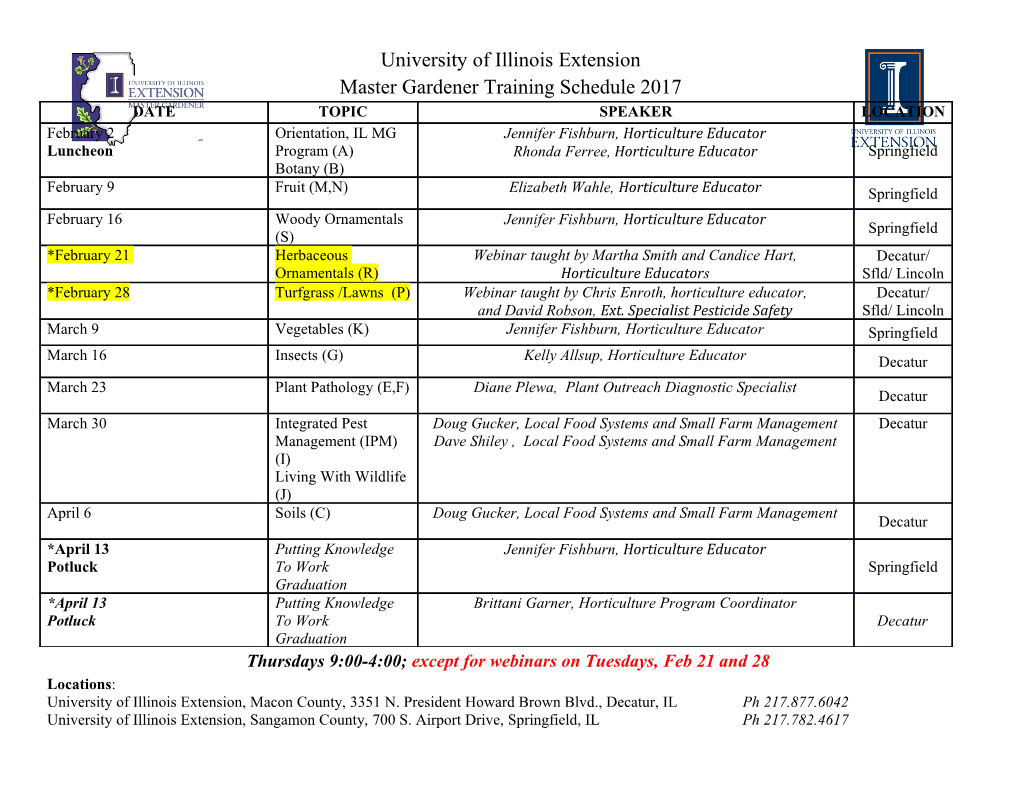
S S symmetry Article Energy Dissipation Characteristics and Parameter Identification of Symmetrically Coated Damping Structure of Pipelines under Different Temperature Environment Feng Jiang 1, Zheyu Ding 1,2, Yiwan Wu 1,* , Hongbai Bai 1, Yichuan Shao 1 and Bao Zi 1 1 Engineering Research Center for Metal Rubber, School of Mechanical Engineering and Automation, Fuzhou University, Fuzhou 350116, China; [email protected] (F.J.); [email protected] (Z.D.); [email protected] (H.B.); [email protected] (Y.S.); [email protected] (B.Z.) 2 Dongfeng Motor Corporation, Wuhan 430110, China * Correspondence: [email protected] Received: 10 July 2020; Accepted: 30 July 2020; Published: 3 August 2020 Abstract: In this paper, a symmetrically coated damping structure for entangled metallic wire materials (EMWM) of pipelines was designed to reduce the vibration of high temperature (300 ◦C) pipeline. A series of energy dissipation tests were carried out on the symmetrically coated damping structure at 20–300 ◦C. Based on the energy dissipation test results, the hysteresis loop was drawn. The effects of temperature, vibration amplitude, frequency, and density of EMWM on the energy dissipation characteristics of coated damping structures were investigated. A nonlinear energy dissipation model of the symmetrically coated damping structure with temperature parameters was established through the accurate decomposition of the hysteresis loop. The parameters of the nonlinear model were identified by the least square method. The energy dissipation test results show that the symmetrically coated damping structure for EMWM of pipelines had excellent and stable damping properties, and the established model could well describe the changing law of the restoring force and displacement of the symmetrically coated damping structure with amplitude, frequency, density, and ambient temperature. It is possible to reduce the vibration of pipelines in a wider temperature range by replacing different metal wires. Keywords: symmetrically coated damping structure; entangled metallic wire material; porous material; parameter identification; energy dissipation; high temperature 1. Introduction Pipelines exist widely in military, civilian, and other fields. The vibration control method of the pipeline includes active control and passive control. Compared with active control technology, passive control (e.g., rubber pipe clamp) has low cost, mature and reliable, and has been widely used. However, the damping performance of the traditional polymer material is poor at high temperature environment [1,2], the vibration reduction of high temperature pipeline is a great challenge for designers and researchers, especially when the temperature exceeds 200 ◦C. Entangled metallic wire materials (EMWM) is a promising porous material made of metallic wire helixes. It is sometimes referred to as “metal rubber (MR)” [3–5], “metal wire mesh (MWM)” [6], or “tangled metal wire (TMW) devices” [7]. Because of its special spatial network structure, EMWM has good elasticity and damping characteristics. Moreover, because EMWM is all-metal material, it has good environmental adaptability. Therefore, EMWM has been used in extreme environments [8], such as aircraft air cycle machines, turbo blowers, and micropower generators [9–11]. Some scholars Symmetry 2020, 12, 1283; doi:10.3390/sym12081283 www.mdpi.com/journal/symmetry Symmetry 2020, 12, 1283 2 of 17 have made a preliminary exploration on the mechanical properties of EMWM at high temperature environment. Ding et al. performed a series of quasi-static compression experiments for plate-like EMWM in the temperature range of 20–500 ◦C and pointed out that the stiffness of EMWM will not fail with the increase of temperature [12]. Hou et al. proposed a new damping capacity measurement method for EMWM and conducted a damping performance test for EMWM in the temperature range of 70–300 C[13]. They reported that the damping capacity of EMWM exhibits good resistance of − ◦ high–low temperature. An EMWM insertion damping structure was proposed by Zhu et al. [14] and applied to the vibration reduction design of foundation under high temperature (300 ◦C). Zhu et al. reported that the maximum insertion loss could reach 15.37 dB. It is an interesting attempt to use EMWM to reduce the vibration of the pipeline. A novel coated damping structure for EMWM of pipelines was designed by replacing a viscoelastic damping material with multiple EMWM blocks, which were uniformly distributed on the outer wall of the pipeline [15]. Xiao et al. proposed a theoretical model of the cladding damping structure for EMWM and carried out the test of pipeline vibration reduction at room temperature [16]. Wu et al. designed a coated damping structure for metal rubber (MR) of bellows, in which metal rubber was