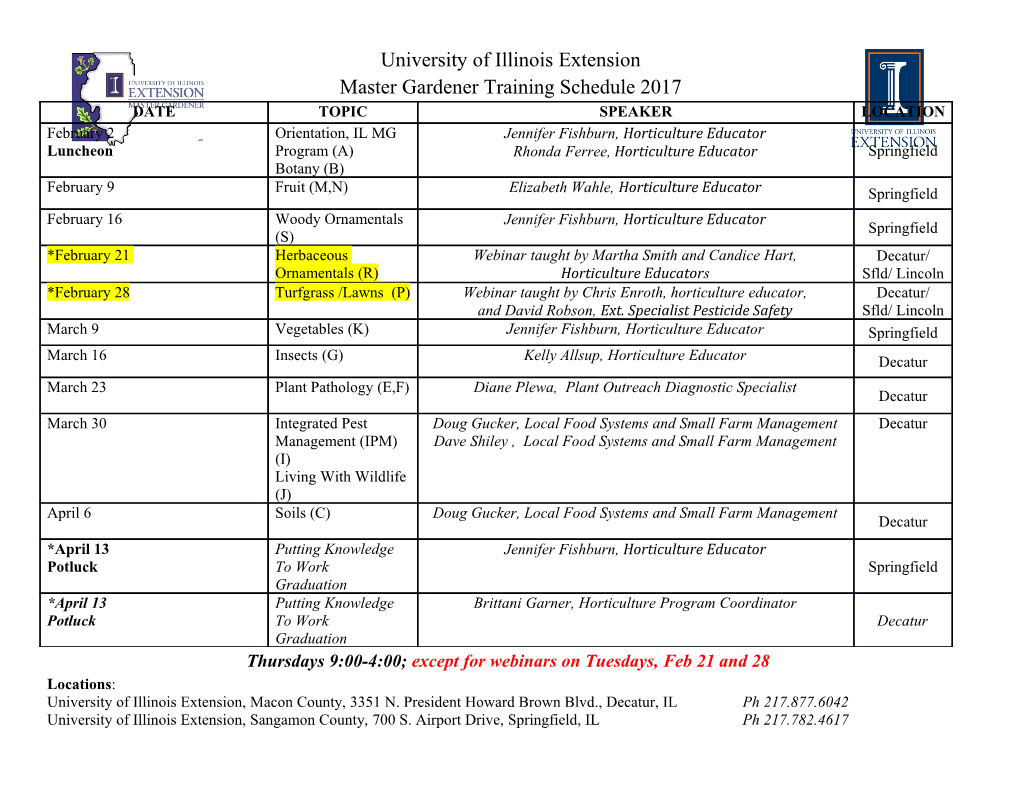
Simulation and Analysis of Ultrasonic Wave Propagation in Pre-stressed Screws Erik Andrén Engineering Physics and Electrical Engineering, master's level 2019 Luleå University of Technology Department of Computer Science, Electrical and Space Engineering ii ABSTRACT The use of ultrasound to measure preload in screws and bolts has been studied quite frequently the last decades. The technique is based on establishing a relationship between preload and change in time of flight (TOF) for an ultrasonic pulse propagating back and forth through a screw. This technique has huge advantages compared to other methods such as torque and angle tightening, mainly because of its independence of friction. This is of great interest for Atlas Copco since it increases the accuracy and precision of their assembly tools. The purpose of this thesis was to investigate ultrasonic wave propagation in pre-stressed screws using a simulation software, ANSYS, and to analyse the results using signal pro- cessing. The simulations were conducted in order to get an understanding about the wavefront distortion effects that arise. Further, an impulse response of the system was estimated with the purpose of dividing the multiple echoes that occur from secondary propagation paths from one other. The results strengthen the hypothesis that the received echoes are superpositions of reflections taking different propagation paths through the screw. An analytical estimation of the wavefront curvature also shows that the wavefront distortion due to a higher stress near the screw boundaries can be neglected. Additionally, a compressed sensing technique has been used to estimate the impulse response of the screw. The estimated impulse response models the echoes as superpositions of secondary echoes, with significant taps corresponding to the TOF of the shortest path and a mode-converted echo. The method is also shown to be stable in noisy environments. The simulation model gives rise to a slower speed of sound than expected, which most likely is due to the fact that finite element analysis in general overestimates the stiffness of the model. iii PREFACE This thesis has been written with the purpose of completing my Master's degree in En- gineering Physics and Electrical Engineering at Lule˚aUniversity of Technology (LTU). I am very thankful to have been given this opportunity working at Atlas Copco, a company with fantastic co-workers and a great working environment. My supervisors at Atlas Copco have been invaluable during the work; Erik Persson for his wide expertise in all fields, and Johan N˚asellfor his talent in explaining and guiding me through many obstacles on the way. Equally, I would like to thank my supervisor at LTU, Professor Johan Carlson, for sharing his research and ideas in this field, always challenging me in a way where the learning objective and my personal development are in focus. A special thanks goes to Andreas Rydin at ANSYS Sweden AB for his professional support and feedback, which in the end made the simulation results possible at all. Finally, thanks again to Johan Carlson for letting me use his stylish LaTeX template during the writing of this thesis. Enjoy reading! Erik Andr´en 16th June 2019 v CONTENTS Nomenclature ix Chapter 1 { Introduction 1 1.1 Background . .1 1.2 Screw Joints . .2 1.3 Tightening . .3 1.3.1 Torque Tightening . .3 1.3.2 Ultrasonic Measurements . .3 1.4 Objective . .5 1.5 Limitations . .5 1.6 Outline . .5 Chapter 2 { Theory 7 2.1 Solid Mechanics . .7 2.1.1 Hooke's Law . .7 2.1.2 Elastic Deformations . .8 2.2 Finite Element Method (FEM) . 