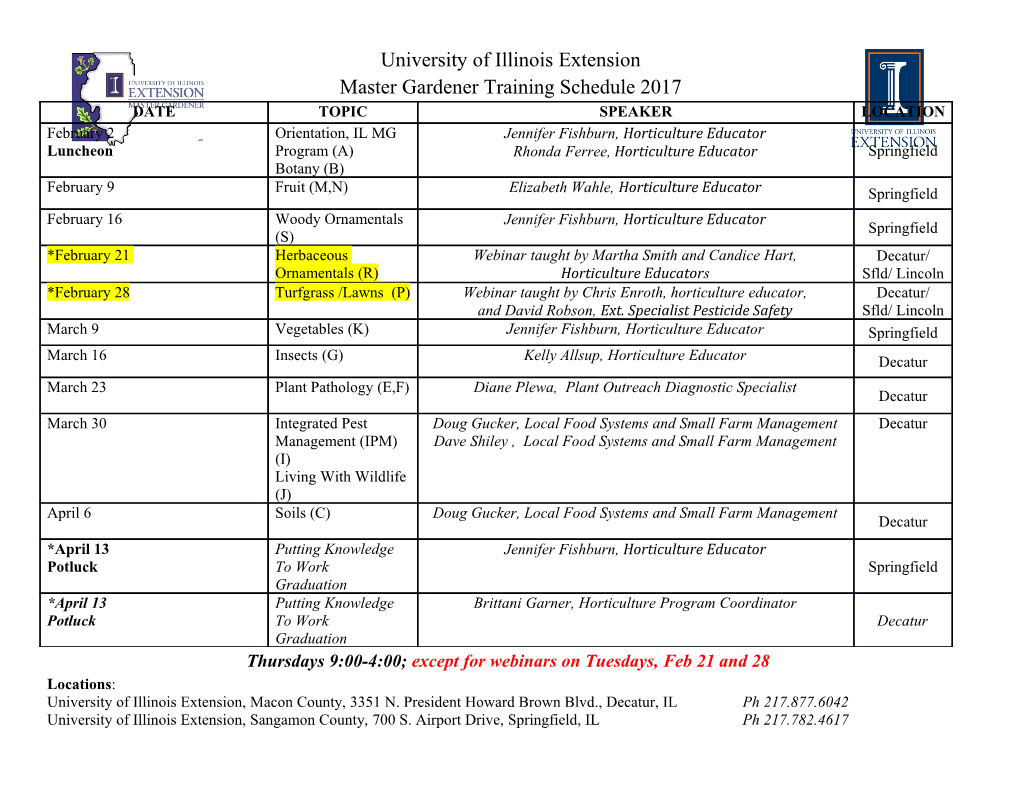
polymers Review A Review of Vat Photopolymerization Technology: Materials, Applications, Challenges, and Future Trends of 3D Printing Marek Pagac * , Jiri Hajnys , Quoc-Phu Ma , Lukas Jancar, Jan Jansa , Petr Stefek and Jakub Mesicek Center of 3D Printing Protolab, Department of Machining, Assembly and Engineering Technology, Faculty of Mechanical Engineering, VSB-TU Ostrava, 17. listopadu 2172/15, 708 00 Ostrava-Poruba, Czech Republic; [email protected] (J.H.); [email protected] (Q.-P.M.); [email protected] (L.J.); [email protected] (J.J.); [email protected] (P.S.); [email protected] (J.M.) * Correspondence: [email protected] Abstract: Additive manufacturing (3D printing) has significantly changed the prototyping process in terms of technology, construction, materials, and their multiphysical properties. Among the most popular 3D printing techniques is vat photopolymerization, in which ultraviolet (UV) light is deployed to form chains between molecules of liquid light-curable resin, crosslink them, and as a result, solidify the resin. In this manuscript, three photopolymerization technologies, namely, stereolithography (SLA), digital light processing (DLP), and continuous digital light processing (CDLP), are reviewed. Additionally, the after-cured mechanical properties of light-curable resin materials are listed, along with a number of case studies showing their applications in practice. The manuscript aims at providing an overview and future trend of the photopolymerization technology to inspire the readers to engage in further research in this field, especially regarding developing new materials and mathematical models for microrods and bionic structures. Citation: Pagac, M.; Hajnys, J.; Ma, Keywords: vat photopolymerization; SLA; DLP; CDLP; CLIP Q.-P.; Jancar, L.; Jansa, J.; Stefek, P.; Mesicek, J. A Review of Vat Photopolymerization Technology: Materials, Applications, Challenges, 1. Introduction and Future Trends of 3D Printing. Additive manufacturing (AM) technology was first introduced in the 1980s with the Polymers 2021, 13, 598. https://doi. aim of producing rapid and functional prototypes from various materials. Particularly, in org/10.3390/polym13040598 May 1980, Dr. Hideo Kodama from the Nagoya Municipal Industrial Research Institute (NMIRI) applied for a patent that describes a method of curing a spatial model of pho- Academic Editor: Paul F. Egan topolymer material by exposing it to ultraviolet (UV) light. Nevertheless, Kodama’s efforts Received: 30 January 2021 toward finding funding for further research and development on the issued patent bore no Accepted: 13 February 2021 Published: 17 February 2021 fruit, even with support from the government. The patent was consequently abandoned and never commercialized [1–4]. Kodama is, however, credited as the first inventor of this technology. Publisher’s Note: MDPI stays neutral with regard to jurisdictional claims in The origin of 3D printing with commercial potential can be traced back to 1986 when published maps and institutional affil- Charles W. Hull filed a patent for a photopolymerization technology called stereolithogra- iations. phy (SLA). The very first printed model was an eye-wash cup. Henceforth, SLA has been developed by 3D Systems Corporation [1–3]. New developments are also closely related to the development of 3D printing in med- ical and regenerative medicine. Dating back to 2004 in [5], a novel technique for printing 3D cell patterns was introduced. Later on, in [6], the author describes the process of manu- Copyright: © 2021 by the authors. facturing structures, namely, scaffolds, on which, cells can grow after being implemented Licensee MDPI, Basel, Switzerland. This article is an open access article into the body. A typical example of 3D bioprinting is artificial vessels, for which, dog bone distributed under the terms and marrow samples were used [7,8]. conditions of the Creative Commons 2. Vat Photopolymerization Attribution (CC BY) license (https:// creativecommons.org/licenses/by/ AM technologies are classified as shown below in Figure1. Each technology differs 4.0/). from another in the manner of the application process, curing principle, and the initial state Polymers 2021, 13, 598. https://doi.org/10.3390/polym13040598 https://www.mdpi.com/journal/polymers Polymers 2021, 13, x FOR PEER REVIEW 2 of 18 2. Vat Photopolymerization Polymers 2021, 13, 598 2 of 20 AM technologies are classified as shown below in Figure 1. Each technology differs from another in the manner of the application process, curing principle, and the initial state of the material. Herein, attention is paid to the historically oldest AM technology, of the material. Herein, attention is paid to the historically oldest AM technology, namely, namely, vat photopolymerization. vat photopolymerization. Figure 1. Division of the additive manufacturing (AM) technologies according to ISO/ASTM 52900: Figure2015 Additive 1. Division Manufacturing—General of the additive manufacturing Principles—Terminology. (AM) technologies according to ISO/ASTM 52900: 2015 Additive Manufacturing—General Principles—Terminology. 