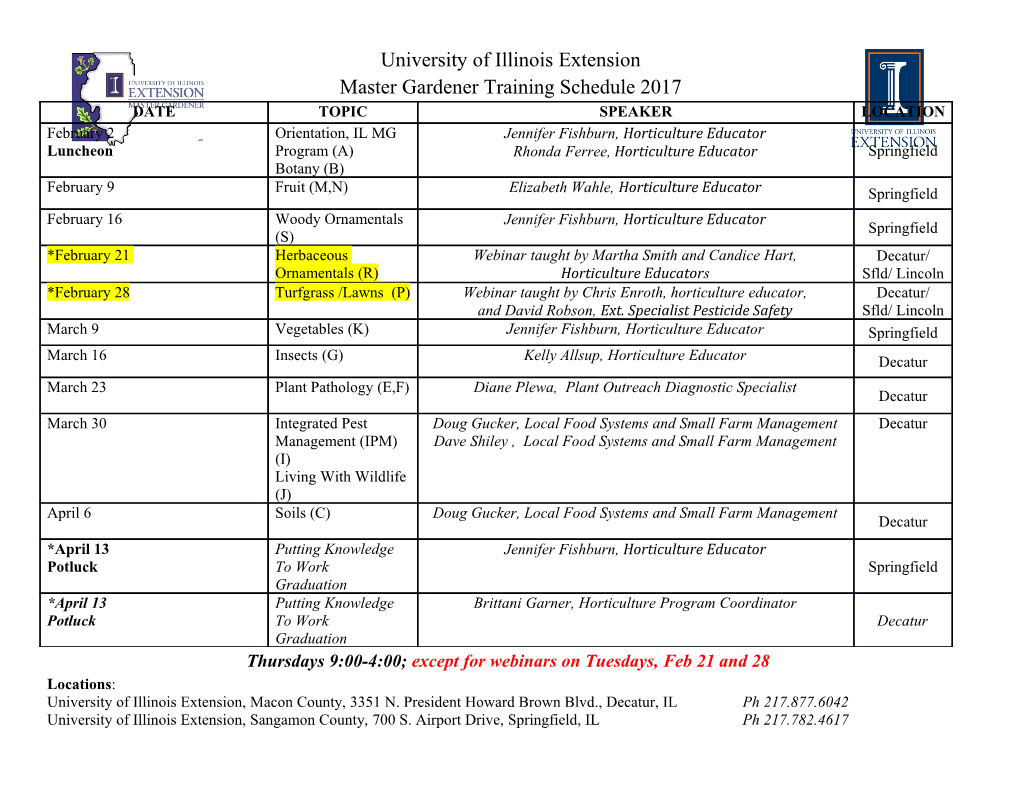
Aeroelasticity & Experimental Aerodynamics (AERO0032-1) Lecture 6 Vortex Induced Vibrations T. Andrianne 2017-2018 Aeroelasticity = Study of the interaction of inertial, structural and aerodynamic forces Applications on aircrafts, buildings, surface vehicles etc. Inertial Forces Structural dynamics Flight Dynamics Dynamic Aeroelasticity Collar’s triangle Structural Forces Aerodynamic Forces Static Aeroelasticity 1 Flow separation Airfoil/wing aeroelasticity • Divergence • Flutter Bluff-body aeroelasticity • Vortex Induced Vibration • Galloping 2 VIV Vortices … Flow visualizaon of vor,ces shed behind a cylinder 3 VIV … induce vibrations Vortex-induced vibraons 4 Today’s lecture Dimensional analysis Examples of VIV Flow around static cylinders Effect of a prescribed motion of the cylinder Free vibration: VIV Modelling VIV Lock-in mechanism 5 Today’s lecture Dimensional analysis Examples of VIV Flow around static cylinders Effect of a prescribed motion of the cylinder Free vibration: VIV Modelling VIV Lock-in mechanism 6 Dimensional analysis Non-dimensional variables • Geometry l = length / width D • Dimensionless amplitude A vibration amplitude / diameter D U Large Ur à Quasi-steady assumption • Reduced velocity U ∞ r = fD Small Ur (< 10) à Strong fluid-structure interaction U∞ f D U A ∞ m 7 Dimensional analysis m m S S = susceptibility of flow induced • Mass ratio mr = = 2 mF ρπ D / 4 vibrations mS = mass (p.u. length) of the structure [kg/m] ρ = fluid density [kg/m3] U D • Reynolds number Re = ∞ = inertial / viscous forces ν ν = kinematic viscosity of the fluid [m2/s] à Measure of the boundary layer thickness à Measure of the transition between laminar and turbulent flows U Ma ∞ • Mach number = c = tendency of the flow to compress when it encounters a structure In this course : incompressible flows à Ma < 0.3 8 Dimensional analysis energy dissipated per cycle • Damping factor (classically) η = S 4π × total energy of the structure YN ln(YN /YN+1) = 2πηS YN (linear system) m When Fluid-Structure interactions are concerned à “reduced damping” or Scruton number ≈ mr ×ηS 9 Dimensional analysis Motion of a linear structure in a subsonic, steady flow Described by : → A = F l ,U , Re, m ,η D ( D r r S ) • Geometry l D • Reduced velocity Ur • Dimensionless amplitude A D • Mass ratio mr • Reynolds number Re • Damping factor ηS Source FIV1977 VIV Galloping (Lecture 2) 10 Today’s lecture Dimensional analysis Examples of VIV Flow around static cylinders Effect of a prescribed motion of the cylinder Free vibration: VIV Modelling VIV Lock-in mechanism 11 VIV examples – in air • Bridges Great-Belt bridge (Denmark) • Chimneys • High rise buildings Burj Khalifa (Dubai) 12 VIV examples – in water / 2 phases flows • Risers source : Imperial college • Heat exchangers source : Sandvik 13 VIV examples : Great-Belt bridge Unacceptable VIV motion (~ 40cm) during final construction stage at low (and frequent) wind speeds (~8m/s) (Larsen 2000) 14 VIV examples : Great-Belt bridge (Frandsen 2001) (Larsen 2000) 15 From 3D to 2D • Vortex shedding is essentially a 3D phenomenon à Flow