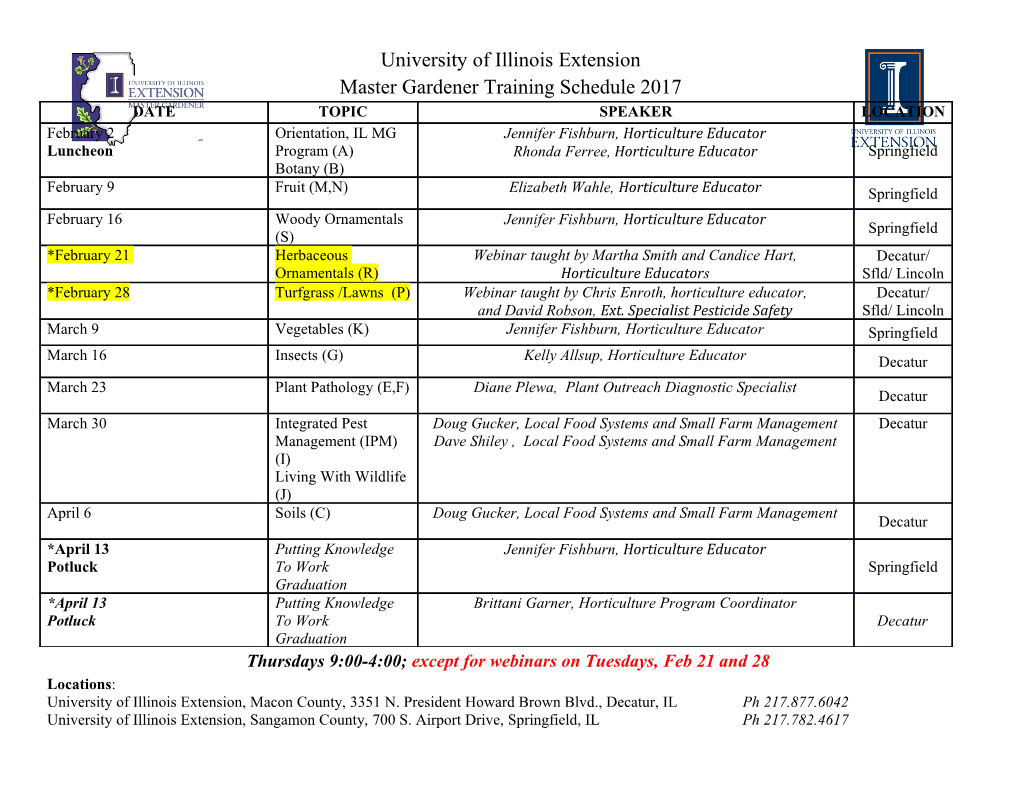
Refinery configurations for maximising middle distillates A comparison of configurations for upgrading residual oil products for the maximum production of diesel ARun ARoRA and ujjAl MukheRjee Chevron Lummus Global efiners globally continue to face numerous challenges as 5.0 World environmental laws become 4.5 R ECA increasingly stringent. Principal 4.0 among them in the near future will 3.5 be the International Maritime 3.0 Organisation’s (IMO) proposed changes to bunker fuel oil sulphur 2.5 limits, from the current limit of over S, wt% 2.0 3.5% down to 0.5% globally and 1.5 from 1% to 0.1% in Emission 1.0 Control Areas (ECA, see Figure 1). 0.5 Global demand for high-sulphur 0.0 residual fuel oil (HSFO) is steadily 2005 2007 2009 2011 2013 2015 2017 2019 2021 2023 2025 declining too, by 35% since 1995. Both of these changes will signifi- cantly impact a refiner’s ability to Figure 1 Requirements of IMO regulations Source: International Maritime Organisation market any significant quantity of HSFO at a price that will maintain technology are just two of the diesel-driven vehicles in Europe refinery profitability. Refineries reasons why the demand for diesel and developing countries. Max two-column width currently making a significant continues to outpace that of gaso- Current refining investment is Blue background around amount of fuel oil and lacking the line. IMO regulations will indirectly predominantly made in Asia, the brown. complexity to upgrade the residual increase diesel demand further as Middle East, Russia and Latin oil to premium products (middle refiners are forced to blend in addi- America — regions with growing Always translate into UK distillates) will face two difficult tional low-sulphur diesel to meet demand for refined products. English (except images). options: either invest in commer- fuel oil sulphur specifications. Tightening of product quality speci- Leading cap on rst word cially proven and reliable solutions Worldwide, production of mid- fications will accelerate the only. to convert HSFO to more valuable distillates is projected to account for implementation of deep conversion liquid products such as Euro V 55% of the rise in oil demand units in existing refineries, but often diesel to greatly improve the refin- expected over the next 20 years. The these refineries are constrained by ery’s profitability, or face a threat to shift to diesel puts emphasis on plot space, hydrogen and other shut down the refinery as the opera- bottom-of-the barrel processing. infrastructural issues. Grassroots, tion becomes uneconomical to export-oriented refineries are all continue. Growing demand geared towards high conversion to Worldwide demand for refined mid-distillates. Shift in product demand products is projected to increase For the strategically oriented The IMO’s looming specification significantly in the next 20 years, refiner, stringent requirements for changes (see Figure 1) are likely to driven by population growth and high-quality products actually accelerate the decline in demand for the transition of emerging markets present an opportunity to invest in HSFO by the year 2020, if not earlier. into the global economy, with the the right technologies to signifi- Worldwide, including emerging majority of growth coming from cantly improve refinery margins. markets such as China, India and China in particular and Asia in Based on increasing product the Middle