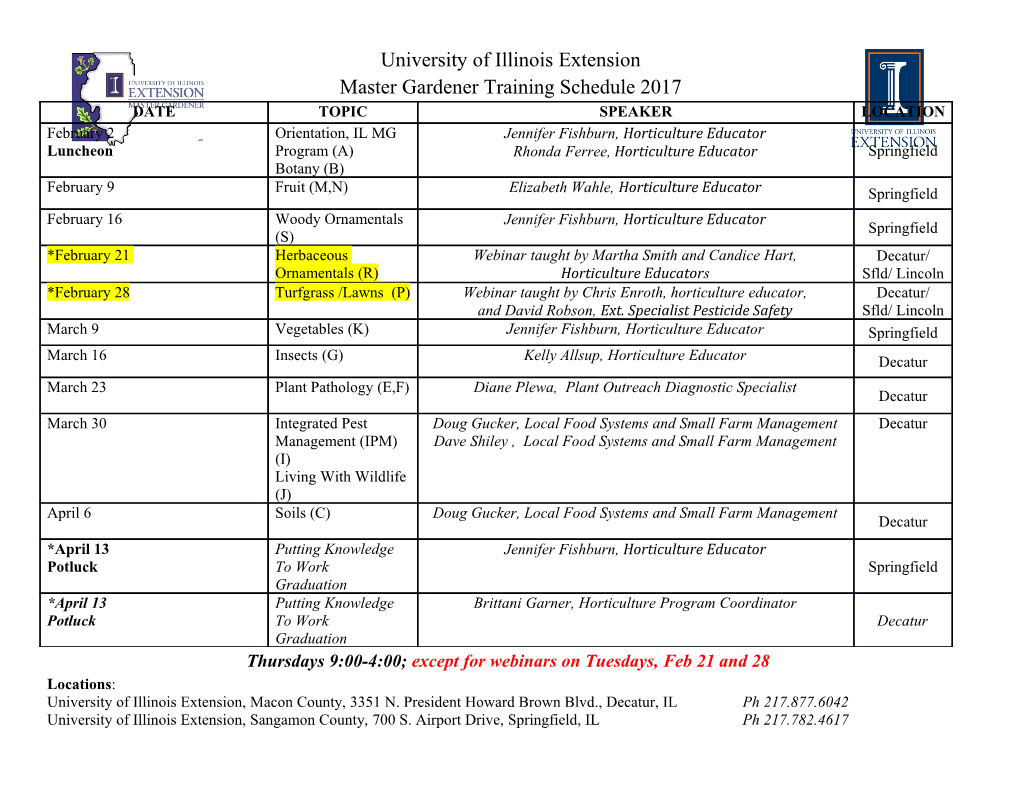
SHIPS HEAT GENERATION PLANT Boilers Water Treatment 2014.07.14 Pag |1 - 94 REPORT: ALVARO SARDINHA BOILERS WATER TREATMENT MARINE ENGINEER DATE: 2014.07.14 [email protected] INDEX 1. Introduction 2. BoilerBoilerssss water treatment ––– three factors 3. Boilers water fundamental knowledge 444.4. Ships heat generation plant 555.5. BoilerBoilerss water treatment 666.6. Main problems in boilers caused by water 777.7. Unex boilerboilerssss water recommendations 888.8. Lessons learned 999.9. Water chemistry terms Pag |2 - 94 REPORT: ALVARO SARDINHA BOILERS WATER TREATMENT MARINE ENGINEER DATE: 2014.07.14 [email protected] 1. INTRODUCTION If boilers water doesn’t receive proper treatment, the boiler will suffer from carryover, sludging, scale and corrosion, leading to weak and dangerous machinery. Long before the boiler fails, water-related problems will cause: ● Growing safety hazard ● Increased maintenance cost ● Additional fuel required - higher energy costs ● Lower boiler efficiency Correct boiler water treatment and follow-up of the water and steam condition, are of utmost importance for keeping the heat generation systems in good condition. By implementing a rigorous program of boiler water treatment, a vessel can greatly extend equipment life, reduce maintenance and enable thermal efficiency to be maintained at the designed level. The present report characterizes a ship heat generation system, its water treatment procedures and maintenance required. The main objective is to document the system and to establish optimal and standard operation processes. It is also an important piece of digital information, part of the ship information system, shareable and available for present and future crews, and a helpful tool to support company management. Pag |3 - 94 REPORT: ALVARO SARDINHA BOILERS WATER TREATMENT MARINE ENGINEER DATE: 2014.07.14 [email protected] 2. BOILERBOILERSSSS WATER TREATMENT --- THREE FACTORS 1. CHEMICAL TREATMENT Water normally contains various levels of contaminants, dissolved solids (minerals) and dissolved gases. These contaminants cause major operational problems and damage to boilers unless they are removed or controlled on a continuing basis. Correct application of chemical treatment programs can eliminate many problems associated with boiler operations. But other problems can and do impact operations. They are into two major areas: Management concerns - Addresses the administration of boiler water operations. Operator performance - Addresses the hands-on operation of boilers. 2. MANAGEMENT CONCERNS Every installation has its own mode of operation and style of management. Boiler water treatment is one small area of operations but is so critical that complete base operations may cease if boilers are not operated properly. Observations indicate that major difficulties found in boiler water treatment systems can be traced to management actions. 