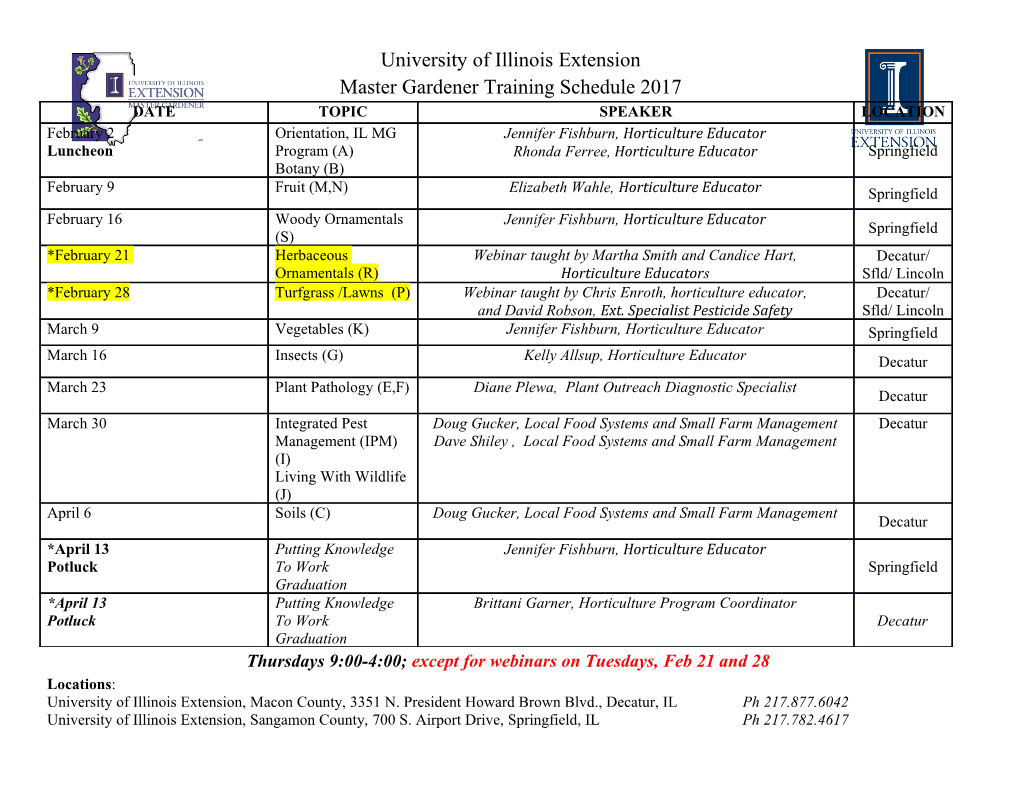
ISIJ International, Vol. 49 (2009), No. 12, pp. 1960–1966 Puddling: A New Look at an Old Process Merton C. FLEMINGS1) and David V. RAGONE2) 1) Professor, Toyota Professor Emeritus, MIT, Room 4-415, Massachusetts Institute of Technology, Cambridge, MA 02139, USA. E-mail: fl[email protected] 2) Senior Lecturer Emeritus, MIT, President Emeritus, Case Western Reserve University, 8 Hillside Road, Wellesley, MA 02481, USA. E-mail: [email protected] (Received on May 7, 2009; accepted on September 9, 2009) Throughout most of the 19th century, the process of choice in the west for producing wrought iron and steel was “puddling” of cast iron. A major development of the process, “wet puddling”, became wide- spread commercially beginning in 1830. That process is examined quantitatively using modern thermody- namic, solidification and rheologic understanding. The ‘clearing’ and ‘boiling’ steps are considered in detail. In the ‘clearing’ step, the silicon is oxidized (by iron oxide) resulting in bath heating. Subsequent carbon re- moval from the melt, prior to initiation of solid iron solidification results first in the ‘low boil’, with simultane- ous melt cooling. Then, as decarburization continues, solidification of iron begins, and with it, the ‘high boil’, with vigorous gas evolution and significant temperature increase. The importance of the iron solidification in promoting the decarburization reaction has not, in our opinion been fully understood heretofore. The lower the carbon content at the start of the boil, the higher the final melt temperature, and the lower the carbon content in the fully solid iron. During the high boil the four phase slurry of slag, liquid iron, solid iron and gas is thixotropic in nature, readily agglomerates, and possesses a low viscosity up to fractions solid of 0.2–0.3, with that viscosity rising rapidly at higher fractions solid. Comparison of the model presented with observa- tions from the actual puddling process is made. The qualitative and quantitative model presented agrees in general outline with the historical record and serves to strengthen our respect for those master puddlers who could control such a complex process with little other than their senses to guide them. KEY WORDS: wrought iron; puddling; iron history. ceed that of wrought iron in Great Britain, and wrought 1. The Puddling Process iron continued to be produced commercially until well into 1.1. Historical Aspects the 20th century. Henry Cort, in 1784, perfected the process of decarburiz- Hall’s development is often referred to as the ‘wet pud- ing cast iron in a reverberatory furnace fired with coke, the dling process’ to differentiate it from the earlier ‘dry pud- oxidizing agent being the furnace atmosphere.1,2) The dling process’ which involved much less slag. Both process required constant stirring and so came to be known processes have been described in a number of recent and as puddling. After about 1795, British iron masters quickly contemporaneous publications, as summarized by Gale,1) adopted Cort’s process, and by 1815 British annual wrought Turner,4) Gordon,5) Morton and Birt6) and Barraclough.7) iron output had risen to 140 000 tons, almost a five fold in- Our attention was first drawn to Hall’s process on realiz- crease from the production in 1788 of 29 000 tons.3) While ing its apparent uniqueness—that the driving force for the Cort’s process represented a significant advance over earlier chemical refining is directly impacted by crystallization of processes for producing wrought iron from cast iron, it was the iron. In this paper we examine quantitatively, using slow, wasteful of iron, and could be used only with a lim- modern thermodynamics and kinetics, this ‘wet puddling’ ited range of compositions of cast iron. process, aiming to highlight its originality and importance. The next, and last, major inventive contribution to the Hall’s process has often been viewed as a minor improve- puddling process was that of Joseph Hall, building on a ment on that developed originally by Cort, but from a met- suggestion of Rogers.1) His essential change was replace- allurgical point of view, it is a wholly new and innovative ment of the silica furnace bottom by iron oxide. The critical process, involving different chemistry and process path, contribution from a chemical reaction standpoint was oxi- with concomitant significant advantages in cost and quality. dation of the carbon, not by the oxygen from the furnace at- This remarkable process built on the work of others over mosphere, but by that from iron oxide. Hall had begun his the previous century, combined a number of non-obvious experiments in 1811, and by 1830 was able to apply the essential elements, and permitted large scale manufacture