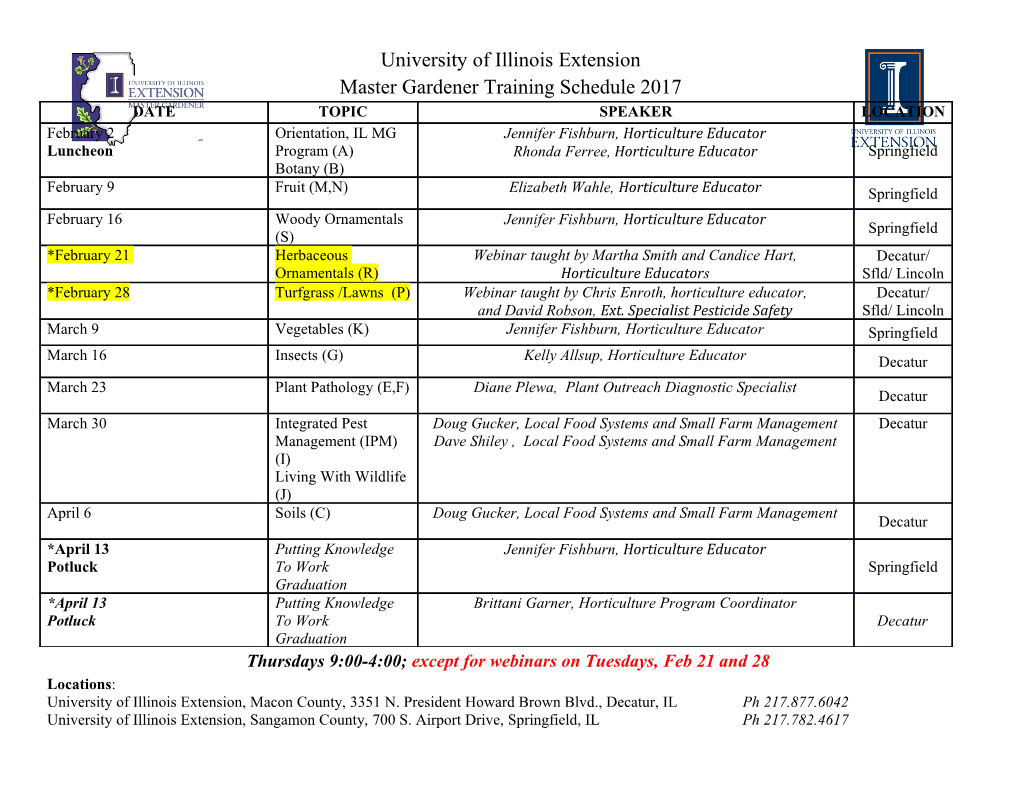
3D Printing as an Alternative Manufacturing Method for the Micro­gas Turbine Heat Exchanger Wolfgang Seiya and Sherry Zhang July 2015 Department of Energy Technology Royal Institute of Technology Stockholm, Sweden Pratt School of Engineering, Smarthome Program Duke University Durham, North Carolina, USA 1 Acknowledgements We would like to thank InnoEnergy, Compower, and the ‘‘STandUP for Energy’’ project for providing resourceful background information for this study. We owe our deepest gratitude to our advisor, Anders Malmquist for his continuous support for this study throughout the summer. His guidance, motivation, and expertise were invaluable assets in all areas of the study. Our sincere thanks goes to Joachim Claesson at KTH for his time and knowledge on the subject of heat exchangers. We take this opportunity to thank all the company correspondents that took their time and interest to help us with the vast information needed for this study. Lastly, we are immensely grateful to Duke Smart Home Program and its director Jim Gaston for providing us with the opportunity and necessary funds to live in Sweden while conducting this study. 2 I. Table of Contents List of Figures …………………………………………………………………………….… 6 List of Tables ……………………………………………………………………………….. 7 Abbreviations and Equation Nomenclature ………………………………………………… 8 Abstract …………………………………………………………………………………...… 9 Introduction …………………………………………………………………………………. 9 Methodology ……………………………………………………………………………….. 10 Materials ……………………………………………………………………………….. 10 Manufacturing ………………………………………………………………………….. 13 Materials ………………………………………………………………………………….... 14 Material Overview ……………………………………………………………………... 15 Silicon Carbide ……………………………………………………………………….... 18 i. Creep and Oxidation ……………………………………………………………... 18 ii. Fatigue Toughness ………………………………………………………………. 18 iii. Crack Healing …………………………………………………………………... 18 iv. Compatibility with 3D Printing ………………………………………………… 19 v. Sustainability ……………………………………………………………………. 19 Inconel alloys ………………………………………………………………………….. 19 i. Impact Strength ………………………………………………………………….. 19 ii. Fatigue Strength ………………………………………………………………… 20 iii. Creep and Rupture Properties ………………………………………………….. 20 iv. Corrosion resistance ……………………………………………………………. 20 v. Compatibility with 3D printing …………………………………………………. 21 vi. Sustainability …………………………………………………………………… 21 Haynes 214 Alloy ……………………………………………………………………… 21 i. Oxidation and Creep ……………………………………………………….…….. 21 ii. Cracking ………………………………………………………………….……… 21 iii. Compatibility with 3D Printing ……………………………………………....… 22 iv. Sustainability ………………………………………………………………….... 22 Stainless Steel 304 ……………………………………………………………………... 22 i. Creep and Creep­Fatigue ………………………………………………………… 22 ii. Oxidation ………………………………………………………………………... 23 iii. Compatibility with 3D Printing ………………………………………………… 23 iv. Sustainability …………………………………………………………………… 23 Evaluating high­temperature thermal and tensile properties …………………………... 24 Ranking results ……………………………………………………………………….... 27 3D Printing / Additive Manufacturing …………………………………………………….. 28 Manufacturing Techniques Overview ……………………………………………….