East, there is a shift in general. According to OPEC, global demand and the closure of multiple product demand from gasoline to demand for diesel fuels is expected non-performing refineries, refining diesel. Ethanol substitution in gaso- to grow by 10 million b/d by 2030, margins are expected to recover line and improvements in engine driven by an increased share of by 2015. www.eptq.com PTQ Q3 2011 75 current trends only such refineries Coke Coke will survive in the future) drum drum • Ideally, should be part of a conversion platform encompassing Fractionator Reflux drum Wet gas complementary technologies. Technologies on the cusp of Unstablised commercialisation were excluded, naphtha because we did not want to prescribe Gas oil any solution without a reasonably stripper long operating history. For example, Light gas oil there are several slurry-phase resi- Residual oil due conversion processes on the Heavy gas oil verge of commercialisation, but Heater without a commercial operating history there is no data on reliability Figure 2 Schematic of a delayed coking unit and on-stream factor — a major consideration in any residue upgrad- A wider and more intense residue conversion technologies, ing process because of the difficult requirement for the deployment of keeping the intentions of a global nature of the feedstock. emissions reduction technologies refiner in mind. The conversion Major refinery processes included may also act as a catalyst for new technology: in this evaluation were: investments. Modern hydroprocess- • Should be commercially proven • Delayed coking ing technology will eliminate the and reliable with a good on-stream • LC-Fining (a high-conversion need for expensive downstream factor residue hydrocracking process) remediation technologies. • Should maximise the most valua- • Residue desulphurisation (RDS) It is our view that refining should ble product (diesel) while retaining • Solvent deasphalting (SDA) be viewed as an ongoing business, the capability to address niche • Combinations of the above, along where long-term average margins product demands for the foreseea- with secondary processes such as and product price differentials will ble horizon hydrocracking, residue catalytic support the investments that are • Should be flexible to handle more cracking (RFCC) and gasification needed. difficult feedstocks (VR and coke), FCC feed/product • Should be environmentally desulphurisation and various Residue upgrading technologies compliant to meet future stringent gasoline-producing processes. In view of the increasingly stricter specifications In the studies we conducted for regulations expected in the near • Should have enough complexity various clients, the residue conver- future, along with the emerging so that the refinery remains profita- sion technologies that rose to the trends in product demand, CLG ble when margins remain depressed forefront were delayed coking, LC- evaluated multiple combinations of for prolonged periods (based on Fining and RDS. The screening www.ptqenquiry.com 76 PTQ Q3 2011 for further information www.eptq.com Advantages and disadvantages of delayed coking Advantages Disadvantages Lower on plot capital investment compared to hydrogen addition processes Coke handling, plot area limitations, and transportation and logistics Can handle very poor-quality (high in contaminants) feeds Additional environmental health and safety (EHS) requirements Widely used, with many references