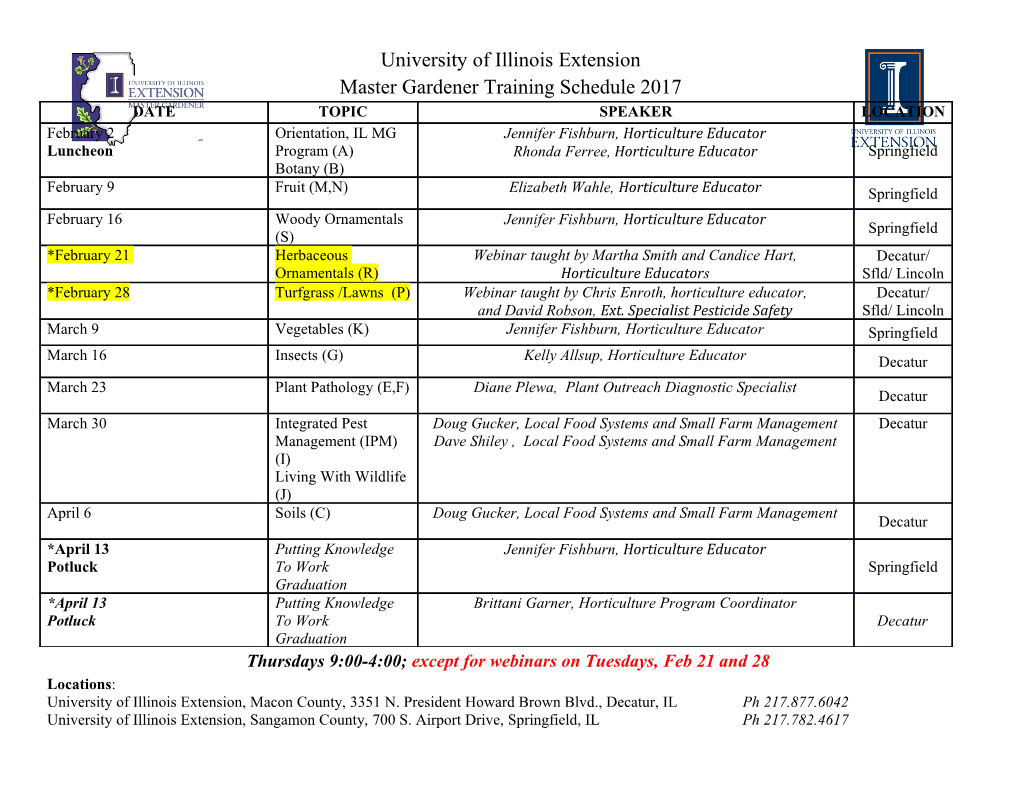
stage 7 triennial report 1 July 2012–30 June 2015 review 1 July 1995–30 June 2012 plans 1 July 2015–30 June 2018 CHARMECNUTEK/VINNOVA Chalmers Railway Mechanics – a Competence Centre Chalmers University of Technology FOREWORD This Triennial Report documents the organization, operation, financing and results of Stage 7 (1 July 2012 – 30 June 2015) for the Swedish National Centre of Excellence in Railway Mechanics, charmec. The presentation also contains a review of previous research activities going back to the establishment of charmec which was based on a nutek/vinnova government grant for the period 1995–2005. Pages 128–130 display an overview of all 117 projects that have been (or are being) carried out within charmec. Some results from the period 1 July 2015 – 31 May 2016 have been added. The report has been compiled by a number of contributors with Professor Roger Lundén, Docent Elena Kabo and Professor Emeritus Bengt Åkesson providing major parts. The layout and typesetting was made by Graphic designer Tomas Wahlberg based on Yngve Nygren’s original design. More details on the activities within charmec (as well as electronic versions of this and previous triennial reports) are available on the charmec website (www.chalmers.se/charmec). Gothenburg in June 2016 anders ekberg Director of charmec William Chalmers (1748–1811) from Gothenburg, Director of the Swedish East India Company, bequeathed a large sum of money to the start in 1829 of an industrial school that later became the Chalmers University of Technology Front cover: Photoelastic experiment illustrating stress fields arising during two-point contact between wheel and rail 2 CONTENTS Foreword 2 Programme area 3 Reflections from the Director 5 Materials and maintenance (MU) Executive summary 6 MU1. Mechanical properties of ballast 39 Introduction 7 MU2. New materials in wheels and rails 39 Vision and goals 8 MU3. Martensite around wheel flats 40 Board and Director 8–9 MU4. Prediction of lifetime of railway wheels 40 Quality assessment and knowledge transfer 10 MU5. Mechanical properties of concrete sleepers 41 Programme areas CHARMEC Stage 7 11 MU6. Rolling contact fatigue of rails 41 Summary of CHARMEC Stage 7 12–13 MU7. Laser treatment of wheels and rails 42 Projects and results 14 MU8. Butt-welding of rails 42 Programme area 1 MU9. Rolling contact fatigue of wheels 43 Interaction of train and track (TS) MU10. Crack propagation in railway wheels 43 TS1. Calculation models of track structures 14 MU11. Early crack growth in rails 44 TS2. Railhead corrugation formation 15 MU12. Contact and crack mechanics for rails 44 TS3. Sleeper and railpad dynamics 15 MU13. Materials at low temperatures 45 TS4. Lateral track dynamics 16 MU14. Damage in track switches 45 TS5. Out-of-round wheels 16 MU15. Microstructure during laser coating 46 TS6. Identification of dynamic forces in trains 17 MU16. Alternative materials for wheels and rails 46 TS7. Dynamics of track switches 17 MU17. Elastoplastic crack propagation in rails 47 TS8. Integrated track dynamics 18 MU18. Wheels and rails at high speeds TS9. Track dynamics and sleepers 19 and axle loads 48 TS10. Track response when using USP 19 MU19. Material anisotropy