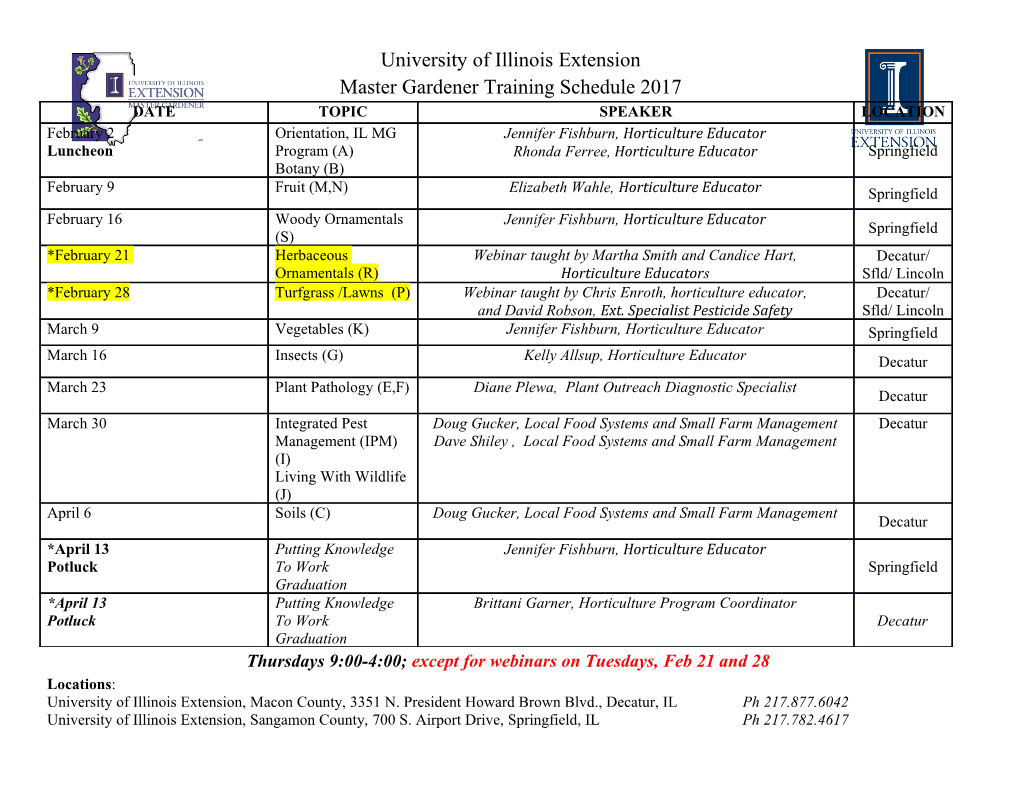
Fast Curing of Composite Wood Products Program Review by A.J. Ragauskas Research Team Institute of Paper Science and Technology Georgia Institute of Technology Art J. Ragauskas, Associate Professor Chemistry Dong Ho Kim, Post Doctoral Research Fellow Jason Montegna, MS student Auburn University School of Forestry Thomas Elder, Professor of Forestry Utilization of Southern Forest Products, USDA-Forest Service Southern Research Station, Pineville, LA Industrial Partners Georgia-Pacific Resins, Inc. -Resins, press time, & Decatur, GA technical expertise Georgia-Pacific Building Products Louisiana-Pacific Corporation Sherwood, OR -Wood chips, technical expertise Weyerhaeuser OSB Business Tacoma, WA -Wood chips & technical expertise Project Objectives Develop low temperature curing technologies for composite wood products manufactured with UF and PF resins by: • Identifying rate limiting UF and PF curing reactions with current market resins. • Examining the use of new catalysts to accelerate curing reactions to reduced press temperatures and times. • Improve Board Properties. U.S. Technology Market • 20 MDF mills • 41 OSB mills • 48 PB mills 1. Debarking 2. Mechanically refined wood 3. Drying 3’. Resins/mat formation/pressing Project Deliverables • Characterize SW and HW woodchips • Prepare OSB, MDF, and PB • Characterize boards for physical strength properties & curing chemistry •NMR & DSC • Evaluate impact of extractives on composite board properties • Evaluate curing chemistry of PF and UF for composite board • Examine impact of plate pressure & temperature on curing resin chemistry • Design & evaluate effect of curing catalyst for composite board formation Program Deliverables • Evaluate pretreatments to mitigate detrimental wood extractives effects • Test catalyst curing technology • Employ catalyst to lower curing temperature • Characterize board properties and chemistry with new catalyst • Perform energy audit for new catalyzed composite board formation process • Final report Characterize Woodchips/Resins Commercial OSB Wood Strands % Extractives % Moisture Content Pine 4.2% 4.0% Aspen 4.4% 3.7% Hardwood 4.4% 7.1% Strand Dimensions: (0.5-0.7mm) x (20-30mm) x (20-40mm) Resins*: UF PF-3110 PF-3121 pH 7.5 11.0 9.7 Solids Content 64.4% 46.2% 58.8% * Commercial resins Evaluate Curing Chemistry PF and UF Gel Time Experiment • ASTM: D 3056-00 • 100.0oC • Insert sample into sample vial •Rapidly add catalyst • Begin stirring • Allow test specimen to remain in bath till stirring stops Evaluate Curing Chemistry PF and UF 40 35 30 25 20 15 Gel Time (min) Time Gel 10 5 0 UF Resin PF: 3121 PF: 3110 Evaluate Curing Chemistry PF and UF O 40 O O 35 O 30 H ) O 25 Me 20 O O Gel time (min 15 O Control 10 O tetraethylenepentamine O 5 10% Triacetin 10% Propylene Carbonate 0 O 10% Methyl Formate UF Resin PF: 3121 PF: 3110 HN NH2 N 2 Evaluate Curing Chemistry PF and UF 40 35 