3. OPERATORS PERFORMANCE The successful operation of boilers requires accurate analysis of the water that is used, proper treatment to remove corrosive minerals and gases, and careful attention to the controls and procedures for the taking of water samples, their testing, and all required inspections. The key players are the boiler operators and, of course, assigned supervisors. A basic knowledge of boiler mechanics and water chemistry is an absolute requirement, whether through formal training or on the job training. Pag |4 - 94 REPORT: ALVARO SARDINHA BOILERS WATER TREATMENT MARINE ENGINEER DATE: 2014.07.14 [email protected] 3. BOILERBOILERSSSS WATER FUNDAMENTAL KNOWLEDGE A boiler is a device for generating steam, which consists of two principal parts: the furnace, which provides heat, usually by burning a fuel, and the boiler proper, a device in which the heat changes water into steam. The steam is then recirculated out of the boiler for use in various processes in heating applications. There are basically two types of boilers: A. WATER TUBE (20% of boilers in use) Water is fed through a bundle of tubes inside the boiler, and heat is applied to the outside of the tubes to heat the water. B. FIRE TUBE (80% of boilers in use) Heat travels through a bundle of tubes inside the boiler to heat the water surrounding the tubes. The bundle of tubes which carries water in the Water Tube Boiler and heat in the Fire Tube Boiler is called the Heat Transfer Surface. Both the Water Tube and the Fire Tube Boiler have the following components: HEAT SOURCE - A gas, oil, or coal burner heats the water in the oiler. HOTWELL - Tank that receives make-up water from ship water tanks and steam condensate from the condenser, feeding the boiler with water. The hotwell is heated to drive off dissolved oxygen and carbon dioxide gases before the water enters the boiler. Since these gases dissolve more readily in cold water, heating helps to eliminate them. Dissolved gases cause corrosion in the boiler. Scale and corrosion prevention chemicals are added at the hotwell to condition the water before it enters the boiler. CONDENSER – Equipment where steam return from consumers and is condensed by lowering its temperature, through sea water circulation and heat transfer. FEED WATER - The water entering the boiler from the hotwell. Feedwater = Make-up Water + Condensate Return Pag |5 - 94 REPORT: ALVARO SARDINHA BOILERS WATER TREATMENT MARINE ENGINEER DATE: 2014.07.14 [email protected] MAKE-UP WATER - The fresh water entering the hotwell from ship water tanks, to compensate steam losses and blow-down. It could be raw water received from shore or distilled water produced on ship. Make-up Water = Blow-Down + Condensate Loss FEED WATER PUMP - When heated water from the boiler is given off as steam, and the pump feeds water into the boiler from the hotwell. The feed water pump must generate sufficient pressure to overcome the pressure in the boiler. BLOW-DOWN VALVE - This valve allows some of the water carrying accumulated solids ("sludge") in the boiler to drain off. The act of removing water and sludge from the boiler is called "blow-down." WATER LEVEL CONTROL - The Water Level Control maintains the proper water level inside the boiler. This water level can be visually checked at the sight glass. The boiler tubes will become overheated if the water level is too low to keep the heat transfer surface covered. Low water level will cause excessive stress to the boiler. High water level will allow water to get into the steam lines, reducing the efficiency of the boiler system. SAFETY VALVES - These valves automatically releases any excess pressure that builds up in the boiler. Every boiler has several safety mechanisms that will shut it