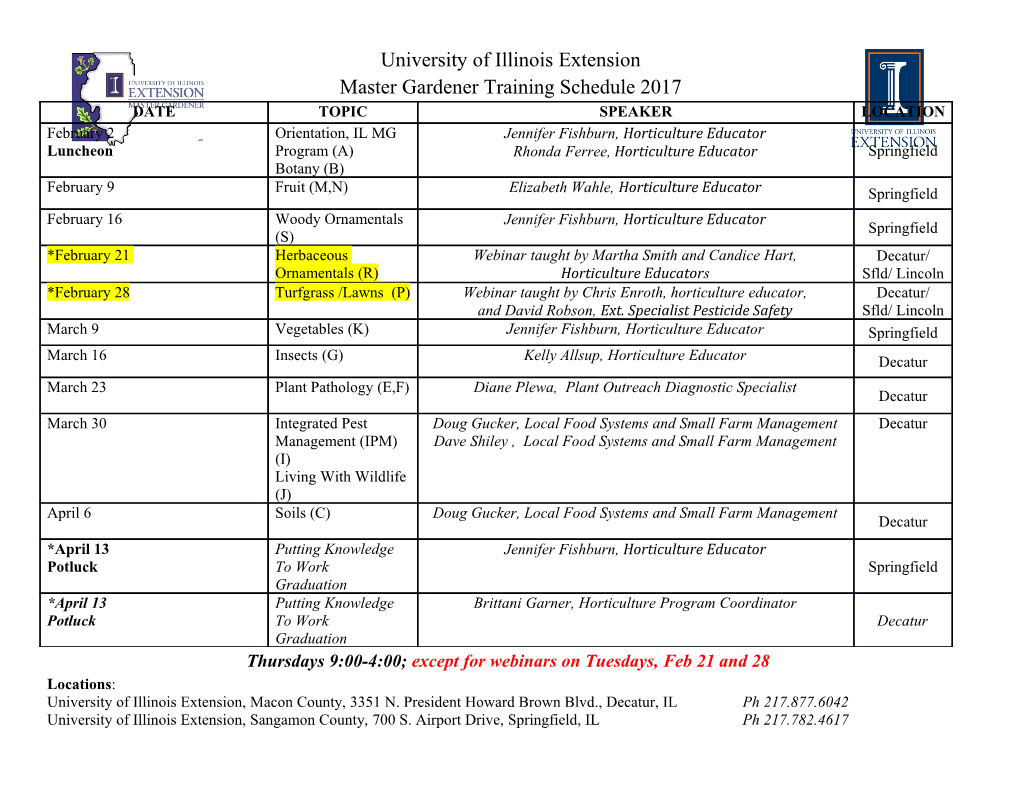
Iowa State University Capstones, Theses and Retrospective Theses and Dissertations Dissertations 1950 Electrolytic concentration of caustic soda Carl Rene Vander Linden Iowa State College Follow this and additional works at: https://lib.dr.iastate.edu/rtd Part of the Chemical Engineering Commons Recommended Citation Vander Linden, Carl Rene, "Electrolytic concentration of caustic soda " (1950). Retrospective Theses and Dissertations. 14031. https://lib.dr.iastate.edu/rtd/14031 This Dissertation is brought to you for free and open access by the Iowa State University Capstones, Theses and Dissertations at Iowa State University Digital Repository. It has been accepted for inclusion in Retrospective Theses and Dissertations by an authorized administrator of Iowa State University Digital Repository. For more information, please contact [email protected]. INFORMATION TO USERS This manuscript has been reproduced from the microfilm master. UMI films the text directly from the original or copy submitted. Thus, some thesis and dissertation copies are in typewriter face, while others may be from any type of computer printer. The quality of this reproduction is dependent upon the quality of the copy submitted. Broken or indistinct print, colored or poor quality illustrations and photographs, print bleedthrough, substandard margins, and improper alignment can adversely affect reproduction. In the unlikely event that the author did not send UMI a complete manuscript and there are missing pages, these will be noted. Also, if unauthorized copyright material had to be removed, a note will indicate the deletion. Oversize materials (e.g., maps, drawings, charts) are reproduced by sectioning the original, beginning at the upper left-hand comer and continuing from left to right in equal sections with small overiaps. ProQuest Information and Learning 300 North Zeeb Road. Ann Arbor, Ml 48106-1346 USA 800-521-0600 NOTE TO USERS This reproduction is thie best copy available. UMI' ULSOTROLYTIO aO?rOHilTPJi.?lO!^ 0? OAUSTIO 30 ISA ^7 Oaxl Hezie Vander Linden A Dissertation Submitted to the Graduate Faculty in Partial Fulfillment of the Requirements for the Degree of DOCTOR OF PKILOSOPKY Major Subject: Chemical Engineering A-onroved: Signature was redacted for privacy. tn Ondrg"e of Major .Worl Signature was redacted for privacy. Head of Major De ment Signature was redacted for privacy. Dean of Grradua.te College Iowa State College 1950 UMI Number: DP13525 UMI UMI Microform DP13525 Copyright 2005 by ProQuest Information and Learning Company. All rights reserved. This microform edition is protected against unauthorized copying under Title 17, United States Code. ProQuest Information and Learning Company 300 North Zeeb Road P.O. Box 1346 Ann Arbor, Ml 48106-1346 ii TABLS OF COHTBIITS Page I. I15TRODUOTIOIJ 1 II. RmSW OF THE LITEHATURS 4 A. The Allcali Chlorine Industry . i , . 4 B. The Hydrogen Industry 14 C. The Oxygen Industry 13 III. SXPalRIISUTAL 26 A. Preliminary Batch Concentration Tests . 27 1. Platinum electrode esperiment ... 37 2. Beaker cell experiments 28 3. Circular Cell Concentration Experiments . 30 1. Apparatus . 31 2. Experimental tests 33 3. Discussion of the results .... 36 C. Preliminary Studies on the Chlorine . 38 "Syolution Point 1. Experiments with caustic-salt ... 39 solutions 2. Experiments with pure salt solutions 40 D. Preliminary Conductivity Tests .... 