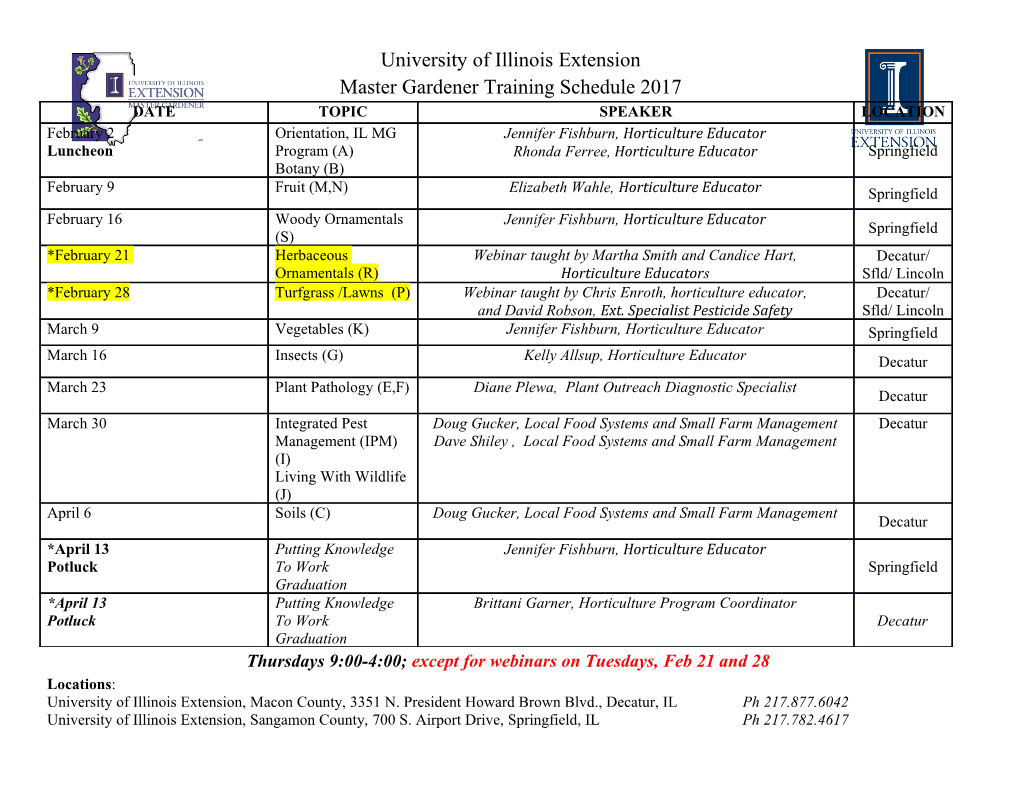
An overview of recent trends in parametric modeling S.S. Wawre 1 and kabadeDK 2 1,2 Asst. Professor, Dept. of Mechanical Engineering SRES COE Kopargaon, India Abstract- In this review paper parametric modeling advances are discussed. Parametric data exchange, feature based parametric discussed. In first section parametric modeling case studies are elaborated. Various case study discusses parametric modeling as a tool for easy update of existing model called master model to various new derived models. For parametric modeling various tools like embedded excel, API, programming language are discussed.3D CAD methodology for developing parametric system involves integration of built in module of CAD software. Part design module is used to model, parameterize and constrain design. API module is used to provide decision constraint. Parametric modeling includes two design variables namely primary or independent variable and dependent variable. In second section problems in parametric modeling is discussed. Typical problem associated with parametric modeling are topology &design intent loss. These problems are discussed which are addressed by various researchers. In last section parametric cad data exchange discussed whichisbackbone of collaborative CAD systems. Earlier CAD data exchanged between different CAD platforms share only shape information.In some research papers CAD data likeconstruction history, parameters, constraints, features and other elements of ‘design intent’ present in the model to be transferred across different CAD platforms are discussed. Keywords - Parametric cad, associative cad, feature based modeling, design automation, topology, constraint based modeling, design intent. I. Introduction Parametric modeling is well developed technology to utilize previous design to develop new design by varying parameters. It is design reuse technique. Parametric modeling has made product development phase quick and efficient.CAD feature command i.e. extrude, revolve,slotetc are itself parametric entity which accelerated design process. History based parametric cad records history of creation of part model which is called design tree showing parent-child relationship of features.Constraints are the mathematical requirements placed on the geometric elements in a 3D solid model. Constraintbased modeling uses feature definitions (extrude, revolve, fillet, etc.), dimensional and geometric constraints (equal, parallel, concentric, etc.), and a feature tree (how the features are arranged) to define 3D solid models. They control the geometric behavior of a dynamic solid model.Parametric modeling involves variation of parameters. Parameter variation for simple object does not pose problem, but as model becomes complex it responds irrationally with parameter change. Parametric interaction that makes a feature nonfunctional,feature parameters rendered obsoletepart geometry and nonstandard topology of part model.For accelerating design process all design activities are performed on different CAD softwares so the CAD data exchange is prime concern for having efficient design process. II. Literature review The term parametric design associated with parametric systems is defined by Shah [13] as "a process of designing with parametric models in a virtual surrounding where geometrical and parameter variation are natural". Parametric CAD models, if well parameterized, allow for the definition of new configurations of products just by changing the values of some parameters. Wang[1] made design change automation possible by parametric sketching and design associability for bottle design by interfacing 3D CAD model and dimension database. Parametric changes are done through text file or @IJMTER-2016, All rights Reserved 381 International Journal of Modern Trends in Engineering and Research (IJMTER) Volume 03, Issue 04, [April– 2016] ISSN (Online):2349–9745; ISSN (Print):2393-8161 database software.Thakkar and patel[2]defined parametric technique by interfacing through MS EXCEL and C language for pulley design.Ongkodjojo and gunawan[3] discussed flatbed conveyor design variation through template design. The technique offered on this paper is how to get a full control of the model by managing and driving parameters attached on it. With the aid of Solid Works 2004 as 3D Solid Modelling Software with the parametric capability, parameters are built by utilising constraints, relations, shared values, equations, and assembly mates features while driving and managing the parameter values are done with the help of design table and configuration.Zheng and Cheng[4] described spur gear design through parameter, relations between parameters and Pro-PROGRAM. Jason [5] describedPro-PROGRAM for secondary design modifications. Fan[6] has automated part library by Family table interfaced by visual C++ and Pro/Toolkit. Kuang[7] built standard part library with UG- NX and MS-Excel by Visual C++.Wawre[55] discussed parametric modeling for valve components to generate part families of it. In hid research article single design variable is used which has mathematical relation with all design parameter so that parametric updates are simplified. 