Hydrogen addition still required to upgrade products and the process does not share the same process platform as other hydroprocessing units Favoured in low crude oil price environment Loss of liquid yield compared to hydrogen addition processes No residual liquid product to deal with Coke disposition is a major issue Table 1 phase quickly ruled out several Installed lC-Fining units technologies as being too expensive, such as gasification, or not geared Start-up Client BPSD unconverted oil towards maximising diesel, the 2011 Shell Canada 47 300 Stable HSSC product of choice. A brief descrip- 2010 GS Caltex 60 000 Stable FO tion of the primary upgrading 2007 Neste Oil 40 000 Stable FO 2003 Shell Canada 79 000 Stable HSSC processes follows. 2000 Slovnaft 23 000 Stable LSFO 1998 AGIP Petroli 25 000 Stable LSFO Delayed coking 1988 Syncrude Canada 40 000 Coker feed Delayed coking is the most widely 1984 BP-Amoco 75 000 Coker feed Total 8 units 389 300 used residue conversion technology and is particularly valuable when a long-term off-take arrangement for Table 2 coke exists. Almost every major grassroots refinery in the world has VGO. HCGO is either sent to a FCC considered it as a primary residue feed pretreater (in a gasoline- Catalyst addition conversion process, with the excep- oriented refinery) or a hydrocracking Effluent tion of locations such as Scandinavia, unit (in a diesel-oriented refinery). line Thermowell Western Europe and Eastern The coke produced by a standalone Density nozzle detector Canada, where coking units are not delayed coker (see Figure 2) is lower radiation preferred. Fuel-grade coke is used in value fuel-grade coke. If a hydro- source infrastructure projects (cement, processing unit such as an LC-Fining well power) and demand remains robust unit precedes the delayed coking Density detectors in developing countries. However, unit, the coke produced from the Normal with even more large coking units delayed coking unit can be of supe- bed level coming online, coke demand could rior anode-grade quality, suitable for come under pressure. use in the aluminium industry. Vacuum residue, normally Table 1 shows the main advantages Skin destined for fuel oil, is thermally and disadvantages of the delayed TCs cracked to obtain nearly 70% of coking process. distillate products. All distillate Catalyst products require further hydro- lC-Fining withdrawal processing to make finished The LC-Fining process is a resid- line Feed Recycle products. Coker naphtha requires uum conversion process that pump special and more severe hydro- hydrocracks the most difficult, processing compared to straight-run heavy, lower-value hydrocarbon naphtha. Light coker gas oil (LCGO) streams such as petroleum residua, that boils in the diesel boiling range heavy oils from tar sands and shale Reactor temperature 410–440°C has a much higher nitrogen content oils to lighter, more valuable prod- Reactor pressure 110–180 bar compared to straight-run diesel and ucts such as VGO, diesel and Resid conversion 55–80% operating pressures required for naphtha. The process involves an Hydrogen P. P. 75–125 bar hydroprocessing are relatively ebullated-bed reactor (see Figure 3) Chem H2 higher. Heavy coker gas oil (HCGO) that completely mixes oil and consumption 35–300 Nm3/m3 boils in the vacuum gas oil (VGO) hydrogen.
Details
-
File Typepdf
-
Upload Time-
-
Content LanguagesEnglish
-
Upload UserAnonymous/Not logged-in
-
File Pages8 Page
-
File Size-