and RCF of rails and switches 49–50 TS11. Rail corrugation growth on curves 20 MU20. Wear impact on RCF of rails 51 TS12. Identification of contact forces 21 MU21. Thermal impact on RCF of wheels 52–53 TS13. Optimization of track switches 22 MU22. Improved criterion for surface TS14. Multicriterion optimization of tracks 23–24 initiated RCF 54–56 TS15. Improved availability and reduced MU23. Material behaviour at rapid thermal life cycle cost of track switches 25–26 processes 57 TS16. Time-domain model of braking noise 27 MU24. High-strength steels for rails 58 TS17. Optimization of materials in track switches 28 MU25. Thermodynamically coupled contact TS18. Numerical simulations of train-track between wheel and rail 59–60 deterioration for RAMS and LCC 29 MU26. Optimum inspection and maintenance Programme area 2 of rails and wheels 61–62 Vibrations and noise (VB) MU27. Progressive degradation of rails VB1. Structural vibrations from railway traffic 30 and wheels 63–64 VB2. Noise from tread braked railway vehicles 30 MU28. Mechanical performance of wheel VB3. Test rig for railway noise 31 and rail materials 65–66 VB4. Vibrations and external noise 31 MU29. Damage in wheel and rail materials 66–67 VB5. Wave propagation under high-speed trains 32 MU30. Modelling of properties and damage in wheel and rail materials 68–69 VB6. Interaction of train, soil and buildings 32 MU31. Squats in rails and RCF VB7. Vibration transmission in railway vehicles 33 clusters on wheels 69–70 VB8. Ground vibrations from railways 33 MU32. Modelling of thermomechanically VB9. Dynamics of railway systems 34 loaded rail and wheel steels 71–72 VB10. External noise generation from trains 35 MU33. Numerical simulation of rolling contact VB11. Abatement of curve squeal 36–37 fatigue crack growth in rails 73 VB12. High-frequency wheel–rail interaction 37–38 MU34. Influence of anisotropy on rolling contact fatigue cracks 74 3 Programme area 4 Programme area 6 Systems for monitoring and operation (SD) Parallel special projects (SP) SD1. Braking of freight trains SP1-6. See pp 97–98 – a systems approach 75 SP7. Lateral track stability 98 SD2. Sonar pulses for braking control 76 SP8. Design of insulated joints 99 SD3. Computer control of braking systems SP9. Sleeper design for 30 tonne axle load 99 for freight trains 77 SP10. Noise reduction and EU project QCITY 99 SD4. Control of block braking 78 SP11. Vertical contact forces of high-speed trains 100 SD5. Active and semi-active systems SP12. New sleeper specifications 101 in railway vehicles 79 SP13. Alarm limits for wheel damage 101 SD6. Adaptronics for bogies and other railway components 79 SP14. Particle emissions and noise 101 SD7. Thermal capacity of SP15. Computer program for design of tread braked wheels 80–81 block brakes 102 SD8. Wear of disc brakes and block brakes 81–82 SP16. Dynamic properties of timber sleepers and concrete replacement sleepers 102 SD9. Multiobjective optimization of bogie system and vibration control 83–84 SP17. Switch sleeper specifications 103 SD10. Enhanced mechanical braking systems SP18. Ground vibrations – influence of for modern trains 85 vehicle parameters 103 Programme area 5 SP19. Optimum track stiffness 104 Parallel EU projects (EU) SP20. Classification