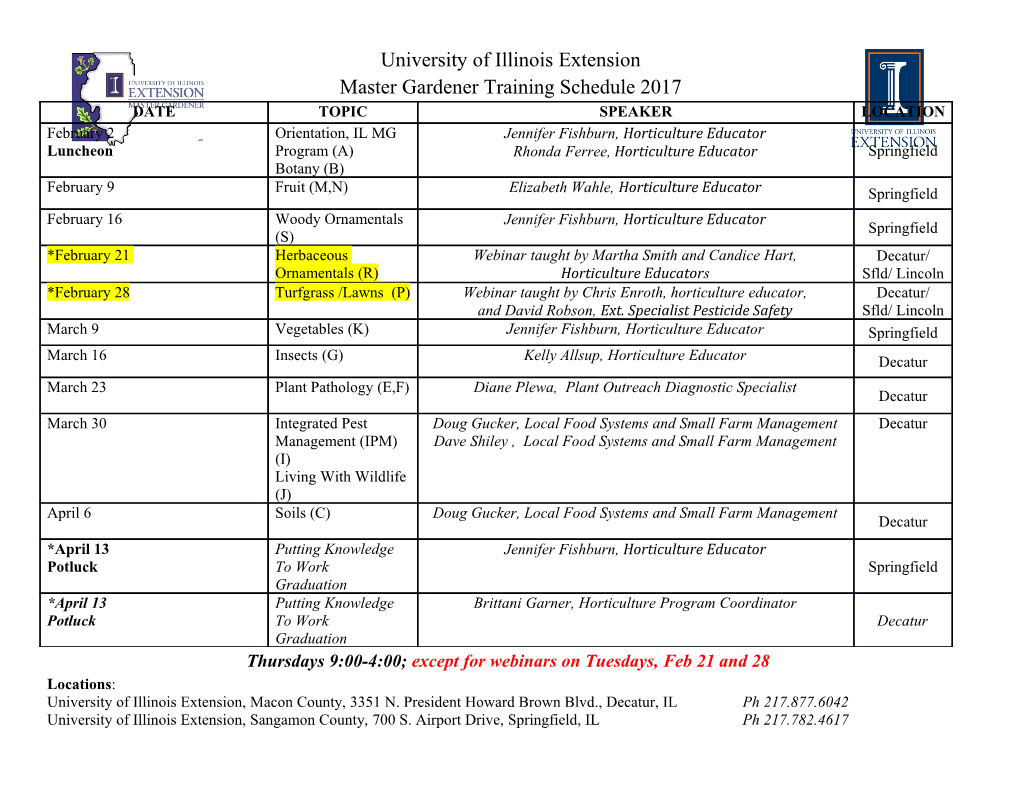
THE EFFECT OF ADDING ASPHERIC SURFACES TO A FIXED FOCAL LENGTH LENS SYSTEM by Rhiannon Katarina Jenkins ______________________ A Report Submitted to the Faculty of OPTICAL SCIENCES (GRADUATE) In Partial Fulfillment of the Requirements for the Degree of MASTER OF SCIENCES In the Graduate College UNIVERSITY OF ARIZONA 2016 0 ACKNOWLEDGEMENTS I would like to thank Jeremy Govier for his help with designing these lenses and being a great support throughout the duration of this project, Jose Sasian for his help in structuring the written project and discussing the project with me and to Jim Schwiegerling for being a part of the final committee. I am greatly indebted to Edmund Optics Inc. for funding my Masters degree at the University of Arizona. I would especially like to thank Robert Edmund for first suggesting that I could move out to the US to undertake this course. 1 TABLE OF CONTENTS LIST OF FIGURES………………………………………………………………………………………….…..3 ABSTRACT…………………………………………………………………………………………………….….5 1. THE OPTICAL TRANSFER FUNCTION………………………………………………………….…6 History of the OTF…………………………………………………………………………………….…6 Concepts of the OTF…………………………………………………………………………………...9 Linear Shift Invariant Approach to the OTF……………………………………………….11 Tolerancing Using the MTF……………………………………………………………………….12 2. ASPHERIC LENSES…………………………………………………………………………………..…14 History of Aspheric Lenses………………………………………………………………………..14 Describing Aspheric Surfaces…………………………………………………………………….17 Manufacturing Aspheres……………………………………………………………….………….18 3. RESULTS……………………………………………………………………………………………………22 The Original Lens with all Spherical Surfaces…………………………………………….22 Re-Design Using a Single Aspheric Surface………………………………………..………23 Re-Design Using Two or More Aspheric Surfaces………………………………………31 4. CONCLUSION…………………………………………………………………………………………….33 APPENDIX 1……………………………………………………………………………………………………34 REFERENCES…………………………………………………………………………………………………..41 2 LIST OF FIGURES Figure 1.1 1951 USAF resolution test target imaged with progressively worsening resolution. (6) Figure 1.2 Representation showing an imaging system forming a sinusoidal image. (6) Figure 1.3 Spread of OTF data measured for a 50mm PCX lens by 13 separate laboratories. (7) Figure 1.4 Schematic of the linear shift invariant system analysis of an optical system. (8) Figure 1.5 Illustration of the difference between square and sinusoidal spatial frequencies. (9) Figure 1.6 The MTF for a 12.5mm focal length micro video lens calculated in Zemax. (10) Figure 1.7 A defocused image of a star pattern with visible spurious resolution. (10) Figure 1.8 Diagram depicting how lower resolution results in spurious resolution. (11) Figure 1.9 The MTF for a defocused 12.5mm focal length micro video lens calculated in Zemax, with a discontinuity at around 275cycles/mm. It would display spurious resolution in the approximate range 275-500cycles/mm. (11) Figure 1.10 Convolution theorem. (12) Figure 2.1 Depiction of a lens displaying spherical aberration, on the left and a corrected asphere on the right. (14) Figure 2.2 Example of a Cartesian oval. (15) Figure 2.3 Lens design #4 from Sloan and Hopkins 1967 paper. (16) Figure 2.4 Comparison of Double Gauss lens performance with variation in asphere placement. (17) Figure 2.5 Table of conics, Cyclopaedia 1728. (17) Figure 2.6 Descartes’ aspheric grinding machine (1638). (19) Figure 2.7 Active fluid jet polishing by OptoTech. (19) Figure 2.8 Hybrid moulding technique as utilised by Edmund Optics Inc. (20) Figure 3.1 The original #59-870 with all spherical surfaces. (22) Figure 3.2 Lens data for the #59-870. (22) Figure 3.3 MTF for #59-870. (23) Figure 3.4 Design #1 with the highlighted surface aspherized. (23) Figure 3.5 MTF data for Design #1. (24) Figure 3.6 Design #2 with the highlighted surface aspherized. (24) Figure 3.7 MTF data for Design #2. (24) Figure 3.8 Design #3 with the highlighted surface aspherized. (25) 3 Figure 3.9 MTF data for Design #3. (25) Figure 3.10 Design #4 with the highlighted surface aspherized. (25) Figure 3.11 MTF data for Design #4. (26) Figure 3.12 Design #5 with the highlighted surface aspherized. (26) Figure 3.13 MTF data for Design #5. (26) Figure 3.14 Design #6 with the highlighted surface aspherized. (27) Figure 3.15 MTF data for Design #6. (27) Figure 3.16 Design #7 with the highlighted surface aspherized, the original design is on the left and the re-sized version on the right. (27) Figure 3.17 MTF data for Design #7. (28) Figure 3.18 Design #8 with the highlighted surface aspherized. (28) Figure 3.19 MTF data for Design #8. (28) Figure 3.20 Design #9 with the highlighted surface aspherized. (29) Figure 3.21 MTF data for Design #9. (29) Figure 3.22 Design #10 with the highlighted surface aspherized. (29) Figure 3.23 MTF data for Design #10. (30) Figure 3.24 Design #11 with the highlighted surface aspherized. (30) Figure 3.25 MTF data for Design #11. (30) Figure 3.26 Design #12 with the highlighted surface aspherized. (31) Figure 3.27 MTF data for Design #12. (31) Figure 3.28 Table showing the MTF performance of all designs, listing the aspheric deviation in µm for all aspherized surfaces. (32) 4 ABSTRACT In imaging applications there is a growing demand for higher performance imaging lenses that are able to meet the demands of high resolution sensors. MTF is an important performance metric used to describe the performance of an imaging lens. MTF is especially important in the design phase, since optical design programs such as Zemax can quickly calculate the theoretical MTF in real time as the design is progressing and many designs will use MTF as a criteria for specifying the final design. Aspheric surfaces are used to reduce optical aberrations in optical systems and are, if carefully designed, able to correct the optical performance of an optical system, pushing the performance closer to the diffraction limit. This project is concerned with the redesign of a 16mm fixed focal length lens that uses all spherical surfaces, to accommodate one or more aspheric surfaces and investigating the effect that this has on the MTF performance of the lens with the aim of producing a design that has an improved optical design and is suitable for manufacture using industry standard machinery. 5 1. THE OPTICAL TRANSFER FUNCTION ‘The Optical Transfer Function (OTF) is the frequency response, in terms of spatial frequency, of an optical system to sinusoidal distributions of light intensity in the object plane; the OTF is the amplitude and phase in the image relative to the amplitude and phase in the object as a function of frequency, when the system is assumed to respond linearly and to be space invariant.’ [1] History of the OTF Before the introduction of the OTF as a standardized way to define the resolution and contrast of an imaging system, resolution was thought of and tested in terms of blur circles and bar charts, the most famous example of which is the 1951 USAF resolution test chart. Figure 1.1 1951 USAF resolution test target imaged with progressively worsening resolution [2]. Optical design at this time depended solely on geometrical ray tracing and even after the development of wave theory, it was not immediately implemented into design techniques. In fact modern computational ray-tracing programs still use geometrical calculations as the main basis of all their algorithms. However, it has long been known that traditional geometric ray tracing is an approximation that does not take diffraction into account, particularly when the aberrations are small and the lens is diffraction limited [3]. Imaging systems output sinusoidal intensity patterns, such as the distinctive Airy disc that is formed when an optical system images a point source [4, 5]. Figure 1.2 Representation showing an imaging system forming a sinusoidal image [6]. Calculation of the OTF requires consideration of the shape of the wavefront at the exit pupil, which must be done using wave theory analysis of the system. However, in the 19 th century, mathematical methods were such that although a number of optical systems had been worked out using wave theory and were found to be in accordance with observation, this involved lengthy integration and 6 was a slow process. Although Fourier published his breakthrough paper as early as 1807 [7], in which he modelled all functions using trigonometric series and Gauss demonstrated the first fast Fourier transform in 1805 [8], it was only in 1946 that Duffieux first demonstrated the use of the convolution theorem and the point spread function to calculate the OTF and his book on the subject was widely used as a practical source book in this field for many years [9]. Another important advance occurred in 1938 when Friesser suggested that instead of a bar chart, the object target should have a sinusoidal grey scale profile, instead of an abrupt black and white one, so that the form of the image would have the same form as the object and this is the concept that is still used in the OTF today [10]. In the 1950s the OTF was not yet in common use, but it was during this decade that instrumentation for measuring the OTF was greatly advanced. By the end of the decade 2 main methods for OTF measurement were considered the most useful to the industry. One method was to incoherently illuminate a sinusoidal object with a known variable spatial frequency and constant contrast. The object was brought into focus by the test lens and the contrast was measured in the image plane using a narrow slit and a photocell. The second method used a very similar setup, but the light was passed through the system in the reverse direction – the slit was illuminated and followed by a sinusoidal mask that chopped the image. Again, the result was detected by a photocell. Experimental complications arose using this method in the construction of truly sinusoidal object, including a test at 0 cycles/mm and measuring at low light levels, but also independent of room lighting.
Details
-
File Typepdf
-
Upload Time-
-
Content LanguagesEnglish
-
Upload UserAnonymous/Not logged-in
-
File Pages44 Page
-
File Size-