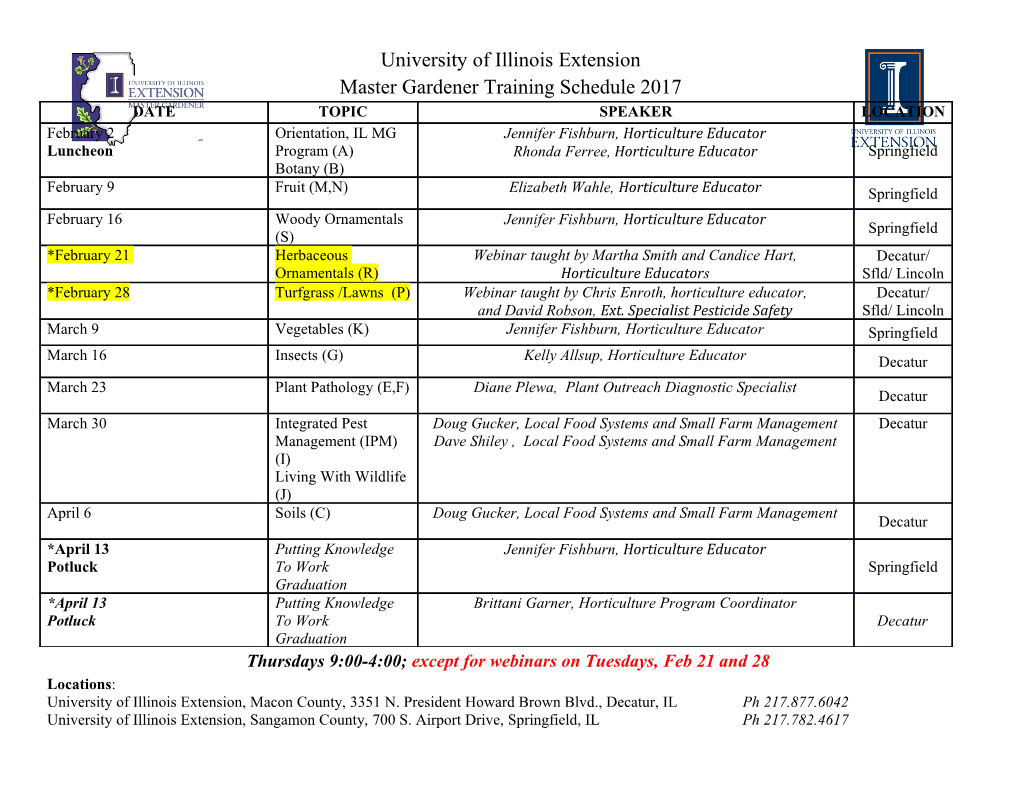
® Copyright 2015 AFVBM, Inc. LECTURE PRESENTATION "THE HISTORY OF REPAIRS AND NEW METHODS OF RESTORATION" MR. RENE A. MOREL On The Occasion Of The Fifth Annual General Meeting Newport Beach, California Saturday 26 April, 1986 i ® Copyright 2015 AFVBM, Inc. ® Copyright 2015 AFVBM, Inc. I N T R O D U C T I O N The Publications Committee is pleased to present this edited transcription of Mr. Morel's lecture to the membership, delivered at the Fifth Annual General Meeting in Newport Beach, California, on Saturday, 26 April, 1986. As Chairman of the Methods and Workmanship Committee, Mr. Morel was asked by the Board of Governors to present these materials in the form of an illustrated lecture. Rene A. Morel, a violin maker with a distinguished reputation as a restorer among artists in the United States and Europe was born in Saint Remy-Aux-Boix, France in 1932. At the age of 12 he studied violin making with Marius Didier in Mirecourt. His training continued under Amedee Dieudonne in Mirecourt and Marius Bossard in Rennes. At the age of 20 Mr. Morel joined the French Air Force where he became a pilot and built two small 2-passenger airplanes. In 1955 he moved to New York City to study with Simone F. Sacconi at the firm of Rembert Wurlitzer for 9 years. In August, 1964, Mr. Morel established a restoration facility at Jacques Francais Rare Violins, Inc., and since that time has worked in directing restoration as well as teaching. He also serves the .firm as Vice-President. Mr. Morel is a member of the International Society of Violin and Bow Makers and a founding member of the American Federation of Violin & Bow Makers. Of himself, Mr. Morel writes: "My work is very French, but now has a strong Italian influence. I care a great deal for sound and varnish. My stay with Maestro Sacconi made me love restoration of the famous instruments, the field which I am known today by the famous string artists of the world." We would like to express the thanks of the Federation to Mr. Morel for his lecture and the illustrated materials that are presented in the body of this publication. The Publications Committee William L. Monical, Chairman Robert Ames David Gusset ii ® Copyright 2015 AFVBM, Inc. ® Copyright 2015 AFVBM, Inc. THE HISTORY OF REPAIRS AND NEW METHODS OF RESTORATION By Rene A. Morel Well, ladies, gentlemen, dear colleagues, it is easier for me to make an appraisal on a restoration or sit at the bench with a knife and a gouge than to make a speech. But I think that the experience that I gained in this country makes it only fair to every one of you, that I share it with you. I was asked to talk to you about the history of repair and how we came to new methods of restoration. I find it very hard to talk about repair history, because you all know that shops were very secretive while I was in my youth, and it was difficult to get information from craftsmen who had a certain way of doing their own repairs. It was also very hard for me to find two books that would agree on the same dates, or the same ideas, and therefore I will not be too specific about anything as far as we talk about the history of repair. Now I will start my lecture, and what I am going to say to you is not to criticize or praise one or another person, or even a country. But it is simply to talk to you about my experience in the field of repair with different ateliers in Europe and the United States. By letting you know what I am doing, I think that we can exchange some of our new approaches in methods to improve restoration. About the history of repair, we know various articles in different books that will give some ideas, but none that give an accurate date for the beginning of methods of repair. Stradivari himself did not do repairs; if an instrument got accidented, he replaced the part that was damaged. We know of a few instruments of Stradivari that were made in the late 17th century and later the top was replaced by him in the 18th century. We witness sometimes repairs done to lute, gambe, or guitar, where cracks were glued and reinforced with paper, linen, or parchment, all of which are soft materials. The 18th century probably saw the very first repair but it is quite difficult to know what was done to the instrument. However, as the neck of the instrument needed to be changed for longer string length to accommodate playing, therefore, the luthier had to learn how to insert the foot of the neck into the upper block. And for this change in the neck, it