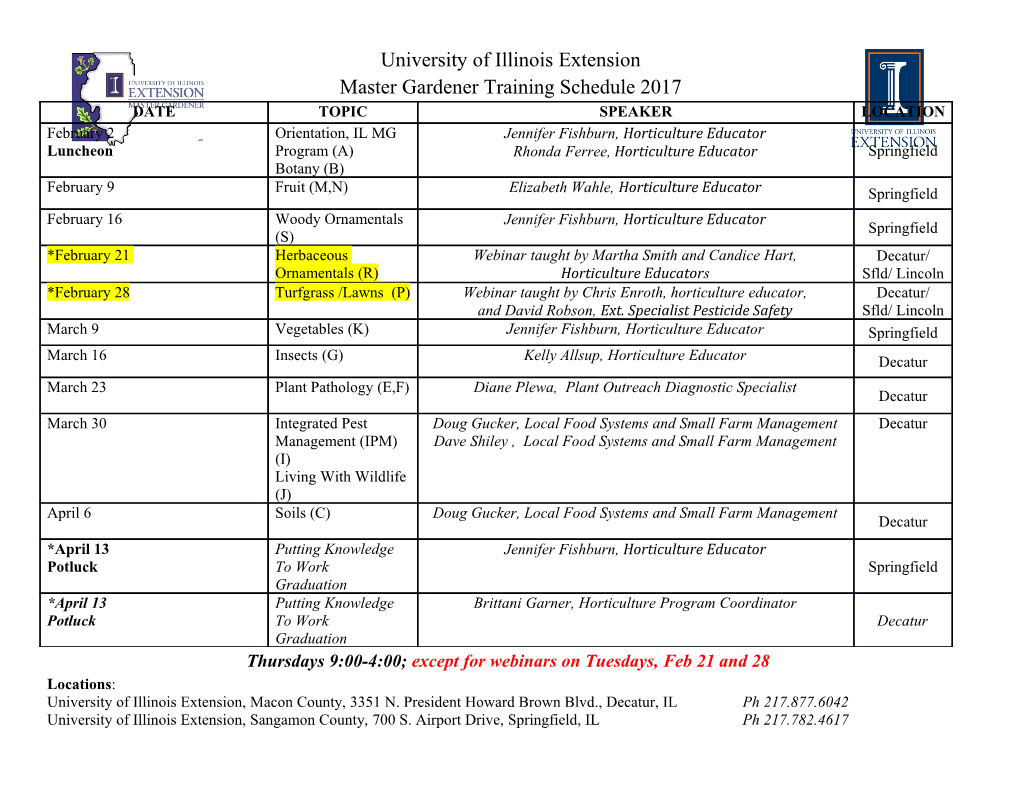
metals Review Overview of the Mechanical Properties of Tungsten/Steel Brazed Joints for the DEMO Fusion Reactor Diana Bachurina *, Vladimir Vorkel, Alexey Suchkov, Julia Gurova, Alexander Ivannikov, Milena Penyaz, Ivan Fedotov , Oleg Sevryukov and Boris Kalin Department of Materials Science, National Research Nuclear University MEPhI, Moscow, Kashirskoe shosse 31, 115409 Moscow, Russia; [email protected] (V.V.); [email protected] (A.S.); [email protected] (J.G.); [email protected] (A.I.); [email protected] (M.P.); [email protected] (I.F.); [email protected] (O.S.); [email protected] (B.K.) * Correspondence: [email protected] Abstract: A Demonstration (DEMO) thermonuclear reactor is the next step after the International Thermonuclear Experimental Reactor (ITER). Designs for a DEMO divertor and the First Wall require the joining of tungsten to steel; this is a difficult task, however, because of the metals’ physical properties and necessary operating conditions. Brazing is a prospective technology that could be used to solve this problem. This work examines a state-of-the-art solution to the problem of joining tungsten to steel by brazing, in order to summarize best practices, identify shortcomings, and clarify mechanical property requirements. Here, we outline the ways in which brazing technology can be developed to join tungsten to steel for use in a DEMO application. Keywords: DEMO; tungsten; reduced activation steel; brazing; divertor; First Wall; joining Citation: Bachurina, D.; Vorkel, V.; Suchkov, A.; Gurova, J.; Ivannikov, A.; Penyaz, M.; Fedotov, I.; Sevryukov, O.; Kalin, B. Overview of the Mechanical Properties of 1. Introduction Tungsten/Steel Brazed Joints for the The creation of a Demonstration (DEMO) thermonuclear reactor is the next step after DEMO Fusion Reactor. Metals 2021, the International Thermonuclear Experimental Reactor (ITER) with the final objective of a 11, 209. https://doi.org/10.3390/ fusion reactor power plant. As a result of the increased loads as compared to ITER, many met11020209 ITER solutions cannot be used in a DEMO, especially for the divertor and the First Wall (FW). This is due to higher heat and neutron fluxes. Therefore, tungsten is considered Academic Editor: suitable as a plasma-facing material (PFM) for both the divertor and the FW. Meanwhile, Kazuyuki Hokamoto steel is considered suitable as a structural material for a helium-cooled divertor [1–4] Received: 30 December 2020 and some FW concepts [5–7]. However, the direct connection of tungsten to steel is Accepted: 20 January 2021 difficult due to the difference in their coefficients of thermal expansion (CTE). Therefore, Published: 24 January 2021 the development of a reliable joining technology is of great interest. At the moment, diffusion bonding and brazing are the two main methodologies Publisher’s Note: MDPI stays neutral being considered to achieve such a joint. The first is carried out by means of hot isostatic with regard to jurisdictional claims in pressing [8,9] and spark plasma sintering [10,11]. The second is carried out by means published maps and institutional affil- of vacuum brazing, using foils [12,13], powders [14], and liquid-forming interlayers [15]. iations. Some of the advantages of considering brazing