10 2.2.1 Mode Superposition (MSUP) Method . 10 2.2.2 Full Method . 11 2.3 Ultrasonic Wave Propagation . 11 2.3.1 Attenuation . 11 2.3.2 Wave Modes . 12 2.3.3 Reflection and Mode Conversion . 12 2.3.4 Piezoelectric Transducers . 14 2.3.5 Wavefront Distortion . 14 2.4 Acoustoelastic Effect . 17 2.4.1 Small-on-large Theory . 17 2.4.2 The Plane Wave . 18 2.5 Ultrasonic Preload Measurements . 20 2.6 Compressed Sensing . 21 Chapter 3 { Method 25 3.1 Finite Element Analysis . 25 3.1.1 Pre-stress . 26 3.1.2 Transient Analysis . 26 3.1.3 Pre-stressed Transient Analysis . 28 3.2 Post-processing . 29 3.2.1 Wavefront Curvature . 29 3.2.2 Compressed Sensing . 29 Chapter 4 { Results 31 4.1 Wave Propagation . 31 4.2 Secondary Echoes . 31 4.3 Pre-stressed Transient Analysis . 34 4.4 Wavefront Curvature . 36 4.5 Compressed Sensing . 36 Chapter 5 { Discussion & Conclusion 41 5.1 Interpretation of Results . 41 5.2 Simulation Limitations . 42 5.3 Conclusion . 44 5.4 Future Work . 44 Appendix A{ ISO Screw Dimensions 45 Appendix B{ Mode-converted Echo 47 viii Nomenclature Acronyms Symbols ∆TOF Difference in time of flight αq Amplitude AWGN Additive white Gaussian noise χ Mapping function ∆x Element size CAD Computer-aided design δ Elongation CS Compressed sensing `1; `2 Norm functions DOF Degrees of freedom κ Bulk modulus FEA Finite element analysis λ, µ Lam´econstants FEM Finite element method Λ Acoustic tensor ISO International Organization for Stan- C; ξi Damping coefficients dardization F Deformation gradient tensor LASSO Least absolute shrinkage and selec- tion operator F Nodal acting forces I Identity matrix LS Least-squares K Global stiffness matrix MSUP Mode superposition M Mass NDT Non-destructive testing m Polarization direction ODE Ordinary differential equation n Propagation direction RR Ridge regression S Nominal stress tensor SNR Signal-to-noise ratio U Convolution matrix TOF Time of flight u Input signal US Ultrasonic u Nodal displacements ix x; X Position vectors f Twice differentiable function y Recorded displacement Fpre Preload µR; γ Regularization parameters H(!); h(t); h Transfer function ν Poission's ratio J Jacobian p ! Frequency j Imaginary unit, −1 φi Mode shapes K Screw stiffness ρ Density k Nut factor σ Tensile load k(!) Complex wave number τ Time delay L Length of screw " Cauchy strain l; m; n Murnaghan constants A cross sectional area P Acoustic pressure A; B; C Third order elastic constants P; p Material points Aii(z) Acoustoelastic constant Q Number of propagation paths aij Acoustoelastic coefficients q Propagation path q cl; cii(z) Longitudinal wave speed R Reflection coefficient cp Phase velocity T Torque cs; cij(z) Transversal wave speed t Time D Nominal diameter W Strain energy E Young's modulus yi Modal amplitudes e(t) Random noise Z Acoustic impedance x CHAPTER 1 Introduction This chapter will give some background and purpose to ultrasonic measurements for determining the preload in screw joints. Thereafter, the objective, limitations and an outline of the thesis will be given. 