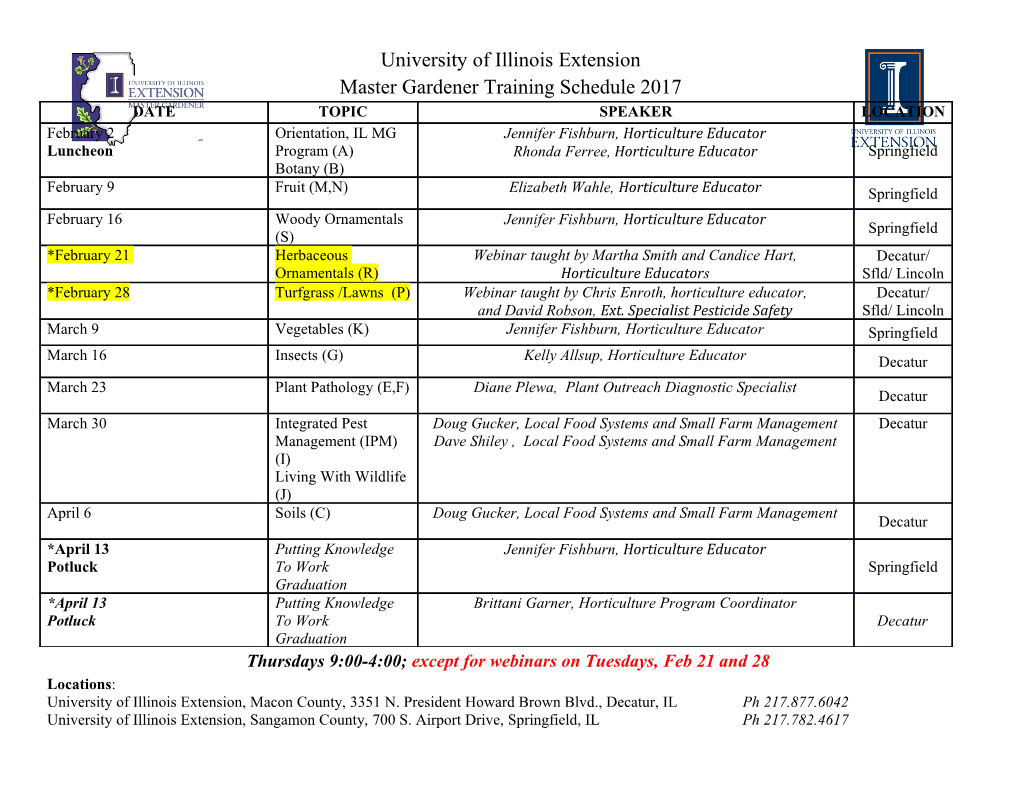
HSE Health & Safety Executive Availability, quality and standards of training for woodworking operators and supervisors Prepared by the Health and Safety Laboratory for the Health and Safety Executive CONTRACT RESEARCH REPORT 339/2001 HSE Health & Safety Executive Availability, quality and standards of training for woodworking operators and supervisors Colin Chambers, Nicola Worsell, Johanna Beswick, Linda Heritage and Becky Wu Health and Safety Laboratory Broad Lane Sheffield S3 7HQ United Kingdom The hazards associated with woodworking machinery and the means of safeguarding against them are well known and documented by the Health and Safety Executive (HSE) in a comprehensive series of free information sheets prepared by the Agriculture and Wood Sector - Woodworking Section. Nevertheless, the accident rate in the woodworking industry remains high. It is an industry in which employees have to regularly work with cutting tools or blades that are exposed. There is also a significant potential in the industry for ill-health caused by poor manual handling and exposure to dust. The proper use of guards and safe working practices are therefore essential in reducing the risk of serious accidents and ill health to a tolerable level. Training and good supervision are therefore fundamental to ensuring good health and safety. HSE needs to promote suitable training to the woodworking industry. The purpose of the research documented in this report was to: identify the training available to both operators and supervisors of woodworking machinery in particular; assess the suitability of this training in terms of quality and standards with reference to the nature of the industry; and identify barriers to training that exist in the industry and propose measures, which could be taken to improve the take-up of suitable training. This report and the work it describes were funded by the Health and Safety Executive (HSE). Its contents, including any opinions and/or conclusions expressed, are those of the authors alone and do not necessarily reflect HSE policy. HSE BOOKS © Crown copyright 2001 Applications for reproduction should be made in writing to: Copyright Unit, Her Majesty’s Stationery Office, St Clements House, 2-16 Colegate, Norwich NR3 1BQ First published 2001 ISBN 0 7176 2015 8 All rights reserved. No part of this publication may be reproduced, stored in a retrieval system, or transmitted in any form or by any means (electronic, mechanical, photocopying, recording or otherwise) without the prior written permission of the copyright owner. ii CONTENTS 1. INTRODUCTION ........................................... 1 1.1. BACKGROUND ............................................. 1 1.2. AIMS AND OBJECTIVES ..................................... 2 2. OVERVIEW OF WOODWORKING INDUSTRY ............. 3 3. AVAILABILITY OF TRAINING .............................. 5 3.1. IDENTIFICATION OF TRAINING PROVIDERS ................... 5 3.2. TRAINING CAPACITY ........................................ 9 3.3. ORGANISATIONS THAT OVERSEE TRAINING ................. 13 3.4. FUNDING FOR TRAINING ................................... 14 4. QUALITY OF TRAINING ................................... 16 4.1. REQUIREMENTS ........................................... 16 4.2. ASSESSMENT OF TRAINING ................................ 17 4.3. NATIONAL VOCATIONAL QUALIFICATION (NVQ) ............. 18 5. FURTHER INFORMATION FROM INDUSTRY ............. 20 5.1. FOCUS GROUPS ........................................... 20 5.1.1. Analysis of Telephone Recruitment Data ................... 21 5.1.2. Main findings from the Focus Groups ...................... 22 5.1.3. Comparison between telephone recruitment and focus group findings .......................................... 24 5.2. OPINIONS OF MEMBERS OF THE WOOD INDUSTRIES FORUM ....................................................... 24 6. EUROPEAN DIMENSION ................................. 28 6.1. APPROACH ACROSS EUROPE OF SMES TO TRAINING ..................................................... 29 6.2. POSSIBLE SOURCES OF EUROPEAN FUNDING TO EXPLORE TRAINING ISSUES ................................... 31 7. DISCUSSION .............................................. 32 7.1. APPROACH OF INDUSTRY TO TRAINING ..................... 32 7.2. AVAILABILITY OF TRAINING ................................ 33 7.3. QUALITY AND STANDARDS OF TRAINING ................... 34 7.4. BARRIERS TO TRAINING ................................... 35 8. SUGGESTED WAY FORWARD ........................... 37 9. CONCLUSIONS ........................................... 40 10. ACKNOWLEDGEMENTS ................................ 42 11. REFERENCES ........................................... 43 iii APPENDIX A: ADDITIONAL DATA ON WOODWORKING INDUSTRY IN THE U.K. ................... 