of wheel damage forms 104 EU1. EuroSABOT – Sound attenuation SP21. Optimum material selection for switches 105 by optimised tread brakes 86 SP22. Implementing INNOTRACK results EU2. Silent Freight – Development of new at Trafikverket 105 technologies for low noise freight wagons 86 SP23. Optimized prestressed concrete sleeper 106 EU3. Silent Track – Development of new tech- SP24. Derailment risks in switches 107 nologies for low noise railway infrastructure 87 SP25. Harmonized measurement sites EU4. ICON – Integrated study of for track forces 107–108 rolling contact fatigue 87 SP26. Holistic optimization of tracks 108–109 EU5. EUROBALT II – European research for an optimised ballasted track 88 SP27. Optimized prestressed concrete sleeper – phase II 109 EU6. HIPERWHEEL – Development of an inno- vative high-performance railway wheelset 88 Academic awards 110 EU7. INFRASTAR – Improving railway International conferences 111 infrastructure productivity by sustainable Partners in industry 112–113 two-material rail development 88 Results and effects in industry 114–115 EU8. ERS – Euro Rolling Silently 89 Tore Dahlberg 1945–2016 115 EU9. EURNEX – European Rail Research Special events and achievements 116–123 Network of Excellence 89 Financial report EU10. INNOTRACK – Report per party 124–126 Innovative Track Systems 90 Report per programme area 126 EU11. QCITY – Quiet City Transport 90 Management and administration 126 EU12. RIVAS – Railway Induced Vibration Abatement Solutions 91–92 CHARMEC Stage 8 127 EU13. D-RAIL – Development of Future Rail Concluding remarks 127 Freight Systems to Reduce Derailments 93–94 CHARMEC research 1995-2016 128–130 EU14. Capacity4Rail – Capacity for Rail 95 Chalmers University of Technology 2016 131 EU15. WRIST – Innovative Welding Processes for New Rail Infrastructures 95–96 EU16. In2Rail – Innovative Intelligent Rail 96 4 REFLECTIONS FROM THE DIRECTOR In many countries – including Sweden – railway operations On the following pages, we provide an overview of our are at an all-time high and many railways are struggling research and how it relates to the overall aims of a more with demanding issues regarding reliability and costs. robust and (cost) efficient railway. We endeavor to under- As operations reach the capacity limit, the margin for stand and predict loading, deformation, vibration, noise, faults diminishes and the cost for maintenance and miti- and deterioration of railway components and systems. gating measures soars. These are known facts, and actions This knowledge can then be translated into engineering so- such as the planning for new lines are taken in many coun- lutions where our research results are being implemented. tries. This will also facilitate the shift of transports from This strive towards implementation is always present, but road to rail as is strongly advocated by, e g, the eu. perhaps most clear in the European projects presented on In this situation the role of railway research, and in pages 86–96. These projects also highlight the close co- particular research in railway mechanics, is more impor- operation
Details
-
File Typepdf
-
Upload Time-
-
Content LanguagesEnglish
-
Upload UserAnonymous/Not logged-in
-
File Pages132 Page
-
File Size-