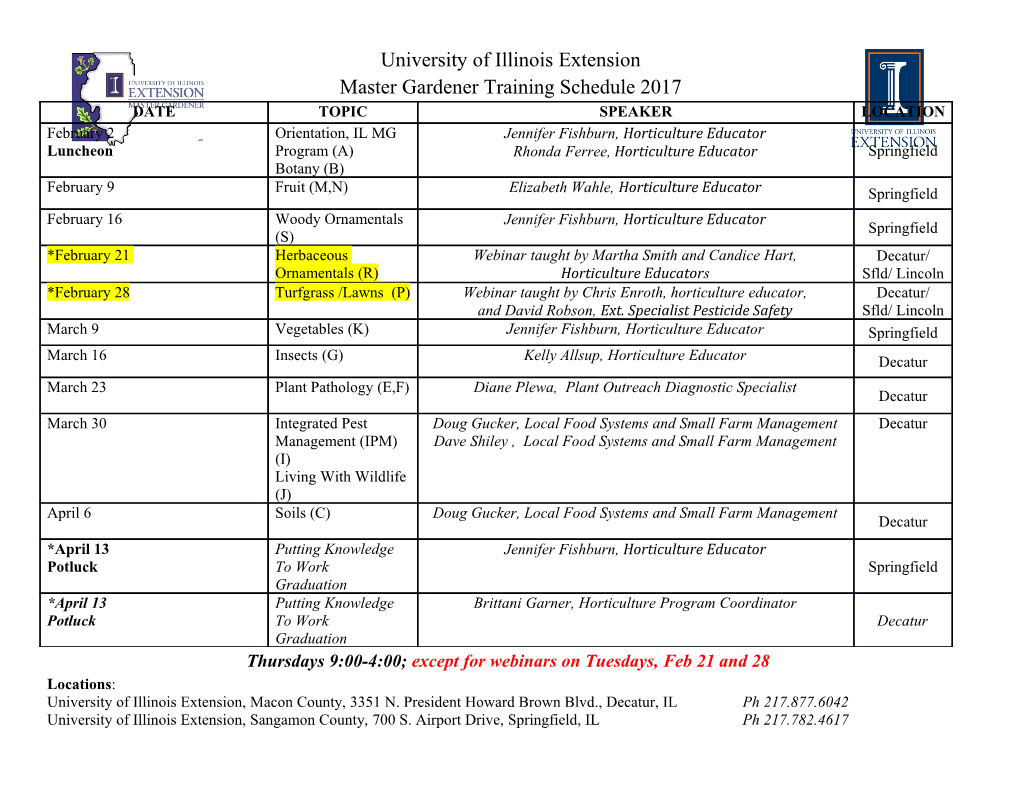
-HOW KNOW CUSTOMER MAGAZINE DECEMBER 2019 TOOLMAKING THE SUPREME DISCIPLINE FLUSHING SYSTEMS MORE CHOICE MORE VALUE document7233463554329238930.indd 1 08.11.2019 14:54:01 ON THE COVER The moulds from the toolmaking depart- ment are used at the production facil- ities in Rapperswil-Jona (CH) and Pfullen- dorf (DE). Pictured here is a high-gloss polished mould used for manufacturing the Sigma01 actuator plate. CONCEPT/DESIGN/REALISATION Linkgroup AG, Zurich www.linkgroup.ch PHOTOS Ben Huggler (cover, page 14) Iris Cook (pages 6–9) Shutterstock (page 13) SARC Architects/Tuomas Uusheimo (pages 17–18) Issued quarterly. The reproduction of individual articles, in part or in full, is subject to approval from the editorial staff. document4160704994437024187.indd 2 08.11.2019 14:53:58 CONTENTS EDITORIAL 6 BEHIND THE SCENES MOULDS WITH MILLI- METRE PRECISION FROM THE TOOLMAK- ING DEPARTMENT Mark Schurr Managing Director 14 COMPETENCES DEAR CUSTOMERS, CALCULATING WATCHMAKING IS A CRAFT THAT SANITARY NOISES IS KNOWN FOR ITS PRECISION. 16 TIPS & TRICKS Similar levels of precision can be found in the in-house toolmaking department at Geberit. With outstanding DESCALING GEBERIT technical skills and a keen eye, toolmakers create moulds AQUACLEAN for injection moulding and blow moulding machines. Accuracy is just as important in the Geberit workshops – and at every work step to boot, starting from the design 5 News data all the way through to honing and then assembling 10 Customer event in Cape Town the individual components to form the finished tool. 13 Geberit Flushing Systems Toolmaking is thus one of the most important success 18 Reference object in Helsinki factors at Geberit. It is not only where all the know-how from product development comes together, but also a source of expertise in production itself as a developer and manufacturer of new moulds. The flawless moulds ensure the undisputed product quality that Geberit is known for. This issue not only contains more information on the in-house toolmaking department, but also other exciting stories about Geberit and the product range. I wish you an entertaining and informative read. 3 document4160704994437024187.indd 3 08.11.2019 14:53:59 document2874352365261011448.indd 4 08.11.2019 14:54:01 NEWS OKTOBERFEST@GEBERIT Fast becoming one of the most antici- pated events of the year. Geberit South- ern Africa held its second annual Okto- berfest. Industry partners were invited for an evening of festivities. The evening was aimed at showing appreciation for relationships and efforts that have as- sisted the Geberit team in South africa grow. The evening was filled with laughs and plentiful conversation. There was also a selection of craft beers as well as German-style cuisine. We look forward to seeing our partners again next year. SHOWROOM UPGRADES The showrooms at the Geberit offices in Cape Town and Johannesburg will RETIREMENT VALERIE NOBEL be undergoing upgrades. These upgrades The team at Geberit Southern Africa are necessary in order to showcase the would like to bid a fond farewell to Valerie new additions to our ranges. These addi- Nobel who will be retiring at the end tions include the new Geberit myDay of the year. Valerie has been a part of the series, as well as upgrades to the Geberit Geberit team in Cape Town since its Smyle range. If you would like to visit inception 20 years ago. Over the years, one of the Geberit showrooms, please Valerie has become a key member of feel free to contact the office located the logistics team and become an inspir- nearest to you. Our team members would ation to the rest of the team in South be happy to assist you with a walk- Africa for her hard work and dedication. through and answer any technical ques- Valerie will officially become the first tions you may have. member of the team of Geberit Southern Africa to retire. The team at Geberit Southern Africa would like to wish Valerie all the best on her well-deserved break and thank her for her many years of service. 5 document2874352365261011448.indd 5 08.11.2019 14:54:02 TOOLMAKING AT GEBERIT THE SUPREME DISCIPLINE document2074879280042026603.indd 6 08.11.2019 14:54:10 BEHIND THE SCENES ← A look inside the assembly area, where the tools are given their finishing touches. In order for Geberit to produce first-class plastic components and products, the corresponding injection moulds and blow moulds have to be of the very highest quality and precision. This is the job of the in-house toolmaking department. The machines in the production halls in Rapperswil- TOOLMAKING = MOULD BUILDING Jona (CH) are running at full steam. Tens of thousands of plastic parts are injection-moulded here every day. Pipe fittings, actuator plates and concealed cisterns – The story is the same at the plant in Pfullendorf (DE). all of these products are made in injection moulding and Without highly automated production facilities with blow moulding