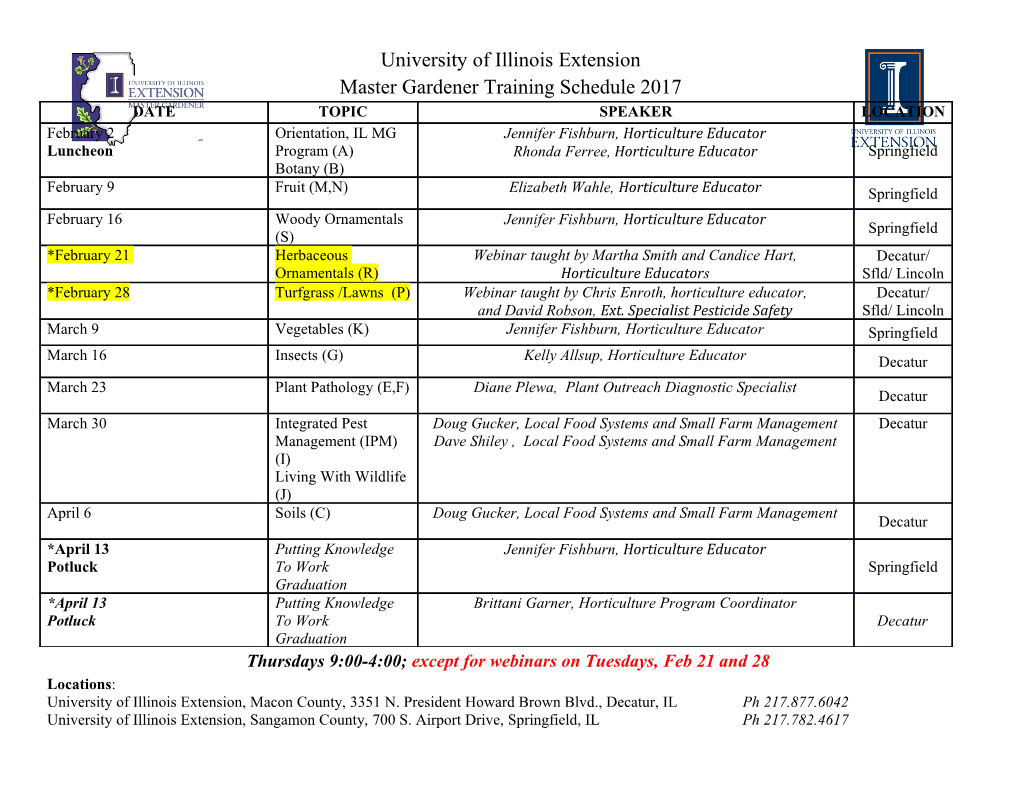
Prototype of magnetic resolver with Hall effect sensors by Marta Arbas Cantero Submitted to the Department of Electrical Engineering, Electronics, Computers and Systems in partial fulfillment of the requirements for the degree of Electrical Energy Conversion and Power Systems MASTER DEGREE at the UNIVERSIDAD DE OVIEDO July 2020 c Universidad de Oviedo 2020. All rights reserved. Author.............................................................. Certified by. David D´ıazReigosa Associate Professor Thesis Supervisor Certified by. Daniel Fern´andezAlonso Assistant Professor Thesis Supervisor 2 Prototype of magnetic resolver with Hall effect sensors by Marta Arbas Cantero Submitted to the Department of Electrical Engineering, Electronics, Computers and Systems on July 22, 2020, in partial fulfillment of the requirements for the degree of Electrical Energy Conversion and Power Systems MASTER DEGREE Abstract The position sensors play a crucial role in the control of electric machines as they provide position feedback. In addition, in recent years the attention over them has grown due to the deployment of the electric vehicles. It is well known that there are two types of position sensors which are more widely used than others: the optical encoder and the resolver (brushless or variable reluctance). The optical encoders could provide incremental or absolute position with high accuracy. However, they have a limited range of operation temperature and low withstand of shocks and vibrations compared to the resolvers. On the other hand, the resolvers inherently provide absolute position. They also properly withstand both thermal and vibration shocks. However, the accuracy of the resolver is lower than the optical encoder one as the latter generates less noise and it does not require an ADC converter at its output. Nevertheless, these types of sensors have the same drawback: their price. There- fore, for overcoming this disadvantage, during this Master Thesis it will be developed a prototype of magnetic resolver with Hall effect sensors. The cost reduction is caused by the fact that it does not require stator/rotor lamination or winding. Moreover, this design will maintain the resolver's properties, it will be electronically compatible with them and it can also be mounted directly on the electric motor without the need of a coupling device. Thesis Supervisor: David D´ıazReigosa Title: Associate Professor Thesis Supervisor: Daniel Fern´andez Alonso Title: Assistant Professor 3 4 Acknowledgments I would like to thank the AECP research group of the University of Oviedo, and its supervisor Fernando Briz, for offering me the opportunity to participate in this project. I would like to specially express my gratitude to my advisors Daniel and David for always being available and to Ye-gu for his help offered and his interest during the whole development of this MTh. 5 6 Contents 1 Introduction and objectives of this Master Thesis 17 2 State of the art 19 2.1 Introduction . 19 2.2 Position sensors . 19 2.3 Synchro . 21 2.3.1 Transmitter . 22 2.3.2 Receiver . 