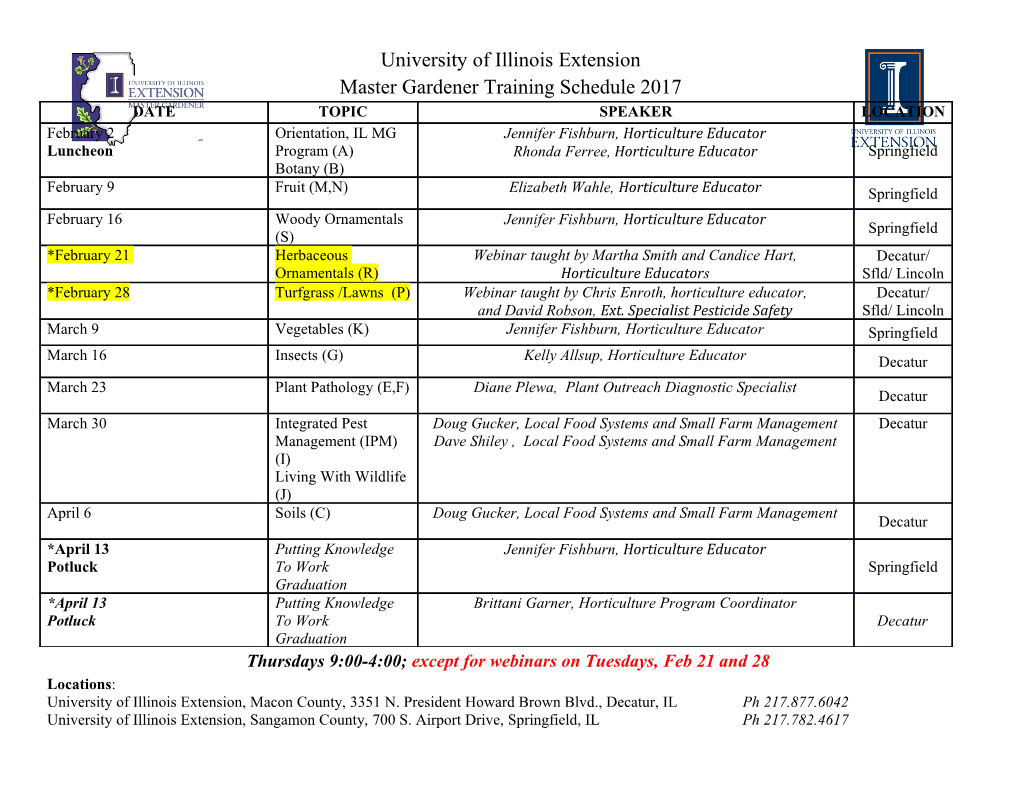
IPT Electronics : High Power Density Inverter 65kW at 250V (80kW at 300V) 500ARMS at 57C coolant, 450ARMS at 72C coolant 22kg => 3000W/kg (includes 3/2kW bidirectional DC-DC converter) Advanced power control circuits High accuracy torque control DC-DC Converter Traction Designed for Section Inverter automotive reliability Section INVERTER R&D System Simulation Framework – E-Drives Customer Specification Matlab/Simulink Controller Transmission Assumptions V DC V AC M M M T DC Supply Transmission Load IDC Inverter IAC Motor N M N T Motor Requirements Motor Electromagnetic Design Ansoft/Speed Performance Evaluation Motor Mechanical Design DyRoBeS Motor Thermal Design MotorCad/Ansoft Inverter Requirements Preliminary Design Matlab Transmission Requirements Preliminary Design Cost Evaluation INVERTER R&D Advanced Technology Developments Power Semiconductor Packaging Design & Manufacturing INVERTER R&D ECOSTAR POWER MODULE FACILITY Spatial Requirements I n t e R r e Silicon c l Efficiency o i a n b n i e l i c t y y t i o n n Thermal & Inductance Paths • Thermal Stress on wire bonds • INVERTER R&D Inductive effects in Power Module Thermal and Mechanical Properties of Each Layers Material Density Thermal condutivity Specific heat Young’s modile CTE (kg 3m ) (W/m K) (J/kg K) (GPa) (ppm/K) Copper 8979 389 381 112.9 16.4 AlSiC 3100 150 880 227 6.8 60Sn/ 40 Pb solder 8470 50 364.5 29.8 21.1 DBC AIN 8930 170 431 327 2.5 95Pb/ 5Sn solder 11100 35 133.7 20.4 25.1 Thermal grease 2703 0.735 796 0.011 16.4 Aluminum 2760 237 858.8 70 23.6 Silicon 2330 153 @ 25 oC 702 112.9 2.54 119 @ 77 oC 98.9 @ 127 oC 76.2 @ 227 oC INVERTER R&D Thermal Resistance Predicted Using Numerical Tools In developing Ballard Custom Power Module with integrated pinfin baseplate, computational fluid dynamics (CFD) was used to simulate fluid flow along fins and heat transfer within solids. CAD model The predicted maximum junction-to-coolant thermal resistance is 0.09 oC/W per switch, and the average number is about 0.08 oC/W per switch. Temperature predicted from CFD simulation INVERTER R&D Junction Temperature of IGBT and Diode 118.2 Application condition similar to 114.9 111.6 IPT “Full Torque Stall”. 108.2 Power loss is 350W for IGBT and 104.9 105W for Diode per switch. 101.6 98.3 o 95.0 Coolant inlet temperature is 85 C, Inlet flow rate is 2 gpm. 91.6 88.3 Outl et 85.0 Temperature predicted from CFD simulation for CPM with pinfin baseplate IGBT and Diode Temperature for CPMs with Flat and Pinfin Baseplates CPM wi th f l at A lSi C baseplate CPM wi th pinf i n A lSi C baseplate o T(jIGBT C) 139 118 o T(jDiode C) 127 112 INVERTER R&D Comparison Thermal resistance reduced by 40% for integrated pin-fin power module. Standard flat Integrated pin-fin Percentage baseplate baseplate reduction Average thermal 0.12 oC/W 0.07 oC/W 40% resistance per swi tch Average IGBT 97 oC 81oC 40% * junct i on