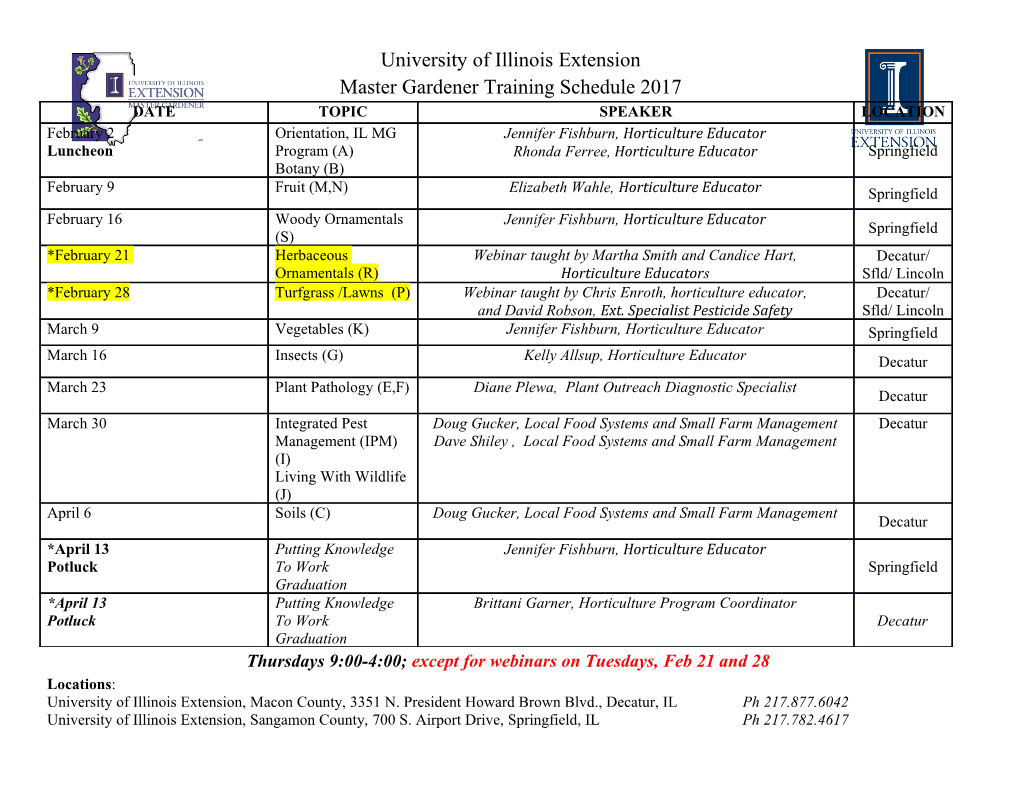
The Space Congress® Proceedings 1980 (17th) A New Era In Technology Apr 1st, 8:00 AM Shuttle Performance Augmentationwith the Titan Liquid Boost Module Arthur E. Inman LBM Project Engineer, Space Launch Systems, Martin Marietta Corporation John G. Muehlbauer LBM Engine Project Engineer, Rocket Engineering, Aerojet Liquid Rocket Company Follow this and additional works at: https://commons.erau.edu/space-congress-proceedings Scholarly Commons Citation Inman, Arthur E. and Muehlbauer, John G., "Shuttle Performance Augmentationwith the Titan Liquid Boost Module" (1980). The Space Congress® Proceedings. 1. https://commons.erau.edu/space-congress-proceedings/proceedings-1980-17th/session-1/1 This Event is brought to you for free and open access by the Conferences at Scholarly Commons. It has been accepted for inclusion in The Space Congress® Proceedings by an authorized administrator of Scholarly Commons. For more information, please contact [email protected]. SHUTTLE PERFORMANCE AUGMENTATION WITH THE TITAN LIQUID BOOST MODULE Arthur E. Inman John G. Muehlbauer LBM Project Engineer LBM Engine Project Engineer Space Launch Systems Rocket Engineering Martin Marietta Corporation Aerojet Liquid Rocket Company Denver, Colorado Sacramento, California ABSTRACT by the space agency during the summer and fall of 1979, the decision was made to adopt the The projected 24000 pound payload lift cap­ Titan Liquid Boost Module (LBM) as the base­ ability for the baseline Space Shuttle, with line Thrust Augmentation System. The LBM anticipated arbiter and external tank weight consists of the Aerojet Liquid Rocket Company's savings programs implemented, will not meet current Titan 34B Stage I engine with Titan . the 32000 pound payload requirements for the type tanks, feed lines and a support truss DOD Mission 4 from Vandenberg Air Force Base, which will be manufactured by Martin Marietta NASA has selected the Titan Liquid Boost Module Corporation. The module will be attached to (LBM) to provide thrust augmentation during the aft end of the external tank and will the boost phase sufficient to meet and provide occupy the space between the Solid Rocket margin for the defined Mission 4 requirements. Boosters. The LBM will use Titan 34D Stage I engines and a cluster of four Titan derived 10 foot diam­ eter tanks. The module will be attached to COMPARATIVE ANALYSIS the aft end of the ET. This paper will pro­ vide a description of the LBM and discuss some The decision to adopt the Titan LBM System was of its advantages and capabilities based on technical, cost and programmatic reasons. Included were consideration of pay- load capability, man-rating» development risk, INTRODUCTION cost per payload pound, system loads and opera­ tional flexibility. Utilization of the exist­ The Space Transportation System (STS) must ing Aerojet/Martin Titan team "know-how" and have a payload lift capability of-32,000 pounds facilities is another plus for the LBM system to meet the requirements of DOD Reference as well as being a benefit to the Air Force in Mission 4 from Vandenberg Air Force Base. The maintaining Titan III technology and capabil­ projected Mission 4 capability of the /baseline ity.': -/. ' ' '.. ' ,'.: ,-; ' .- -. '.