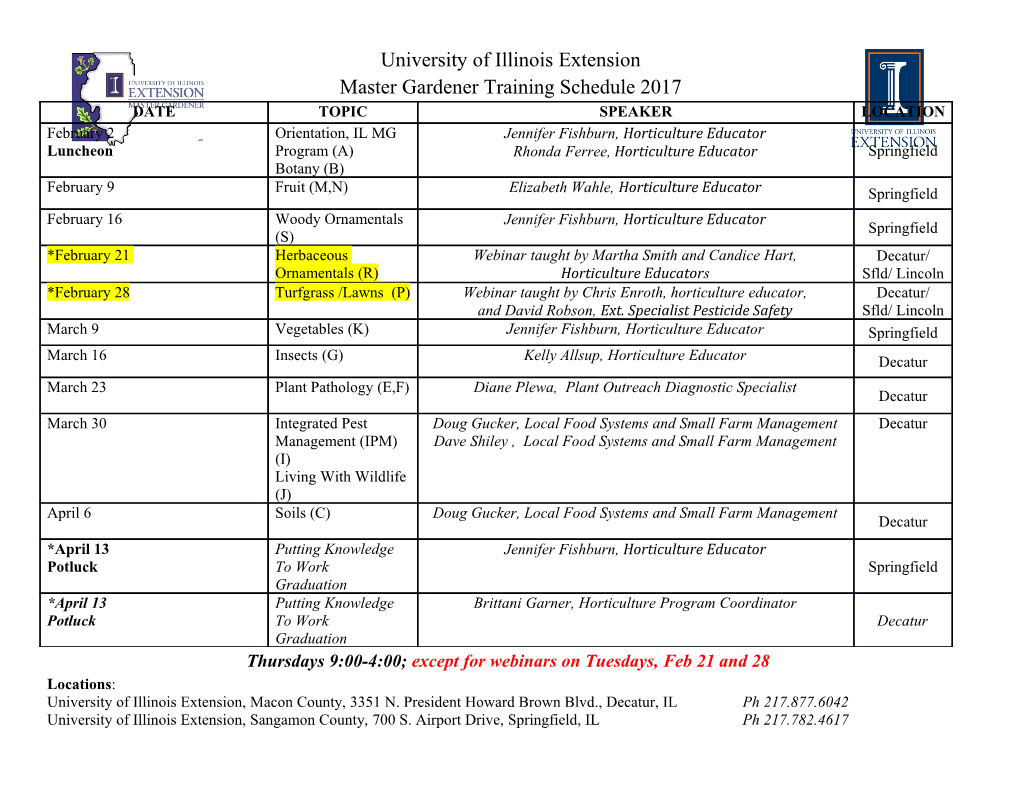
MIKE BUSCH COMMENTARY / SAVVY AVIATOR Not-So-Plain Bearings There’s a lot more to engine bearings than meets the eye ACCORDING TO MERRIAM-WEBSTER, a bearing is “a machine part in swings. That’s why nearly all reciprocating which another part turns.” Most aircraft have lots of them. engines—from one-cylinder motorcycle Wheels spin on their axles with the help of tapered roller bear- engines to giant marine diesels—use plain ings. Magnetos, alternators, generators, and starter motors bearings instead of ball or roller bearings. incorporate ball bearings to support their rotors. The landing gear These plain bearings and bushings look trunnions on my Cessna 310 pivot on needle bearings. Variable-pitch simple, but they aren’t. There’s a lot more to propeller blades are supported by large-diameter ball bearings. them than meets the eye. Turbine engine rotor shafts spin in ball and roller bearings. All these bearings consist of inner and outer “races” with spherical or cylin- LUBRICATION drical rolling elements between them. Such “rolling-element When I had the engines in my Cessna 310 bearings” do a superb job of supporting a shaft in precise position torn down for overhaul in 1990, I made a while permitting it to rotate with very little friction. point of paying a visit to the engine shop to But tear down a Continental or Lycoming engine and you won’t survey the damage before the engine was fi nd bearings like those. The bearings in which the crankshaft, crank- put back together. The engines had accumu- pins, camshaft, rocker shafts, and piston pins run have no races, balls, lated 1,900 hours over 11 years, and I rollers, needles, or other moving parts. They’re just curved pieces of remember being rather astonished at the metal—known variously as “plain bearings” or “sleeve bearings” or appearance of the main and rod bearings; “bushings”—that rely on sliding elements rather than rolling ones. they looked nearly brand new! Plain bearings are usually constructed of two semicircular halves How can a plain bearing with no rolling called “shells”; one-piece plain bearings are usually called “bushings.” elements withstand the torturous environ- There’s a good reason that reciprocating engines use plain bear- ment of a high-performance turbocharged ings: They reciprocate! This means that the crankshaft, crankpin, reciprocating aircraft engine for 1,900 hours piston pin, rocker shaft, and camshaft bearings are subject to contin- and 11 years without showing any signifi cant uous sharp cyclic loads. Rolling-element bearings don’t handle such signs of wear? There’s a two-word answer: loads very well, because they concentrate loads into very tiny con- hydrodynamic lubrication. tact regions between the rolling elements and the races, resulting in Plain bearings rely on hydrodynamic extremely high pressures. If ball bearings were used in a reciprocat- lubrication to prevent metal-to-metal ing engine, the result would be peened races, fl at-spotted balls, and contact between the rotating journal and consequent short bearing life. the stationary bearing. (See Figure 2.) By contrast, plain bearings tolerate such cyclic loads better Pressurized oil is pumped continuously because they distribute the loads over a much larger area, so the