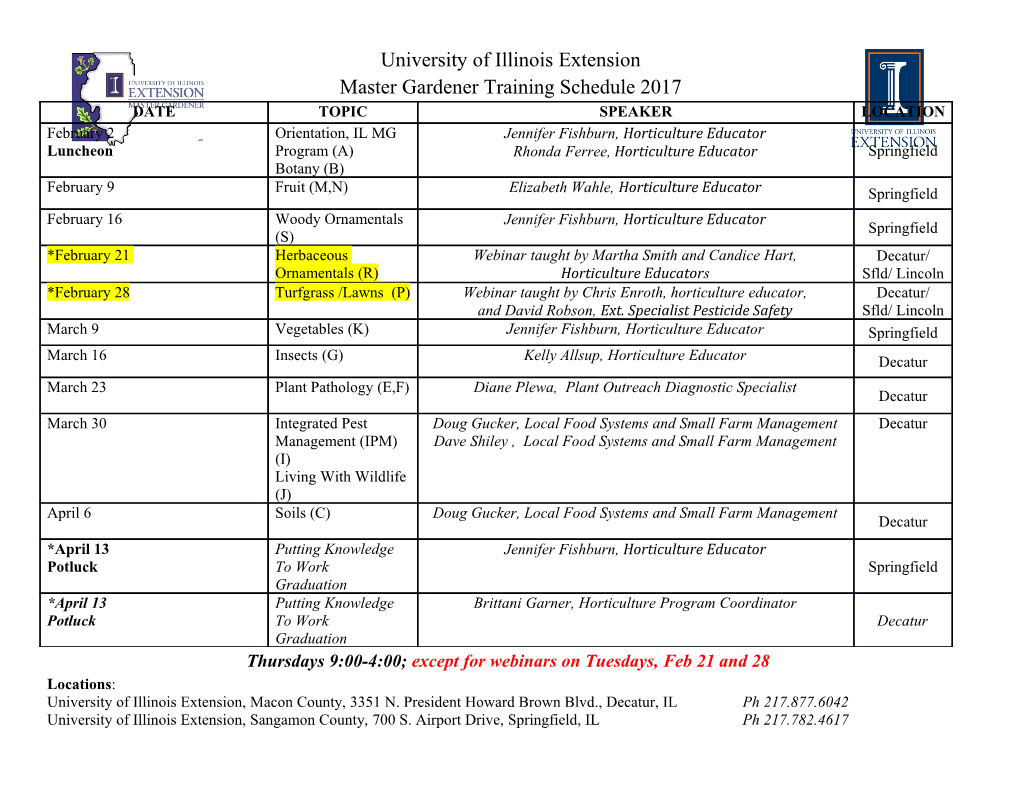
Fleet Management Good Practice Guide – 20 Point Plan Issue 14 – January 2019 AMENDMENT RECORD Issue Dated Notes Section 2: MP code removed from Technical incident reasons 14 December 2018 table “701D” 14 December 2018 Inclusion of new Section 10: Managing Ageing Rolling Stock 14 December 2018 Sections new cover inserted 14 December 2018 General document sections restructure 14 December 2018 Gary Cooper’s foreword updated Fleet Management Good Practice Guide: Issue 14 - January 2019 ii Foreword Our customers’ needs have been consistent ever since the birth of the railway, whether they are passengers, or businesses that send freight by rail, and the message is simply: run my train on time. Meeting this need is a priority for all of us in rail, and the desire for on-time service delivery shows in the correlation between punctuality and customer satisfaction and, in turn, the correlation between customer satisfaction and rail businesses’ revenues. It is important therefore, for the industry and the country as well as customers that we run punctual trains. We have been failing to do this for too long. After improving performance every month from 2002 – 2011, we now repeatedly miss the punctuality levels that TOCs and NR Routes agree they will deliver. The reliability of the vehicles we operate is part of that under-delivery and we have to do better. In 2013, the fleet planned a national passenger fleet performance challenge of delivering 11 500 MTIN by March 2019, a 20% improvement in reliability over this five- year control period. The reality is that we are likely to deliver only 9 000 MTIN by then. The industry’s National Task Force (NTF) brings together TOCs, Network Rail, the DfT and the ORR with the purpose of agreeing and then delivering levels of punctuality that meet or exceed customers’ needs. At the time of writing, technical fleet failures cause 18% of all industry delays. With close to 7 000 new vehicles planned to come into service in the next three years we have to manage the risks to performance of their in-service introductions as well as continue to improve current fleet reliabilities if we are to reap the reputational benefit, and thereby financial rewards, for our businesses, customers and GB, on which their procurement is predicated. The 20 Point Plan is our practitioner-created guide to help businesses deliver improvements in their rolling stock performance through willingly sharing hard-earned knowledge. The continued evolution of the plan is a visible demonstration of the will that differing businesses have in collaborating to meet the challenge of providing reliable punctual journeys for customers, be they passengers or those consigning freight by rail. Its authority comes from the fact that what is shared is things that practitioners and experts have found to work in practice. Focusing on: improving entry into service reliability quickly, reducing technical events that cause delay, and using diagnostics to recover from failure faster are all necessary to meet customers’ needs on our increasingly busy railway. We face a bigger challenge than was posed by replacing Mk 1 fleets in the first years of the National Fleet Reliability Improvement Plan – but together that challenge was met. We need to meet this new challenge and ensure that fleet reliability improves through the period 2019-24. Gary Cooper Director, RDG Planning, Engineering and Operations Fleet Management Good Practice Guide: Issue 14 - January 2019 iii Meeting the Challenge The Fleet Reliability Focus Forum (ReFocus) was introduced by the Engineering Council in November 2010 and tasked with identifying best practice and sharing knowledge amongst rail industry partners such as TOCs, OEMs, RoSCos, Network Rail and others. This forum has made a very valuable contribution to fleet delivery over this time and continues to provide an evolutional good practice guide to support the industry. ReFocus captures knowledge through peer groups who are experts and this knowledge is then incorporated in the Fleet Management Good Practice Guide. ReFocus has developed new sections of the Guide and revised existing sections. Sharing knowledge and best practice ultimately allows TOCs and their partners to deliver a reliable and punctual service. However, the railway still faces many challenges. With the increase in demand and society’s expectations constantly evolving, it is attracting more and more customers and businesses. This creates significant challenges, with historic methods of delivering continuous improvement only able to provide marginal benefits. A more holistic view, covering not only the technical aspects but also the people and the culture, will need to be explored and set out in the Guide. This includes integrating new technology, data, people and processes to allow for more trains to