temperature Maxi mum measured 105 oC 84oC 47% * IGBT temperature * Note: Percentage reducti on refers to temperature difference between junction and coolant that has inl et temperature of 60 oC in th i s test. INVERTER R&D Problem Approach to Inductance Challenge 1.00 Simulation & Modeling of Structure 2.00 Inductance formulae for current paths 3.00 Physical Systems Test INVERTER R&D Inductance Analysis OBJECTIVES • Optimize layout for minimum inductance • Reduce Parasitics • Lower switching losses • Minimize effects of body diode recovery • Reduce bond wire stress • Minimize EMI Alternative Embedded Busbar Structures INVERTER R&D Inductance Analysis of the D.C. Link ANSOFT Simulation Model Measured Results Units = nH Termi na ls shorted Ta Tb Tc phase Sa 4.5 7.2 9.2 Sb 6.0 4.1 6.0 Sc 9.2 7.2 4.5 INVERTER R&D Path Inductance - The Bond Wires Delta Inductance - 15 mil & 20 mil Path Inductance of Bond Wires Wires 1.2 1 1 0.8 0.8 0.6 20mil nH 0.6 nH 15 mil 0.4 0.4 Inductance in nH 0.2 0.2 0 0 0 1020 30 Wire #'s - (1-2), (2-3), (3-4) Wire Diameter in mil Physical Testing Formulae Based 15 mil wire INVERTER R&D Achieved Benefits Increased package performance: Significant reduction in parasitic inductance Significant reduction in thermal resistance Increased power density Increase packaging integration Reduced system packaging space Reduced system cost Improved reliability INVERTER R&D Transient Thermals ° C/W 1.00 E +00 Cu Junction to Base Cu Substrate to Base - Al203 Comparison 1.00 E-01 AlSic : Junction to Base Cu baseplate AlSic : Substrate to Base - AlN With Al203 DBC compared to 1.00 E-02 AlSic and Aln DBC. 1.00 E-03 AlSic & Aln offers a 10% improvement in thermal resistance 1.00 E-04 Due to the Aln DBC substrate 1.00 E-05 1.00 E-05 1.00 E-04 1.00 E-03 1.00 E-02 1.00 E-01 1.00 1.00 E+00 E+00 1.00 E+01 1.00 100mS - Pulse - 800A Power Module INVERTER R&D Materials Reliability 1.00 E +08 Comparison Wire Bond Capabili ty with coati ng 1.00 E+07 • Cu with Al203 Wire Bond Capabili ty with NO protecti ve coat ing 1.00 E+06 • AlSic with Aln • Wire Bond Coating improvement 1.00 E+05 Solder fati gue for A lSi c & A ln 1.00 E-04 Solder fati gue for Cu & Al 203 1.00 E-03 110 130 150 30 50 70 90 Temperature Delta in Tj INVERTER R&D POWER SILICON • IGBT Heat Diffusion • Stress in bond wire. - IGBT Devices evaluated - Eupec, Semikron, ABB, Toshiba, Hitachi, Fuji This view is below bond wire. INVERTER R&D TOSHIBA IGBT Technical Trend for Cross Section (600V – 1700V) ConventionalConventional Design Design CurrentCurrent Design Design FutureFuture Design Design PT-Trench Thin NPT-Trench Ultra Thin PT-Trench Emitter Gate Emitter Gate Emitter Gate P+ P+ P+ P- Base P- Base P- Base N+ N+ N+ N­ N- (Epi) N Buffer N­ N Buffer P+ P+ Collector P+ Collector • Ultra Thin Wafer ImprovementImprovement for for TradeTrade off off of of • Low Injection Efficiency Eoff-VCE(sat)Eoff-VCE(sat) Collector INVERTER R&D TOSHIBA 