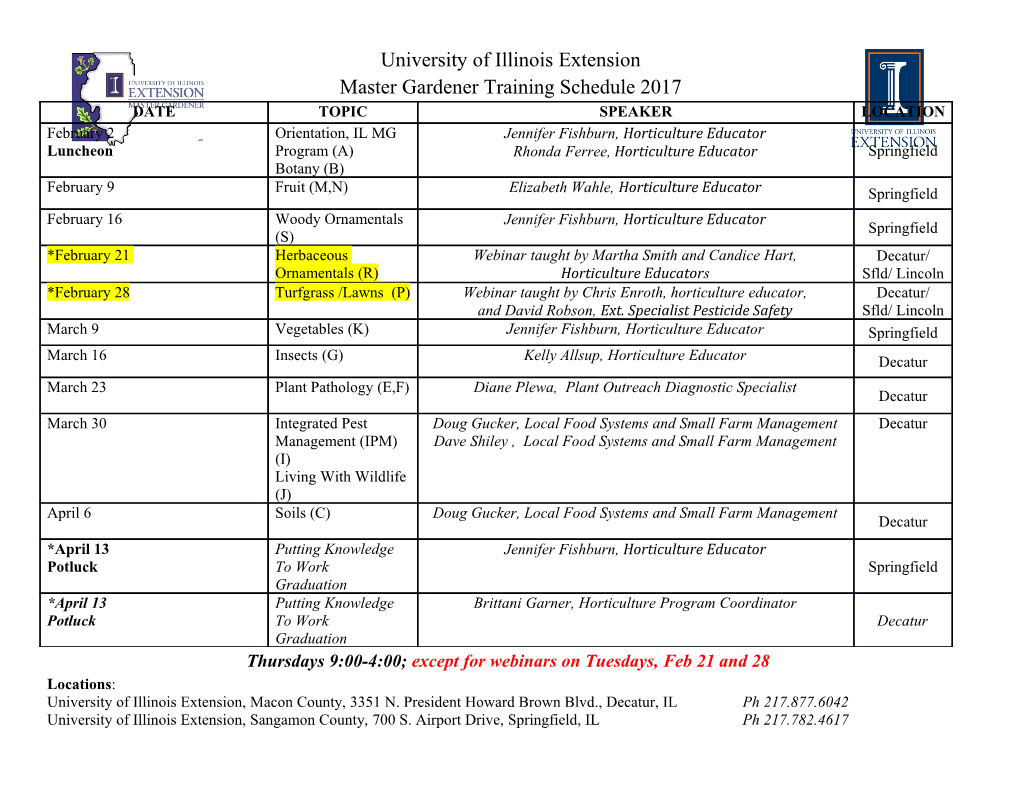
(19) TZZ Z¥_T (11) EP 2 420 593 B1 (12) EUROPEAN PATENT SPECIFICATION (45) Date of publication and mention (51) Int Cl.: of the grant of the patent: C23C 18/20 (2006.01) H05K 3/42 (2006.01) 03.04.2013 Bulletin 2013/14 C23C 18/32 (2006.01) C23C 18/38 (2006.01) H05K 3/38 (2006.01) H05K 3/46 (2006.01) (2006.01) (2006.01) (21) Application number: 11173897.7 C25D 5/12 C25D 5/56 H05K 3/18 (2006.01) (22) Date of filing: 14.07.2011 (54) Metalized Plastic Articles and Methods Thereof Metallisierte Kunststoffartikel und Verfahren dafür Articles plastiques métallisés et procédés associés (84) Designated Contracting States: •ZHOU,Liang AL AT BE BG CH CY CZ DE DK EE ES FI FR GB 518118 Shenzhen (CN) GR HR HU IE IS IT LI LT LU LV MC MK MT NL NO • MIAO, Weifeng PL PT RO RS SE SI SK SM TR 518118 Shenzhen (CN) • ZHANG, Xiong (30) Priority: 19.08.2010 CN 201010260236 518118 Shenzhen (CN) (43) Date of publication of application: (74) Representative: Gulde Hengelhaupt Ziebig & 22.02.2012 Bulletin 2012/08 Schneider Patentanwälte - Rechtsanwälte (73) Proprietor: BYD Company Limited Wallstrasse 58/59 Shenzhen 518118 (CN) 10179 Berlin (DE) (72) Inventors: (56) References cited: • GONG, Qing EP-A1- 1 650 249 US-A- 3 546 011 518118 Shenzhen, (CN) US-A- 4 767 665 US-A- 5 162 144 Note: Within nine months of the publication of the mention of the grant of the European patent in the European Patent Bulletin, any person may give notice to the European Patent Office of opposition to that patent, in accordance with the Implementing Regulations. Notice of opposition shall not be deemed to have been filed until the opposition fee has been paid. (Art. 99(1) European Patent Convention). EP 2 420 593 B1 Printed by Jouve, 75001 PARIS (FR) 1 EP 2 420 593 B1 2 Description CuFe204-δ, Ca0.25Cu0.75TiO3-β, and Ti02-σ, wherein δ, β, σ is deemed to be 0.05 ≤δ≤0.8, 0.05≤β≤0.5, and [0001] The present disclosure relates generally to 0.05≤σ≤1.0; plastic articles and a manufacturing method thereof. In removing plastic material in a determined area of a more particularity, the present disclosure relates to a sur- 5 surface of the plastic substrate; and face metallization method for the plastic article. plating the exposed surface of the plastic substrate to form a first metal layer; plating the first metal layer BACKGROUND OF THE PRESENT DISCLOSURE to form a second metal layer. [0002] Plastic substrates having a metalized layer on 10 [0005] Optionally, further metal layers may be subse- theirsurfaces as pathways of electromagnetic signal con- quently plated. duction are widely used in automobiles, industries, com- [0006] According to another aspect of the present in- puters and telecommunications etc. Selectively forming vention, there is provided a plastic substrate being made a metalized layer is one of the important processes for of a plastic material, in which a plurality of accelerator preparing such plastic products. The method for forming 15 particles are dispersed, the accelerator particles being a metalized layer in prior art is usually practiced by form- made of a compound selected from the group consisting ing a metal core as a catalytic center on the plastic sup- of: CuFe2O4-δ, Ca0.25Cu0.75TiO3-β, and TiO2-σ, wherein port surface so that chemical plating may be performed. δ, β σ is deemed to be 0.05≤δ≤0.8, 0.05≤β≤0.5, and However, processes related thereto are complex where 0.05≤σ≤1.0; and a metalized surface directly disposed strict demand on equipment is needed whereas the en- 20 on the plastic substrate and being composed of a plurality ergy consumption is high. Further, there is a low adhesive of metal layers. force between the coating and the plastic support. [0007] Another aspect of the present invention refers [0003] One example in US patent No. US2003031803 to a plastic substrate being made of a plastic material, in A1 discloses a process for metalizing a substrate part, which a plurality of accelerator particles are dispersed, including the following three steps: coating said part with 25 the accelerator particles being made of a compound se- a precursor composite material layer consisting of a pol- lected from the group consisting of: CuFe2O4-δ, Ca0.25 ymer matrix doped with photoreducer material dielectric Cu0.75TiO3-β, and TiO2-σ, wherein δ, β , σ is deemed to particles, irradiating the surface to be metalized of said be 0.05≤δ≤0.8, 0.05≤β≤0.5, and 0.05≤σ≤1.0. substrate part with a light beam emitted by a laser, im- [0008] Further embodiments of the invention could be mersing the irradiated part in an autocatalytic bath con- 30 learned from the claims and the following description of taining metal ions, with deposition of the latter in a layer the invention. on the irradiated surface, and wherein the dimension of said dielectric particles is less than or equal to 0.5 mi- DETAILED DISCRIPTION OF THE EMBODIMENT crons. Another example in US patent No. US7060421 discloses a method of producing a conductor track struc- 35 [0009] In the following, a new method of manufacturing ture on a non-conductive support comprising: providing a plastic article with a metalized surface is disclosed. a non-conductive support having at least a surface Thereby, a plastic article is provided having a metalized formed of a non-conductive supporting material having surface, which is directly disposed on the plastic sub- at least one thermally stable, spinel- based, non-conduc- strate and being composed of a plurality of metal layers. tive metal oxide which is stable and insoluble in aqueous 40 Further, a substrate useful for the manufacturing method acid or alkaline metallization baths dispersed therein; ir- is disclosed. radiating areas of said support on which conductive tracks are to be formed with electromagnetic radiation to Accelerator particles break down the non- conductive metal oxides and release metal nuclei, and subsequently metalizing the irradiated 45 [0010] The accelerator particles are selected from the areas by chemical reduction. group consisting of: CuFe 2O4-δ, Ca0.25Cu0.75TiO3-β, and TiO2-σ, and δ, β, σ is deemed to be 0.05≤δ≤0.8, 0.05≤β SUMMARY OF THE DISCLOSURE ≤0.5, and 0.05≤σ≤1.0 [0011] The average diameter of each accelerator par- [0004] According to one aspect of the present inven- 50 ticle may range from 20 nanometers to 100 microns, al- tion,there isprovided a method of manufacturinga plastic ternatively from 50 nanometers