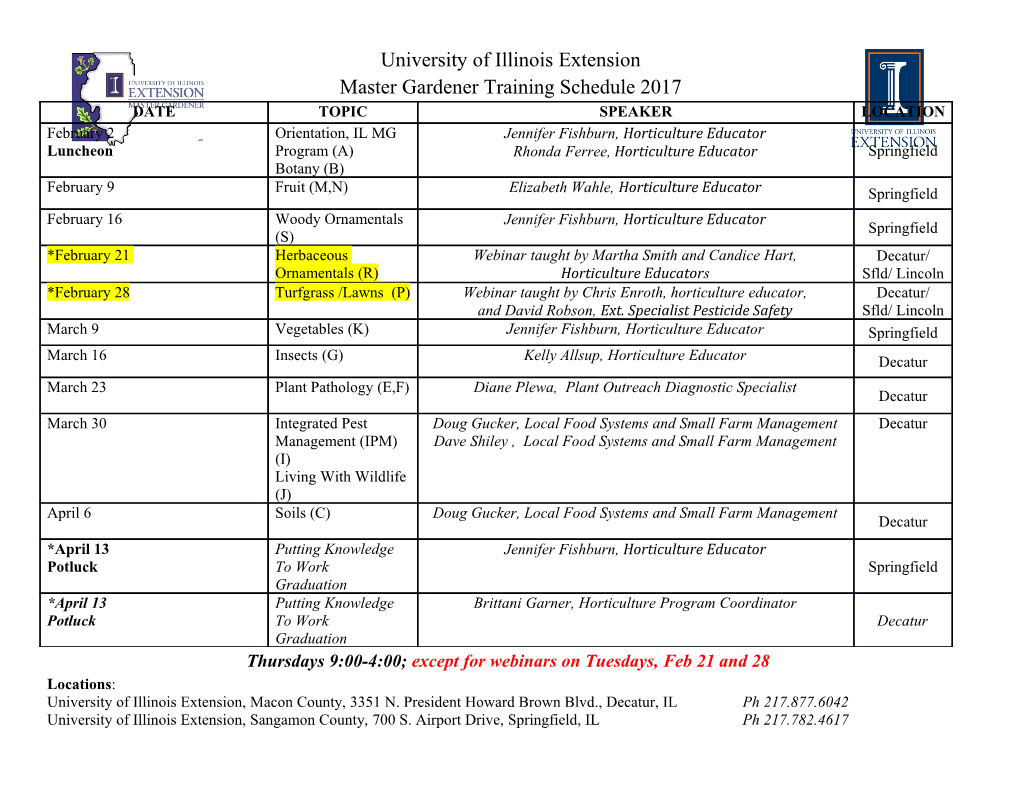
Design, Construction and Control of an Industrial Scale Biped Robot Volume 1 Joe Cronin Supervisors Associate Professor RA Willgoss Associate Professor R Ford Revision 2.0 December 2005 A thesis submitted in fulfilment of the requirements for the degree of doctor of philosophy. ABSTRACT A 500Kg, self-contained biped robot, named Roboshift, has been conceived and tested to investigate issues associated with the control of industrial scale biped robots. This project represents the first credible attempt to build a heavy weight autonomous biped robot. The recent expansion in humanoid robot development has highlighted advances made in anthropomorphic biped technology. Current research into speech recognition, vision systems, laser topography, artificial intelligence and electroactive polymers will ultimately achieve an Android capable of human like actions and thought processes. Justification for this most demanding and expensive research is based on philanthropic models that suggest these robots will attend to the bedridden, or replace humans in dangerous areas. However, the cost of a biped robot when compared to that of a wheeled or tracked vehicle restricts commercialisation for these applications. As well, the size and working capacity of current humanoid robots is not compatible with the heavy lifting requirements found in such environments. It is proposed that only biped robots of an industrial scale, possessing a capacity much greater than that of a human, will be of commercial value in the future. Typical applications may include the handling of materials in confined or uneven terrain, where a forklift or other commercially available materials handling equipment would be unsuitable. For example, field handling in military, mining or geological environments. Minimal research has been conducted into the realisation of such a device, which presents challenges in terms of the magnitude of dynamic forces produced and of the systems required to control the robot in real-time. Review of relevant literature reveals that little research has been completed in this field. Therefore, operational characteristics for an industrial scale biped robot are defined. The design then details the structure and integration of mechanical, hydraulic, and electrical systems. Roboshift is powered by an internal combustion engine and is the first biped robot with a capacity for extended operation. Modelling was conducted to determine joint trajectories, power requirements, hydraulic flow parameters and dynamic characteristics. The robot is controlled by a distributed, hierarchical system comprising sixteen microprocessors, a control computer acting as the midbrain and a communications computer acting as the central nervous system. Sensors measure attitude Abstract and heading (vestibular system) as well as ground reaction forces and joint angles (propreoception). The control strategy is based on feed forward trajectories generated by inverse kinematic analysis. Corrections to trajectories are made in real time by higher level routines running on the main control computer. Joint position is achieved by local feedback control. Software for the robot was written in the C language. Experimental