2.1. 3D Printing Process 2.1. 3DThe Printing 3D printing Process production process begins with a 3D model that is designed with computer-aidedThe 3D printing design production (CAD) software process or begins 3D scanned with froma 3D amodel physical that object. is designed The 3D with model is subsequently converted to the standard triangulation language (STL) format. It computer-aided design (CAD) software or 3D scanned from a physical object. The 3D should be noted that since 1987, STL has been the standard and most frequently used modelformat is for subsequently preparing data conver for AMted production. to the standard Specifically, triangulation the STL formatlanguage solely (STL describes) format. It shouldthe surface be noted of the that 3D modelsince with1987, a STL network has ofbeen triangles the standard of different and sizes, most depending frequently on used formatthe required for prepar resolution.ing data Thefor AM smaller production. the size ofSpecifically, the triangles, the theSTL more format accurately solely describes the thetriangular surface meshof the represents 3D model the with desired a network surface, of yielding triangles a smootherof different surface sizes of, depending the to-be- on theprinted required object. resolution. The stage T inhe which smaller preparing the size the of desired the triangles mesh model, the more takes accurately place is called the tri- angularpreprocessing mesh [represent9]. s the desired surface, yielding a smoother surface of the to-be- printedThe object second. The production stage in stagewhich is preparing called processing. the desi Asred a mesh 3D printed model object takes is place fabricated is called preprocessinglayer by layer, [9] each. consecutive layer has to be supported by either the platform, the pre- cedingThe layer, second or extra production support stage elements. is called After processing. designing the As correct a 3D printed and optimal object orientation is fabricated layerof the by model layer, and each the consecutive supports, the layer STL model,has to be including supported the supports,by eitheris the sliced platform into layers, the pre- with a plane parallel to the platform surface, namely, the xOy plane. Each layer is then ceding layer, or extra support elements. After designing the correct and optimal orienta- built consecutively in the Oz direction. The layer thickness depends on the printer, AM tion of the model and the supports, the STL model, including the supports, is sliced into technology, and quality requirements. The sliced model is subsequently sent to the printer. layersDiffering with from a plane the traditional parallel to subtractive the platform manufacturing surface, namely, process the (machining), xOy plane. where Each thelayer is thenmaterial built is consecutively taken out of a in workpiece, the Oz direction. AM offers The more layer efficient thickness material depends usage. on the printer, AM technologyAfter the printing, and quality is finished, requirements. the model The is removedsliced model from is the subsequently platform and sent other to the printer.technical Differing processing from procedures the traditional are used subtractive to refine the manufacturing printed object process in a stage (machining called ), wherepostprocessing. the material In is the taken case ofout photopolymerization, of a workpiece, AM theoffers as-built more models efficient are material rinsed inusage. a washAfter solution, the printing most commonly, is finished isopropyl, the model alcohol is removed (IPA), to get from rid ofthe the platform liquid layer and of other resin. tech- nicalTo enhance processing the mechanicalprocedures properties, are used to these refine models the printed are subsequently object in a stage artificially called cured postpro- cessing.with UV In light the orcase naturally of photopolymerization, exposed to sunlight. the Other as-built processes models include are supportrinsed in removal, a wash so- lution,grinding, most sealing, commonly, gluing, isoprop polishing,yl painting,alcohol (IPA), varnishing, to get coating,rid of the sterilization, liquid layer inspection, of resin. To enhanceand measurement. the mechanical There properties, are specific these post-processing models are treatments subsequently for photopolymer artificially cured parts. with It is noteworthy that the rinsing time, temperature, and duration of the curing process
Details
-
File Typepdf
-
Upload Time-
-
Content LanguagesEnglish
-
Upload UserAnonymous/Not logged-in
-
File Pages20 Page
-
File Size-