components in the Z-direction à Geometric variation of the structure à Dynamic behaviour of the structure • 2D analysis as a starting point to understand VIV : Even on 3D structures, 2D approaches are carried out (flow visualization, load analysis) • A/D >> à 2D dominated Structural motion takes the control of aerodynamics Sumer 2006 16 Dimensional analysis Motion of a 2D linear structure in a subsonic, steady flow Described by : A F U , Re, m , → D = ( r r ηS ) Great Belt bridge D U∞ m Other parameters: • Surface roughness of the structure (for rounded shapes) • Turbulence intensity of the upstream flow à Effect on the wake, hence of the lift and on the VIV 17 Today’s lecture Dimensional analysis Examples of VIV Flow around static cylinders Effect of a prescribed motion of the cylinder Free vibration: VIV Modelling VIV Lock-in mechanism 18 Flow around a static cylinders Lifting cylinder (potential flow theory) * 2 - 2 2Γsinθ $ Γ ' à Steady lift force C =1−,4sin θ + +& ) / p RV 2 RV +, π ∞ % π ∞ ( ./ à No drag (D’Alembert Paradox) Γ cl = RV∞ Viscous effects à Flow separation 19 Flow around a static cylinders Creeping flow : vorticity created in the BL is totally dissipated near the body Transition to turbulence Increasing Re = inertial / viscous forces Effect of viscosity in the vicinity of the body. Large amount of viscosity not dissipated near the body 20 Flow around a static cylinders How vortex shedding appears ? Flow separation • Flow speed outside wake is much higher than inside • Vorticity gathers in upper and lower layers • Induced velocities (due to vortices) causes this perturbation to amplify à Origin of the vortex shedding process = shear layer instability (purely inviscid mechanism) Vortex shedding = global instability : the whole wake is affected = robust : vorticity is continuously produced @ a well defined frequency (see Strouhal) 21 Flow around a static cylinders Strouhal number 600 400 fVS D S VS St ≡ f f U∞ 200 f = shedding frequency VS 0 0 5 10 15 20 25 30 D = cross dimension U ∞ U∞ = free stream velocity à Linear dependency of the shedding frequency with free stream velocity à St ~ cste in a limited range of Reynolds numbers ! 22 Flow around a static cylinders Aerodynamic forces à Impact of the shed vortices on the aerodynamic forces L D à Lift force varies at fVS à Drag force varies at ~ 2 fVS Sumer 2006 23 Flow around a static cylinders Aerodynamic forces • Lift coefficient is an image of the fluctuating vorticity in the wake (where the dominant frequency is fVS) rms à C (t) is characterized by f and C L L L f D à Dimensionless Strouhal number St = L U∞ L(t) rms rms St 2πU∞ CL (t) = 2 = 2CL sin(ωLt) = 2CL sin( t) 1/ 2ρU∞D D • Drag coefficient : typically fD ~ 2 fVS D(t) rms rms rms St 2πU∞ CD (t) = 2 = 2CD sin(ωDt) = 2CD sin(2ωLt) = 2CD sin(2 t) 1/ 2ρU∞D D 24 Flow around a static cylinders Aerodynamic forces Strongly Reynolds dependent ! L(t) rms CL (t) = 2 = 2CL sin(ωLt) 1/ 2ρU∞D rms St 2πU = 2C sin( ∞ t) L D D(t) rms rms CD (t) = 2 = 2CD sin(ωDt) = 2CD sin(2ωLt) 1/ 2ρU∞D rms St 2πU = 2C sin(2 ∞ t) D D 25 FIV2011 Today’s lecture Dimensional analysis Examples of VIV Flow around