machines. The moulds found in these injection moulding and blow moulding machines, machines are produced by the toolmaking department these volumes would not be possible – and certainly (also known as mould building). In the injection mould- not in the precision and surface quality that Geberit ing process, liquid plastic is injected into a mould at strives for. What not many people know is that behind a pressure of up to 2,000 bar, where it then hardens be- this outstanding quality are toolmakers that work at fore the finished component can be taken out of the the very highest level. mould. Due to the high quality standards and the heavy loads they are subjected to, the moulds have to meet HIGHLY CONCENTRATED AND WITH particularly strict requirements. For example, the PINPOINT ACCURACY machining and heat treatment of the wear-resistant The in-house toolmaking departments in Jona and special-grade steel mean that the tool is relatively Pfullendorf specialise in the production of moulds robust. Perfect assembly of the individual components that are required in the injection moulding and blow and a final inspection of the functions ensure that the moulding processes. At the two sites, a total of some liquid plastic then flows into the prefabricated mould as 70 toolmakers, draughtsmen and other specialists go required and that there are no unexpected quality about their tasks in workshops equipped with state- defects on the final product. of-the-art machines. It is immediately clear that qual- ity and precision are of huge importance here. → 7 document2074879280042026603.indd 7 08.11.2019 14:54:17 BEHIND THE SCENES A member of staff painstakingly inspects a compo- “Constructing an injection nent that has been milled from a block of steel by a moulding tool is like computer-controlled machine before they can then combine this with the remaining components to make in Formula 1 – one mistake a complete mould. It’s clear to see that working by and we won’t reach the hand is still in demand here despite the high levels of chequered flag.” automation. “A toolmaker works at a level of precision down to mere one thousandth of a millimetre. Such Michael Zinser accuracy can only be achieved by well-trained staff,” Head of Toolmaking Geberit explains Michael Zinser, Head of Toolmaking. Even the smallest deviation can mean that a mould is rendered useless. Days of work would then have gone to waste in such cases, not to mention the associated financial as the design has to meet the requirements of the in- losses. As Michael Zinser explains: “A finished tool can jection moulding or blow moulding machines exactly. cost several hundred thousand francs.” Special attention is already paid here to the separ- ation of the two halves of the mould. Ventilation and FROM THE BLUEPRINT TO THE FINAL MOULD temperature control of the mould are also already The toolmaking department springs into action when taken into account during this early phase. moulds are worn out or damaged, or when Geberit launches a new product. In the event of new products, Based on the design data, the machine programmers the production of a new mould starts when the prod- then write a CAM program for manufacturing the indi- uct data is passed on by the development depart- vidual components. This program contains all relevant ment. Using this already very precise data – consisting data from the design phase that the CNC machine of 2-D drawings and 3-D data – the draughtsman needs, meaning it can then manufacture the cor- builds the virtual mould on the computer using CAD responding component step by step – ideally in a software. This results in a detailed tool design. Even completely automatic process. Here, the steel plates at this early stage, there is only a low fault tolerance from which the moulds are made are clamped in the machine and then processed using a range of meth- ods, including milling, eroding, turning and grinding. Milling and erosion are used particularly often, with “Our moulds are the former ensuring rotation-symmetric preparation highly complex, precise of easily accessible geometries and the latter used for sharp edges and openings. The components also un- one-off items.” dergo different heat treatment processes. Michael Zinser Head of Toolmaking Geberit Once the individual components have been prefabri- cated, they are then finished, measured, examined and then assembled into a complete mould. “The as- sembly process is a particularly delicate job that re- quires a lot of experience and a steady hand,” explains Michael Zinser. “In order for the mould to remain in use for a long time, all the components must be perfectly coordinated with one another.” FAST REACTION TIMES The toolmaking department not only produces new moulds – they are also responsible for the maint- enance and repair of existing ones.
Details
-
File Typepdf
-
Upload Time-
-
Content LanguagesEnglish
-
Upload UserAnonymous/Not logged-in
-
File Pages20 Page
-
File Size-