had to happen probably at the beginning of the 18th century. I will not be able to give you a specific date on this. It is my opinion that the 19th century saw the start of more complicated repair and probably also more radical re-graduation which caused bad damage to instruments. Re-graduation was done in search of more response and volume to the sound. Wood was removed from top and back plates, making the instrument easier to vibrate, but of course as we know today, losing the core and the very essential fundamental of sound. Later, the creation of a harder string plus a larger audience proved that the thinned instrument didn’t have the same power and projection and therefore there was a need to add new wood. If the lute and guitar could be reinforced with paper and linen, the violin family needs studs for more strength, especially when the soundpost cracks happened. I will quote to you some reading of 1 ® Copyright 2015 AFVBM, Inc. ® Copyright 2015 AFVBM, Inc. books and give you information on where I was able to learn by then how to repair in more advanced techniques. Everyone had to know how to remove the top of the instrument, how to make a different bass-bar, and how to give more support to the top by raising the neck to a higher "pitch", or neck angle. This in turn required a new top block in order to reset the neck. The opening and closing process was already going strong in the last quarter of the 18th century. By taking the top off maybe a little carelessly, wood chips would be missing. With the wear and tear of the edge at the shoulder area, eventually new underlay edges were necessary to reinforce those areas. Now we are faced with the underlay, and the need of a counterpart to apply pressure for the gluing of this underlay. The first material used for this counterpart, I suppose, was some sort of a cardboard or some kind of a soft material. Later, some more industrious luthiers backed the counterpart up with wood. It was then that the arching and groove of instruments were greatly damaged. We will see further on how we can remedy this and restore it. In the first re-cutting of instruments, the groove disappeared because repairmen did not know of materials to produce an accurate counterpart. I'm sure many of you have seen cut-down instruments with no groove. A book from l'Abbe Sibire is very interesting. Some of you may have heard of this man. He was a Priest who was in love with instruments. His book, Le Parfait Luthier, published first in 1806, said, and I quote, "Violin making is the only craft in the world where the old is better than the new and the upkeep more difficult than building." Then he mentions a great maker-restorer named Namy. Jean Theodore Namy was famous throughout the world for 25 years for his ability to replace a damaged top with a copy, or to cut down and enlarge instruments. The book is printed in 1806. He doesn't give you any further explanation, but just mentions 25 years of experience. This shows that there was a man able to cut and enlarge instruments. I went to the Vannes book that you all know, and it says Namy, Jean Theodore worked in the shop of Salomon's widow in 1772. Died, Place de Louvre in Paris in 1808. The l'Abbe Sibire mentioned that Namy cut and enlarged instruments for 25 years. Now, was that man so ahead of everybody else? If this is true, it does mean that by 1775, there was already a man able to cut and enlarge instruments. And the l'Abbe Sibire praised Lupot as the new Stradivari, probably because Nicolas Lupot, born in 1758, was the source of information for l'Abbe Sibire’s book. In his book he is convinced that Lupot has found the secret of the varnish. Sibire mentions Lupot as a great restorer and gave his method of raising archings and reshaping tops. Hold on now! It consists of using the soft part of bread. "Break it in small pieces, dip it in water and milk, (I don’t know why the milk), lay it on the inside of the plate for about l cm thick. Keep it moist, and the moisture gradually will give back the wood its natural shape." I must admit to you, I haven't tried this method yet. Sibire continues: "The first soundpost patch, if at best, a counterpart was made; it was certainly fitted by eye. The fitting of the patch leaving l mm of the original wood and crossing two or three grains with the new wood was done in order to make sure the repair was stronger.
Details
-
File Typepdf
-
Upload Time-
-
Content LanguagesEnglish
-
Upload UserAnonymous/Not logged-in
-
File Pages22 Page
-
File Size-