46 APPENDIX B: ADDITIONAL DATA ON TRAINING PROVISION .................................................. 49 APPENDIX C: COMPREHENSIVE LISTING OF TRAINING PROVIDERS BY REGION AND COUNTY .................................................... 96 APPENDIX D: WOODWORKING ACCIDENT STATISTICS ................................................ 122 APPENDIX E: FOCUS GROUP INFORMATION ............. 125 E.1 FOCUS GROUP RECRUITMENT, QUESTIONS AND ANSWERS .................................................... 125 E.2 FOCUS GROUP QUESTIONS ............................... 130 E.3 EXAMPLE CONFIRMATION LETTER ......................... 134 E.4 ANALYSIS OF FOCUS GROUP DATA ........................ 136 APPENDIX F: CONTACTS IN THE UK AND EUROPE .................................................... 145 F.1 UK CONTACTS ............................................ 145 F.2 EUROPEAN CONTACTS .................................... 149 F.3 SUMMARY OF INFORMATION SUPPLIED BY EUROPEAN CONTACTS 155 ................................... 153 F.4 USEFUL WEBSITES ....................................... 155 iv 1. INTRODUCTION 1.1. BACKGROUND The hazards associated with woodworking machinery and the means of safeguarding against them are well known and documented by HSE in a comprehensive series of free information sheets [HSE 1992 to 1999] and by others e.g. the BWF guide to H&S [BWF, 2000] . Nevertheless, the accident rate in the woodworking industry remains high. In the previous 3 years there have consistently been over 600 major injuries and over 2,100 minor injuries resulting in over 3-days absence from work. Recent accident statistics, providing by HSE Strategy and Analytical Support Directorate are given in Appendix D. There is no indication of any sustainable downward trend. In 1996 HSE conducted a survey of accidents at woodworking machines reported under the Reporting of Injuries and Dangerous Occurrences Regulations 1992 (RIDDOR) [HSE 1999]. It found that over an 18 month period there were 1239 accidents at woodworking machines, over 30% involving amputations. 64% of the accidents occurred in the woodworking industry and the remaining 36% across all other industry sectors. There are also, in addition, various health problems caused by manual handling, noise, dust and vibration, associated with woodworking machines. In order to meet the targets of the Health and Safety Commission's "Revitalising Health and Safety" initiative [HSE 2000] a concerted effort aimed at the woodworking sector will be needed. Woodworking is one of the few, possibly only, remaining industries where employees have to work regularly with machinery where cutting tools or blades are necessarily exposed. There are four groups of classical woodworking machines identified by HSE as being associated with a high proportion of the total number of reported accidents: circular saws, vertical spindle moulders, planer/ thicknessers and band saws. Many companies contacted during the research documented in this report use at least one of these. The proper use of guards and safe working practices are essential in reducing the risk of serious accidents and health problems to a tolerable level. Training and good supervision are therefore fundamental to ensuring health and safety. Furthermore, adequate training of operators and supervisors is a requirement of the Provision and Use of Work Equipment Regulations (PUWER), and the Health and Safety at Work etc. Act 1974, and considered vital to ensure that safe working practices are followed. Training is also key in reducing the risk of injury from manual handling and dust, other significant causes of injury and ill-health in this sector. However, there are indications that the current level and standard of training is in decline, resulting in a serious skills shortage [Anon 2000, Hollyer 1999]. A survey by questionnaire conducted by the Wood Industry Forum (a national consultative group for the woodworking industry with representation from major trade associations, the GMB Trade Union, relevant National Training Organisations (CITB, FFINTO) and HSE) in line with the purpose1 for which the forum was set up revealed that one potential reason for this may be the lack of availability of suitable training courses. 1 To act as a voice for the industry to enable developments in health and safety to be discussed to make sure the action HSE takes is both practical and sound. The Forum is also an opportunity for the industry to alert HSE to national issues affecting health and safety.' 1 The woodworking industry is large, diverse and dominated by small businesses with less than 50 employees and the majority with less than 10. A recent report [HSE 1999] estimated that at the beginning of 1997 there were approximately 226,000 people employed in the industry
Details
-
File Typepdf
-
Upload Time-
-
Content LanguagesEnglish
-
Upload UserAnonymous/Not logged-in
-
File Pages162 Page
-
File Size-