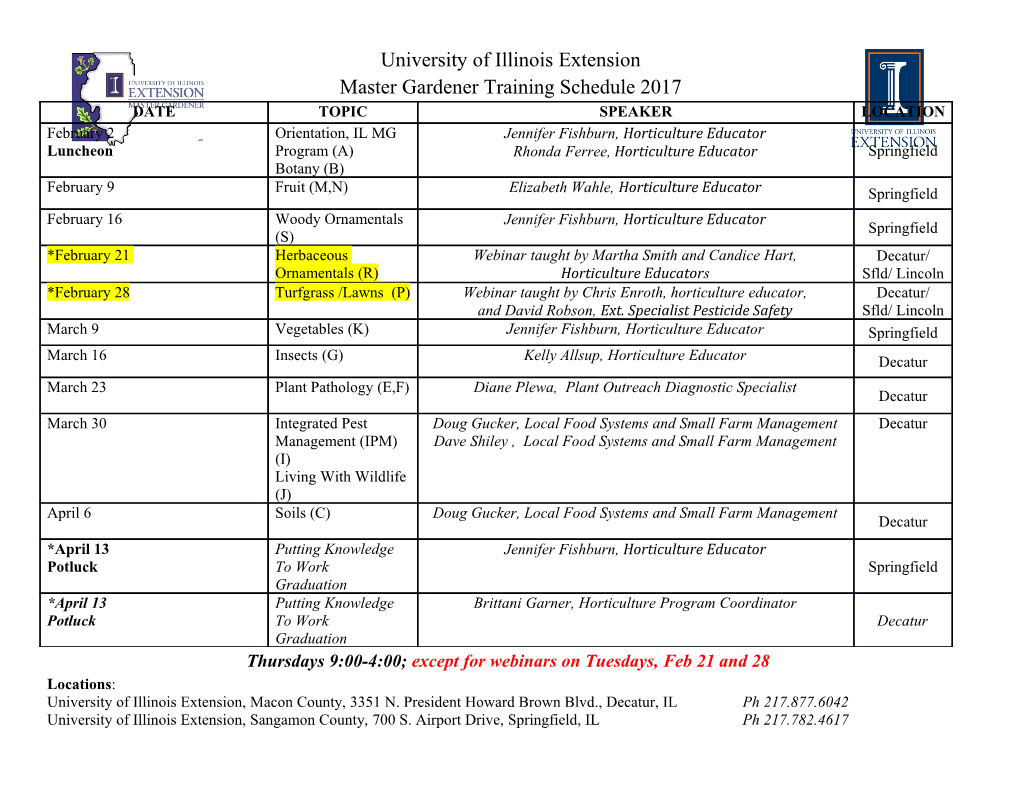
UNIT 7 SECTION VIEWS 7.1 Introduction A section view is an orthographic projection view drawn to reveal internal or hidden features in an object. Section views are used to supplement standard orthographic view drawings in order to completely describe an object. They improve visualization of designs, clarify multiviews and facilitate dimensioning of drawings. Hence they are an important aspect of design and documentation. Section views are created by defining an imaginary cutting plane or planes on the object so that the observer can see the internal details. Hidden lines are generally not shown in sections. Hatch lines (also called section lines) are used to indicate solid materials that are cut through. A combination of hatch lines is called a pattern. A hatch pattern has certain attributes such as orientation and line spacing. Some hatch pattern types are used to represent specific materials or group of materials. Both part and assembly sections can be created. Sometimes, auxiliary section views may be needed for clarity. 7.2 Concept of Sections In orthographic projection, the standard projection planes are top (horizontal), front (frontal), side (profile). The frontal and profile planes are vertical, while the top is horizontal. Standard drawing views are created on these planes with preferred view directions. The view direction for the frontal and profile planes is horizontal while the view direction for the horizontal plane is vertical. Fig. 7.1a shows the standard front and top views a cylinder. Fig. 7.1b shows the same cylinder in mixed (standard, section, cut isometric) views with the front view converted to a section view. Several elements associated with the concept of sections are indicated in Fig. 7.1b. These are i) cutting plane line, ii) view direction, iii) removed portion, iv) retained portion, v) hatching, and vi) section caption or label. The cutting plane is an imaginary plane that passes through the object at a position of interest. It is represented by a line (the edge view of the section plane) in an adjacent view to the section view. In Fig. 7.1b, the cutting plane is vertical since its edge view is seen on the horizontal plane. Cutting planes can change direction within an object. The view direction is the line of sight or the direction an imaginary viewer is facing. The view direction is indicated by the arrow head and is perpendicular to the cutting plane. In Fig. 7.1b, the view direction is horizontal. The removed portion is the portion of an object that is assumed to have been removed in order to expose the interior. It is the cut- out portion of the object. The viewer is able to directly see the interior of the object when the cut-out is removed. Top view Top view Section view Front view a) Standard views b) Mixed views Fig. 7.1: Concept of sections The retained portion is the portion of an object that is assumed to be left in front of the viewer. The hatching is the pattern of hatch lines used to indicate solid material. The section label is the name given to the section or cutting plane. A very important difference between standard and section views is the replacement of hidden lines in standard views with visible lines in section views. This is very fundamental since it indicates the feature is now visible in a section view. Comparing the standard and mixed views of Fig. 7.1 shows the clarity advantage of section views. Another advantage of section views is that the visible lines from hidden lines in standard views can be used for 1 dimensioning; hidden lines are not used for dimensioning. When parts or assemblies have complex internal features, hidden lines in standard views become confusing, sections are then indispensable. 7.3 Cutting Plane Linestyles A cutting plane is represented by a line that shows the edge view of the cutting plane. A limited number of linestyles are used to represent cutting planes. In Fig. 7.2, the common linestyles for cutting planes are shown. They are a) thick center line, b) thick phantom line and c) broken visible line. The representation in c) is used if the cutting plane line would hide important details in a drawing. Each of these lines is usually joined to two arrows at their ends. The direction of the arrow is the viewer’s line of sight. Cutting plane lines are drawn in the view adjacent to the section view and may go beyond the boundary of the adjacent view. The thickness of a cutting plane line should be more than that of normal visible line. a) Thick centerline b) Thick phantom line c) Broken visible line Fig. 7.2: Cutting plane linestyles 7.4 Hatch Patterns Hatch lines are thin lines and when they are laid out in a specific angle and spacing, a hatch pattern is formed. A hatch pattern is always