600V IGBT Eoff-VCE(sat) Trade-off Ultra Thin PT-Trench Thin NPT-Trench PT-Planer (Future) VS (Latest) VS (Conventional) Eoff - VCE(sat) of 600V Type @V C C =300V, IC =Rated-IC , VGE=+-15V 0.12 Future(Target) 125͠ 0.10 Compact MIP 25͠ 0.08 0.06 ThinThin-NPT-Trench NPT-Trench PT-PlanerPT-Planer UltraUltra-Thin-PT-Trench Thin PT-Trench Eoff (mJ/A) 0.04 0.02 0.00 1.0 1.1 1.2 1.3 1.4 1.5 1.6 1.7 1.8 1.9 2.0 2.1 2.2 2.3 2.4 2.5 2.6 2.7 2.8 VCE(sat) (V) INVERTER R&D Switching Waveforms Clamped inductive load switching at 25C. Red trace SiC, blue trace 1200V hyperfast Si pin diode 25 0 20 -100 15 10 -200 5 -300 0 Id (A) (A) Id Vd (V) (V) Vd -400 -5 -10 -500 -15 -600 -20 -25 -700 0 100 200 300 400 500 0 100 200 300 400 500 Time (ns) Time (ns) current voltage INVERTER R&D Reverse Recovery Summary 25C Si PiN SiC SiC vs Si Peak reverse current Ipr (A) 12.5 3 24% Reverse recovery time Trr (ns) 37 19 51% Recovered charge Qrr (nC) 231 28 12% Diode loss Eoff Diode PJ) 69 9 13% IGBT loss Eon IGBT PJ) 173 149 86% 125C Si PiN SiC SiC vs Si Peak reverse current Ipr (A) 17.5 3 17% Reverse recovery time Trr (ns) 51 19 37% Recovered charge Qrr (nC) 446 28 6% Diode loss Eoff Di ode (PJ) 139 9 6% IGBT loss Eon IGBT (PJ) 198 149 75% INVERTER R&D Hybrid Power Inverter Development Power Inverter Hardware & Analysis for a Hybrid Vehicle Platform INVERTER R&D PM Synchronous Motor Model INVERTER R&D PM Synchronous Motor – 15 kW Operation 15 kW Continuous Operating Points 15 kW Peak Operating Points 250.0 1.000 300.0 1.200 250.0 1.000 200.0 0.800 200.0 0.800 150.0 0.600 150.0 0.600 100.0 0.400 100.0 0.400 50.0 0.200 50.0 0.200 Torque (Nm) Current (Apk) Voltage (Vrms)(Apk) Torque Current (Nm) Torque (Nm) Current (Apk) Voltage (Vrms) (Vrms) Voltage (Apk) Current (Nm) Torque 0.0 0.000 0.0 0.000 0 1000 2000 3000 4000 5000 6000 0.0 1000.0 2000.0 3000.0 4000.0 5000.0 6000.0 Motor Speed, RPM Motor Speed, RPM Torque L-N Vol tage, Vpk Phase Current, Pk Power Pactor Torque L-N Vol tage, Pk Phase Current, Pk Power Factor INVERTER R&D Maximum Coolant Temperature – 15 kW Drive 15 kW Inverter - CPM IGBTs / Switch 150 100 50 0 -50 Temperature, C Temperature, -100 Maximum Allowable Coolant Allowable Maximum 12 April 2003 -150 1 2 3 4 Number of IGBT Die Per Switch 8 kHz Swi tch i ng 4 kHz Swi tch i ng 2 kHz Swi tch i ng Phase-Phase Rotation INVERTER R&D Maximum Coolant Temperature – 25 kW Drive 25 kW Inverter - CPM IGBTs / Switch 150 100 50 0 -50 Temperature, C Temperature, -100 Maximum Allowable Coolant Coolant Allowable Maximum 12 April 2003 -150 1 2 3 4 Number of IGBT Die Per Switch 8 kHz Swi tch i ng 4 kHz Swi tch i ng 2 kHz Swi tch i ng Phase-Phase Rotation INVERTER R&D Voltage Overshoot Reduction Integrated DC-Bus Snubbers INVERTER R&D Further Work • Faster Temperature Sensing of Silicon Junction.
Details
-
File Typepdf
-
Upload Time-
-
Content LanguagesEnglish
-
Upload UserAnonymous/Not logged-in
-
File Pages27 Page
-
File Size-