to 10 microns, and alter- article with a metalized surface composed of a plurality natively from 200 nanometers to 4 microns. The accel- of metal layers comprising the steps of: erator particles may be from 1 wt% to 40 wt% of the total weight of the plastic substrate, alternatively from 1 wt% providing a plastic substrate made of a plastic ma- 55 to 30 wt%, and alternatively from 2 wt% to 15 wt%. terial, in which a plurality of accelerator particles are [0012] Particularly suitable accelerators may include: dispersed, the accelerator particles being made of a CuFe2O3.65, CuFe2O3.2, Ca0.25CU0.75TiO2.84, Ca0.25 compound selected from the group consisting of: Cu0.75TiO2.5, TiO, and TiO 1.9. Still further suitable accel- 2 3 EP 2 420 593 B1 4 erators, may include CuFe2O3.65, Ca0.25CU0.75TiO2.84, cancies may have strong reducibility and instability. For and TiO. example, the accelerator particle CuFe2Ox (x<4) has [0013] The accelerator particles may be commercially strong reducibility and instability due to: a) CuFe 2Ox(x<4) provided, or prepared by any technique known to those has oxygen vacancies and oxygen may be efficiently 5 skilled in the art. For example, suitable methods for pre- combined to crystal lattice of CuFe2Ox(x<4); b) In paring the accelerator particle may include steps of: pre- CuFe2Ox(x<4), electron transfer may exist not only be- paring metal oxides/composite metal oxides by any tech- tween Cu+ and Cu2+, Fe2+ and Fe3+, but also between nique known to those skilled in the art, such as co-pre- Cu+ and Fe3+, electron transfer may cause the lost of cipitation, sol-gel, hydrothermal process, solid state sin- electrons which indicates a strong reducibility; c) During 10 tering, etc., or commercially provided; and calcining the the period of forming oxygen vacancies in CuFe2O4, a metal oxides/composite metal oxides at high tempera- large amount of cations may be combined in the crystal- ture in the presence of hydrogen of inert gases to form line lattice thereof, causing a extension of crystalline lat- oxygen vacancies thereof to obtain the accelerator par- tice gap, change of crystalline lattice, and the increasing ticle. of chemical potential energy. Therefore, CuFe2Ox(x<4) [0014] Methods of preparing suitable accelerator par- 15 with oxygen vacancies may have very instable structure ticles are generally known. A method for preparing and oxygen ions may be needed to fill the oxygen vacan- CuFe2O4-δ may comprise the steps of: adding a mixture cies, which may form a strong reducibility. of Cu(NO3)2 and Fe(NO3)3 into a stirring potassium hy- [0020] According to various embodiments of the droxide solution by a peristaltic pump with a speed of 1 present disclosure, the metal oxide or metal composite milliliter per minutes; heating the solution to a tempera- 20 oxide with a certain range of oxygen vacancies may be ture of 80 °C and keep stirring for 24 hours, PH value of used as accelerator particles, and metal layers may be the solution maintaining at 10 to 11 while stirring; cleaning plated directly on the accelerator particles.
Details
-
File Typepdf
-
Upload Time-
-
Content LanguagesEnglish
-
Upload UserAnonymous/Not logged-in
-
File Pages11 Page
-
File Size-