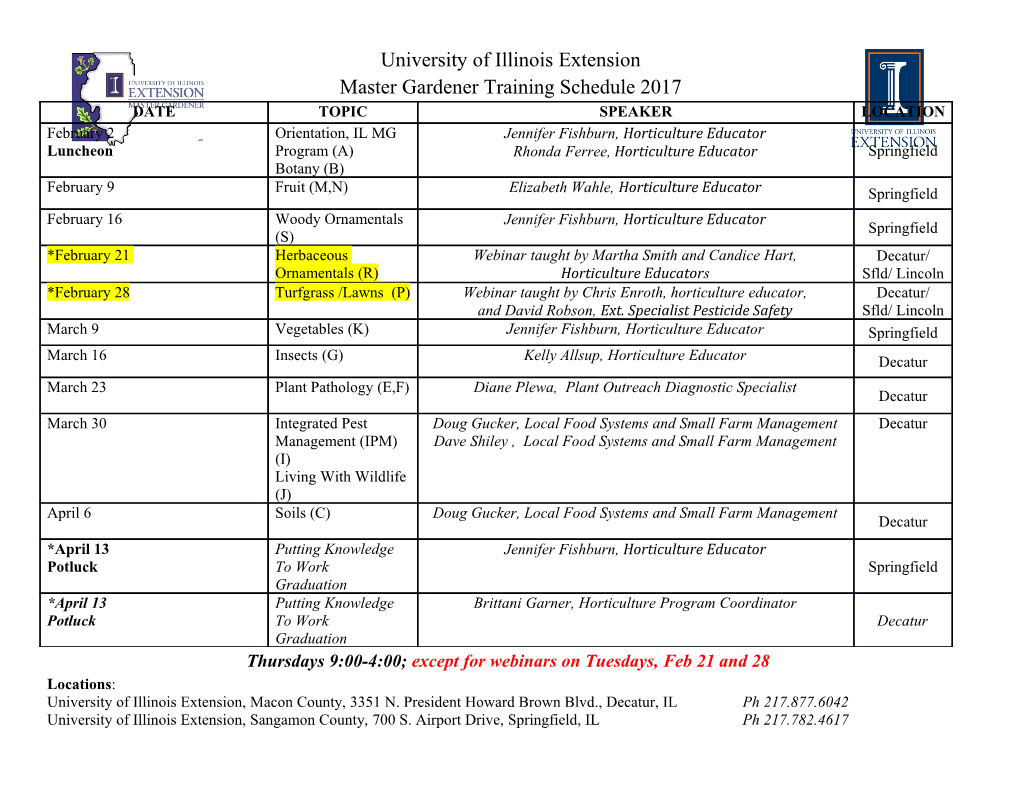
Tall Oil Soap Recovery TAPPI Kraft Recovery Short Course C.D. Foran, Arizona Chemical Co., Savannah GA Slide 1 Tall oil soap is a mixture of the sodium salts of rosin acids, fatty acids and neutrals that separates from kraft black liquor. Composition of Crude Tall Oil Northern New Southern USA & Zealand & USA Canada Scandinavia Chile Acid Number 165 135 132 158 Resin Acids % 41 30 23 43 Fatty Acids % 51 55 57 40 Neutrals % 8 15 20 14 1 Slide 2 How Much Tall Oil Can Be Recovered ? Soap Recovery Tall Oil Tall Oil 52 26 51 25.5 kg/1000 kg lb/ ODT Region 50 25 OD Wood Wood 49 24.5 Piedmont 24 48 48 24 47 23.5 kg CTO/ODt Pine Wood Pine CTO/ODt kg Coastal 26 52 Lb. CTO/ODT Pine Wood46 23 45 22.5 Canada 11.5 23 Jan Feb Mar Apr May Jun Jul Aug Sep Oct Nov Dec Average Southwestern 31.5 63 Impact of Storage Time on West of 7.5 15 Tall Oil Loss 100% Cascades 80% 60% NZ & Chile 12 24 40% Tall Oil Loss Tall Finland 18.5 37 20% 0% 0 2 4 6 8 10 12 14 16 18 20 22 24 26 28 Sweden 25 50 Storage Time (weeks) Outside Chips Roundwood Chips Slide 3 Why Should Tall Oil Soap Be Recovered ? •To improve pulp and paper mill operations •To reduce the toxicity of pulp mill effluents, •To reduce accidents due to slips and falls. •To increase mill revenue 2 Slide 4 Tall Oil Soap Should Be Recovered To Improve Pulp and Paper Mill Operations : Impact of Improved Soap Removal on Evaporator Overall Heat Transfer 1. Reduce evaporator fouling, 110% 2. Increase evaporator uptime, 3. Increase recovery boiler 100% solids burning capacity, 90% reduction efficiency 4. Reduce paper machine 80% (of Initial Maximum) (of foaming, 70% Heat Transfer Coefficient Coefficient Transfer Heat 5. Reduce bleaching costs, 60% 0 10203040 Hours Running No Soap Recovery Poor Soap Recovery Good Soap Recovery Slide 65 Influence of Skimmer Outlet Residual on: Evaporator Time On-Line Evaporation Rate 100% 100% 98% 98% 96% 94% 96% 92% 90% 94% Availability 88% 92% 86% 84% 90% Fraction of Maximum Evaporation Rate 82% 80% 88% 0.5 0.7 0.9 1.1 1.3 1.5 1.7 1.9 2.1 0.5 0.7 0.9 1.1 1.3 1.5 1.7 1.9 2.1 Skimmer Outlet Soap Residual Skimmer Outlet Soap Residual (% CTO on a Solids Basis) (% CTO on a Solids Basis) 3 Slide 6 How Soap Skimming Affects Evaporator Performance Overall Good Poor Skimming Skimming Change Skimmer Residual (%) 0.6 1.1 0.5 Downtime (hr./month) 45 75 30 Evaporation 323 315 -8 Rate (Mkg/hr) Production (Tonnes) Unbleached 34500 32100 -2400 Bleached 24700 23000 -1700 Slide 7 Tall Oil Soap Should Be Recovered To Reduce Pulp Mill Effluent Toxicity 1. Fatty Acids, Resin Acids and Phenols affect both the toxicity to fish and the taste and color of fish. 2. Sodium soaps of resin acids account for 80% of the effluent toxicity. 3. Sodium soaps of unsaturated fatty acids account for 20% of the effluent toxicity. 4. Toxicity is independent of oxygen demand. 4 SlideSlide 8 9 What causes soap to separate from black liquor ? • Increased liquor solids, • Decreased liquor temperature, • Residual effective alkali above 6 gpl, • Increased fatty acid to resin acid ratio • Decreased hardwood liquor content. Slide 9 Soap Solubility 3.5 3.0 PAST 2.5 160 F 71 C 2.0 120 F 49 C 1.5 NOW 80 F 27 C 1.0 0.5 Tall Liquorof Solids Oil % 0.0 10 15 20 25 30 35 40 45 50 55 Black Liquor Total Solids (%) At washer filtrate temperatures, soap begins to come out of solution at about 8% solids. Minimum solubility occurs at 25 – 30% solids. 