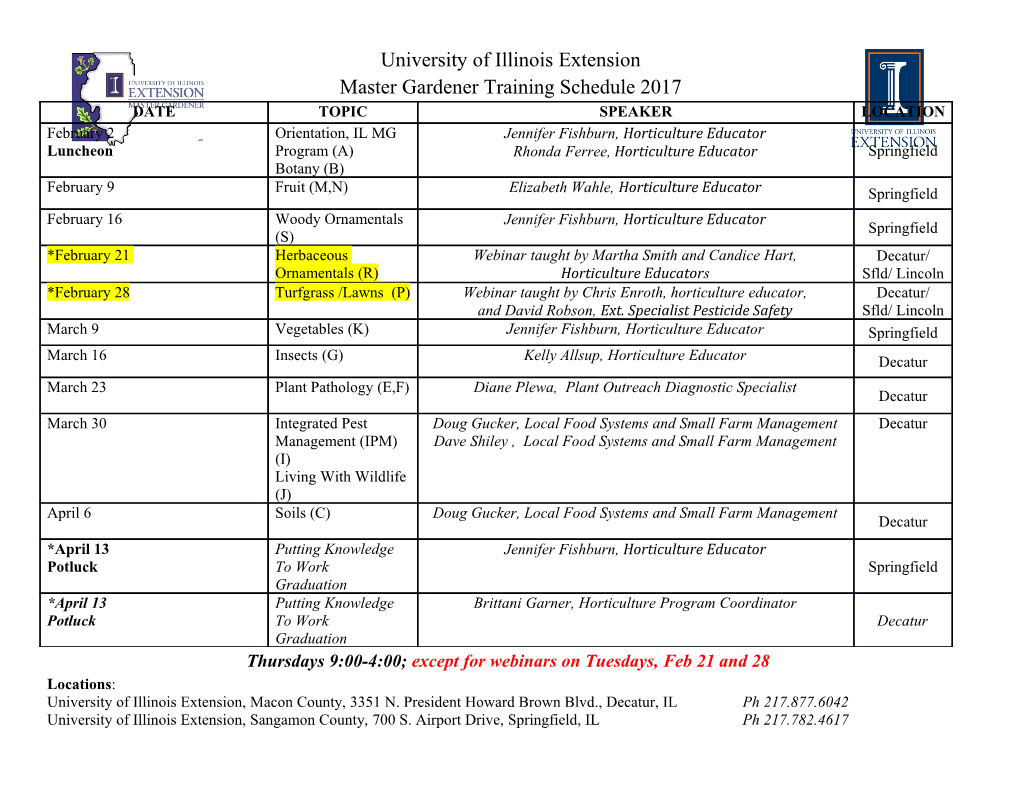
Novel Design and Optimization ofVehicle's Natural Gas Fuel Tank A Thesis Presented to The Faculty ofthe Fritz J. and Dolores H. Russ College ofEngineering and Technology Ohio University In Partial Fulfillment ofthe Requirement for the Degree Master ofScience \ by , Shr-Hung Chen March 1997 QHIO UN!VERSlrv LIBRARY Acknowledgments I would like to thank my advisor, Dr. Bhavin V. Mehta, Assistant Professor of Mechanical Engineering, for having given me the privilege of working on this problem. Working on this thesis has been an invaluable experience and has greatly contributed to my knowledge and understanding ofthe subject. I would also like to thank Dr. M. Khairul Alam, Professor of Mechanical Engineering and Dr. Daniel Gulino, Associate Professor of Chemical Engineering of being on my thesis committee. I dedicate this thesis to my parents who have been my source inspiration In pursuing my Master's degree. A special word ofthanks to my sister for her support. Table of Contents Topic Page List ofTable III List ofFigure IV 1. Introduction 1 1-1 Introduction 1 1-2 Objective 1 1-3 Natural Gas Vehicles and High Pressure Storage Tanks 2 2. Literature Review 4 2-1 Natural Gas Vehicle 4 2-2 The Shape ofNatural Gas Storage Tanks 5 2-3 The Materials ofCompress Natural Gas Storage Tanks 6 3. Materials Consideration ofNatural Gas Storage Tanks 9 3-1 Introduction 9 3-2 Different Materials Considered 9 3-3 Aluminum-6061-T6 10 3-4 Steel-AISI-I040 16 3-5 Composite Material (Kevlar) 19 4. FEM Modeling and Design ofNatural Gas Storage Tanks 24 4-1 Introduction 24 ii Topic Page 4-2 Creation of3-D Model ofthe Tank Using Intergraph's CAD/CAM System 24 4-3 Creation of3-D Model ofTank Using Patran3.0 36 5. Theory and FEM Analysis ofCylindrical Tank 38 5-1 Introduction 38 5-2 The Mathematical Model ofA Cylindrical Tank 38 5-2-1 Thin-Walled Cylindrical Pressure Vessels 38 5-2-2 Thick-Walled Cylindrical Pressure Vessels 41 5-3 FEM Analysis ofCylindrical Pressure Vessels 47 5-4 The Comparison ofTheoretic and FEM Analysis Result 52 6. FEM Analysis ofNoncylindrical Tanks and Optimization 55 6-1 Introduction 55 6-2 FEM Analysis ofNon-Cylindrical Model Considering 2 Materials 55 6-3 FEM Analysis Considering Kevlar Composite Material 70 . 6-4 Optimization 75 7. Conclusion and Discussion 79 7-1 Conclusion 79 7-2 Future Work and Recommendations 82 8. Bibliography 83 111 List ofTables Table Title Page 3-1 Mechanical Properties ofMaterials 12 3-2 Designation system for aluminum alloys 13 3-3 Temper designation for alloys 14 3-4 The properties ofAluminum-6061-T6 15 3-5 SAE-AISI plain carbon steels 18 3-6 Properties ofKevlar Composite Material 22 4-1 3-D Modeling 26 4-2 The Dimensions Used in 3-D Modeling 27 5-1 The equation for the generalized Hook's Law 45 6-1 The Nodes and Tetrahedral Elements ofFinite Element Mesh 57 6-2 The Constrained Area 58 6-3 Model Versus Internal Pressure 59 6-4 The Maximum Stress Development with I/FEM and Patran3.0 System 78 7-1 The Density and Yield Stress ofMaterials 81 iv List ofFigures Figures Title Page 3-1 Comparison ofthe Yield Strength 20 3-2 The Structure ofKevlar 23 4-1 Square Shape 28 4-2 Cylindrical Shape 29 4-3 Cylindrical Shape