43 1. Apparatus and procedure 42 2. Discussion of the results .... 44 E. Batch Concentration Experiments with a . 48 Parallel Electrode Monel Cell '1. Apparatus 48 2. Experimental results 53 iii ?, Continuous Concentration "Sxperiments witli 55 the Parallel "Slectrode Monei Cell 1, Apparatus 55 2. Concentration tests 58 3, Conductivity tests 67 4. Conclusions 69 G. Further Studies on Variables Affecting . 70 the Chlorine Evolution Point 1. Apparatus and procedure 70 2. Discussion of the results .... 72 H. Conductivity Tests 78 1. Apparatus 79 2. alffect of electrode spacing on the . 83 cell voltage 3. Comparison of monel metal and nickel 91 electrodes 4, Use of stainless steel electrodes . 93 5, Variation of conductivity with . 95 solution concentration I. Electrode Life Tests 99 1, Apparatus and Tjrocedure 99 2. Hesults and conclusions 100 J. Pilot Plant Studies 101 1. Apparatus 101 2. Continuous concentration tests . 107 3. Conductivity test 112 4. Moisture and caustic loss tests . 112 IV, ECOSfOJfIC inTALUATIOU OF TEE PROCESS.... 117 iv A. Pro"oosed Design of a Oonsnexcial Size . 117 Cell 1. Apparatus . 117 2. Cost estimate for the comnercial cell 122- B. Preconstruction Cost Estimate . 122 1. Flowsheet 124 2. Plant investment costs 125 3. Production cost estimate .... 131 7. C-EIJSRAL DISCUSSION 140 YI. COTJGLUSIONS 144 YII. SUISJARY 146 VIII. LITERATUHi: CITED 147 IX. ACICro-^LEDGEMEIT 149 X. APPEUDxX 150 1 I. INTRO i]iaCTION The caustic soda industry is recognized as an essential element of our modern culture. At present about two-thirds of the caustic soda manufactured in this country is produced "by the electrolytic process. Although this process was introduced about fifty years ago, no major changes in the basic process hams-been accepted by the industry. Admittedly, there have been changes in equipment, such as in cell and evattorator design, and a purification process has been added bf some plants; but the basic process still remains unchanged. Although a small amount of the caustic soda produced in the United States is made by the electrolytic process utilizing mercury cathode cells, the major portion of electrolytic caustic is manufactured by the process using diaphragm cells. It is this latter process with irshich this research project is concerned. In the process utilizing diaphragm cells a saturated brine is made up and purified so as to remove any calcium, magnesium, and iron present. Usually this is carried out by a. lime-soda treatment. This treated brine is then fed to the electrolytic cells and is subjected to electrolysis. In this operation three products are formed; chlorine, hydrogen, and the cell effluent containing both salt and caustic soda in solution. The actual concentration of the 2 effluent depends ttpon tlie tirpe of cell used and the operat­ ing conditions; "but tiie usual concentration varies from 100 to 135 grams of sodiiim hydroxide per liter and 170 to 130 grams of sodium chloride per liter. This solution zaust be concentrated in order to recover the salt and to produce a caustic of marketable concentration- Modern practice in­ volves the use of multiple effect evaporators to concentrate the cell effluent to a 50 percent caustic. To prevent con­ tamination of the caustic mth iron, modern evaporators have bodies constructed of nicfeel-clad steel and heater tubes of nic^jel. Forced