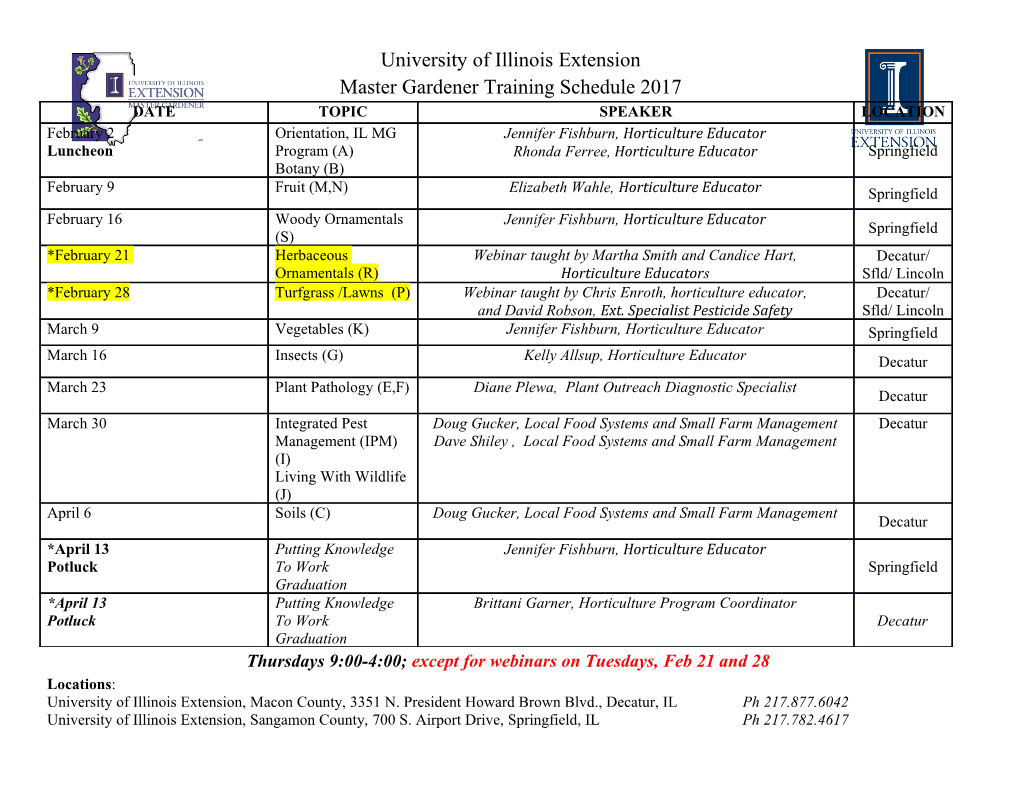
University of Huddersfield Repository Kubiak, Krzysztof, Mathia, T.G. and Fouvry, S. Interface roughness effect on friction map under fretting contact conditions Original Citation Kubiak, Krzysztof, Mathia, T.G. and Fouvry, S. (2010) Interface roughness effect on friction map under fretting contact conditions. Tribology International, 43 (8). 1500 - 1507. ISSN 0301-679X This version is available at http://eprints.hud.ac.uk/id/eprint/21593/ The University Repository is a digital collection of the research output of the University, available on Open Access. Copyright and Moral Rights for the items on this site are retained by the individual author and/or other copyright owners. Users may access full items free of charge; copies of full text items generally can be reproduced, displayed or performed and given to third parties in any format or medium for personal research or study, educational or not-for-profit purposes without prior permission or charge, provided: • The authors, title and full bibliographic details is credited in any copy; • A hyperlink and/or URL is included for the original metadata page; and • The content is not changed in any way. For more information, including our policy and submission procedure, please contact the Repository Team at: [email protected]. http://eprints.hud.ac.uk/ Published in Tribology International 2010 Vol. 43, Issues 8 (2010) p. 1500-1507 http://dx.doi.org/10.1016/j.triboint.2010.02.010 Interface roughness effect on friction map under fretting contact conditions K.J. Kubiak, T.G. Mathia, S. Fouvry 1 Laboratoire de Tribologie et Dynamique des Systèmes, CNRS UMR 5513, Ecole Centrale de Lyon, 36 Avenue Guy de Collongue, 69134 Ecully, France *Corresponding author: [email protected] Abstract: In many industrial applications where fretting damage is observed in the contact (e.g. rotor/blade, electrical contacts, assembly joint, axe/wheel, clutch) the external loadings or geometry design cannot be changed. Therefore, the surface preparation and finishing process become essential to control and reduce the damage caused by fretting. In this paper, the authors present the experimental study of the initial surface roughness and machining process influence on fretting conditions in both partial and full sliding regimes. Surfaces prepared by milling and smooth abrasive polishing processes have been analysed. The influence of roughness on sliding behaviour and analysis of friction have been reported. Also, the contact pressure influence and qualitative analysis of fretting wear scar have been presented. Keywords: Fretting map, Surface roughness, Sliding regime, Texturation. Nomenclature: δ - displacement ( µm), δ* - displacement amplitude ( µm), δt - sliding transition displacement amplitude ( µm), ∆δ - incremental step of displacement amplitude ( µm), P - normal force (N), Q - tangential force (N), Q* - tangential force amplitude (N), po - maximum Hertzian’s contact pressure (MPa), a – Hertzian’s contact radius ( µm), N - number of fretting cycles, ∆N - number of fretting cycles between the incremental steps of displacement, Sq - 3D surface root mean square (RMS) roughness (µm), Sa - 3D surface average roughness (µm), Sz - 3D surface peak-to-valley average maximum height (µm), St - 3D surface peak-to-valley maximum peak height (µm), µ - coefficient of friction Q */P, 1 Published in Tribology International 2010 Vol. 43, Issues 