30 25 20 15 10 Control Gel Times (min) 5 5% Additive 1 10% Additive 1 0 15% Additive 1 UF PF: PF: Resin 3121 3110 Evaluate Curing Chemistry PF and UF 35 30 25 20 15 Gel time10 (min.) 5 0 Control 0.1% Additive 2 0.5% Additive 2 1.0% Additive 2 5.0% Additive 2 P P U F F: F :3 3 1 12 10 1 Evaluate Curing Chemistry UF: Binary Effects 40 35 30 25 20 15 Gel Time (min) Time Gel 10 5 0 Control 1% Methyl 10% Additive 1 1% MeF + 10% Formate Add. 1 Evaluate Curing Chemistry PF: Binary Effects 35 30 25 20 15 Gel Time (min) Time Gel 10 5 0 PF:3121 Control PF3110 1% P r o p y l e n e Carbonate 10 % A d d i t i v e 1 10 % A d d . 1 + 1% P r o p y l . Evaluation of Additive 1 For OSB Production Preliminary Studies OSB Production: Experimental Procedure •Wood strands were weighed to yield final board densities of approximately 0.62 gr/cm3. •The PF and UF resins/additives applied onto wood strands via air sprayer unit •Blended furnish was then hand felted into a form box with aluminum cauls. •Mat consolidation and curing were accomplished using a laboratory hydraulic press (Carver press, 6” x 6”). •PF resins treated strands were cured at a press temperature of 350oF with 2.8 Mpa pressure for 3 minutes. •UF treated strands were treated in a comparable method except the press temperature was 300oF. OSB Production: Experimental Procedure After board formation •All boards were conditioned at 20oC and 50% humidity for 72 hrs. Thickness swelling and water adsorption were measured according to ASTM D1037 and DIN52364. The specimens were soaked in deionized water at 20oC. After 2 hrs, the specimens were withdrawn from the water and wiped with a paper towel to remove excess water. Increases in weight and thickness during the immersion were calculated on a mass basis and expressed as percentage. OSB Laboratory Results 160 140 120 100 80 % increase 60 40 20 0 PF3110(5%) PF3110(5%)/Additive I (5%) PF3121(5%) PF3121(5%)/Additive 1(5%) UF(5%) UF(5%)/Additive 1(5%) W T a hi te ck r A ne b s so s rp Sw t. ell ing Preparation and Evaluation of Control and Additive OSB Production Follow-Up Studies OSB Follow-Up Studies: Pilot Plant OSB Strands: 2.1kg per a board Mat Dimension: 40.6 x 40.6 x 2.9 cm Mat Formation: One layer with random orientation Target Density: 0.688 gr/cm3 Resin Content: 3.5%(based on OD wt of strands) Wax Content: 1% on oven dry wood Resin: PF3110 Blend Moisture Content: 7.0-7.5% Press temp: 400oF Press pressure: 95, 120 tons - recommended by GP OSB Follow-Up Studies: Pilot Plant Thickness Sw elling: 2h 20 Water Absorption: 2h 18 16 14 12 10 8 6 % Change 4 2 0 Wa ter Absorption: 2h Thickness S w e llin g :2h OSB Follow-Up Studies: Pilot Plant 60 Thickness Sw elling: 24 h 50 Water Absorption: 24h 40 30 % Increase 20 10 0 Wa ter Absorption: 24h Thickness S w e llin g :24 h Control, 95tons 120tons tons Control, 120tons 0.5% Additive 2, 0.5% Additive 1% 1, 95tons Additive 2% 1,95tons Additive 5% Additive 1, 