as a prospective technology include: • No deformation of the materials being joined, while during diffusion bonding the steel creeps up to 8% [16]; • Full integrity of the seam if the brazing alloy and brazing mode are chosen correctly, Copyright: © 2021 by the authors. Licensee MDPI, Basel, Switzerland. which is important for good heat transportation; • This article is an open access article The possibility of simultaneous heat treatment of the base materials and the braz- distributed under the terms and ing procedure; conditions of the Creative Commons • The possible replacement of defective elements after manufacturing and during pro- Attribution (CC BY) license (https:// duction [17]; creativecommons.org/licenses/by/ 4.0/). Metals 2021, 11, 209. https://doi.org/10.3390/met11020209 https://www.mdpi.com/journal/metals Metals 2021, 11, 209 2 of 11 • Low cost, i.e., no expensive equipment is required to carry out the process. There is a wide range of brazing methods available, from vacuum brazing to ohmic or induction brazing, even in air under flux, or blowing with an inert gas. Therefore, this technology is used in the assembly of ITER components and is cur- rently actively investigated with a view to its use in DEMO production. Meanwhile, a compensating interlayer is usually used [12,18,19] to reduce the residual stresses arising from differences in CTE. In this case, the development of brazing alloys suitable for two seams (tungsten/interlayer and interlayer/steel) is required. This work examines the state-of-the-art solution to the problem of joining tungsten to steel by brazing in order to summarize best practices, identify shortcomings, and clarify mechanical property requirements: • Section2 is a review of the working conditions of a tungsten/steel joint, including heat loads (Section 2.1), understanding the mechanical property requirements using Finite Element Analysis (FEM) (Section 2.2), and other requirements aside from the mechanical properties (Section 2.3); • Section3 gives an overview of the recent progress made in tungsten/steel brazing (attention is mainly paid to mechanical properties); • Section4 presents conclusions based on the overview of Sections2 and3. Finally, recommendations to all authors working on tungsten/steel brazing are given. 2. Working Conditions and Requirements 2.1. Heat Loads The most challenging application in which tungsten/steel joints are used is a helium- cooled divertor. The operating conditions of such a divertor are more extreme than the operating conditions of the FW, i.e., a heat flux of at least 10 MW/m2 [20]. This concept requires a tungsten/steel joint capable of withstanding a ≈700 ◦C operating temperature [2,21,22]. As a result of the very extreme operating conditions, Eurofusion’s target design was changed [23]. As a result, an ITER-type CuCrZr pipe concept was chosen for Research & Development (R&D) activities for divertor applications. However, a lot of studies have already been published on helium-cooled divertor concepts [13,15,24–27]. Tungsten surfaces are subjected to cyclic power loads by particles and radiation from plasma. It is expected that a heat load during steady-state operation will be no higher than 0.5–1 MW/m2 [28,29], but a load of 7 MW/m2 is expected in the inner and outer baffle regions [29]. The DEMO reactor will work in a quasi-stationary pulse mode, whereby the reactor starts up and shuts down for several cycles. The entire pulse [30] will take 7200 s, in which the plateau takes 7000 s. The number of pulses will reach 1000–10,000 cycles, which will require nearly 20 years of functionality at operating temperature. This means that not only base materials, but brazed joints must be resistant to long-term aging and creep. Additionally, the damage of plasma-facing components, due to the huge heat loads during disruptions, is of great concern in a DEMO. The power load of uncontrolled-edge localized modes (ELMs) is expected to be ~0.2–0.5 MJ/m2 over 0.6 ms [31], so the tungsten temperature can change from ≈280 to ≈630 ◦C in 1 s several times. Thus, resistance to thermocycling is very important for any tungsten/steel joints. 2.2. FEM Calculations The first and foremost requirement for any joint is to be strong enough for a chosen application. However, there are still no clear requirements for the mechanical properties of a tungsten/steel joint. Therefore, we decided to make an approximate calculation of a direct joint under minimal heat load (0.5 MW/m2), using the example of the Water Cooled Lithium Lead (WCLL) FW. We calculated a simplified part of the FW component by means of Finite Element Analysis in ANSYS Workbench 18.2. The test component and the boundary conditions for modeling are shown in Figure1. The temperatures used are mean values, designed for cooling and breeding in the WCLL blanket. The geometry was designed based on the Metals 2021, 11, x FOR PEER REVIEW 3 of 11 Metals 2021, 11, 209 ic-martensitic steel (RAFM) Rusfer were modeled, and the properties of the materials3 of 11 Metals 2021, 11, x FOR PEER REVIEWwere taken from [26]. 3 of 11 The following load steps were modeled: 1.parameters Cooling, presentedfrom a joining in [32 temperature]. The 2-mm-thick of 1100 °C tungsten to room and temperature reduced activation within 100 ferritic- s; 2.martensitic Increasing steel the (RAFM) temperature Rusfer and were pressure modeled, of the and breeder the properties and coolant of the within materials 1 h; were ic-martensitic steel (RAFM) Rusfer were modeled, and the properties of the materials 3.taken Power from ignition—with [26]. a heat load of 0.5 MW⁄m2 on the tungsten surface within 100 s. were taken from [26]. The following load steps were modeled: 1. Cooling, from a joining temperature of 1100 °C to room temperature within 100 s; 2. Increasing the temperature and pressure of the breeder and coolant within 1 h; 3. Power ignition—with a heat load of 0.5 MW⁄m2 on the tungsten surface within 100 s. FigureFigure 1. 1.TestTest component component (a ()a and) and boundary boundary conditions conditions for for FEM FEM model model (b (b). ). TheThe mesh following near the load contact steps wereregion modeled: for FEM calculations is shown in Figure 2. There are1. 10 inflationCooling, layers from aon joining each side; temperature the smallest of 1100 elements◦C to roomare 0.02 temperature mm by 0.2 within mm, and 100 the s; growth2. Increasing rate in the the vertical temperature direction and is 1.1.
Details
-
File Typepdf
-
Upload Time-
-
Content LanguagesEnglish
-
Upload UserAnonymous/Not logged-in
-
File Pages11 Page
-
File Size-