within a closed boundary. If there is a gap in an section, hatching will not occur when using CAD systems. Spacing of hatch lines should enhance readability. Depending on the size of the drawing, it may be between 1.5 mm (0.06 in) to 6 mm (0.25 in) in relatively small drawings. Likewise, the inclination of hatch lines should be guided by clarity. The angle of inclination for hatch lines normally varies between 15 o and 75 o. Popular angles are 15 o, 30 o, 45 o, 60 o, and 75 o. The angle 45 o is the default angle in most CAD software. Hatch lines must not be drawn or placed parallel to object lines or features in a section. In Fig. 7.3, the left column views have hatch lines parallel to some object features and they are, therefore, unacceptable. The acceptable representations are shown in the right column views. The angle of inclination of the hatch lines must be different from the angles of inclination of all the features forming the boundary of a hatch pattern. Fig.7.4 shows some examples of assembly hatch patterns. When components are assembled, the hatch patterns must not be parallel to object lines or features of hatch boundary. Also, hatch lines are inclined at different angles in each component in order to distinguish them. Fig. 7.3: Hatch pattern layout Fig. 7.4: Assembly hatch patterns 2 Conventionally, some hatch patterns are associated with specific materials. However, the proliferation of available materials today makes it impractical to have a unique hatch pattern for material types and grades. Thus selected material hatch patterns are in common use. In architectural drawings, some material hatch patterns are in popular use. Machine drawings use few material hatch patterns and ANSI 31 pattern for cast iron in Fig. 7.5 is the recommended today for machine drawings. This pattern may be used for all types of materials in machine drawings. Fig. 7.5 shows some material hatch pattern types. Fig. 7.5: Material type hatch patterns 7.5 Section View Representation and Placement Proper representation of section features is very important. Every feature directly exposed to the view needs to be included as visible entities in the section view. Gaps between feature segments must not be allowed. In Fig. 7.6, two section view representations are given. The left representation is right while the right representation is wrong because of gaps between the view segments. The line features omitted in the right representation are clearly visible in the indicated section plane. Section view position in a drawing has a definite relationship with the view direction. A section view should be placed behind the tail end of the view direction arrow. Fig. 7.7 illustrates the application of this principle for a) top section view, b) front section view, and c) right section view. Sufficient gap should be allowed between the section and the adjacent view it is derived from. This gap is very important because sufficient space must be made available for dimension placement. a) Right b) Wrong Fig. 7.6: Section view representation 3 a) Top section view b) Front section view c) Right section view Fig. 7.7: Placement of section views 7.6 Section View Types Section views may be classified in different ways. For our discussions, we shall group them into full, partial, and special section views. In full section views the full length of the principal dimension perpendicular to the view direction of the object is shown in section view. Hence the cutting plane or planes pass through the whole cross- section of the object. Partial section views do not reveal the whole sections, but show a portion of the interior. Special sections include auxiliary sections, assembly sections, and un-sectioned features. Full Section Views Full section views provide section views along the full length of the cross-section of an object. They include straight, offset, removed, revolved, and aligned section views. Each is briefly discussed below. Straight Sections A straight section is also called a full section by some authors. The cutting plane for a straight sections cuts right through the middle of the object so that one half of it is revealed after the second half is imagined removed. Thus a straight section is created from a single cutting plane. Straight sections are best for objects with an axis of symmetry. In multiview drawings, a section view can replace a standard view, and straight sections are commonly thus employed. Fig. 7.8 shows an example of a straight section view. Offset Sections Offset sections are similar to straight section except the cutting plane changes direction at 90 o at a time as it goes through the object.
Details
-
File Typepdf
-
Upload Time-
-
Content LanguagesEnglish
-
Upload UserAnonymous/Not logged-in
-
File Pages10 Page
-
File Size-