into the gap between the journal and the pressure is greatly reduced. They also do a better job of accommo- bearing. This gap is only about 0.002 inch dating shaft fl exing, minor misalignments, and wide temperature wide—about the thickness of a human hair. 26 Sport Aviation March 2014 PHOTOGRAPHY COURTESY OF MIKE BUSCH 226-30_savvyMAR.indd6-30_savvyMAR.indd 2626 22/12/14/12/14 33:26:26 PPMM Rotation of the journal within the bearing, for hydrodynamic lubrication simply do not together with the viscosity of the oil, creates exist. Consequently, there is metal-to-metal a dynamic wedge of high-pressure oil that contact between the journal and the bearing, keeps the parts separated. So long as the and wear is inevitable. bearing gets adequate oil pressure and the This startup wear is mitigated in several journal rotates rapidly enough, there is no ways: The mating journal and bearing sur- metal-to-metal contact and therefore no faces are polished as smooth as possible. The wear on either the bearing or the journal. bearing surface is made of a material that has Does this mean that plain bearings can last low sliding friction against the steel journal. Figure 2—Plain bearings rely on hydrodynamic lubrication to prevent forever? Actually yes, provided the engine is Anti-wear additives in the oil react with the metal-to-metal contact between the rotating journal and the run continuously (as it might be in a test cell) metal to form a thin protective fi lm on the stationary bearing. with an uninterrupted oil supply and uninter- surfaces that further reduces friction through rupted journal rotation. Unfortunately, that’s a phenomenon known as “boundary lubrica- not what happens in the real world. We start tion.” (See Figure 3.) up our engines, run them for an hour or three while we’re fl ying from point A to point B, GETTING OIL TO THE BEARINGS and then shut them down. It’s mainly those Once the engine is running, pressurized oil pesky startups and shutdowns that limit the passes through “galleries” (often misspelled useful life of plain bearings. “galleys”), which are internal passageways When we fi rst crank the engine, there’s machined into the crankcase halves to con- Figure 3—Hydrodynamic lubrication depends on adequate oil pressure no oil pressure and the crankshaft cranking duct oil to key components such as main and journal rotation speed. If those aren’t present (as at engine startup speed is pathetically slow. The conditions bearings and hydraulic lifters. Oil passages in and shutdown), the parts must depend on boundary lubrication. www.eaa.org 27 226-30_savvyMAR.indd6-30_savvyMAR.indd 2727 22/12/14/12/14 33:26:26 PPMM each main bearing saddle connect to the that strength under high heat. It also galleries. (See Figure 4.) Each main bearing needs to be resistant to corrosive attack by shell has an oil supply hole that lines up moisture and acids. Yet another key prop- with the oil passage in the saddle. erty is called “embeddability” and means Getting oil to the crankpin bearings in the that the bearing’s running surface is soft big ends of the connecting rods is a bit trick- enough to allow small particles of dirt, ier. The crankshaft is machined with diagonal metal, or other foreign material to become passages to conduct oil from the main bear- embedded