results are presented detailing the performance of the robot in comparison to theoretical analysis. After construction and testing of actuators and sensors, calibration software was tested successfully. Once calibrated, the robot was lowered to the ground where the active balance software was able to control the robot in the frontal and sagittal planes. Frontal sway software was tested with mixed success as natural oscillation of the structure, which was not detectable by the control system, led to erroneous force data. Detailed dynamic modelling was then completed to determine the causes of oscillation in the robot. The modelling led to the formulation of a control strategy where non-collocated sensors are used to measure link strain as a feedback to a modified proportional controller. The project has demonstrated that an industrial scale biped incorporating an internal combustion engine and hydraulic power system is feasible.. Analysis presented proposes that as the height of a biped robot increases, the expected elastic deformation of the structure increases as the cube of the height, making control extremely challenging. A strategy for the control of heavy-weight robots is suggested It is also proposed that technology incorporated in current humanoid robots can not be scaled to control industrial bipeds. TABLE OF CONTENTS Abstract Acknowledgements Contents I List of Figures, Tables and Flowcharts VI List of Special Names and Abbreviations XII 1.0 Introduction 1.1 The Quest for Biped Motion 1 - 1 1.2 Embodiments of Bipedal Motion 1 - 4 1.3 About this Project 1 - 7 1.4 Structure of this Document 1 - 8 2.0 Walking Robots 2.1 Walking robots 2 - 2 2.1.1 Wheels versus Legs 2 - 4 2.1.2 Legged Robots 2 - 6 2.2 Biped Robots 2 - 10 2.3 Control of Biped Robots 2 - 22 2.4 Design Criteria of an Industrial Biped 2 - 33 2.5 Conclusion 2 - 36 3.0 Mechanical Design of Roboshift 3.1 Design Philosophy 3 - 1 3.2 Mechanical Configuration 3 - 4 3.2.1 Basic Structure 3 - 4 3.2.2 Configuration of Joints 3 - 6 3.2.3 Range of Movement 3 - 8 3.2.4 Mechanical Design for Aspects of Control System 3 - 10 3.2.4.1 Transducers 3 - 11 I Table of Contents 3.2.4.2 Actuators 3 - 12 3.2.4.3 Power and Electrical Systems 3 - 13 3.3 Detail Mechanical Design 3 - 14 3.3.1 Feet 3 - 14 3.3.2 Knees, Lower and Upper Legs 3 - 21 3.3.3 Hip 3 - 23 3.3.4 Body 3 - 25 3.3.5 Construction 3 - 26 4.0 Power and Electrical Design 4.1 Hydraulic Design 4 - 2 4.1.1 Flow Calculation 4 - 2 4.1.2 Hydraulic Circuit Design 4 - 4 4.1.3 Conclusions on Hydraulic Design 4 - 10 4.2 Electrical Design 4 - 10 4.2.1 Electrical Power Requirements 4 - 10 4.2.2 Circuit Protection 4 - 11 4.2.3 Power Distribution 4 - 12 4.2.4 Wiring 4 - 14 4.2.5 Conclusions on Electrical Power 4 - 15 4.3 The Engine 4 - 15 4.3.1 Engine Power 4 - 16 4.3.2 Engine Selection 4 - 18 5.0 Control System Philosophy 5.1 Robot vs Cybermachine 5 - 1 5.2 Control System Overview 5 - 3 5.3 Control Strategy 5 - 5 5.4 Walking Control 5 - 8 II Table of Contents 5.5 Software Structure 5 - 9 6.0 Control System Hardware 6.1 Main Control Computer (PC) 6 - 1 6.2 Communications PC 6 - 3 6.3 Local Joint Controllers 6 - 3 6.4 Sensors 6 - 6 6.4.1 Joint Movement (Opto Encoders & Limit Switches) 6 - 6 6.4.2 Attitude (Gyro & Flux Gate Compass) 6 - 9 6.4.3 Force (Strain Gauges and Amplifiers) 6 - 12 6.4.4 Foot Contact Switches 6 - 15 6.5 Conclusions on Control Hardware 6 - 15 7.0 Control System Modelling 7.1 Kinematic Simulation 7 - 1 7.2 Dynamic Simulation 7 - 4 7.3 Formulation of Joint Trajectories 7 - 12 Conclusion 7 - 13 8.0 Control System Software 8.1 Main Control Program 8 - 1 8.1.1 Data Acquisition Routine 8 - 4 8.1.2 Maintenance Routines 8 - 6 8.1.3 Calibration Routine 8 - 7 8.1.4 Locomotion Routine 8 - 10 8.1.4.1 Frontal Balance 8 - 19 8.1.4.2 Frontal Sway 8 - 21 8.2 Communications Program 8 - 24 8.2.1 Receiving Data from The Microprocessors 8 - 26 8.2.2 Sending Data 8 - 28 8.3 Local Joint Control Software 8 - 30 III Table of Contents 8.3.1 Main Control Loop 8 - 30 8.3.2 Interrupt Service Routine 8 - 32 8.3.3 Calibration Routine 8 - 35 8.3.4 Motion Control Routine 8 - 38 8.4 Summary of Control Software Implementation 8 - 40 8.5 Software Development and Testing 8 - 40 8.6 Starting the Robot 8 - 46 9.0 Operational Trials on Roboshift 9.1 Transducer Calibration and Performance 9 - 1 9.1.1 Force Transducers 9 - 1 9.1.2 Artificial Horizon and Compass 9 - 6 9.1.3 Shaft Encoders 9 - 7 9.1.4 Electronic Noise 9 - 8 9.2 Power Pack 9 - 10 9.3 Joint Control 9 - 12 9.4 Initialisation Program 9 - 13 9.5 Stationary Balancing Program 9 - 15 9.6 Locomotion 9 - 18 9.5.1 Frontal Sway 9 - 19 10.0 Discussion 10.1 Mechanical Design 10 - 1 10.1.1 Compliance 10 - 1 10.1.2 Joints 10 - 2 10.1.3 Hydraulic Actuation 10 - 3 10.2.1 Power 10 - 4 10.2.2 Electronic Noise 10 - 5 10.3 Control Hardware 10 - 5 10.3.1 Sensors 10 - 6 IV Table of Contents 10.4 Control Software 10 - 8 10.4.1 Local Joint Control 10 - 8 10.4.2 Communication Software 10 - 9 10.4.3 Calibration 10 - 9 10.4.4 Balance 10 - 10 10.4.5 Sway 10 - 10 10.4.6 Project 10 - 11 11 0 Additional Modeling 11.1 Modeling Strategy 11 - 2 11.2 Matlab Model 11 - 3 11.3 Effects of Link Stiffness 11 - 5 11.3.1 Frontal Sway Driven by Feed Forward 11 - 6 Sinusoidal Local Joint Trajectories using a range of Link Stiffness 11.3.2 Frontal Sway Driven by Feed Forward Sinusoidal 11 - 10 Local Joint Trajectories using a Calculated Member Stiffness 11.4 System Response to Step Input 11 - 11 11.5 System Response to Square Wave Force Input 11 - 15 11.6 Force Feedback Control 11 - 17 11.7 Strain Feedback Control 11 - 21 11.8 Summary of Simulation 11 - 29 12.0 Conclusion 12.1 Achievement of design criteria 12 - 1 12.2 Novel research 12 - 3 12.3 Future work 12 - 4 12.0 References & Bibliography R - 1 V LIST OF FIGURES Figure Name Page 1.1 Robby the Robot 1 - 1 1.2 Kawada’s HRP2, Honda’s Asimo and 1 - 2 Toyota’s trumpet playing humanoid 1.3 Roboshift 1 - 7 2.1 Japanese toy Android 2 - 6 2.2 Rygg’s mechanical horse 2 - 7 2.3 The Adaptive Suspension Vehicle 2 - 10 2.4 Range of biped robot weights 2 - 11 2.5 Classes of legged robots 2 - 13 2.6 The GEC Hardiman exoskeleton 2 - 17 2.7 Waseda University’s WH 11 2 - 19 2.8 Honda’s humanoid robot Asimo 2 - 20 2.9 Scatter plot of mass vs height of documented biped robots 2 - 21 2.10 All terrain forklift 2 - 36 3.1 Device configuration
Details
-
File Typepdf
-
Upload Time-
-
Content LanguagesEnglish
-
Upload UserAnonymous/Not logged-in
-
File Pages497 Page
-
File Size-