5 Slide 10 The Effect of Residual Effective Alkalinity and Soap Composition on Soap Solubility 0.5 0.45 0.4 1. Minimum solubility 0.35 occurs at 6 - 8 gpl REA, 0.3 2. Increasing the fatty acid : 0.25 resin acid ratio will 0.2 reduce soap solubility. 0.15 3. The fatty acid : resin acid 0.1 ratio is determined by the 0.05 Soap Solubility% ( Soap-Solids basis) wood species used. 0 051015 Residual Effective Alkali ( g/l) FA/RA = 5 FA/RA < 2 Slide 11 Influence of Hardwood Content on Tall Oil Soap Solubility 1.2 1 0.8 Mill A 0.6 Mill B 0.4 lb CTO/ 100 lb BLS lb 100 CTO/ lb 0.2 0 0% 20% 40% 60% 80% 100% Hardwood in Furnish 6 Slide 12 Where does soap separate from black liquor ? 1. Washer filtrate tanks 2. Weak liquor storage tanks 3. Evaporator soap skimmers 4. (Heavy liquor storage tanks) Slide 1413 Why Soap Should be Removed from Weak Liquor Storage Tanks • Soap acts as a surfactant that stabilizes foams and increases evaporator liquor carryover. • At weak liquor solids levels greater than 14%, soap accumulates rapidly, reducing weak liquor storage significantly. • Weak liquor skimming increases overall soap removal by reducing the load on the evaporator soap skimmers. 7 Slide 14 Foam liquor carryover will occur if the height of a column of foam is taller than the height of the vapor space in the evaporator. Foam Height = Volumetric Evap. Rate* Bubble Life Foam Column Area • The bubble life is increased by lower temperatures, smaller bubble diameter and increased soap content. • Removal of the soap before evaporation will reduce the bubble life and reduce liquor carryover. Slide 15 Slide 15 Common Configurations for Manual Weak Liquor Soap Skimming Soap Liquor Advantage Simple and inexpensive to install Disadvantages Requires much operator attention Can result in significant liquor carryover. 8 Slide 16 Weak Liquor Floating Soap Skimmers VENT TO NCG SYSTEM SOAP CONCENTRATOR (OPTIONAL) SOAP LEVEL LIQUOR LEVEL SOAP PUMP TO STORAGE LIQUOR FEED 16% SOLIDS LIQUOR RETURN PUMP Advantages Disadvantages •Reduces the risk of soap Higher capital surges to the evaporators cost •Increases the effective liquor storage capacity Slide 17 Soap Skimmer Efficiency (Inlet Soap - Outlet Soap) (3.0% - 0.6%) = (Inlet Soap - Soap Solubility) (3.0% - 0.45%) =94% Good skimming greater than 85% efficiency Tall Oil Solubility @ 71 C (160 F) 3.5 3 2.5 2 1.5 1 0.5 Tall Oil % Solids Liquor of Oil Tall 0 10 15 20 25 30 35 40 45 50 55 Black Liquor Solids (%) 9 Slide 18 Skimmer Baffling to Prevent Soap ShortCircuiting Baffle Baffles Liquor Path Liquor Path Poor Baffling Good Baffling Soap To Storage Soapy Liquor to Soap Bed Skimmer Skimmed Liquor Circular Soap Skimmer Layout Soap Liquor Collection Soap Trough Scraper In Rotation Baffle Liquor Out Soap Scraper Liquor In Soap Bed Baffle Soap Pump Liquor Soap Out Collection Trough 10 Slide 19 How Skimmer Dimensions Affect Skimmer