with Two Hemispheric Ends 30 4-4 Square Shape with 4 Fins 31 4-5 Rounding Edge Square with 4 Fins 32 4-6 Rounding Square with 4 Fins and Hole Opening on Fins (Thickness ofthe Wall is 0.5 in) 33 4-7 Rounding Square with 4 Fins and Hole Opening on Fins (Thickness ofthe Wall is 0.7 in) 34 4-8 Rounding Square with 4 Fins and Hole Opening on Fins (Thickness ofthe Wall is 1.0 in) 35 4-9 The Patran3.0 Finite Element Modeling (Thickness ofthe Wall is 1 in) 37 5-1 Diagrams for analysis ofthin-walled cylindrical pressure vessels 40 5-2 Diagrams for analysis ofthin-walled cylindrical pressure vessels 40 v Figures Title Page 5-3 Diagrams for analysis ofthin-walled cylindrical pressure vessels 41 5-4 Diagrams for analysis ofthick-walled cylindrical pressure vessels 43 5-5 Diagrams for analysis ofthick-walled cylindrical pressure vessels 43 5-6 The Constrained Area ofCylindrical Pressure Vessel 49 5-7 The Distribution ofStresses ofAluminum-6061-T6 Material Model 50 5-8 The Distribution ofStresses of Steel-AISI-I040 Material Model 51 6-1 The Distribution ofStresses ofAluminum-6061-T6 Material Model (Shape 1) 60 6-2 The Distribution ofStresses ofAluminum-6061-T6 Material Model (Shape 3) 61 6-3 The Distribution ofStresses ofAluminum-6061-T6 Material Model (Shape 4) 62 6-4 The Distribution of Stresses ofAluminum-6061-T6 Material Model (Shape 5) 63 6-5 The Distribution ofStresses ofAluminum-6061-T6 Material Model (Shape 6) 64 VI Figures Title Page 6-6 The Distribution of Stresses ofSteel-AISI-I040 Material Model (Shape I) 65 6-7 The Distribution of Stresses ofSteel-AISI-I040 Material Model (Shape 3) 66 6-8 The Distribution ofStresses ofSteel-AISI-I040 Material Model (Shape 6) 67 6-9 The Distribution ofStresses ofSteel-AISI-I040 Material Model (Shape 7) 67 6-10 The Distribution ofStresses ofSteel-AISI-I040 Material Model (Shape 8) 68 6-11 The Distribution ofStresses ofSteel-AISI-I040 Material Model under Patran3.0 Analysis (Shape 8) 72 6-12 The Model ofLaminate Material 73 6-13 The Distribution ofStresses ofKevlar Composite and Steel- AISI-I040 Material Model under Patran3.0 Analysis (Shape 8) 74 6-14 The Gasoline Tank ofA Ford Escort 77 CHAPTERl Introduction 1-1 Introduction The price of petroleum has become increasingly more expensive since the early 1970s. To fmd a new motor fuel for automobile use is an important challenge; natural gas is one of the most prospective of these fuels. Compared with gasoline, it is inexpensive and less polluting. Although some automobiles now run on compressed natural gas, storing sufficient gaseous fuel to accommodate the needs ofthe car is still a major problem. For a natural gas vehicle to travel as far as a gasoline vehicle (between 250 miles and 300 miles) without refueling, it must carry a very heavy high pressure natural gas storage. Many high-pressure tanks that meet the 300-mile distance requirements take up a lot of space and add weight to the vehicle. That is, few vehicles, such as mid-to-full-size pickup trucks, vans and heavy-duty vehicles, are large enough to provide sufficient storage space to install this equipment. Thus, developing a lighter tank which can store more high pressure natural gas is essential for natural gas vehicle's commercial success. 