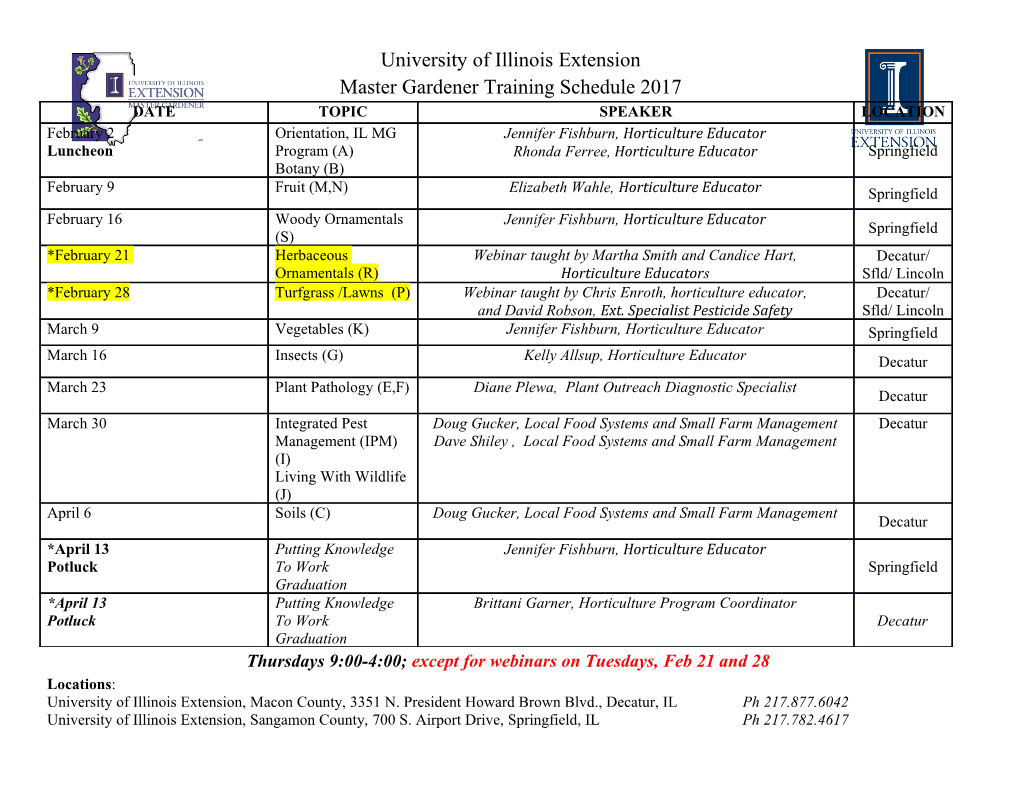
<p>Model Predictive Control</p><p>• Model Predictive Control (MPC) – regulatory controls that use an explicit dynamic model of the response of process variables to changes in manipulated variables to calculate control “moves”. • Control moves are intended to force the process variables to follow a pre- specified trajectory from the current operating point to the target. • Base control action on current measurements and future predictions.</p><p>Figure: Two processes exhibiting unusual dynamic behavior. (a) change in base level due to a step change in feed rate to a distillation column. (b) steam temperature change due to switching on soot blower in a boiler.</p><p>DMC – dynamic matrix control became MPC – model predictive control</p><p>• Optimal controller is based on minimizing error from set point • Basic version uses linear model, but there are many possible models • Corrections for unmeasured disturbances, model errors are included • Single step and multi-step versions • Treats multivariable control, feedforward control</p><p>When Should Predictive Control be Used?</p><p>1. Processes are difficult to control with standard PID algorithm – long time constants, substantial time delays, inverse response, etc. 2. There is substantial dynamic interaction among controls, i.e., more than one manipulated variable has a significant effect on an important process variable. 3. Constraints (limits) on process variables and manipulated variables are important for normal control.</p><p>Model Predictive Control Originated in 1980s</p><p>• Techniques developed by industry: 1. Dynamic Matrix Control (DMC) - Shell Development Co., Cutler and Ramaker (1980), - Cutler later formed DMC, Inc. - DMC acquired by Aspentech in 1997. 2. Model Algorithmic Control (MAC) • ADERSA/GERBIOS, Richalet et al (1978) • Over 4000 applications of MPC since 1980 (Qin and Badgwell, 1998 and 2003).</p><p>Model Predictive Control Based on Discrete-time Models</p><p>• Time-delay compensation techniques predict process output one time delay ahead. • Here we are concerned with predictive control techniques that predict the process output over a longer time horizon. (e.g., open-loop response time).</p><p>Figure 20.2 Basic concept for Model Predictive Control General Characteristics • Targets (set points) selected by real-time optimization software based on current operating and economic conditions • Minimize square of deviations between predicted future outputs and specific reference trajectory to new targets • Discrete step response model • Framework handles multiple input, multiple output (MIMO) control problems. • Can include equality and inequality constraints on controlled and manipulated variables • Solves a quadratic programming problem at each sampling instant • Disturbance is estimated by comparing the actual controlled variable with the model prediction • Usually implements the first move out of M calculated moves</p><p>Discrete Step Response Models</p><p>Consider a single input, single output process:</p><p>Where u and y are deviation variables (i.e. deviations from nominal steady-state values).</p><p>Denote the sampled values as y1, y2, y3, etc. and u1, u2, u3, etc. The incremental change in u will be denoted as</p><p>Duk = u k - u k -1</p><p>The response, y(t), to a unit step change in u at t = 0 (i.e., Δu0 = 1 is shown in Figure 7.14.</p><p>Figure 7.14 Unit Step Response</p><p>In Fig. 7.14, {Si} Astep response coefficients</p><p>{hi} Aimpulse response coefficients</p><p>Note: hi = Si – Si-1 y1 = y0 + S1Δu0 y2 = y0 + S2Δu0 (Δu0 = 1 for unit step change at t = 0). . . . . yn = y0 + SnΔu0</p><p>Alternatively, suppose that a step change of u occurred at t = t. Then, 1 y = y + S u 2 0 1 1 y = y + S u 3 0 2 1 . .</p><p>. . . . y = y + S u N 0 N-1 1</p><p>If step changes in u occur at both t = 0 (u ) and t = t (u ). 0 1 From the Principle of Superposition for linear systems:</p><p> y = y + S u 1 0 1 0 y = y + S u + S u 2 0 2 0 1 1 y = y + S u + S u 3 0 3 0 2 1 ...... y = y + S u + S u N 0 N 0 N-1 1</p><p>Can extend also to MIMO Systems</p><p>Figure 20.8. Individual step-response models for a distillation column with three inputs and four outputs. Each model represents the step response for 120 minutes. Reference: Hokanson and Gerstle (1992).</p><p>Selection of Design Parameters Model predictive control techniques include a number of design parameters: N: model horizon t: sampling period P: prediction horizon M: control horizon (number of control moves) Q: weighting matrix for predicted errors (Q > 0) R: weighting matrix for control moves (R > 0) Selection of Design Parameters (continued)</p><p>1. N and t These parameters should be selected so that N t > open-loop settling time. Typical values of N: 30 < N < 120</p><p>2. Prediction Horizon, P • Increasing P results in less aggressive control action Set P = N + M</p><p>3. Control Horizon, M • Increasing M makes the controller more aggressive and increases computational effort, typically 5 < M < 20</p><p>4. Weighting matrices Q and R • Diagonal matrices with largest elements corresponding to most important variables. </p>
Details
-
File Typepdf
-
Upload Time-
-
Content LanguagesEnglish
-
Upload UserAnonymous/Not logged-in
-
File Pages7 Page
-
File Size-