run on an increasingly busy network. ReFocus has made real progress in tackling some of these problems by working with industry partners and not just on a fleet-centric basis. This allows us to comprehensively examine generic railway issues by working with operational colleagues and Network Rail, as well as other industry partners such as the OEMs and the RoSCos. This collaborative approach has enabled us to update the Fleet Management Good Practice Guide to reflect today’s thinking. ReFocus also takes a holistic view of society and cultural challenges in order to drive change. It looks at technology and innovations that allow new processes and practices to be developed and addresses the gaps where clear value can be added. This knowledge is used to inform other industry strategy groups, such as Fleet Challenge and RDG’s Supply Chain Forum, of gaps and shortfalls which may need addressing now or in the near future. Other industries face similar challenges to the railway with ever-increasing demand from users and the constant need to move forward and deliver a reliable and safe service. Benchmarking with other industries gives members opportunities to transfer knowledge and incorporate it within their own business. Mark Johnson Fleet Reliability Focus Forum Chairman Engineering Director, Southeastern Railway Fleet Management Good Practice Guide: Issue 14 - January 2019 iv Contents 1. Summary .......................................................................................................... viii 2. Common Reliability Data ...................................................................................... 2 3 Management for Improvement .......................................................................... 11 4 Seasonal Management ....................................................................................... 20 5. Train Preparation ............................................................................................... 32 6. Delivering the Service ........................................................................................ 38 7 The Depot .......................................................................................................... 45 8 On-Depot Fault Finding ...................................................................................... 53 9 The Vehicles ...................................................................................................... 62 10 Managing Ageing Rolling Stock ........................................................................... 71 11 The Infrastructure .............................................................................................. 83 12 Managing the Impact of Fleet Incidents on the Railway ....................................... 89 13 The Supply Chain ............................................................................................. 100 14 New Train Introduction .................................................................................... 107 15 No Fault Found Warranty Claims ...................................................................... 121 16 ROSCOs ........................................................................................................... 128 17 Overhaul Management .................................................................................... 141 18 Outsourced Maintenance ................................................................................. 155 19 Business Continuity Management .................................................................... 162 20 Useful Links ..................................................................................................... 168 Appendix A - Evidence Flow Chart ................................................................................ 170 Appendix B – High-Performing Depot Specification ....................................................... 171 Fleet Management Good Practice Guide: Issue 14 - January 2019 v Appendix C - Supply Chain Sub-Group Issues List ........................................................... 176 Appendix D –Industry Supply Chain Workstreams ......................................................... 179 Appendix E – Examples of Best Practice Supply Chain Management .............................. 184 Appendix F - Fleet Transfer Checklist ............................................................................ 187 Appendix G - Incident Decision Support Tool Customer Requirement Specification ........ 192 Appendix H – Example of a Checklist ............................................................................ 195 Appendix I - Decision Support Tools .............................................................................
Details
-
File Typepdf
-
Upload Time-
-
Content LanguagesEnglish
-
Upload UserAnonymous/Not logged-in
-
File Pages215 Page
-
File Size-