1-2 Objective The objective of this research is to use I1FEM and Patran3.0 software to analyze eight shapes and three materials (Aluminum-6061-T6, Steel-AISI-I040 and Laminate Composite material). The maximal stresses of these shapes and materials will be 2 compared to help fmd the best model and material for a compressed natural gas storage tank which can store at higher natural gas pressure. Chapter 1 is an introduction to natural gas vehicles and the rationale for their development. Chapter 2 is an overview of the literature pertaining to natural gas vehicles and high pressure storage tanks. Chapter 3 evaluates materials used in natural gas storage tanks, the choices of three materials (Aluminum-6061-T6, Steel-AISI-I040 and laminate composite material), and discusses the properties ofthese materials. Chapter 4 examines the designs of several models of high pressure vessels. Intergraph's Engineering Modeling System (I/EMS) and MSC's Patran3.0 are used to develop 3-D fmite element models ofhigh pressure vessels. Chapter 5 presents the mathematical models and results of the finite element analysis of a cylindrical vessel, and compares theoretical and fmite element analysis result. Chapter 6 describes the fmite element analysis of non-cylindrical vessel models that were created by IIFEM and Patran3.0, and discusses optimization of natural gas storage tank models. Chapter 7 presents conclusions and offers directions for future research. 1-3 Natural Gas Vehicles and High Pressure Storage Tanks Natural gas is a widely available, inexpensive, efficient and clean burning fuel. When used in automobile propulsion, natural gas is cheaper than the per gallon equivalent 3 of gasoline. Including compression costs, natural gas can be 25 percent to 50 percent cheaper than gasoline and costs as much as 50 percent less than such alternative fuels as methanol. Natural gas bums cleaner than most alternative fuels. It produces only low levels ofpollutants, such as reactive organic gases, nitrogen oxide (NOx) and carbon monoxide (CO), and produces virtually no particulates. Highly efficient, natural gas provides high engine thermal efficiency. Engine power can be increased by 40 percent with natural gas. The fuel tank used by natural gas vehicle (GNV) is a high pressure storage tank. In general, natural gas storage tank pressure is rated at 3000-psi to SOOO-psi. Tanks are most frequently composed of Steel-AISI-I040 or Aluminum-6061-T6. The purpose of this research is to find an optimal material and shape for storing high pressure natural gas. 4 CHAPTER 2 Literature Review 2-1 Natural Gas Vehicles Many studies have been conducted on natural gas vehicles. Research has most frequently focused on the efficiency, pollution and economics ofnatural gas vehicles. In addition to investigating the advantages of natural gas vehicles, some university or research organizations have modified engine designs to improve the efficiency ofnatural gas vehicles. Ecole Polytechnique de Montreal [1] has modified the design of a 364-ci engine with 12.7:1 compression ratio.
Details
-
File Typepdf
-
Upload Time-
-
Content LanguagesEnglish
-
Upload UserAnonymous/Not logged-in
-
File Pages92 Page
-
File Size-