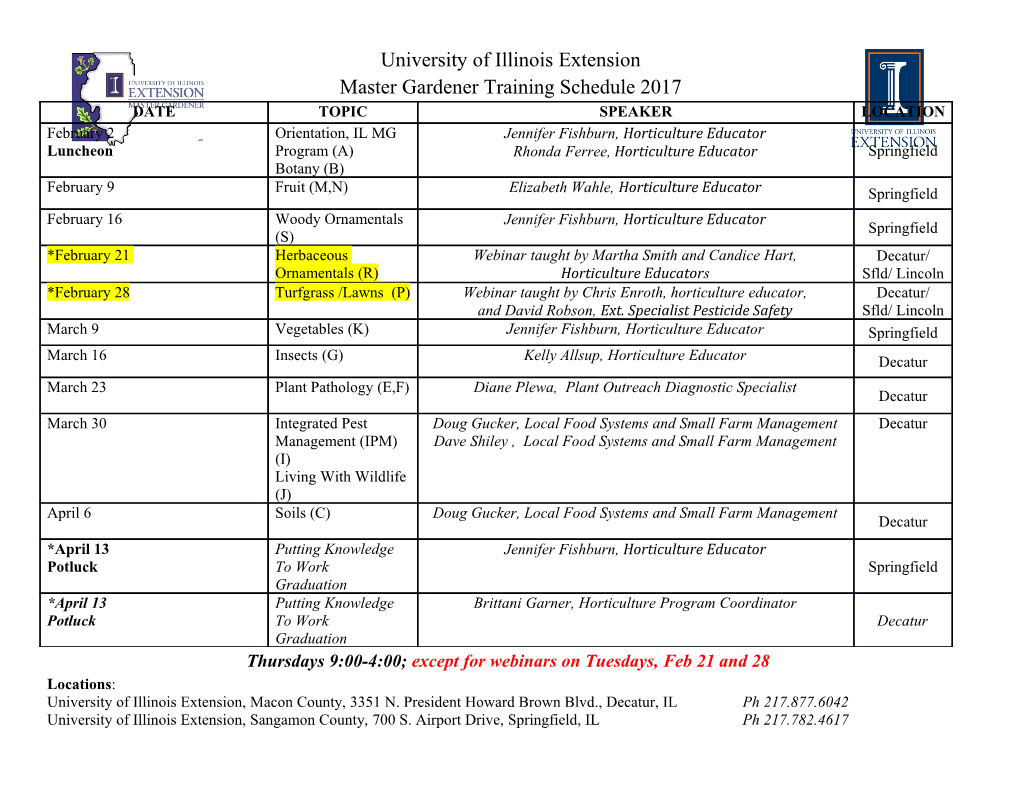
Ill XA9949546 3. REACTOR PRESSURE VESSEL MATERIALS K. Suzuki, The Japan Steel Works, Ltd., Muroran Plant 1 INTRODUCTION The demands placed on reactor pressure vessel (RPV) steels are severe. They must be manufactured in required sizes and thicknesses, be of sufficient strength and toughness, show little deterioration under irradiation, allow the production of high quality welds and be compatible with the cladding. This Chapter refers to non-WER pressure vessels, but many of the guiding principles described here apply to that particular case. Starting with carbon steel plates and forgings for conventional boiler drums in the dawn of commercial light water reactors (LWRs) followed by a few changes thereafter, SA533 and SA508 and similar grade steels have become well established [1]. Both grades are of the vacuum treated, quenched and tempered type of 600 N/mm2 strength class, which is not the highest level in weldable structural steels. - 71 - The specific requirements for RPV steels are to give, even to large- size component materials of RPVs, higher values of the following properties: - uniformity and isotropy of mechanical properties, including less mass effect in the mid-section - fracture toughness - internal defects - weldability - resistivity to neutron irradiation embrittlement Some further items were added during the past two decades primarily for the purpose of easier execution of non-destructive examinations both pre-service and in-service. These are: - fewer weld seams in RPV - larger and more integral design of component materials The requirements have been steadily realized. - 72 - With respect to the weld, improvements have been made by adequate selection of flux in combination with requirements on the chemical composition of the weld wire, welding parameters such as weld bead size and sequence to minimize the coarse grained areas in the heat affected zone (HAZ) [2]. 2 HISTORICAL REVIEW [3] Many of the earlier plants were constructed of so-called carbon or mild steels (usually in normalized and tempered, NT, condition), but several of these were prototypical units and applications have moved to the widely accepted low alloy manganese, molybdenum, nickel, quenched and tempered (QT) grades of higher strength. Early gas cooled reactors were also of carbon steel, but these were replaced in later versions by prestressed concrete vessels. Most of the reactors operating at mid-1973 were constructed of the manganese-molybdenum steels in QT condition. In practice, the use of the low alloy steels has predominated. For example, all of the Japanese reactors of BWR and PWR types have A533-B Class 1 (QT) pressure vessels except Tsuruga which uses A302-B (QT) and JPDR-2 with A302-B in NT condition [4]. The sole Japanese gas cooled reactor (Tokai Nuclear Power Station) was contained in a vessel of a Japanese C-Mn steel. Typical composition data for the Japan Steel Works (JSW), Ltd. steel used is C-0.10*, Mn-1.30%, Si-0.25%, P- - 73 - 0.014%, and S-0.018* (equivalent to the UK steel, BS NDIV originally planned for this reactor vessel). Special care was taken to minimize phosphorus and sulphur and to refine grain size, thereby enhancing notch toughness. In addition, an experimental programme was conducted to develop the best welding electrode material for joining plates of the Tokai vessel [5]. The relative content of manganese and silicon was determined for optimum toughness of welded structures. The Agesta reactor of Sweden was contained in a carbon steel, equivalent to ASTM Type A212-B (a carbon-silicon-manganese steel), the Oskarshamn-1 vessel steel was equivalent to ASTM Type A302-B [6] (a manganese-molybdenum steel). The A212-B steel was also used in one of the early U.S. reactors, Indian Point-1, and a limited number of experimental reactors. In the Federal Republic of Germany (F.R.G.) the steel designations match national conventions, but most water reactor steels were quite similar to U.S. grades A508-C1.1 for forging and A533-B for plate steel [7]. And the most RPVs were strongly dependent on the 22 NiMoCr 37 composition (similar to A508, C1.2 : a nickel-chromium- molybdenum steel). 22 NiMoCr 37 steel was used in F.R.G. until 1976 and fulfilled all requirements [8]. However, this type of steel exhibited some susceptibility to stress relief cracking and underclad cracking [9-11]. By this reason the use of 20 MnMoNi 55 steel (similar to A508, C1.3 : a manganese-molybdenum-nickel steel) - 74 - was increased. Little basic difference in steel type exists among the vessels of reactors now operating throughout the world. However, certain metallurgical differences of crucial importance are identificable, but other considerations such as neutron flux and fluence, irradiation temperature, stress state etc. have equal or greater bearing on radiation embrittlement sensitivity. Relative to radiation embrittlement, however, it is important to realize that all steels used to date have the same basic weakness. They