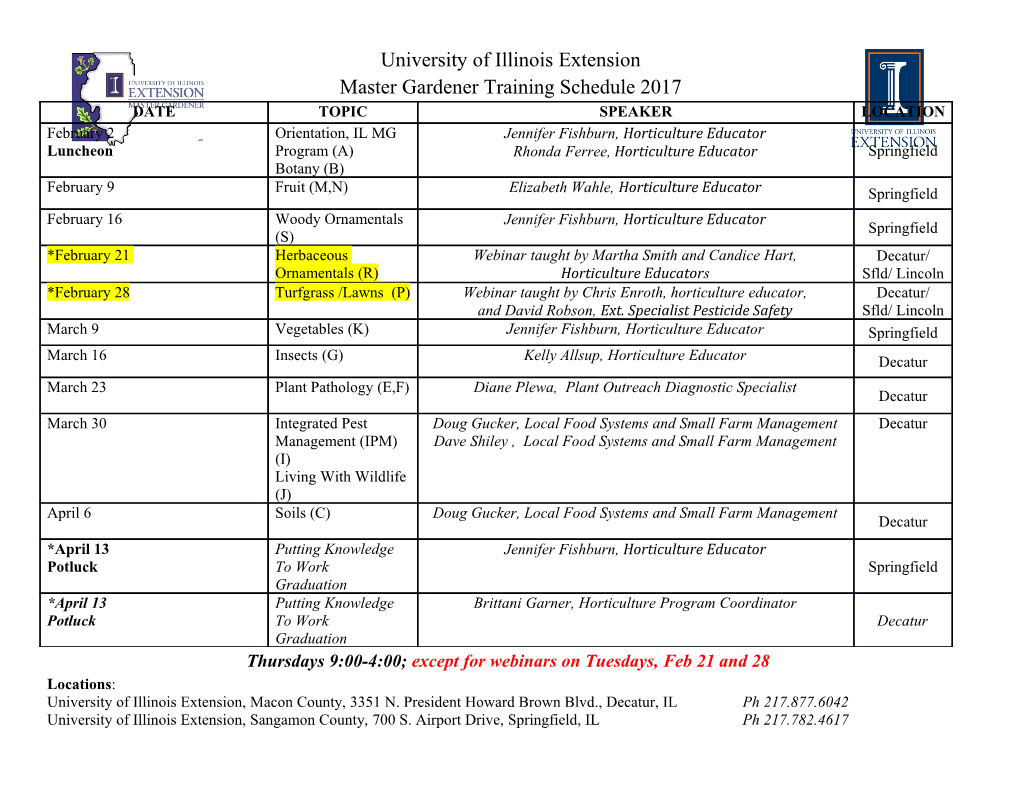
1 of 15 “I Have Inclusions! Get Me the Cheapest and Best Flux for Cleaning My Melt!”–Is This the Best Driven, Cost-Saving Approach by a Foundry? R. Gallo Pyrotek Inc. Aurora, Ohio Copyright 2017 American Foundry Society ABSTRACT This article will provide a guideline to better understand the interrelated aspects between oxides, inclusions, dross, Elimination of inclusion defects requires proper collection fluxes and molten metal quality. and analysis of data. Attempting a corrective action without knowing exactly what the inclusion is may prove Keywords: molten metal quality, inclusions, oxides, very expensive. Unfortunately, it is not uncommon dross fluxes practice that despite the magnitude of the cost of quality due to inclusion defects in castings, a large number of INTRODUCTION aluminum foundries continues to: 1) inaccurately identifying an inclusion based on an educated guess, 2) Many foundries have experienced costly outbreaks of erroneously avoiding paying for the cost of properly high reject rates due to inclusions in castings. An diagnosing the inclusion, 3) inaccurately correlating the inclusion defect may arise from a single clearly defined effects of all the molten metal and casting process cause or may be a result of a combination of factors, so contributing factors, and 4) incorrectly blaming the that the necessary preventive measures are initially melting department for producing and delivering “bad unclear. However, to prevent recurrence it is necessary to metal”. correctly identify the inclusion before troubleshooting the process to find the root cause of the defect. To make matters worse, in many instances foundries limit defect analysis to a single or a couple of defects despite The root cause of the inclusion defects may present great having inclusion issues in a number of different castings. difficulty because of the wide range of interdependent In many instances, foundries overlook the fact that in molten metal and casting process contributing factors. most other part numbers there are no inclusion issues. Thus, why to blame the melting department for the The elimination of inclusion defects in castings require inclusions instead of analyzing why other castings do not the proper collection and analysis of data. There are many have inclusion defects if the starting molten metal statistical techniques to help us control process variables, cleanliness is the same? correlate the effects of variables, and establish priorities for problem solving. Perhaps the Pareto chart is the most Molten metal cleanliness is determined by the amount of common tool used to pinpoint major causes of scrap in a hydrogen gas, dissolved chemical impurities and foundry. Still, these techniques are of little use if the inclusions present in the molten bath before it is cast. The defect is improperly diagnosed. use of a solid flux is the first step for eliminating dissolved impurities, and for ensuring molten cleanliness To correctly diagnose inclusion casting defects, it is by preventing excessive oxide formation, removing non- imperative to: A) fully examine the general characteristics metallic inclusions from the melt, and preventing and/or and occurrence of the inclusions and to describe in detail removing oxide build up from furnace walls. their size, distribution, and appearance, B) document the Furthermore, some fluxes could also help in maximizing defects location with photographs, and C) understand the metal recovery from the dross. casting process. Attempting a corrective action without knowing exactly the type of the inclusion may prove very Foundries need to understand, recognize, and accept that a expensive. Once a corrective action is found, it must be commercial flux recipe is created for a specific not just implemented but also monitored and re-evaluated. metallurgical need, and that none of all the commercially Even though quantitative metallography is essential to available fluxes could provide all the optimum benefits in effectively obtain data on the inclusions, foundries are not just one recipe -since some of the benefits are conflicting always willing to invest time, effort, and money for in nature. In addition, foundries must understand that the proper inclusion assessment either in the molten bath or cost of flux is influenced by the quality of the compounds, the castings. as well as by the type and complexity of the formulation. In general, as the cost of the flux decreases, so does the Typically, 4 techniques are being used in foundries to effectiveness and efficiency of the flux. evaluate casting inclusion defects: Originally published as paper 17-105 in the 2017 Proceedings of the 121st Metalcasting Congress of the American Foundry Society. Used with permission of the publisher and not for distribution. 