… 29 3 Powder­Based Fusion Processes (PBF) ……………………………………………….. 30 i. Solid­State Sintering …………………………………………………….………. 31 ii. Chemically­Induced Sintering ………………………………………………….. 32 iii. Liquid­Phase Sintering (LPS) ………………………………………………….. 32 iv. Full Melting …………………………………………………………………….. 32 v. Electron Beam / Electron Beam Melting (EB / EBM) ………………………….. 32 vi. Sustainability …………………………………………………………………… 33 Binder Jetting Additive Manufacturing (BJAM) …………………………………….... 33 Laminated Object Manufacturing (LOM) ……………………………………………... 33 Electron Beam Additive Manufacturing (EBAM) …………………………………..… 34 Ultrasonic Consolidation (UC) ……………………………………………………….... 35 Ranking Techniques …………………………………………………………………… 36 Companies / Researchers ………………………………………………………………. 37 Arcam AB …………………………………………………………………………. 38 Aurora Labs 3D ……………………………………………………………………. 38 Ceralink ……………………………………………………………………………. 39 EOS ….…………………………………………………………………………….. 39 ExOne ……………………………………………………………………....……… 39 Fabrisonic ………………………………………………………………………….. 40 Renishaw ……………………………………………………………………...…… 40 Sciaky …………………………………………………………………………….... 40 Other Companies ………………………………………………………………..…. 40 Growth ……………………………………………………………………………….… 42 Heat Exchanger Design ………………………………………………………………….… 43 Classification of Heat Exchangers …………………………………………………….. 43 i. From Construction ………………………………………………………………. 43 ii. Based on the Heat Transfer Process ……………………………………………. 45 iii. Based on Surface Compactness ……………………………………………...… 45 iv. Based on Flow Arrangements …………………………………………….….… 45 Thermal Hydraulic Performance of Heat Exchangers ………………………………… 46 i. Heat Transfer Mechanisms in Heat Exchangers ………………………………… 46 ii. Conduction …………………………………………………………………….... 46 iii. Convection …………………………………………………………………...… 46 iv. Heat Transfer and Temperature Difference ………………………………….… 47 Pressure Drops ………………………………………………………………………… 49 Effectiveness and Rating …………………………………………………………….... 50 Design Recommendations …………………………………………………………….. 52 Economics ……………………………………………………………………………….... 54 Barriers ……………………………………………………………………………………. 57 4 Recycling ………………………………….…………………………………………….… 57 Discussion and Recommendations …………………………………………………...…… 58 Sensitivity Analysis ……………………………………………………………………….. 59 Conclusion ………………………………………………………………………………… 61 References ………………………………………………………………………………… 62 Appendix ………………………………………………………………………………..… 69 5 II. List of Figures Figure 1 ­ AspenPlus model of Compower’s ET10 …………………………………...….. pg. 10 Figure 2 ­ Ashby’s Material and Selection Chart ……………………………………….... pg. 15 Figure 3 ­ Internal oxidation attack in Inconel 601 ………………………………………. pg. 21 Figure 4 ­ Thermal conductivities of the top five materials with temperature ……….…... pg. 24 Figure 5 ­ Specific heat capacities measured from a reference of 20°C ………………….. pg. 24 Figure 6 ­ Coefficient of linear expansion of the top five materials with temperature ….... pg. 25 Figure 7 ­ Yield strengths of top 5 materials with temperature …………………………... pg. 26 Figure 8 ­ Elastic modulus of top five materials with temperature ………………………. pg. 26 Figure 9 ­ Schematic of selective­laser sintering …………………………………………. pg. 31 Figure 10 ­ Schematic of solid­state sintering ……………………………………………. pg. 32 Figure 11 ­ The laminated object manufacturing process ………………………………... pg. 34 Figure 12 ­ Schematic of the ultrasonic consolidation process …………………………... pg. 35 Figure 13 ­ Different types of tubular heat exchangers …………………………………... pg. 44 Figure 14a ­ Different types of plate heat exchangers ……………………………………. pg. 44 Figure 14b ­ Different types of plate heat exchangers ……………………………………. pg. 45 Figure 15 ­ Parallel, counter and cross flow configurations …………………………….... pg. 45 Figure 16 ­ LMTD Method for parallel and counterflow heat exchangers ………………. pg. 48 Figure 17 ­ Temperature profile along a cross­flow heat exchanger …………………….. pg. 48 Figure 18 ­ Brayton cycle ………………………………………………………………... pg. 49 Figure 19 ­ Plot of overall performance coefficient P vs. relevance factor α …………….. pg. 52 Figure 20 ­ Cost in US dollars of commercial computers from 1950 to 1985 ……………. pg. 54 Figure 21 ­ Price index of personal computer and peripheral equipment ……………….... pg. 55 6 III. List of Tables Table 1 ­ Weights for each criteria used to rank the materials …………………………... pg. 11 Table 2 ­ Ranking criteria for top five materials and their respective weights ………….. pg. 12 Table 3 ­ Weights for each criteria used to rank manufacturing techniques …………….. pg. 14 Table 4 ­ All the materials initially considered for the heat exchanger design ………….. pg. 15 Table 5 ­ The top 22 materials and their material properties ……………………………. pg. 16­17 Table 6 ­ Ranking results for the top five materials …………………………………….. pg. 28 Table 7 ­ Overview of additive manufacturing techniques compatible with plastics, metals, and ceramics …………………………………………………………………….. pg. 30 Table 8 ­ Ranking and totals for each manufacturing technique ………………………... pg. 37 Table 9 ­ Machine data from various companies ……………………………………….. pg. 41 7 IV. Abbreviations and Equation Nomenclature Abbreviations Equation Nomenclature 2 ABC­SiC = Aluminum­Boron­Carbon­Silicon Carbide A = Area (m ) AM = Additive Manufacturing C = Heat capacity (J/kg.K) BJAM = Binder Jetting Additive Manufacturing dT/dx = thermal gradient (K/m) BJT = Binder Jetting Technology D = Hydraulic diameter (m) CAD = Computer­Aided Design f = Friction factor CAGR = Compound Annual Growth Rate h = Specific enthalpy (J/kg) 2 CNC = Computer Numerical Control hc = Convective heat transfer coefficient (W/m K ) DMLM = Direct Metal Laser Melting k = Material’s thermal conductivity constant (W/mK) DMLS = Direct Metal Laser Sintering L = Length (m) EBAM = Electron Beam Additive Manufacturing m = Mass (kg) EB / EBM = Electron Beam / Electron Beam Melting m’ = Mass flow (kg/s) HX= Heat Exchanger Ns = Number of entropy production units LMTD = Log Mean Temperature Difference Nu = Nusselt number LOM = Laminated Object Manufacturing Q’ = Rate of heat transfer (J/s) LPS = Liquid­Phase Sintering ΔP = Pressure drop (%) PBF = Powder Based Fusion Processes Pr = Prandtl number R&D = research and development Re = Reynold’s number SiC = Silicon Carbide St = Stanton number SLA = Stereolithography T = Temperature (K) SLM = Selective Laser Melting V
Details
-
File Typepdf
-
Upload Time-
-
Content LanguagesEnglish
-
Upload UserAnonymous/Not logged-in
-
File Pages71 Page
-
File Size-