process commercially. His process was spectacularly suc- of high quality iron by artisans without recourse to modern cessful and was to become the predominant ironmaking means of sensing and control. process for all the years wrought iron remained a significant engineering material. Only in 1885 did steel production ex- © 2009 ISIJ 1960 ISIJ International, Vol. 49 (2009), No. 12 burns in small flames called ‘puddler’s candles’. This is the 1.2. Melting and Rabbling ‘high boil’. In the words of Davis: ‘This formation of gas in As is to be expected, details of wet puddling practice the molten puddle causes the whole charge to boil up like changed somewhat over time and differed from location to an ice cream soda. The slag overflows. Redder than straw- location. Differences, for example, were in furnace size, berry syrup and as hot as the fiery lake in Hades it flows to components of the furnace lining (the ‘fettling’), and when the rim of the hearth and out through the slag hole. My and if additions were made during the process. Comparison helper has pushed up a buggy there to receive it. More than of descriptions of puddling dating to the 1870’s with those an eighth and sometimes a quarter of the pig iron flows off of puddling in the early 20th century, indicates a significant in the slag and is carted away. Meanwhile I have got the job increase in heat size and decrease in cycle time. Nonethe- of my life on my hands. I must stir the boiling mess with all less, the furnace design and puddling process were essen- the strength of my body’. tially unchanged, including a furnace lining containing a The puddler increases the stirring of the bath while de- high percentage of iron oxide, a cooled metal base plate on creasing the heat until the metal ‘comes to nature’. Again, which the furnace lining rested, and a vigorous boil during in Davis’ words, ‘Little spikes of pure iron like frost spars the carbon reduction stage. glow white-hot and stick out of the churning slag. These Several eyewitness accounts of puddling in the early to must be stirred under at once; the long stream of the flame mid 20th century provide an excellent overview of the from the grate plays over the puddle, and the pure iron if process. Gale1) and Morton and Birt6) have given first hand lapped by these gases would be burned up. Pasty masses of detailed accounts of puddling in Great Britain and Davis8) iron form at the bottom of the puddle. These would stick has done the same for puddling in the United States. In ad- and become chilled if they were not constantly stirred. The dition, Gordon,5) Lankford9) and Bray10) have summarized whole charge must be mixed and mixed as it steadily thick- accounts of others. Following is a composite description of ens so that it will be uniform throughout’. As the reaction the puddling operation one would have seen in an iron nears completion it becomes pasty and hard to work. The works during these later years of puddling, based on ac- change occurs rapidly, over a period of 6–8 min. With the counts of Gordon, Bray and Davis. elimination of the carbon nearly complete, the boiling sub- The puddler first fires his furnace, which is a reverbera- sides and the apparent volume of the slag decreases, called tory furnace capable of handling a 250 kg cast iron charge. ‘the drop’ by puddlers. Grains of iron, each enveloped in A furnace lining comprising usually mostly Fe3O4 forms slag, appear as clusters as the slag drains away from the sur- the melting basin. It is sintered to form a monolithic struc- face. The metal has ‘come to nature’, and is ready for ture, with the aid of some added iron or slag. The lining balling. rests on an air cooled iron base. To start a heat, the puddler shovels the 250 kg of pig iron 1.4. Final Steps into the furnace, and also adds some mill scale (iron oxide). With the temperature under the melting point of iron, the He and his helper then do their best to seal all openings to puddler next separates the pasty mass of metal and slag into minimize entrance of oxygen to the furnace interior and three ‘balls’, transports them with the aid of his helper to a open the damper to get maximum heating and minimum “squeezer”, where much of the slag is removed. Then, after oxidation of the melting iron. Charging the furnace takes shaping and passing the metal through a series of roughing about 2 min. The heating and melting another 30 min. The and finishing rolls, the resulting product is ‘muck bars’, puddler then lowers the damper to keep heat input low and iron bars of about 20 mm thick, by 60–200 mm wide, by make the atmosphere less oxidizing, while his helper begins 5–9 m long.
Details
-
File Typepdf
-
Upload Time-
-
Content LanguagesEnglish
-
Upload UserAnonymous/Not logged-in
-
File Pages7 Page
-
File Size-