are susceptible to radiation hardening, increases in strength, and reduction to fracture toughness. Thus, it is appropriate, even necessary, to generalize initially in describing radiation embrittlement of vessel steels. The current choice of material is of specific A-533B, Cl.l alloys for plates and A-508, C1.3 alloys for forgings (Table 1 ) [12]. These are very similar steels of the low alloy manganese-molybdenum type (A302-B) with nickel added. Significant differences have been developed between the old and new steels. Major differences are in improved strength and toughness for the new steels with a change of micro-structure from basically pearlitic to tempered bainitic to temperecd martensitic or mixed bainitic-martensitic microstructure. Chemically, the new steel is purer, that is, it contains smaller amounts of residual or tramp elements, because steel-making procedures incorporating vacuum degassing steps are applied routinely in their production. These steps, producing singificant - 75 - changes, are considered improvements from the view of radiation embrittlement, but the resulting implication is that the greatest concern must be addressed to the older plants, where our knowledge of the alloys used and the service conditions is least. Knowledge about welds is probably both the most critical and the most limited. Emphasis then must be placed on learning more about the old systems materials, especially welds, and improving the new (future) materials. 3 BASE MATERIAL 3.1 Chemical Composition [12] Specifications for the structural steels which are extensively used for the LWR components in Germany and in the United States are listed in Table 1 [12]. Some basic investigations were conducted to confirm the effect of chemical composition on 20 MnMoNI 55 in addition to the basic studies for heavy forgings [10, 13]. Fig.l shows the continuous cooling transformation curves (CCT curve) for this steel with 0.17% and 0.20* C. The differences in ferrite, pearlite and bainite transformation range are observed due to a little difference in C content. Also the effect of Mn, Ni, Mo on the hardenability was investigated, but the results do not indicate substantial differences in the CCT curve. - 76 - In order to maintain sufficient toughness of large forgings at lower temperature, it is important to provide fine grain as well as proper structure. There are some procedures to refine the grain size, and it is an usual procedure to add Al. During the quenching of large and massive forging, austenitizing requires considerably long time to obtain uniform heating. In this case, the presence of AIH is strongly effective in preventing grain growth. V is known as a predominant element to enhance the tensile properties of material. However, the toughness and weld crack sensitivity of the material are also affected by the addition of this element. Thus no V should be added, even though the maximum content of 0.03 or 0.05% is allowed in the material specifications- It is said that Cu and P affect the irradiation damage which is evaluated by the shift in Charpy impact curve [14]. In response to this requirement, the target values of Cu and P content of 0.0835 max. and 0.008% max. respectively are maintained. Concerning weldability of the steel, liquation cracking and stress relief cracking in particular, crack promoting elements and threshold values for cracking occurrence were investigated. Cracking can be avoided by limiting the Mo content, the elements P, S, Cu, Sn, N, As, Co and Al as well [11]. - 77 - 3.2 Steel and Ingot Making [15] 3.2.1 Manufacturing Process of Large Ingots (1) History of the production of large ingots In Fig.2, major changes in the history of the production of large ingots in JSW are summarized. It also shows the transition of maximum ingot size. Before Bochumer Verein-type vacuum casting facilities were installed in 1959, steel was melted by acid open hearth furnaces to minimize hydrogen pick up and the steel cast in air. After the installation, acid open hearth was replaced by basic open hearth and electric arc furnace (EAF), because hydrogen removal was made possible during vacuum casting. In order to obtain higher degree of vacuum during casting, a steam ejector was introduced in 1970. In 1973 a holding furnace was installed to replace the open hearth. According to the demand from industries, sizes of ingot became larger year after year. In 1969 a world largest 400 ton ingot was produced, and the record was soon renewed by 500 ton ingot in 1971, 570 ton ingot in 1980, then 600 ton ingot in 1985. (2) Installation of ladle refining furnace (LRF) In 1980, to meet higher requirements for the record 570 ton ingots of nuclear vessel application, vacuum facilities were installed to the holding furnace to convert it into a ladle refining furnace. - 78 - Fig.3 shows a schematic outline of the furnace.
Details
-
File Typepdf
-
Upload Time-
-
Content LanguagesEnglish
-
Upload UserAnonymous/Not logged-in
-
File Pages95 Page
-
File Size-