coated on the bellows by wire rope [17]. They conducted a dynamically tested on their structure in the bending direction at normal temperature and reported that the coated damping structure for metal rubber of bellows has a strong damping energy dissipation ability. Ulanov et al. proposed a calculation method of pipeline vibration with damping supports made of the MR material by means of the finite element ANSYS software package [18]. However, the effectiveness of the calculation method was not verified by experiments, and the effect of temperature on the structure was not taken into account. Although Bai [15], Xiao [16] and Wu [17] have verified the effectiveness of EMWM in pipeline vibration reduction, they did not take into account the effect of temperature and only carried out experiments and analysis at room temperature. This paper designs a symmetrically coated damping structure for EMWM of pipelines, and investigates the energy dissipation characteristics of the designed structure in the temperature range of 20–300 ◦C. The effects of vibration frequency, amplitude, density, and temperature on the energy dissipation characteristics of the structure are analyzed. To provide an effective theoretical basis for predicting the energy dissipation characteristics of the symmetrically coated damping structure for EMWM of pipelines and guiding its design under high temperature, a model of nonlinear elastic restoring force is set up, which describes the dynamic characteristics of the coated damping structure for EMWM of pipelines under different temperature. 2. Design of the Symmetrically Coated Damping Structure for EMWM of Pipelines To reduce the vibration of pipelines under different temperature environment, a symmetrically coated damping structure for EMWM of pipelines was designed as shown in Figure1. The coated damping structure is composed of plate-like EMWMs, constraining rings, pipe section and bolts. This structure is a kind of elastic damping pipe clip. Symmetrically installed EMWMs are the main energy dissipation elements of the structure. Symmetry 2020, 12, x FOR PEER REVIEW 2 of 16 such as aircraft air cycle machines, turbo blowers, and micropower generators [9–11]. Some scholars have made a preliminary exploration on the mechanical properties of EMWM at high temperature environment. Ding et al. performed a series of quasi-static compression experiments for plate-like EMWM in the temperature range of 20–500 °C and pointed out that the stiffness of EMWM will not fail with the increase of temperature [12]. Hou et al. proposed a new damping capacity measurement method for EMWM and conducted a damping performance test for EMWM in the temperature range of −70–300 °C [13]. They reported that the damping capacity of EMWM exhibits good resistance of high–low temperature. An EMWM insertion damping structure was proposed by Zhu et al. [14] and applied to the vibration reduction design of foundation under high temperature (300 °C). Zhu et al. reported that the maximum insertion loss could reach 15.37 dB. It is an interesting attempt to use EMWM to reduce the vibration of the pipeline. A novel coated damping structure for EMWM of pipelines was designed by replacing a viscoelastic damping material with multiple EMWM blocks, which were uniformly distributed on the outer wall of the pipeline [15]. Xiao et al. proposed a theoretical model of the cladding damping structure for EMWM and carried out the test of pipeline vibration reduction at room temperature [16]. Wu et al. designed a coated damping structure for metal rubber (MR) of bellows, in which metal rubber was coated on the bellows by wire rope [17]. They conducted a dynamically tested on their structure in the bending direction at normal temperature and reported that the coated damping structure for metal rubber of bellows has a strong damping energy dissipation ability. Ulanov et al. proposed a calculation method of pipeline vibration with damping supports made of the MR material by means of the finite element ANSYS software package [18]. However, the effectiveness of the calculation method was not verified by experiments, and the effect of temperature on the structure was not taken into account. Although Bai [15], Xiao [16] and Wu [17] have verified the effectiveness of EMWM in pipeline vibration reduction, they did not take into account the effect of temperature and only carried out experiments and analysis at room temperature. This paper designs a symmetrically coated damping structure for EMWM of pipelines, and investigates the energy dissipation characteristics of the designed structure in the temperature range of 20–300 °C. The effects of vibration frequency, amplitude, density, and temperature on the energy
Details
-
File Typepdf
-
Upload Time-
-
Content LanguagesEnglish
-
Upload UserAnonymous/Not logged-in
-
File Pages17 Page
-
File Size-