2 of 15 • In the majority of the cases, when inclusion defects originally implemented would become inefficient. Typical are considered a minor nuisance, a simple visual and very common process changes and deviations, evaluation (“educated guess”) of the inclusion is noticed in a vast number of foundries, related to the conducted. treatment and handling of liquid aluminum that would • An optical microscope and/or stereomicroscope. negatively impact the quality of the molten metal are: • Optical microscope coupled with computer and • Accepting raw materials of lower quality. image analysis. • Charging dirtier returns/scrap (i.e., contaminated with • A SEM analysis. Unfortunately, many foundries oil, and grease due to poor foundry equipment would limit the usage of this technique to a few maintenance). samples that in many instances are not enough to • Operating equipment which has inoperative and properly identify the different inclusion casting malfunctioning flow meters, pressure regulators, and defects that they are facing. RPM counters. • Failing to replace worn off degassing consumables. Nearly everyone who casts aluminum alloys, regardless of • Reusing poor quality residual pieces of ceramics sophistication, has at some time experienced an issue with and/or graphite materials (that have already exceeded inclusions from molten aluminum. Even the molten their life expectancy) to make other components to be aluminum being used for sheet ingot and beverage cans, used in molten aluminum. which is considered the cleanest molten aluminum, will • Lack of preventive maintenance in both: equipment, have inclusions to some extent (smaller sizes and lower and refractory in furnaces and transport ladles. concentrations of them). Thus, various types of inclusions • Failing to follow process procedures during the such as oxides, nitrides, carbides, fluorides, borides, casting (molding) process. For example, not placing chlorides and salts may be present in molten aluminum the filter in the gating system and/or not blowing air alloys. before closing the mold. While the existing types of inclusions that would be More progressive foundries have made continuous efforts present in the melting furnaces will vary from foundry to to better understand and disseminate, within their foundry, their removal is essential for proper molten organization, concepts and knowledge such as: metal cleanliness. A number of commercially accepted • Molten metal quality and molten cleanliness. melt treatment techniques is being used by aluminum • Difference between impurities, inclusions, and dross. foundries to remove and separate inclusions from the • Influence of the raw material charge on oxides. molten aluminum alloy prior to casting. These include • Importance of minimizing skim generation. various methods of fluxing, degassing, and filtration in • How fluxes work. the furnaces and in the gating system. Any of these • techniques will have an impact on the melt cleanliness of Importance of identification, and quantification of the the molten aluminum alloy. However, the effectiveness to inclusion defects. • evaluate their removal would rely on the melt cleanliness Benefits of using analytical commercial instrument to measurement technique being used. Ideally, the optimum evaluate metal cleanliness, and seeking assistance in technique would provide assessment of three inclusions identifying and solving defects due to inclusions. parameters: size, distribution, and composition. MOLTEN METAL QUALITY AND MOLTEN During the last 50 years, several techniques have been CLEANLINESS developed and used for assessing the cleanliness of molten aluminum casting alloys. These include It is very important to understand that molten aluminum qualitative, quantitative, and analytical laboratory quality encompasses molten metal cleanliness. procedures, as well as on-line and off-line techniques. The level of quality of a molten aluminum bath is based Better understanding of the cleanliness level of the molten on the degree to which the chemical properties (chemical metal being delivered by the melting department and the element composition) and physical properties (hydrogen additional influence that other casting process factors may content, dissolved chemical impurities, and inclusions) have on the molten metal quality level would help are controlled within a specific foundry’s internal aluminum foundries to implement feasible, practical and specification, which is established to meet casting robust controls during the molten metal treatment and requirements. In general, the goal of the melting handling operations to minimize inclusion defects. department is to produce and deliver quality metal, while However, implementation alone would not be sufficient
Details
-
File Typepdf
-
Upload Time-
-
Content LanguagesEnglish
-
Upload UserAnonymous/Not logged-in
-
File Pages15 Page
-
File Size-