reviewing this dissertation. Further, the author is indebted to Lafarge North America, the Natural Sciences and Engineering Research Council (NSERC), and the Ontario Graduate Scholarship (OGS) Program for providing financial support throughout the project. My thanks are also due to my wife, children, and family members for their support and understanding throughout the course of this project. v Table of Contents 1.0 INTRODUCTION .................................................................................................. 1 1.1 Background......................................................................................................... 1 1.2 Problem Statement.............................................................................................. 2 1.3 Incentives and Objectives of This Study ............................................................ 4 1.4 Summary of Chapters ......................................................................................... 6 2.0 LITERATURE REVIEW ....................................................................................... 8 2.1 CKD Manufacture and Management.................................................................. 8 2.1.1 Portland Cement Manufacture Overview ................................................... 8 2.1.2 CKD Generation ....................................................................................... 17 2.1.3 Fresh and Landfill CKD............................................................................ 20 2.1.4 CKD Applications: Cement Industry Perspective .................................... 21 2.1.5 Costs Associated with CKD Disposal....................................................... 22 2.1.6 CKD Environmental Considerations ........................................................ 23 2.2 CKD and Portland Cement ............................................................................... 24 2.2.1 Chemical Properties.................................................................................. 24 2.2.2 Mineralogical Properties........................................................................... 26 2.2.3 Physical Properties.................................................................................... 29 2.2.4 CKD Types ............................................................................................... 32 2.2.5 Variability of CKD from a Single Plant ................................................... 34 2.3 Portland Cement Hydration .............................................................................
Details
-
File Typepdf
-
Upload Time-
-
Content LanguagesEnglish
-
Upload UserAnonymous/Not logged-in
-
File Pages344 Page
-
File Size-