3D Parametric Modeling for Product Variants Using Case Study on Inner Ring of Spherical Roller Bearing Ruchik D. Trivedi, Dhaval B. Shah, Kaushik M. Patel[31] presented paper, In this paper an attempt has been made to integrate the commercially available package Pro/E with Microsoft Excel spreadsheet for 3D parametric modeling. Various product variants of the inner ring of spherical roller bearing have been executed by parametric designing concept in Pro/Engineer Wildfire. Pro/Program is a powerful secondary generation tool to validate parametric design of the component. Pro/Program reflects all parameters and geometric data of the part in a text data form. This data can be modified to add new feature, delete existing feature, suppress the feature and change the dimension of the feature. A proper user interface (API) can directly modify the Pro/Program and the part model can be driven according to the user input in user interfacing. Here Microsoft Excel and pro/E are integrated by Excel Analysis tool which acts as an interfacing media. Excel Analysis tool transfers the spreadsheet data to the Pro/E database. The high potential of this technology for routine design has been fully recognized and highlighted in the research community for more than a decade by Anderl and Mendgen [14] and Hoffman [15,16].However, to obtain a valid and functional CAD model, the preliminary task is to identify the right functional parameters from the requirements and to build the appropriate parametric structure. Several research studies propose practical or integrated methods for the identification of functional parameters [17] and for structuring information and entities in parametric CAD models [18,19]. Existing methods for parametric CAD systems embedded in CAD methodologies and guidelines mainly work at assembly level to ensure a product-centric development (top-down design approach) rather than a part-centric development (bottom-up approach). YannickBodein, Bertrand Rose, Emmanuel Caillaud[54] presented a paper entitled as “A roadmap for parametric CAD efficiency in the automotive industry”, The novelty of this work is therefore to propose a general strategy for utilizing the advantages of parametric CAD in the automotive industry in the form of a roadmap. The main stages of the roadmap are illustrated by means of industrial use cases. The roadmap is composed of five key phases:1. Standardization 2.Methodology3.Generic modeling.4.Expert rules.5.Automation.Standardization phase involves Define a common CAD environment and practices for all designers, Define CAD data quality minimum criteria, Ensure the compatibility of CAD data structure with the PLM system (CAD integration capability).Advanced methodology involves Optimize modeling practices based on each component’s characteristics, Improve interoperability and exchange between other tools from the design chain and PLM environment (i.e. simulation tools).Knowledge-based design involves Integrate knowledge inside CAD models, Create generic 3D features embedding know-how. Create generative design models/product expert models. Expert rules checks involves Check design rules, companies’ expert rules and data quality on the @IJMTER-2016, All rights Reserved 382 International Journal of Modern Trends in Engineering and Research (IJMTER) Volume 03, Issue 04, [April– 2016] ISSN (Online):2349–9745; ISSN (Print):2393-8161 product, Ensure compliance of the design with standards and norms Automation involves Accelerate low value added tasks/automate repetitive tasks/create new functions. Jorge D. Camb, Manuel Contero , Pedro Company[30] presented a paper titled as “Parametric CAD modeling: An analysis of strategies for design reusability”. In this paper, we present ananalysis of formal CAD modeling strategies and best practices for history-based parametric design: Delphi’s horizontal modeling, explicit reference modeling, and resilient modeling. Horizontal modeling starts part modeling with only datum plane as parent feature. In explicit referencing focus is on minimizing constraints linked to existing geometry and align constraint to datum plane. Child feature are created near parent feature to group localized model tree. In resilient modeling [developed by Gebhard], methodology is based on design tree for proper sequence and structure of it. Aspects considered in our study include the rationale to avoid
Details
-
File Typepdf
-
Upload Time-
-
Content LanguagesEnglish
-
Upload UserAnonymous/Not logged-in
-
File Pages9 Page
-
File Size-