8 (2010) p. 1500-1507 http://dx.doi.org/10.1016/j.triboint.2010.02.010 PS - partial slip (sliding condition regime), FS - full sliding (sliding condition regime), µt - coefficient of friction at the transition PS/FS, µstab - stabilised coefficient of friction in FS regime, σY(0.2%) - yeld stress (MPa), σUTS - ultimate tensile stress (MPa), E- elastic modulus (GPa), 1 Introduction Fretting phenomenon is considered as a special damage process related to wear and cracking. Fretting occurs in the contact between two bodies subjected to the normal load and sliding induced by external cyclic forces or vibration. Depending on the relative displacement at the interface, Partial Slip or Full Sliding condition can be observed in the contact. In PS situation, the central zone of the contact, remains in stick condition, without the relative displacement and the external zone of contact is subjected to sliding (Fig. 1). In the FS condition, the entire area of contact is subjected to sliding (Fig. 1). Therefore, the fretting damage mode depends on sliding conditions, leading to cracking under PS and wear under FS condition [1]. Fretting is a dynamical process where sliding conditions and surface morphology of contacting materials can vary with time. In many industrial applications, it is not possible to control the fretting degradation process. Therefore, the initial design of such elements is the only way to prevent or to reduce the fretting phenomenon and surface damage. If it is not possible to modify the contact loading to reduce fretting degradation, the initial roughness could be optimised. Dulias et all. noted strong influence of surface roughness on sliding conditions [2]. However, relation between surface morphology and friction behaviour has been mainly studied in the mono-directional sliding [3] or in the FS conditions in order to evaluate the influence of roughness on wear behaviour [4]. In this paper, focus will be given on small amplitude, fretting sliding conditions. Under fretting and especially in the PS condition not much work has been published. Wong et all. [5] have reported influence of roughness on ceramics under mixed and hydrodynamic lubrication, a decreasing friction coefficient has been found for smoother surfaces. For aluminium alloy under dry fretting contact conditions Proudhon et all. [6] have noted influence of roughness where the rough surface tends to decrease the coefficient of friction at transition from PS to FS. 2 Published in Tribology International 2010 Vol. 43, Issues 8 (2010) p. 1500-1507 http://dx.doi.org/10.1016/j.triboint.2010.02.010 Contact behaviour damages stick zone Partial Slip (PS) sliding zone cracking δ sliding transition : t displacement amplitude Full Slip (FS) full sliding wear Fig. 1: Typical fretting damage observed under Partial Slip and Full Slip conditions [7]. To illustrate the transition between PS and FS the relationship between contact loading conditions (normal load, displacement amplitude, tangential load) and the sliding conditions (Partial Slip, Full Sliding) have to be considered. This relationship and observed damage phenomenon (cracking in PS and wear in FS) can be illustrated on the so-called Fretting Maps (FM). Firstly introduced by Vingsbo [8] the FM can present the running conditions (Running Conditions Fretting Map, RCFM, Fig. 2a) and material response (Material Response Fretting Map, MRFM, Fig. 2b). 