Efficiency Soap will not separate if the soap particle rise rate is less than the liquor downdraft. (Superficial Liquor Velocity) Effect of Superficial Liquor Velocity on Skimmer Efficiency 100% 80% 60% 40% 20% Skimmer Efficiency Skimmer 0% 0123456 Superficial Liquor velocity ( mph) Canadian Mills Southeast US Mills Slide 20 How Skimmer Dimensions Affect Skimmer Efficiency Efficiency 75% Efficiency 90% 40 Ft. 12 m Residence time 155 min 60 Ft. 18 m 33 Ft. Superficial Liquor Residence time 158 min 10 m 15 Ft. Velocity 13 fph (4 Superficial Liquor Velocity : 4.6 m mph) 6 fph (2 mph) Feed Rate 2000 gpm (7580 lpm) 11 Slide 21 Skimmer Level Control Soap To Storage X Soap Bed A Soapy Liquor to Liquor Skimmer Overflow Standpipe Skimmed Liquor A= X *Dl/(Dl-Ds) A= 4 *1.13/(1.13-0.94) Ds - Density of Soap = 24 Dl - Density of Liquor Slide 22 Soap Skimmer Efficiency Improvement Stabilize skimmer level control. Soap bed depth < 2 ft. (0.6 m) Effect of Air Injection Remove solids buildup 90 min. Residence Time 8 24 Ensure that the inlet is well 6 18 isolated from the outlet 4 12 Evaluate air injection to the 2 6 Dens. & Skim. Resid. suction of the skimmer feed Soap Liquor Content (%) 0 0 pump. 00.511.522.5 SCFM/1000 gpm Skimmer Feed Density (lb/gal) Residual lb/Mlb BLS Liquor Content (%) Evaluate chemical additives 12 Slide 23 How Air Addition Affects Soap and Liquor Bed Depth at a Fixed Skimmer Level Set-Point Liquor Soap Soap Soap sp.gr. 1.14 sp.gr. 0.12 sp.gr. 0.54 sp.gr. 0.96 200 150 Depth 100 50 0 High Air Addition Moderate Air No Air Addition Addition Liquor Depth (in.) Soap Bed Depth Slide 24 Soap Pumping, Piping Î Ensure that the pump suction is not restricted or reduced, Î Minimize the length of the pump suction Î Use positive closure ball valves Î Isolate spare soap pumps by ball valves, never use check valves Î Use positive displacement pumps Î Provide steam clean-out lines Î See also http://www.pumpschool.com 13 Positive displacement pump flow rate is relatively independent of viscosity Flow vs. Viscosity 100 80 60 40 Flow (%)Flow 20 0 0 250 500 Viscosity centi-poise Positive Displacement Centrifugal Positive Displacement Pumps Produce Essentially Constant Flow That Is Almost Independent Of Pressure Centrifugal Pump Curve Pressure (Head) Positive Displacement Pump Curve Flow Rate 14 Positive displacement pump flow rate is relatively independent of viscosity Flow vs. Viscosity 100 80 60 40 Flow (%)Flow 20 0 0 250 500 Viscosity centi-poise Positive Displacement Centrifugal Positive Displacement Pumps Produce Essentially Constant Flow That Is Almost Independent Of Pressure Centrifugal Pump Curve Pressure (Head) Positive Displacement Pump Curve Flow Rate 15 Slide 25 Soap Pumping Problems ÎEnsure that the pump suction is not restricted or reduced, ÎCheck the pump rotation ÎPositive displacement pumps: Set the internal pressure relief valve 50 – 100% above the Normal system pressure ÎCheck Gear pumps for wear ÎToo much Liquor – Lower the skimmer level ~ 1% ÎLow Soap Density ( < 0.23 sp.
Details
-
File Typepdf
-
Upload Time-
-
Content LanguagesEnglish
-
Upload UserAnonymous/Not logged-in
-
File Pages17 Page
-
File Size-