23 2.3.3 Differential . 24 2.3.4 Control transformer . 25 2.3.5 Transolver . 26 2.3.6 Differential resolver . 27 2.3.7 Resolvers . 27 2.3.8 Linear transformer . 27 2.3.9 Brushless synchros . 27 2.4 Tacho dynamo . 30 2.4.1 DC tachometer generator . 30 2.4.2 AC tachometer generator . 31 2.5 Resolvers . 31 2.5.1 Resolver operation principle . 32 2.5.2 Brushless wound field resolvers . 34 2.5.3 Variable reluctance resolvers . 35 2.6 Encoders . 36 7 2.6.1 Classification according to the way the position is established 36 2.6.2 Classification according to the way the pulses are generated . 38 2.7 Comparison between position sensors . 43 3 Magnetic resolver using Hall-Effect Sensors 45 3.1 Introduction . 45 3.2 Magnetic resolver architecture . 46 3.2.1 Hall-effect sensors . 46 3.3 Principle of operation . 48 3.3.1 Design optimization . 50 3.3.2 Design optimization software . 57 4 Mechanical assembly of the magnetic resolver using Hall effect sen- sors 65 4.1 Introduction . 65 4.2 Mechanical assembly . 65 4.2.1 Shaft-type resolver model . 66 4.2.2 In-shaft resolver mounted model . 67 4.3 PCB . 68 4.3.1 Mechanical model . 69 4.3.2 Electrical model . 70 4.4 PCB simulation . 76 4.4.1 PCB without voltage divider . 76 4.4.2 PCB with voltage divider . 77 5 Demodulation techniques 79 5.1 Introduction . 79 5.2 Amplitude demodulation techniques . 79 5.2.1 Diode rectifier envelope detector . 80 5.2.2 Product detector . 81 5.2.3 Synchronous detection . 84 8 5.3 Demodulation techniques simulation . 85 5.3.1 Diode rectifier envelope detector without low-pass filter . 88 5.3.2 Product detector . 95 5.3.3 Comparison between both methods . 95 6 Electric motor position measurement 99 6.1 Introduction . 99 6.2 Techniques for determining the position of the electric motor . 99 6.2.1 Arctangent calculation . 100 6.2.2 Phase-locked loop (PLL) . 100 6.3 Simulation of both 'Product detector' demodulation technique and PLL103 6.3.1 Microcontroller implementation . 105 6.3.2 Comparison between the magnetic resolver error and that of the commercial encoders and resolvers . 106 7 Conclusions 109 8 Future developments 111 A Drawing plan: Shaft-type model 113 B Drawing plan: In-shaft mounted model 119 C Drawing plan: PCB schematic and views without voltage divider 123 D Drawing plan: PCB schematic and views with voltage divider 127 9 10 List of Figures 2-1 Position closed-loop feedback [3]. 20 2-2 Synchro transmitter [8]. 22 2-3 Back-to-back transmitter and receiver connection [7]. 23 2-4 Differential connection with the transmitter and the receiver [7]. 24 2-5 Differential connection with two transmitters [7]. 25 2-6 Transmitter and control transformer connection [7]. 25 2-7 Transmitter and control transformer control [7]. 26 2-8 Schematic view of the brushless synchro design [9]. 29 2-9 DC tachometer generator [10]. 31 2-10 AC tachometer generator [10]. 31 2-11 Resolver operation principle. 33 2-12 Brushless wound field resolver scheme [17]. 34 2-13 Variable reluctance resolver scheme [19]. 35 2-14 Variable reluctance resolver scheme 3D [19]. 35 2-15 Incremental encoder output [23]. 37 2-16 Absolute encoder output [23]. 