95tons5% Additive 1.5% 2, 120 Additive additive 2, 120 tons 0.5% 2, 5% Additive OSB Follow-Up Studies: Pilot Plant OSB Board IB Density/(kg/m3)IB/psi Control 4.50 min, 95 ton 705 36.9 4.75 min, 95 ton 692 37.8 Additive 1 1% 4.50 min, 95 ton 712 54.1 2% 4.50 min, 95 ton 700 45.3 4.75min, 95 ton 722 42.5 5% 4.50 min, 95 ton 707 39.2 OSB Follow-Up Studies: Pilot Plant OSB Board IB Density/(kg/m3)IB/psi Control 4.75 min, 120 ton 734 40.0 5.00 min, 120 ton 705 42.9 Additive 2 0.5% 4.75 min, 120 ton 689 43.1 1.0% 4.50 min, 120 ton 709 45.3 NMR Studies: PF and UF Curing OH OH OH PF resin Chemistry CH2 CH2 O OH OH HOH C CH OH 2 2 CH CH CH Heat 2 2 2 H2CO O O O Water Released CH2 CH2 CH2 Phenol CH2OH CH2 CH2 OH OH OH UF Curing Chemistry O O O H CO 2 OH H2CO HO OH H N NH 2 2 H2N NH HN NH Urea Monomethylol Urea Dimethylol Urea OO Heat HO NH NH N NH Loss of Water H2C HO N NH N NH H2C OO NMR Studies: PF and UF Curing C2-6 -CH2- C2-6 downfield -CH2-O- sidebands C =O C2-6 upfield 1 sidebands -COx Solid state CP/MAS 13C NMR spectrum of PF 3110 resin as curing of 64 minutes. NMR Studies: PF and UF Curing 3.0 F / P -CH2-/ P CH2-O / P o 2.0 Mol Rati 1.0 0.0 0 20 40 60 80 100 120 140 Curing Time, min The mol ratio of methylene C to phenol C of the resin PF 3110. –CH2-/P: ratio of methylene/phenol; CH2-O /P : ratio of oxygenated methylene /phenol NMR Studies: PF and UF Curing 3.0 F / P -CH2-/ P CH2-O / P o 2.0 Mol Rati 1.0 0.0 0 20406080100120140 Curing Time, min The mol ratio of methylene C to phenol C of the resin PF 3121. –CH2-/P: ratio of methylene/phenol; CH2-O /P : ratio of oxygenated methylene /phenol NMR Studies: PF and UF Curing 3.0 o 2.0 F / U -CH2-/ U Mol Rati 1.0 CH2-OH /U 0.0 0 20 40 60 80 100 120 140 Curing Time, min The mol ratio of methylene C to urea C of the UF resin. –CH2-/U: ratio of methylene/urea; CH2-O /U : ratio of oxygenated methylene / urea; F/U: ratio of total methylene/ urea. Data indicated that the ratio of methylene and hydroxymethyl C/ urea C decreased as the curing proceeded. Evaluate Impact of Extractives on Composite Board Properties Evaluating Extractives: Exper. Procedure • Received industrial SW MDF, OSB, and PB furnish • Solvent extracted the wood furnish for 36 h • Used starting and extracted wood furnish for OSB, PB, and MDF • Tested for Physical Properties including: Thickness Swelling, Water Adsorption Evaluating Extractives: Experimental Results 140 120 100 80 % Change 60 40 20 0 OSB (PF:3110) OSB extractives free PB (UF) PB extractives free MDF (UF) MDF extractives free Water Absorption Thickness Sw elling Enzyme Pretreatment: OSB Results 80 75 70 65 % 60 55 50 45 40 O SB control O SB pretr Enzy 1 (1 U/g) O SB pretr Enzy 1 (5 U/g) O SB pretr Enzy II (1 U/g) OSB pretr Enzy II (5 U/g) % TS % WA Enzyme Pretreatment: Results % C h a n g e 130.0 12 0 .
Details
-
File Typepdf
-
Upload Time-
-
Content LanguagesEnglish
-
Upload UserAnonymous/Not logged-in
-
File Pages62 Page
-
File Size-