1.1 Background The industrial company Atlas Copco is a world leading provider of sustainable productivity- enhancing solutions. Their business area in industrial technique is mainly providing power tools and assembly systems [1, 2]. The by far most common method when se- curing parts and components to one other is to use a screw and a nut (or a threaded hole) to clamp the joint members together. The reason for this is its simplicity and cost efficiency. When tightening a screw joint, the force with which it is tightened is known as the preload. The accuracy of the preload is essential for the screw joint to work properly. Some of the factors that affect the accuracy of the preload are: tools, operator, control method, short and long-term relaxation, external loads, and the quality of parts. This thesis will look at improvements of the control method, i.e. measuring the preload. Most tightening techniques are very sensitive to variation in friction in the contact areas of the screw joint, resulting in a poor accuracy. Atlas Copco is therefore investigating the possibility of measuring the preload with ultrasonic pulses, a technique independent of friction. The time of flight (TOF) for an ultrasonic pulse is defined as the time it takes for a sound wave to propagate back and forth through the screw. As the screw is tight- ened the TOF will increase; partially from the fact that it gets longer, but also due to a decrease of sound speed (a phenomena known as the acoustoelastic effect). Thus the preload can be estimated very accurately by measuring the difference in TOF (∆TOF) between an untightened and tightened screw. Previous studies have proven this by fitting a mathematical model to measured data. However, when the clamp length could not be assumed to be much longer than the diameter of the screw the one-dimensional analysis 1 2 Introduction failed [3]. Further, the ultrasonic pulse suffers from distortion, resulting in difficulties in detecting the received pulse and its TOF. Quantization errors will also arise due to a limited sampling rate. Martinsson et al have presented a parametric method for determining the frequency dependent attenuation and phase velocity in dispersive media using ultrasonic pulse-echo measurements [4, 5]. This method is based on finding a parametric model for the fre- quency dependent transfer function of the system. Unlike cross-correlation methods (like TOF measurements) the method is unbiased, and the noise is significantly suppressed compared to non-parametric methods such as Fourier analysis. Continuing with a similar approach, Carlson et al have used a compressed sensing technique to find the impulse response from overlapping ultrasonic echoes when investigating thin materials [6]. This can be compared to the overlapping of echoes that results from sidewall reflections and secondary propagation paths in a screw. 1.2 Screw Joints The screw joint to be considered in this work is depicted in Fig. 1.1, which consists of a screw and a nut, holding two different parts together.
Details
-
File Typepdf
-
Upload Time-
-
Content LanguagesEnglish
-
Upload UserAnonymous/Not logged-in
-
File Pages63 Page
-
File Size-