600 600 500 500 Partial Slip Cracking 400 400 300 300 200 Full Slip 200 Wear Normal forceN/mm P, Normal force N/mm P, 100 100 0 0 0 5 10 15 20 25 30 0 100 200 300 400 500 600 a) Displacement amplitude δ*, µm b) Tangential force amplitude Q*, N/mm Fig. 2 Fretting maps: a) RCFM, b) MRFM, (AISI 1034, cylinder/plane configuration, R=40mm, normalised by cylinder axial contact length, N/mm) [9]. In PS condition where displacement is limited to external zone of contact (Fig. 1) surface roughness can influence local sliding condition, and generate local plastic deformation at contacting surface peaks. This lead to change in sliding behaviour and can cause uncontrolled damage. Therefore, better understanding of the surface roughness influence on fretting sliding phenomenon have a great interest for practical applications. This paper present the experimental results of initial surface roughness influence on fretting sliding conditions, to illustrate 3 Published in Tribology International 2010 Vol. 43, Issues 8 (2010) p. 1500-1507 http://dx.doi.org/10.1016/j.triboint.2010.02.010 this relationship fretting map concept have been used. Reported fretting map curves, plotted for surfaces with different initial roughness, demonstrate their influence on friction behaviour. 2 Experimental procedure Fretting tests have been curried out using classical sphere/plane configuration, where the radius of sphere was 50 mm. Specific fretting device has been rigidly mounted on the universal fatigue machine [10]. Schematic diagram of fretting test equipment is presented in the Fig. 3. measured relative displacement δ(t) sphere R=50mm 52100 normal plane sample force AISI 1034 P Y X measured FIXED MOVING tangential force Q(t) imposed displacement Fig. 3: Schematic diagram of fretting test device in sphere/plane configuration. During the test, applied normal force P has been kept constant, sinusoidal displacement has been successively increased (see section 2.2). The normal force P, tangential force Q and relative displacement δ have been recorded. All experiments have been performed at displacement frequency of 20 Hz. Before the tests, all specimens have been cleaned in acetone and ethanol. Tests have been performed in ambient labolatory conditions at the temperature ~23ºC, and the relative humidity between 40 and 45%. 2.1 Studied materials One of the industrial applications where fretting problem is occurring is contact between the axe and wheel of the train. In this application, the important plastic deformation have been observed due to fitting process. Authors inspired by this application, have selected similar low carbon alloy AISI 1034 for the plane material. In order to reduce the plastic deformation in the contact, the AISI 52100 material has been used for the sphere 4 Published in Tribology International 2010 Vol. 43, Issues 8 (2010) p. 1500-1507 http://dx.doi.org/10.1016/j.triboint.2010.02.010 counterbody. Chemical composition and the mechanical properties of the studied materials are listed in the Table 1 and Table 2 respectively. Table 1: Chemical composition of tested materials. Materials C Mn Cr Ni Ti Cu Si P S Mo V AISI 1034 max 0.38 1.2 0.3 0.3 - 0.3 0.5 0.02 0.02 0.08 0.06 (plane) (%) 5210 max 1.0 0.3 1.5 0.4 1.0 1.0 0.2 0.02 0.02 0.1 0.3 (sphere) (%) Table 2: Mechanical properties of tested materials.
Details
-
File Typepdf
-
Upload Time-
-
Content LanguagesEnglish
-
Upload UserAnonymous/Not logged-in
-
File Pages16 Page
-
File Size-