static cylinders Effect of a prescribed motion of the cylinder Free vibration: VIV Modelling VIV Lock-in mechanism 26 Oscillating cylinder à Cylinder forced to move Imposed motion : y(t) = Asin(2π f f t) A = Amplitude ff = Forcing frequency Order of magnitude of the diameter (D) Varying around the stac cylinder shedding 0 à A/D ~ 1 frequency (fVS ) à 0< f /f 0 < 2 f VS 0 fVS = vortex shedding frequency that would be observed with cylinder at rest (i.e. following the Strouhal relaon) Remember : Re has also a strong effect on the shedding process à Effect of the motion of the cylinder, for a given Re range. We can observe: Change in the flow pattern and in the shedding frequency 27 Oscillating cylinder : Patterns Williamson 2004 • Limited range of forcing frequency and amplitude: à Two single vortices (“2S mode”) • Higher forcing frequencies and amplitudes: à Two pairs of vortices (“2P mode”) • Even higher frequencies and amplitudes : non-symmetric “P+S mode” 28 Oscillating cylinder : Frequency 0 Around ff / fVS ~ 1 à No change in pattern à But effect on the shedding frequency fVS f D i.e. f does not follow anymore the Strouhal relation St = VS VS U ∞ For a given Reynolds number and amplitude of imposed motion (A) 0 fVS /fVS fVS = ff ff is increased 1 fVS is measured 0 Around ff / fVS ~ 1 à fVS = ff = Lock-in phenomenon 1 f /f 0 f VS (wake capture) !! Different from lock-in in VIV !! 29 Oscillating cylinder : Frequency Lock-in range mainly depends on the imposed amplitude (ratio A / D) FIV2011 A/D ì à Range ì 30 Oscillating cylinder : Lift force Imposed motion: y(t) = Asin(2π f f t) à The resulting lift force L(t) is not necessarily harmonic (idem static cylinder) But through a standard Fourier analysis, it can approximated by L (t) = L0 si n(2π f f t + ϕ ) = component of lift @ the forcing frequency (ff) 0 0 0 Driving parameters: A/D and ff /fVS à L0(A/D, ff /fVS ) and φ(A/D, ff /fVS ) Three different representations of the lift force : 1. Modulus and phase 2. Phased lift coefficients 3. Inertia and drag coefficients 31 Oscillating cylinder : Lift force 1. Modulus and phase 2. Phased lift coefficients C for A/D = 0.5 3. Inertia and drag coefficients L 5 CL (t) = CL sin(2π f f t + ϕ) 4 3 modulus phase 2 1 0 à both function of A/D and ff /fVS 0 0 ff /fVS max C 0 .5 .75 1 1.25 1.5 1.75 ( L ) for ff /fVS = 1 CL (A = 0) ϕ 2 270 180 1 90 0 -90 0 0 .5 1 1.5 2 A/D -180 0 .5 .75 1 1.25 1.5 1.75 ff /fVS adapted from Carberry et al. (2005) 32 Oscillating cylinder : Lift force 1. Modulus and phase y(t) Asin(2 f t) 2. Phased lift coefficients = π f 3. Inertia and drag coefficients CL (t) = (CL cosϕ)sin(2π f f t)+(CL sinϕ)cos(2π f f t) in phase with y (and - ! y! ) in phase with y! Conservative forces Non-conservative forces 0 à both function of A/D and ff /fVS à might lead to positive or negative work for A/D = 0.5 C sin CL cosϕ L ϕ 1 1 0 0 0 f /f 0 .5 .75 1 1.25 1.5 1.75 ff /fVS .5 .75 1 1.25 1.5 1.75 f VS adapted from Sarpkaya (1979) 33 Oscillating cylinder : Lift force 1.
Details
-
File Typepdf
-
Upload Time-
-
Content LanguagesEnglish
-
Upload UserAnonymous/Not logged-in
-
File Pages73 Page
-
File Size-