off in the event of malfunction. The boiler receives the feed water, which consists of varying proportion of recovered condensed water (return water) and fresh water, which has been purified in varying degrees (make-up water). The make-up water is usually distilled water or natural water, either in its raw state, or treated by some process before use. Feedwater composition therefore depends on the quality of the make-up water and the amount of condensate returned to the boiler. The steam, which escapes from the boiler, frequently contains liquid droplets and gases. The water remaining in liquid form at the bottom of the boiler picks up all the foreign matter from the water that was converted to steam. The impurities must be blown down by the discharge of some of the water from the boiler to the drains. The permissible percentage of blow-down is strictly limited by running costs and initial outlay. The tendency is to reduce this percentage to a very small figure. Pag |6 - 94 REPORT: ALVARO SARDINHA BOILERS WATER TREATMENT MARINE ENGINEER DATE: 2014.07.14 [email protected] Proper treatment of boiler feed water is an important part of operating and maintaining a boiler system. As steam is produced, dissolved solids become concentrated and form deposits inside the boiler. This leads to poor heat transfer and reduces the efficiency of the boiler. Dissolved gasses such as oxygen and carbon dioxide will react with the metals in the boiler system and lead to boiler corrosion. In order to protect the boiler from these contaminants, they should be controlled or removed, trough external or internal treatment. Natural water can damage a boiler by producing: 1) Scale and 2) Corrosion Water always contains some impurities in the form of dissolved solids and gases. The solids are calcium, magnesium, and other salts that form scale; the dissolved oxygen and carbon dioxide gases cause corrosion of metal. DISTILLED WATER SHOULD BE USED AT ALL TIMES. SCALE As water flows over rock formations and through the earth, it picks up and dissolves calcium and other metallic salts. When water enters a boiler, where it is heated to produce steam, these dissolved solids precipitate out of solution. The precipitates are left behind in the boiler water - they do not travel with the steam. If they are allowed to accumulate, they will settle out as scale on the boiler metal. This is what happens when water in a pan on the stove is allowed to boil dry, or when water in a glass is allowed to evaporate completely. A residue of salts will be left, which is scale. When chemical treatment is not used, scale forms in a boiler. If scale is allowed to build up, it reduces the heating efficiency of the boiler. A heavily scaled boiler heats water to steam at a slower rate, because the scale acts as an insulator. This increases operating costs. Pag |7 - 94 REPORT: ALVARO SARDINHA BOILERS WATER TREATMENT MARINE ENGINEER DATE: 2014.07.14 [email protected] The amount of scale depends on the amount of dissolved solids in the water. If water is added, the scale residue will not go back into solution. The U.S. Bureau of Mines has determined that a thickness of only 2,82 mm scale in a boiler increases fuel costs in 16%.
Details
-
File Typepdf
-
Upload Time-
-
Content LanguagesEnglish
-
Upload UserAnonymous/Not logged-in
-
File Pages94 Page
-
File Size-