circulation is normally used to obtain higher evaporator capacity. Since salt is less soluble in concen­ trated caustic solutions, the salt precipitates during the evaporation. This is removed in special settling chambers. The 50 percent caustic solution is cooled and filtered, leaving a product containing about 1 percent salt. The major portion of the caustic produced today is shipped as a 50 percent solution, Sojjse industries demand a caustic free frojs salt and sodiiam chlorate; and, as a result, a nusiber of processes have been developed by which this purification step can be accomplished. If a more concentrated product is desired, the 50 percent solution is evapora.ted to 65 to 'J'S percent in a single effect evaporator. This is then pumped to cast iron caustic pots and heated by direct fire to produce anhydrous caustic. 3 It is tlie purpose of this research project to develop a neiT metliod of concentrating tlie effluent from the chlorine- caustic cell. In the proposed process the water of the solution is removed by electrolyzing it rather than removing it "by the conventional evaporation method. The development of a process which novCLd replace the evaporation step isroiild he of particular importance for three reasons: (i) the evaporators are very expensive pieces of equipment, (2) they require a large amount of maintenance, and (3) their oper­ ation is costly. Although it is obvious that the electrical energy, used in the new process -srould be more costly than the steam used in the evaporation, the proposed process furnishes two additional sala.ble products; namely, hydrogen and oxygen. The sale of these by-products coiild conceivably more than make TO the difference between the cost of the steam and the cost of the power, and thus provide, a means of increasing the profit derived from the production of caustic. 4 II. HSVI2iT OF THE LITE5UTURS A. The Alkali Chlorine Industry- Man has long needed a source of alkali; but it has only "been with the growth of the chemical industry that large quantities have "been available. The principal sources, prior to Le Blanc's discovery, were natural deposits and that ex­ tracted from ashes of seaweed and wood (14). In 1775 the French Acadeiay of Science offered a prize for the invention of a practical process for the manufacture of soda. With this as an incentive, Le Blanc developed his no-sr famous process and was granted a patent in 1791, Basically, the process consists of reducing salt cake -srith carbon to form sodium sulfide, leaching out the soliible sodium sulfide, and the subsequent treatment of the sulfide -with hydrated lime to form caustic soda and relatively insoluble calcium sulfide. To produce salt cake, salt T?as reacted with sulf\iric acid, thus producing hydrogen chloride as a by-product. This by-product hydrogen chloride was a nuisance at first, but later it was utilized as the raw material for the production of chlorine by the l^ldon and the Deacon processes. This interest in chlorine was brought about by the development of bleaching powder and its use in the 5 textile industry. Heitlier of these processes iias any appreci­ able application at the present time. In I80I "Smest SolYay rediscovered and perfected an old process known as the aEanonia-soda process.
Details
-
File Typepdf
-
Upload Time-
-
Content LanguagesEnglish
-
Upload UserAnonymous/Not logged-in
-
File Pages178 Page
-
File Size-