- STS is only 24,000 pounds considering.a weight savings program of 5,100 pounds for the Orbiter Because the Titan LBM is based upon proven and 6,000 pounds for-the External Tank (ET) hardware* minimal development risks are in­ and 109% of Rated'Power Level for the Space. '. curred. The system will use the existing Stage Shuttle Main.Engine (SSME) . ' I Titan 34D engine, developed to its present state by testing and flights conducted during Recognizing that additional weight .savings the past 20 years. Martin Marietta will build programs and state-of-the-art performance the 10-ft diameter tanks (same as Titan) utili­ improvements on the baseline STS would not zing technology, materials, facilities and make up the performance deficit, NASA, in 1978, techniques developed for the Titan systems. initiated.analyses of performance augmenta­ tion concepts. Early studies were centered- Initial studies by NASA with the solids options on combinations of solid motors strapped onto indicated that it would have been difficult to the Solid Rocket Boosters and clusters of keep below the maximum STS allowable dynamic solid rocket motors attached beneath the ET. pressure of 650 pounds per square foot. The In early 1979 Martin Marietta Corporation and Titan LBM system, with its lower thrust being Aerojet Liquid Rocket Company presented a applied over a longer flight time will not thrust augmentation concept which utilized violate the maximum pressure constraint. Titan technology,, hardware and propellants. Accordingly, the LBM will provide a softer Subsequent to further comparative analysis ride to shuttle payloads and less severe load- 1-66 ing during launch for the STS vehicle as a fuel) . Engine shutdown will be initiated by whole. propellant depletion which is a standard mode for Titan III Stage I engines. After shutdown The LBM, as currently concepted, will provide the module will be jettisoned. an increase in the anticipated Mission 4 payload capability of more than 17,000 pounds. The Titan Liquid Boost Module offers great This would bring the capability of the flexibility in operation. Although the tanks Thrust Augmented STS to over 41,000 pounds. are being sized to carry propellants for 200 (Figure 1) seconds burn time, missions that require less thrust augmentation can be accommodated by off NASA estimates indicate development costs loading the LBM tanks to provide a burn time would have been comparable for both the solid compatible with mission requirements. Pay- strap-on and the LBM options. While the cost load growth can be achieved by simply filling per flight estimate is higher for LBM aug­ the baseline tanks to a minimum ullage level, mented flights, costs per pound of payload providing additional auxiliary pressurization delivered is more favorable. NASA estimates and extending the engine burn duration to 225 these costs at approximately $1,700 per pound seconds. Other growth options are available for the strap-on solid version compared to by adding additional tank capability or add­ $1,500 per pound for the LBM. ing additional engine subassemblies. Because the LBM augmented STS shows such a TITAN-LBM generous performance margin over the Mission ENGINE 4. requirements, considerable mission planning The current Stage I, Titan III engine for the flexibility will be available. For instance, Titan 34D (T34D) is a pump fed, hypergolic the SSME's could be programmed for less propellant engine. It consists of two iden­ operating time at 109% of rated power level tical subassemblies, each producing 264,500 during a mission, thereby enhancing the life pounds of thrust at altitude. The