in the bearing so it doesn’t ings to the crankpin journals. (See Figure 5.) scratch the crankshaft journal or jam the Oil pumped into the main and rod bear- tiny oil clearance zone between the jour- ings is extruded from the edges of the nal and the bearing. (See Figure 6.) bearings and returns to the engine’s oil Most bearings in piston aircraft engines sump or tank. The rapidly rotating crank- have a running surface made of a family of shaft fl ings this oil in all directions, fi lling alloys known as “babbitt” or “white metal” the crankcase with a dense oil mist that pro- that are about 90 percent tin combined vides “splash lubrication” to other engine with small quantities of antimony and cop- components like the cam lobes, lifter faces, per. (The term “babbitt” derives from Isaac piston pin bushings, and cylinder barrels. Babbitt, who invented the original version of this bearing alloy in 1839 in Taunton, MATERIAL PROPERTIES Massachusetts.) Babbitt off ers exceptional Plain bearings must have a running sur- slipperiness and embeddability, but its face that will slide against steel journals fatigue resistance and temperature strength with low friction and be highly resistant to deteriorate rapidly if more than a few thou- galling (i.e., adhering). Because the bear- sandths of an inch thick. ing is exposed to high cyclic loads and high temperatures, its running surface TRIMETAL BEARINGS must have good fatigue strength and retain Consequently, most piston aircraft engine bearings use a layered construction referred to as “trimetal,” although they actually have four or fi ve layers. (See Figure 7.) The bearing shell starts out with a semi- circular steel backing, to which is bonded an intermediate layer of copper/lead alloy designed to provide the necessary cushion- ing, fatigue strength, and temperature conduction. A thin overlay of babbitt is then electroplated over the intermediate layer in order to provide the required surface prop- Figure 4—Oil supply passages (yellow arrows) in each main erties (slipperiness, embeddability, bearing saddle in the crankcase provide a fl ow of pressurized corrosion-resistance). A micro-thin layer of oil to the main bearings. nickel is deposited between the intermedi- ate layer and overlay in order to prevent tin from migrating from the babbitt into the copper/lead alloy. Sometimes, another micro-thin layer of pure tin is deposited on top of the babbitt overlay to protect it from corrosion prior to installation in the engine. It can be useful to think of the construc- tion of a trimetal bearing as being like a Figure 5—The crankshaft is machined with diagonal oil pas- bed: The steel backing is like the box spring sages to conduct oil from the main bearings to the crankpin (providing support), the intermediate layer journals in order to lubricate the big-end rod bearings. is like the mattress (providing cushioning), 28 Sport Aviation March 2014 PHOTOGRAPHY COURTESY OF MIKE BUSCH 226-30_savvyMAR.indd6-30_savvyMAR.indd 2828 22/12/14/12/14 33:26:26 PPMM Figure 6—“Embeddability” means the ability of a bearing’s running surface to capture particles of dirt, metal, or other foreign materials.
Details
-
File Typepdf
-
Upload Time-
-
Content LanguagesEnglish
-
Upload UserAnonymous/Not logged-in
-
File Pages5 Page
-
File Size-