37 2-17 Optical encoder scheme [24]. 38 2-18 Magnetic encoder scheme[25]. 40 2-19 Capacitive encoder simplification [26]. 41 2-20 Capacitive encoder scheme [24]. 41 2-21 Inductive encoder scheme[26]. 42 3-1 Schematic representation of the proposed magnetic resolver. 46 11 3-2 Operating principle of the Hall-effect sensor[31]. 47 3-3 Input and output voltages of the proposed magnetic resolver. !ex = 2 · π · 500 rad/s. !r = 2 · π · 50 rad/s. 50 3-4 Interior permanent magnet rotor. 51 3-5 Dimensions of the magnetic resolver prototype [30]. 52 3-6 Magnetic resolver geometry in FEMM. 60 3-7 Flux amplitude calculation in FEMM. 62 3-8 Resolver performance. 63 4-1 Complete exploded view: Shaft-type. 66 4-2 Complete exploded view: In-shaft. 67 4-3 3D total model assembled. 68 4-4 PCB mechanical scheme. 69 4-5 Electronic circuit scheme of the PCB. 74 4-6 Electronic scheme of the PCB with adaptation. 75 4-7 Inputs to the PCB. 76 4-8 PCB outputs: Without voltage divider. 77 4-9 Vcc+ and Vcc- for supplying the instrumentation amplifiers. 77 4-10 Voltage used for power the Hall effect sensors HG0815. 78 4-11 PCB outputs: With voltage divider. 78 5-1 Output signal of each Hall effect sensor: The original signal is shown in blue and the demodulated one in red. 80 5-2 Diode rectifier envelope detector [44]. 81 5-3 Synchronous demodulation: SIN Hall effect sensor. 83 5-4 Torque disturbance introduced into the asynchronous electric machine. 86 5-5 Rotor speed and rotor position when the input to the asynchronous machine is the torque shown in Fig. 5-4. 87 5-6 Excitation voltage and AM output signals of the magnetic resolver. 88 5-7 Circuit diagram of the 'Diode rectifier envelope detector without low- pass filter’ method. 88 12 5-8 Description of the elements in Fig. 5-7 [47]. 89 5-9 Comparators [Zoom 0.487-0.5075 sec.]: a) Vex and φC1, b) VHS and φC3 and c) VHC and φC2.......................... 90 5-10 First part of the control signal generator [Zoom 0.487-0.49 sec.]: a)φC1, b)φJK , c)φ1 and d) φ2........................... 91 5-11 Second part of the control signal generator [Zoom 0.487-0.537 sec.]: a)φC1, b)φ3, c)φC2 and d) φ4....................... 91 5-12 SIN full wave rectifier [Zoom 0.487-0.58 sec.]: a)VHS and b)jVHSj... 92 5-13 Amplitude detection [Zoom 0.487-0.4974 sec.]: a)VHS, b)φ1, c)Va1, d) φ2 and e)VA1................................ 93 5-14 ± unity gain amplifier [Zoom 0.487-0.58 sec.]: a)VA1, b)φ3 and c)VS.. 94 5-15 Demodulated signals achieved with the method 'Diode rectifier enve- lope detector without low-pass filter’. 94 5-16 Demodulated signals achieved with the method 'Product detector'. 95 5-17 Comparison of the demulation techniques simulated. '1' is the 'Diode rectifier envelope detector without low-pass filter’ method and '2' is the 'Product detector' one. a)SIN Hall effect sensor and b)COSINE Hall effect sensor. 96 6-1 Basic structure of a PLL [51]. 100 6-2 PLL for phase detection with the LF on the q-axis of the QSG [51]..
Details
-
File Typepdf
-
Upload Time-
-
Content LanguagesEnglish
-
Upload UserAnonymous/Not logged-in
-
File Pages135 Page
-
File Size-