engine is expectancy of the engine. qualified to twelve 200 second burns. The Titan-LBM design flight duration is 200 LIQUID BOOST MODULE CONFIGURATION seconds. Major engine performance values are provided in Figure 3. The baseline configuration of the Titan Liquid Boost Module consists of four Titan-type ten Each subassembly is started by a solid pro­ foot diameter tanks (two fuel and two oxizi- pellant start cartridge fired into the two zer), a Titan 34D Stage I engine, a truss stage turbine system which is gearbox con­ that ties the tanks and engine together and nected to the fuel and oxidizer pumps. Rising a skirt assembly to attach the module to the fuel pressure opens the thrust chamber valves aft end of the external tank. The skirt allowing oxidizer to flow directly through assembly includes an ordnance separation the injector, into the thrust chamber plenum joint to allow the module to be jettisoned cavity. Fuel flows through the regeneratively from the ET after the propellants have been cooled 6:1 thrust chamber, into and through expended. As on Titan vehicles, an engine the injector causing the hypergolic ignition. heat shield assembly will be provided to A honeycomb constructed, fiberglass/phenolic protect the engine components from the launch resin ablative skirt expands the combustion environments. The heat shield will also pro­ gases to the final 15:1 area ration. tect components of an auxiliary helium Small amounts of pressurization system for the oxidizer tanks. each propellant are boot­ strapped off the thrust The major components are shown in Figure 2. chamber inlet lines to feed a gas generator which drives the The four propellant tanks will be arranged turbine during steady state operation. Some gas generator symmetrically with their centers on a 21.3 hot gas is subsequently cooled and provides autogenous foot circle under the ET. The LBM assembly pressurization to the fuel tank. will extend 24.2 feet below the liquid Similarly, oxidizer is tapped off the main discharge line, vaporized hydrogen tank dome on the external tank. The in a superheater and supplies module has an overall length of 34.6 feet autogenous pressur­ ization to the oxidizer from the attachment to the liquid hydrogen tank, tank at the barrel to dome ring frame to the The entire engine system is supported by a exit plane of the LBM engines. tubular constructed, steel engine frame. Mechanical and electrical interfaces are The LBM engines will be ignited five seconds nearly identical to Titan 34D excepting only after SRB ignition and will burn for 200 the autogenous plumbing interface locations. seconds. This LBM engine start sequence is designed to minimize launch facility impacts. The T34D launch vehicle first stage consists During operation, the engine will burn of one each oxidizer and fuel tank. Space 350,000 pounds of hypergolic propellants constraints under the STS External Tank re­ (nitrogen tetroxide oxidizer and Aerozine 50 sulted in the packaging of four propellant 1-67 tanks, a pair supplying each engine sub- PRQPELLANT TANKS assembly for the LBM. The packaging results in the addition of an identical fuel auto­ The four propellant tanks will be developed genous gas cooler and some fuel and oxidizer using technology, materials, facilities, autogenous plumbing rerouting.
Details
-
File Typepdf
-
Upload Time-
-
Content LanguagesEnglish
-
Upload UserAnonymous/Not logged-in
-
File Pages12 Page
-
File Size-